Sand Casting
Summary
TLDRThe video explains the sand casting process, highlighting why sand is ideal for holding molten metal due to its high heat resistance. The procedure involves mixing sand with bonding agents, forming it in a molding box (flask), and placing a pattern inside to create a mold. The mold is used to pour molten aluminum, which solidifies into the desired shape. After cooling, the mold is broken to retrieve the casting. Excess parts are cut off, leaving the final cast ready for further machining.
Takeaways
- 🔥 The reason sand is used in casting is because it can withstand the high heat of molten metal, such as aluminum.
- 🤚 Properly mixed sand should hold its shape when squeezed, achieved by adding agents like bentonite, water, and wood.
- 🛠️ The sand is mixed in a drum before being packed into a mold, known as the flask, which has two parts: the drag (bottom half) and the cope (top half).
- 🧩 A pattern, often placed in the center of the mold, creates a cavity in the sand for the metal to flow into, forming the casting.
- ⚙️ Runners, gates, and wells are critical in guiding the molten material into the casting cavity while also filtering out foreign material.
- 🌟 Talcum powder is applied to the pattern to prevent the sand from sticking to it, ensuring a clean removal after packing the sand.
- 🔧 Sifted sand is packed tightly around the pattern to provide a smoother surface finish for the casting.
- 🔄 After the sand is packed and the mold is completed, the flask is carefully separated to remove the pattern, leaving a void where the metal will flow.
- ⚡ Molten aluminum is poured into the mold through a sprue, filling the casting cavity and solidifying into the final shape.
- 🗡️ Once solidified, the mold is broken apart, and excess material like runners and gates is cut off, leaving the final casting ready for machining.
Q & A
What is the purpose of using sand in the sand casting process?
-Sand is used in the sand casting process because it can withstand the high temperatures of molten metals. In this case, aluminum is being cast, and sand helps maintain the shape of the mold during the process.
Why are materials like bentonite and wood added to the sand?
-Bentonite, wood, and a small amount of water are added to the sand to help bind it and allow it to hold its shape during the casting process. This mixture ensures the sand stays packed and firm when creating the mold.
What is a 'match plate' and what is its function in sand casting?
-A match plate is the pattern placed in the middle of the molding box to form the shape of the casting. It consists of the part to be cast and other features like gates and runners that direct the molten metal.
Why does the pattern used in the sand casting process need a taper (called a 'draft')?
-The pattern has a taper or 'draft' to ensure it can be removed easily from the sand without disturbing the mold. Without the taper, the sand would grip the pattern and ruin the casting.
What are runners, gates, and wells, and what are their roles in the sand casting process?
-Runners are channels that direct molten metal into the mold, gates are the entry points into the casting, and wells act as reservoirs to catch impurities and hold extra molten metal as it solidifies.
Why is talcum powder applied to the pattern before adding sand?
-Talcum powder is applied to prevent the sand from sticking to the pattern when it is removed. This ensures a clean and undisturbed mold.
Why is the sand sifted around the pattern in the flask?
-Sifting the sand around the pattern removes foreign materials and ensures a finer texture. This helps achieve a smoother surface finish on the final casting.
What is the purpose of flattening the sand on top of the flask after packing?
-Flattening the sand ensures the flask has a smooth surface for alignment when the two halves of the mold are assembled. It also ensures a stable base for the casting.
What happens after the molten aluminum is poured into the mold?
-After the molten aluminum is poured, it solidifies within the mold. Once it has fully solidified, the sand mold is broken apart to remove the casting.
What happens to the excess material like the sprue, runners, and gates after casting?
-The excess material such as the sprue, runners, and gates is cut off from the casting using tools like a vertical bandsaw. These excess pieces can be melted down and reused in future casts.
