CR Masterclass 1 - GET Improvement
Summary
TLDRIn this masterclass, Quintin Ninaber, GM of Product Management at CR, discusses how Ground Engaging Tools (GET) can boost productivity by 5% and reduce total cost of ownership. He explains the evolution of GET from simple steel to a highly engineered system, crucial for excavators and loaders. The focus is on tooth design, lip shrouds, and retainers, which directly affect productivity, maintenance, and costs. The introduction of cast lip systems for 100-400 ton excavators and wheel loaders is highlighted as a significant innovation, offering durability, reduced maintenance, and potential for increased productivity. The session concludes with a real-world example demonstrating the impact of these advancements on operational efficiency and cost savings.
Takeaways
- 🔨 GT (Ground Engaging Tools) is a highly engineered system that goes beyond being just a piece of steel, directly impacting excavator productivity and total cost of ownership.
- 🦷 The design of GT teeth is crucial for productivity as they break ground and open the cleavage plane, affecting machine fill times, GT consumption, and dig energy.
- 💼 Lip shrouds play a significant role in productivity by directing material into the bucket efficiently, which is critical for maintaining cycle times and payload.
- 👄 The lip's profile is essential for dig energy, fill times, and overall durability of the bucket system, with different types of lips suited for different machine sizes.
- 🔩 Retainers are vital for ensuring GT stays attached to the lip and bucket, preventing productivity loss and maintenance costs due to lost or broken GT.
- 📈 Machine productivity is defined by the ability to fill trucks efficiently, with durability and dig efficiency being key factors for effective machine utilization.
- ⏱️ Small improvements in cycle time, such as a one-second reduction, can lead to significant productivity gains, especially on large excavators.
- 🚚 The right bucket size and GT configuration can greatly impact productivity by ensuring efficient filling and higher payloads.
- 🏭 The introduction of cast lip systems represents a significant innovation, offering optimized design, lighter weight, and increased strength, leading to improved productivity and reduced maintenance costs.
- 💡 Advanced monitoring and analysis technologies allow for real-time tracking of productivity improvements, demonstrating the impact of GT design changes on machine performance.
- 🔩 The conversion to cast lip systems can significantly reduce infield maintenance and overhaul costs, potentially saving thousands of dollars per machine per year.
Q & A
What is the main focus of the masterclass presented by Quintin Ninaber?
-The main focus of the masterclass is to discuss how Ground Engaging Tools (GET) can deliver a five percent increase in productivity and improve total cost of ownership in mining operations.
What has the evolution of technology done for Ground Engaging Tools (GET) in the mining industry?
-The evolution of technology has transformed Ground Engaging Tools (GET) from being just a piece of steel to highly engineered tools that can directly impact the productivity of excavators, wheel loaders, rope shovels, and drag lines.
What are the key components of GET that affect productivity?
-The key components of GET that affect productivity include the teeth, lip shrouds, and retainers. These components are crucial for breaking the ground, directing material into the bucket, and ensuring all parts stay attached to the lip and bucket, respectively.
Why are teeth important for productivity in mining operations?
-Teeth are important for productivity because they break the ground and open the cleavage plane, which loosens the material in front of the bucket. If the tooth design is not suitable for the application, it can slow down the machine, increase wear and tear, and cost more in maintenance.
What role do lip shrouds play in the productivity of mining operations?
-Lip shrouds play a significant role in productivity by directing material into the bucket as it moves through the digging phase. Misalignment of planes and surfaces can dramatically impact fill energy, dig energy, and cycle times.
How does the design of the lip affect the overall performance of the bucket?
-The lip serves to hold and point the GET, and its profile is critical to dig energy, fill times, and overall durability of the system. The design of the lip can impact the machine's ability to fill trucks efficiently and effectively.
What are the two main types of lips mentioned in the script, and what are their typical applications?
-The two main types of lips are the traditional platelet style, which is used on excavators below the 400-tonne mark and wheel loaders, and the cast lip, which is used for machines with an operating weight of over 400 tonnes.
How can the design of Ground Engaging Tools (GET) impact maintenance practices and costs?
-The design of GET can impact maintenance practices and costs by ensuring durability and ease of maintenance. For instance, the introduction of cast lip systems can reduce infield maintenance and overall overhaul costs by eliminating the need for weld-on components.
What is the significance of the five percent improvement in productivity mentioned in the script?
-A five percent improvement in productivity means that for every hour of operation, an additional truck can be filled, which translates to significant tonnage moved annually and a substantial increase in operational efficiency.
How does the introduction of cast lip systems contribute to reducing maintenance costs and increasing productivity?
-The introduction of cast lip systems contributes to reducing maintenance costs by eliminating the need for weld-on components, which reduces infield maintenance and overhaul costs. It also increases productivity by allowing for a lighter, stronger design that aligns better with the digging process.
