Thus shaping the future of dies and moulds: With EOS tooling applications
Summary
TLDREOS, a leading manufacturer of laser centering systems, showcases its technology for efficient and cost-effective production from electronic data, suitable for complex and individualized manufacturing needs. The script highlights a partnership with customers to optimize manufacturing solutions, focusing on a children's cup production case study. EOS integrates conformal cooling channels to enhance tooling performance, using its M 270 system with a hybrid design method. The process involves layer-by-layer manufacturing from 3D CAD data, using EOS Maraging Steel S1, a high-performance material for tool making. The result is a 70% increase in productivity, reduced cycle time, and improved product quality, demonstrating EOS's ability to revolutionize the injection molding process.
Takeaways
- 🌟 The OS is a leading manufacturer of laser centering systems, which are crucial for fast, flexible, and cost-effective production from electronic data.
- 🔧 This technology is ideal for industries where complexity and individuality are paramount, or where conventional solutions are insufficient.
- 🚀 The aim is to enhance the productivity of single-cavity injection molds and to elevate the quality of the end product, exemplified by a high-quality plastic children's cup.
- 🤝 In collaboration with customers, the company showcases how to maximize the optimization potential of manufacturing solutions.
- 🔄 By integrating conformal cooling channels, the cooling performance of the tooling insert is significantly improved, enhancing production efficiency.
- 📐 The 3D CAD model is sliced into layers, and the data is transferred to the EOS M 270 system, setting up a hybrid design method that saves time and costs.
- 🏭 The manufacturing process involves a pre-milled tool insert, which is placed in the EOS M 270's process chamber for layer-by-layer construction using a focused laser beam.
- 🛠 EOS Maraging Steel and S1 are chosen materials for their high performance in series tool making, meeting stringent industry requirements.
- ♻️ Unwelded powder from the manufacturing process is removed and can be reused after a simple sieving process, promoting sustainability.
- 🛎️ The finished tool insert undergoes a hardening heat treatment, milling to final dimensions, and polishing to achieve a high-gloss surface finish.
- 📈 The integration of conformal cooling channels results in more efficient cooling, reducing cycle time by up to 40% and minimizing product warpage, leading to higher quality and up to 70% increased productivity.
Q & A
What is the primary function of the laser centering systems manufactured by EOS?
-The laser centering systems by EOS are key for manufacturing fast, flexible, and cost-effective production directly from electronic data.
In which industries is EOS's technology particularly beneficial?
