Future of manufacturing is FOREVER changed! Industry 4.0 & Smart Manufacturing | EXPLAINED
Summary
TLDRIndustry 4.0 transforms manufacturing with five key pillars: Kaizen and 6S for continuous improvement and an organized workspace; Connected Systems for real-time data sharing across devices; Data Transparency to enhance visibility and problem-solving; Automation to take over repetitive tasks, increasing efficiency; and Machine Learning to predict and prevent disruptions. These pillars integrate technology and smart systems to reduce waste, improve decision-making, and optimize production, helping businesses achieve faster, more cost-effective product development.
Takeaways
- 😀 Industry 4.0 is the integration of connected digital technologies and methodologies to optimize manufacturing processes.
- 😀 The goal of Industry 4.0 is to reduce waste, defects, allocate resources efficiently, lower production lead times, and reduce costs.
- 😀 Kaizen, meaning continuous improvement, is a key principle of Industry 4.0, supported by the 6S methodology for maintaining an organized and efficient workplace.
- 😀 The 6S methodology involves Sorting, Shining, Sustaining, Safeguarding, Setting in Order, and Standardizing for better workplace discipline and improvement.
- 😀 Connected Systems leverage the Industrial Internet of Things (IIoT) to enable real-time data sharing between machines, products, and operators.
- 😀 IIoT provides valuable insights into raw material usage, machine downtime, production bottlenecks, and more, aiding in smarter decision-making.
- 😀 Data Transparency in Industry 4.0 ensures that operators can view real-time information on task progress, inventory, machine status, and lead times.
- 😀 With greater transparency, operators can easily identify and resolve production issues, such as bottlenecks or delays at workstations.
- 😀 Automation is used in routine tasks to improve reliability, consistency, and efficiency, while freeing human workers to focus on creative and problem-solving tasks.
- 😀 Machine Learning and AI enhance manufacturing systems by predicting and responding to issues, such as scheduling maintenance before tools wear out, reducing downtime and optimizing resource use.
Q & A
What is Industry 4.0?
-Industry 4.0 refers to a system of connected digital technologies that integrate the entire manufacturing ecosystem, aiming to improve efficiency, reduce waste, and streamline production processes through automation, data sharing, and smart decision-making.
What are the five pillars of Industry 4.0?
-The five pillars of Industry 4.0 are Kaizen and 6S, Connected Systems, Data Transparency, Automation, and Machine Learning.
How does Kaizen and 6S contribute to Industry 4.0?
-Kaizen focuses on continuous improvement through small, incremental steps, while 6S establishes an organized and disciplined workplace. These principles foster a culture of improvement that supports the efficient, smart manufacturing processes central to Industry 4.0.