What is the Titan Load Hole Optimization System, and how does it benefit the optimization of Ground Engaging Tools (GET)?
-The Titan Load Hole Optimization System is a tool used to pinpoint key factors for efficient digging and track changes to productivity in real-time. It helps in optimizing the design of GET to ensure efficient digging, proper filling of buckets, and reduced cycle times.
Outlines
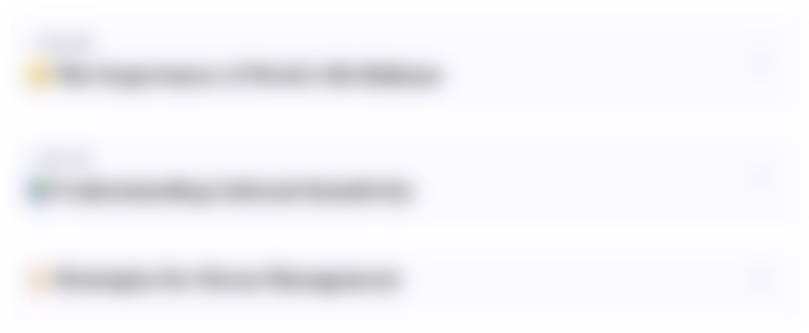
This section is available to paid users only. Please upgrade to access this part.
Upgrade NowMindmap
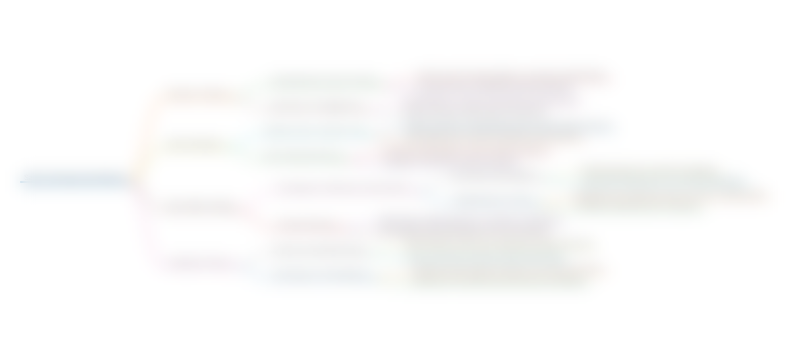
This section is available to paid users only. Please upgrade to access this part.
Upgrade NowKeywords
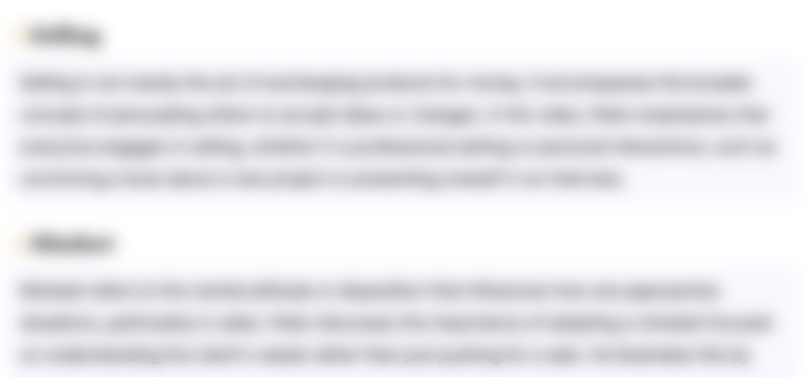
This section is available to paid users only. Please upgrade to access this part.
Upgrade NowHighlights
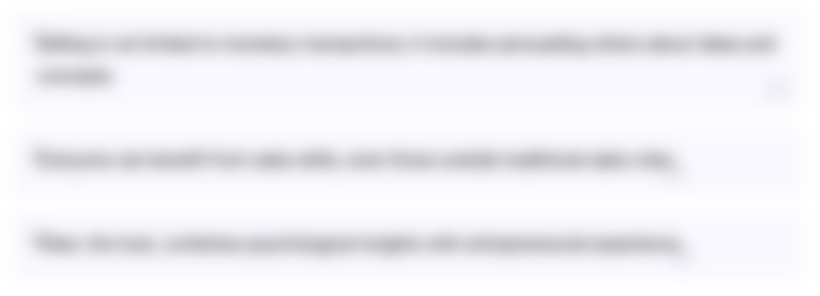
This section is available to paid users only. Please upgrade to access this part.
Upgrade NowTranscripts
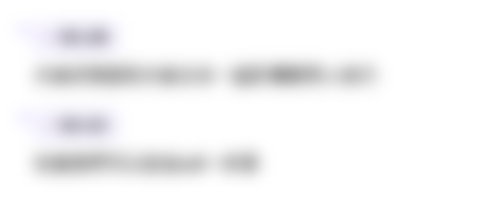
This section is available to paid users only. Please upgrade to access this part.
Upgrade Now5.0 / 5 (0 votes)