Honda ACCORD Assembly🚘2024: How it's made?😲Production line video➕Crash Testing & FACTORY TOUR
Summary
TLDRThe Honda Accord's manufacturing process at the Marysville Auto Plant in Ohio is detailed, showcasing the transformation from steel rolls to finished vehicles. Key stages include cutting, pressing, welding with over 900 robots, painting with a new 2K primer process, and assembly. Innovative techniques like high-performance adhesive and laser brazing enhance quality. The plant's commitment to efficiency and sustainability is evident through energy-saving technologies and water recycling.
Takeaways
- 🏭 The Honda Accord is manufactured at the Honda Marysville Auto Plant in Ohio, which is one of the most integrated and flexible auto plants in North America.
- 🔩 The production process starts with steel that undergoes a blanking process to cut it into specific shapes, followed by a four-stage press process.
- 🔍 Quality control is emphasized with associates inspecting parts for flaws and defects after the press process.
- 🚗 The forming department is responsible for making bumpers, boomerangs, and dashboards, with different machines assigned to specific parts.
- 🤖 The welding department is highly automated with over 900 robots, including handling, ceiling, and welding robots, working across a large area with over 800 associates.
- 🏗️ Innovative areas introduced include the inner frame, roof razor area, and high-performance adhesive, enhancing the car's quality and rigidity.
- 🎨 The paint department applies new colors to the cars after they leave the weld shop, involving a series of processes including cleaning, sealing, priming, and coating.
- 🛠️ The assembly process includes the installation of interior parts, engine mounting, and rear suspension, with a focus on timing and efficiency.
- 🔍 Rigorous quality inspections are conducted, including a 200-check item list, exterior and lock function checks, and a dyno area for alignment and feature tests.
- 💧 A unique feature is the use of a 2K primer, a two-part primer process, and a waterborne coating system in the paint shop to reduce emissions.
- 🌱 Environmental sustainability is a focus, with investments in energy-efficient facilities, water recycling systems, and reduced emissions in the paint process.
Q & A
What is the initial process for creating a Honda Accord?
-The initial process involves taking a roll of steel, cutting it into specific shapes through a blanking process, and then pressing it through a four-stage die press which includes a draw die, trim die, pierce die, and a final bend die.
How are flaws and defects in the steel parts of the Honda Accord detected?
-After the parts come out from the press, associates on the back line check and inspect the parts for any flaws and defects.
What is produced in the plastic department of the Honda Accord manufacturing?
-The plastic department is responsible for making all the Honda Accord bumpers, boomerangs, and dashboards.
How many different machines are used in the forming department, and what do they produce?