What role do connected systems play in Industry 4.0?
-Connected systems enable real-time data sharing across machines, products, and operators through wireless sensors and the Industrial Internet of Things (IIOT), providing insights into production processes, machine maintenance needs, and resource allocation.
What is the importance of data transparency in Industry 4.0?
-Data transparency ensures that operators can access real-time data on key metrics, such as machine status, inventory, and lead times. This visibility helps identify issues quickly and make informed decisions to improve production efficiency.
How does automation improve manufacturing in Industry 4.0?
-Automation reduces human labor for repetitive or dangerous tasks, increasing reliability and consistency. It allows workers to focus on creative, problem-solving tasks while automated systems handle routine jobs, improving overall efficiency and reducing errors.
Can you give an example of automation in Industry 4.0?
-An example of automation in Industry 4.0 is the use of 3D scanners to measure parts in-line and detect non-conformities much faster than a human operator could, reducing errors and improving quality control.
How does machine learning contribute to Industry 4.0?
-Machine learning uses large datasets to anticipate and respond to emergent issues in the production process. It enables systems to predict tool maintenance needs or resource allocation, optimizing production and reducing downtime.
What is the significance of using machine learning for predictive maintenance?
-Machine learning enables predictive maintenance by forecasting when tools or machinery will need repair or replacement. This proactive approach minimizes unexpected downtime, preventing costly disruptions in production.
How does Industry 4.0 improve product development goals?
-Industry 4.0 improves product development by reducing production lead times, lowering costs, enhancing resource allocation, and increasing product quality through automation, data transparency, and connected systems.
Outlines
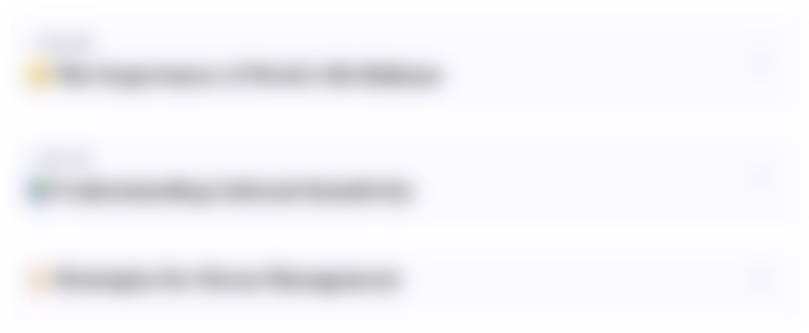
This section is available to paid users only. Please upgrade to access this part.
Upgrade NowMindmap
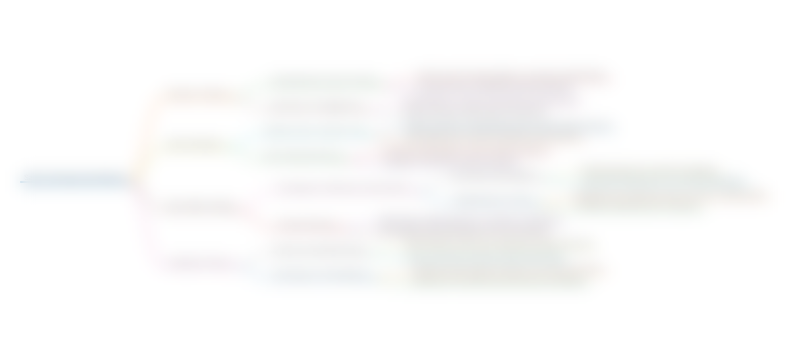
This section is available to paid users only. Please upgrade to access this part.
Upgrade NowKeywords
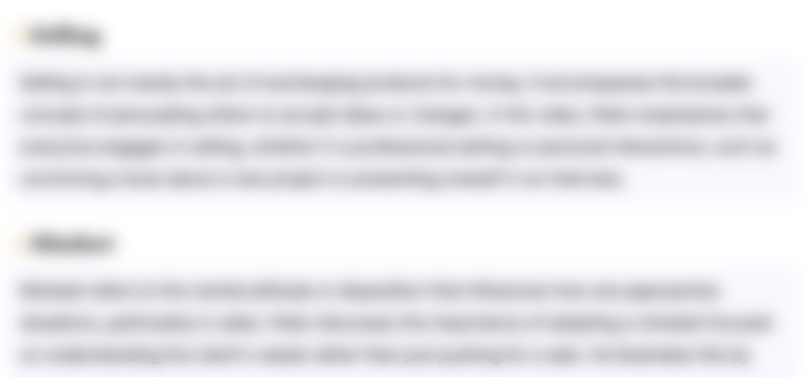
This section is available to paid users only. Please upgrade to access this part.
Upgrade NowHighlights
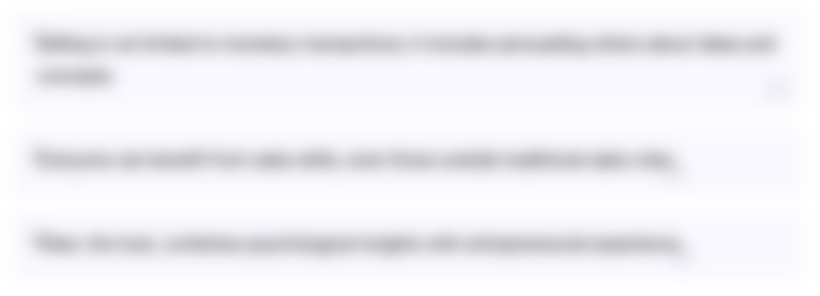
This section is available to paid users only. Please upgrade to access this part.
Upgrade NowTranscripts
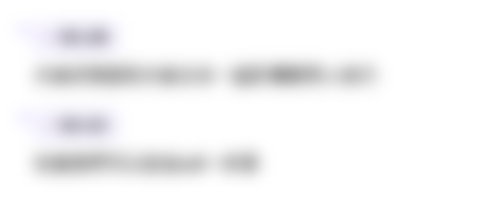
This section is available to paid users only. Please upgrade to access this part.
Upgrade NowBrowse More Related Video