-EOS's technology is suitable for industries where complexity and individuality converge or where conventional solutions don't exist.
What is the main goal of integrating conformal cooling channels in the tooling insert?
-The goal is to increase the productivity of a single cavity injection mold and to improve the quality of the final product.
How does EOS's technology contribute to the manufacturing of a children's cup?
-EOS's technology enables the production of a children's cup made of high-quality plastic by optimizing the manufacturing process.
What is the significance of the hybrid design method mentioned in the script?
-The hybrid design method saves time and costs by using a combination of pre-milled tool inserts and additive manufacturing processes.
What material is used in the EOS M 270 system for the manufacturing of tool inserts?
-EOS M 270 uses a martensitic thermosetting high-performance steel material, known as EOS Maraging Steel and S1, for manufacturing tool inserts.
How does the EOS M 270 system apply material to the building platform?
-The EOS M 270 system uniformly applies the material in powder form to the building platform with a weak odor through a process involving concentrated melting of the powder with a focused laser beam.
What happens to the unwelded powder after the tool insert is completed?
-The unwelded powder is removed from the completed tool insert and can be reused after a simple sieving process.
What is the hardness level of the finished tool insert after the heat treatment process?
-The finished tool insert is hardened to a Rockwell C scale of 254 after an age-hardening heat treatment process.
How does the integration of conformal cooling channels affect the injection molding process?
-The integration of conformal cooling channels enables more efficient cooling of the plastic cups, shortens the cycle time by up to 40%, and reduces warpage in the product, leading to a lower scrap rate and a quality-optimized final product.
What is the potential increase in productivity when using EOS's manufacturing solution in tool making?
-Using EOS's manufacturing solution can lead to a productivity increase of up to 70%, achieving a rapid return on investment.
Outlines
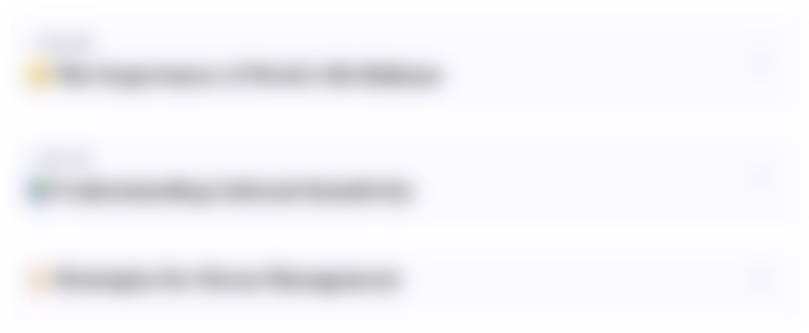
This section is available to paid users only. Please upgrade to access this part.
Upgrade NowMindmap
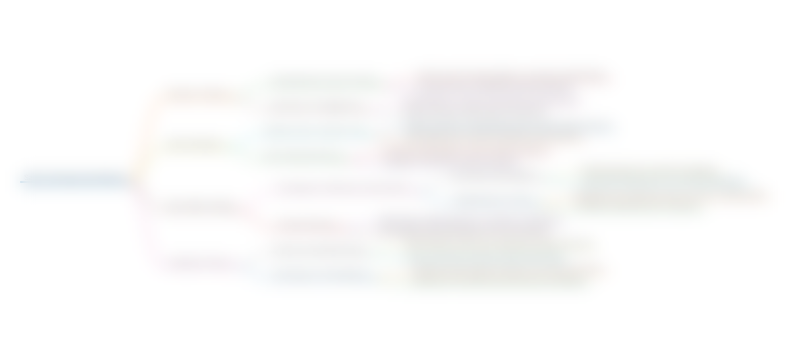
This section is available to paid users only. Please upgrade to access this part.
Upgrade NowKeywords
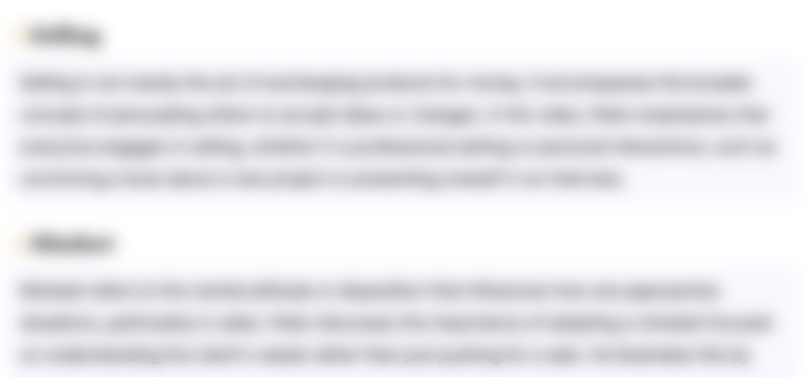
This section is available to paid users only. Please upgrade to access this part.
Upgrade NowHighlights
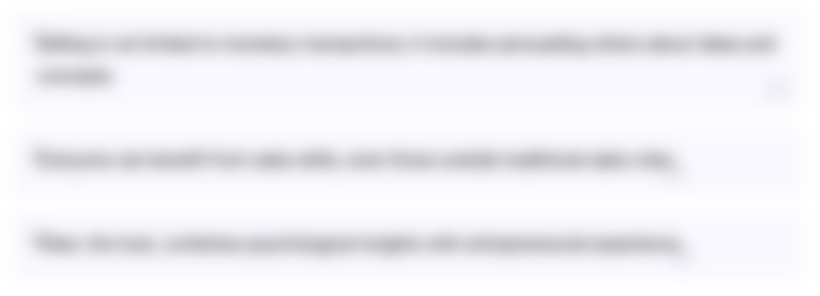
This section is available to paid users only. Please upgrade to access this part.
Upgrade NowTranscripts
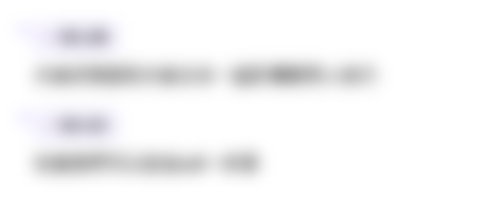
This section is available to paid users only. Please upgrade to access this part.
Upgrade NowBrowse More Related Video