-There are five different machines in the forming department. Number five produces the rears, number seven produces the front, number eight also produces the front bumper, number one produces the instrument panels (IPs), and number eleven produces the rear low grade.
What is unique about the welding department in the Honda Accord manufacturing process?
-The welding department has over 900 robots, including handling robots, ceiling robots, and welding robots, spread across five areas. It is also one of the most integrated and flexible auto plants in North America.
What are the three innovative areas introduced in the Honda Accord manufacturing process?
-The three innovative areas are the inner frame, the roof razor area where the plant is the only Honda plant that does the sunroof model in a brace, and the high-performance adhesive which adds to the rigidity of the body.
What happens to the Honda Accord after it leaves the welding department?
-After leaving the welding department, the Honda Accord goes to the paint department where various colors are applied.
What is unique about the 2K primer process used in the Honda Accord's paint application?
-The 2K primer is a two-part primer process that uses a resin and a catalyst mixed before application. This is unique to the auto industry and is part of the several processes the car goes through in the paint department.
How long does it take to assemble a Honda Accord after it comes from the weld shop?
-It takes an average of about eight and a half to nine hours to assemble a Honda Accord after it comes from the weld shop.
What is the significance of the vehicle quality inspection process for the Honda Accord?
-The vehicle quality inspection process includes a human inspection and a computer-led inspection, performing around a 200-check item list while driving the car through the department. This ensures the car's quality and functionality before it is shipped.
What are some of the environmental improvements made at the Marysville Auto Plant where the Honda Accord is manufactured?
-The Marysville Auto Plant has made several environmental improvements including the use of high efficiency ovens, air recycling systems, more efficient variable drive motors, a 20 million gallon pond to recycle rainwater, and a new waterborne coating system in the paint shop that reduces emissions of hazardous substances.
Outlines
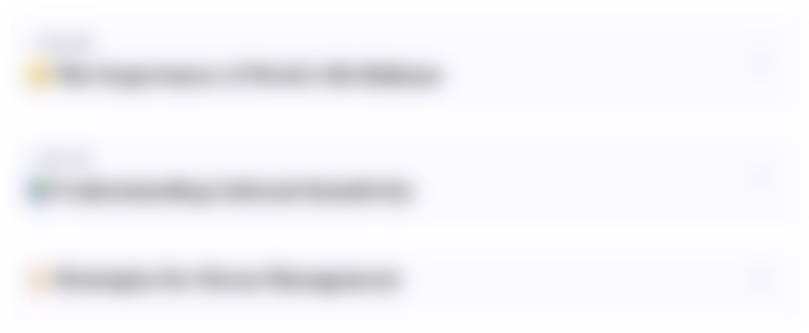
This section is available to paid users only. Please upgrade to access this part.
Upgrade NowMindmap
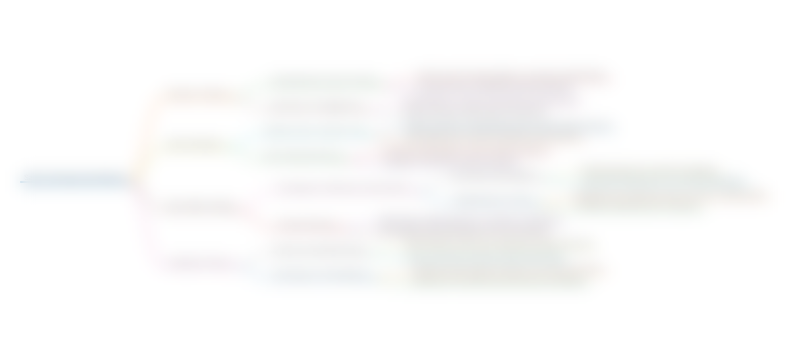
This section is available to paid users only. Please upgrade to access this part.
Upgrade NowKeywords
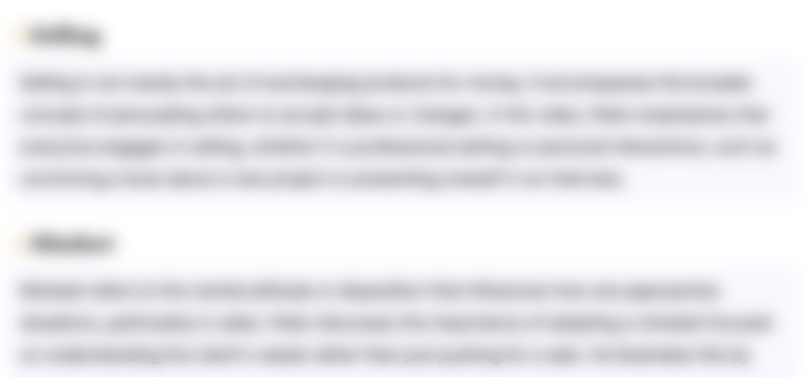
This section is available to paid users only. Please upgrade to access this part.
Upgrade NowHighlights
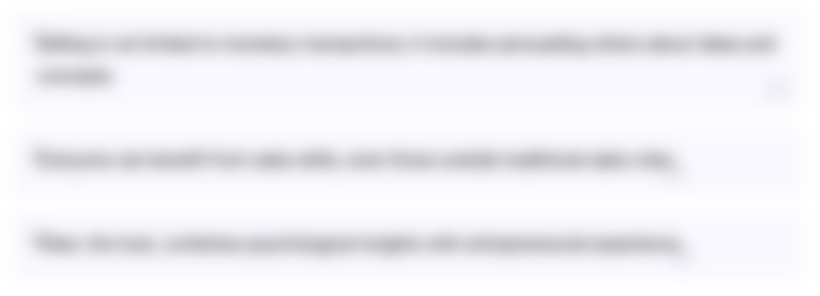
This section is available to paid users only. Please upgrade to access this part.
Upgrade NowTranscripts
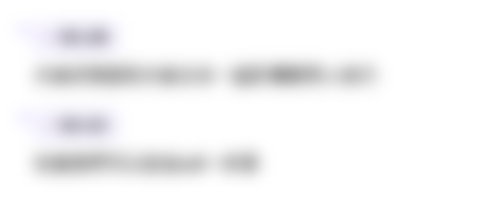
This section is available to paid users only. Please upgrade to access this part.
Upgrade NowBrowse More Related Video