The DIRTY Truth About EA's Layoffs & The Sims' Future! 😱

Data Analyst Roadmap 2024 | Data Analyst Weekly Study Plan | Free Resources to Become Data Analyst

E003 - NFA Form Types
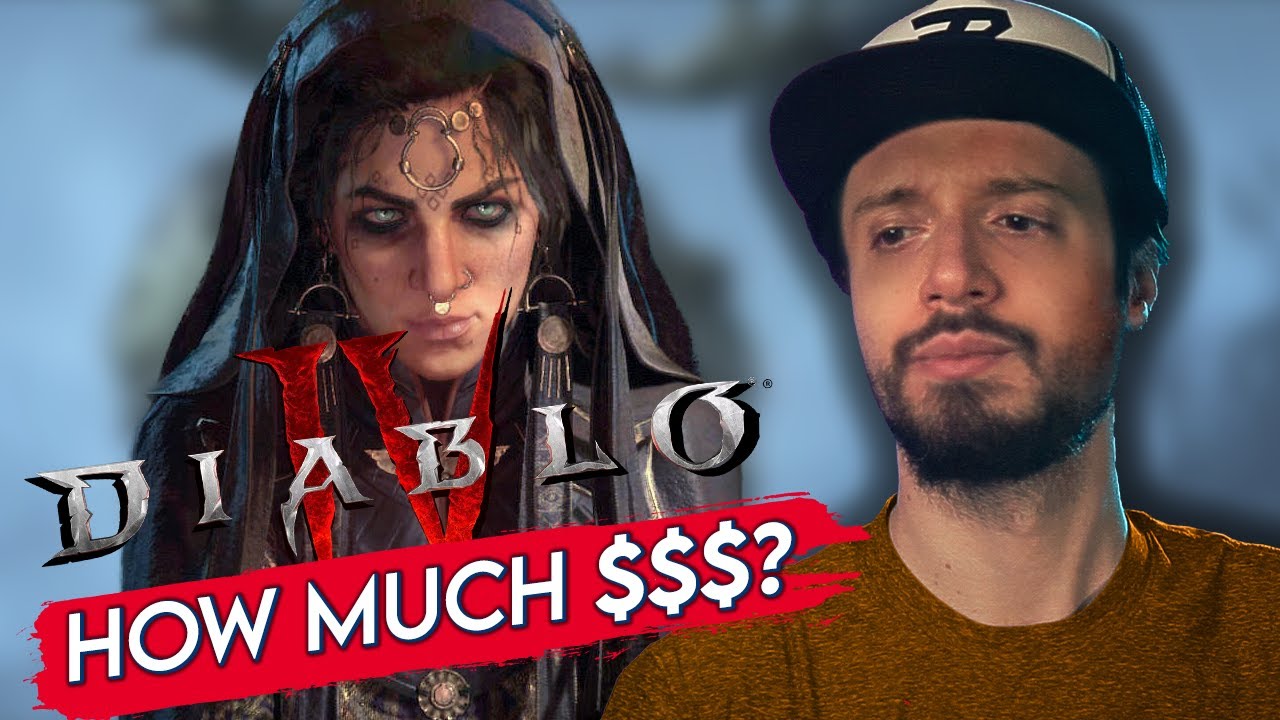
You Won't Believe these Diablo 4 Microtransaction Revenue Numbers

AI News: OpenAI & ChatGPT Surpassed AGAIN?!

VIDEO E003 eForms Types
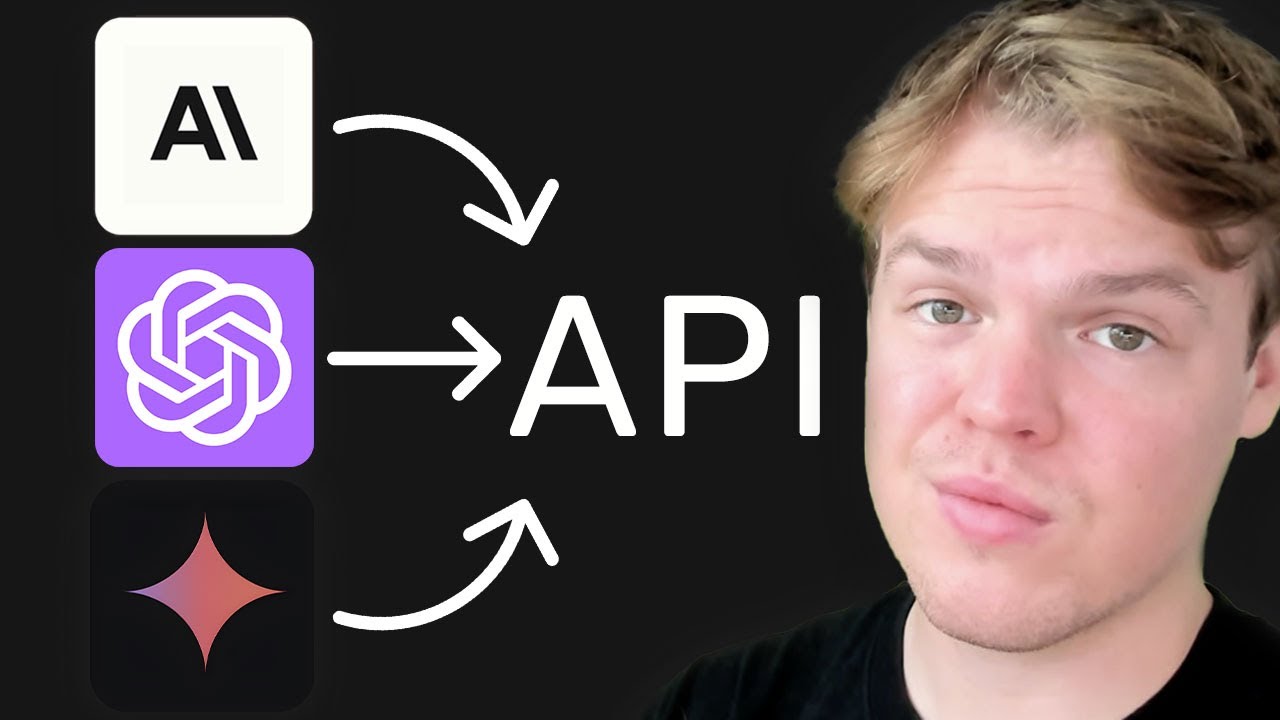
Which AI API is Best For Creating Software: OpenAI's ChatGPT, Google's Gemini, or Anthropic's Claude
5.0 / 5 (0 votes)