Revolusi Otomasi industri

How to implement IoT to create a smart factory
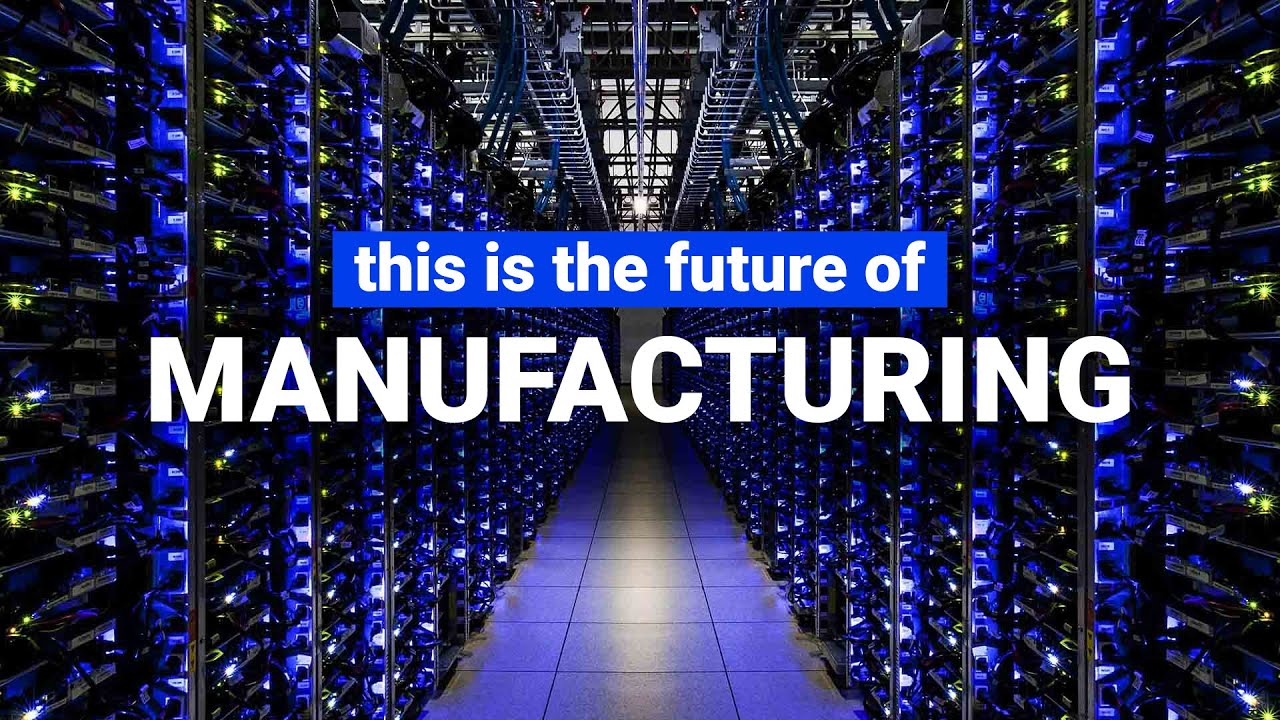
Future of manufacturing is FOREVER changed! Industry 4.0 & Smart Manufacturing | EXPLAINED

Sentury Tire Thailand Factory

15.2.5 Virtual tools in sustainable production systems development

An Introduction to Additive Manufacturing/3D Printing
5.0 / 5 (0 votes)