STEEL: From Start to Finish

3 Types of Inventory (Raw Materials, WIP, and Finished Goods)

Así se fabrica el Acero - Discovery Channel

Toyota & Honda Are Leaving America — 840,000 Jobs at Risk!
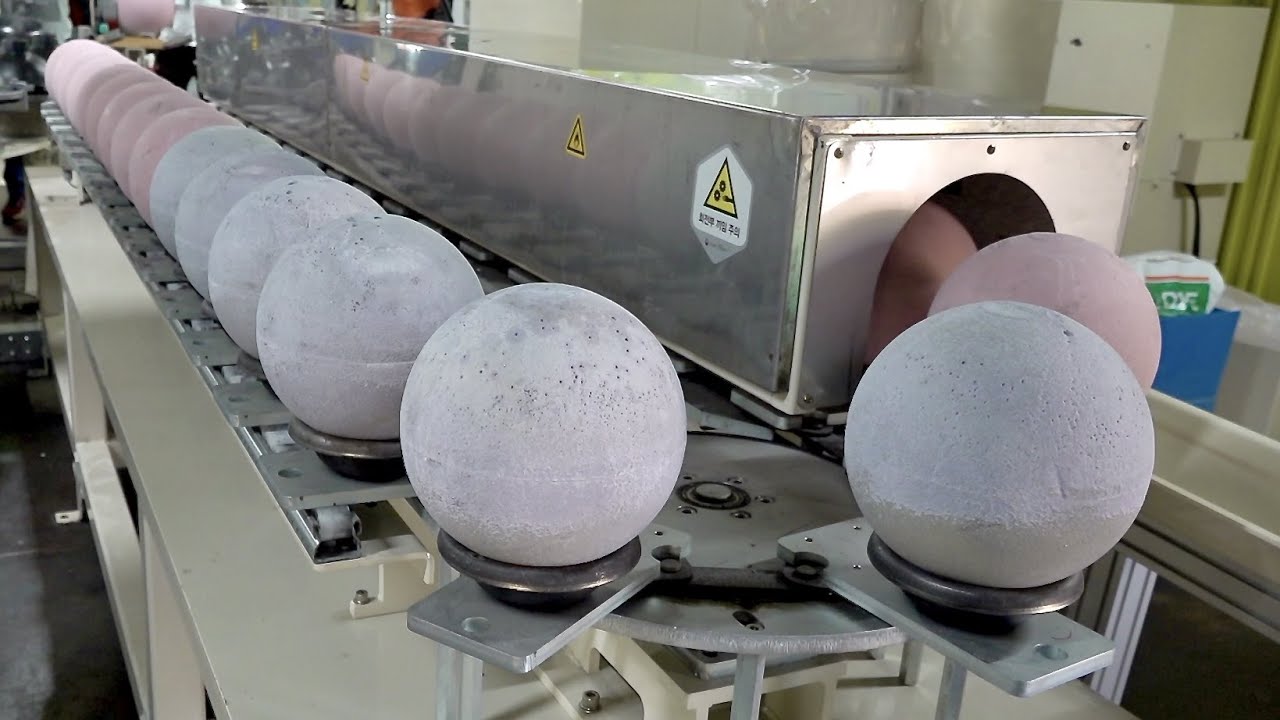
How Bowling Balls Are Made. Interesting Bowling Ball Mass Production Factory

Steel Forming! Process of making Metal Roof Steel Roof Factory in Korea
5.0 / 5 (0 votes)