Outlines
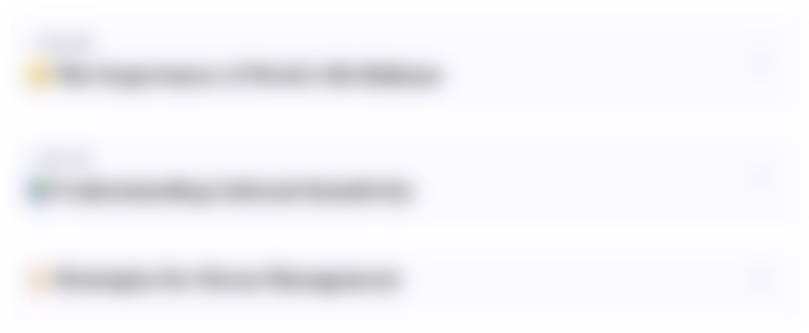
This section is available to paid users only. Please upgrade to access this part.
Upgrade NowMindmap
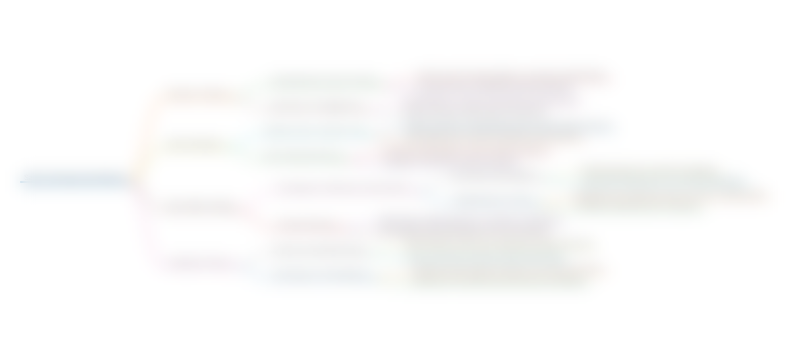
This section is available to paid users only. Please upgrade to access this part.
Upgrade NowKeywords
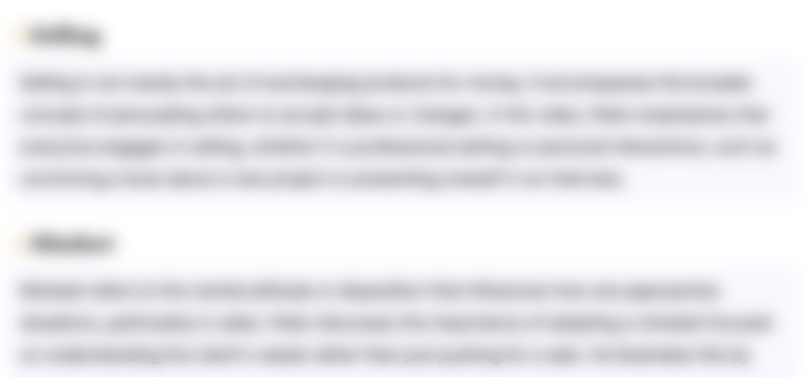
This section is available to paid users only. Please upgrade to access this part.
Upgrade NowHighlights
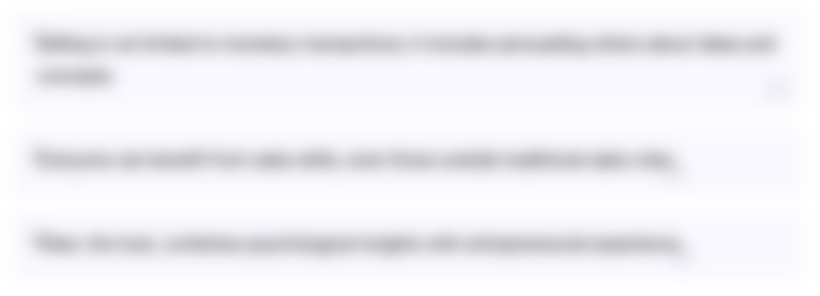
This section is available to paid users only. Please upgrade to access this part.
Upgrade NowTranscripts
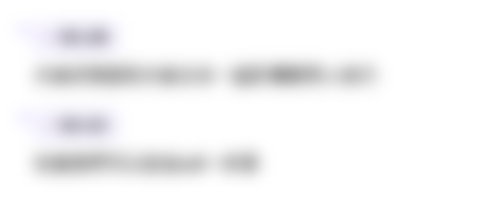
This section is available to paid users only. Please upgrade to access this part.
Upgrade NowBrowse More Related Video
5.0 / 5 (0 votes)