How Japanese Swords are Made
Summary
TLDRThis video script delves into the intricate art of sword-making, detailing the meticulous process from selecting raw materials like steel with precise carbon content to forging, annealing, and sharpening. It explores traditional methods like cementation and modern techniques such as laser cutting. The script also covers the historical evolution of sword materials, from copper and bronze to iron and steel, highlighting the Japanese katana's unique heat treatment. The journey concludes with the finishing touches, including adding a guard, pommel, and hilt, before the sword's final polish.
Takeaways
- ⚔️ Swords have been a central weapon in warfare across different geographical locations and time periods.
- 🔩 Modern swords are primarily made from steel, an alloy of carbon and iron, with carbon content carefully controlled between 0.6 to 0.9 percent for optimal properties.
- 🔨 Forging is a key process in sword making, where the steel is heated and hammered into shape, with techniques like stock removal for mass production and traditional forging for higher quality blades.
- 🌡️ Normalization and annealing are critical heat treatment steps that relieve stress, refine the steel's crystalline structure, and prepare the blade for sharpening.
- 🗡️ Sharpening is done using wet stones or electronic belt grinders, with different techniques for single or double-edged swords, and considerations for blade weight and handling.
- 🔥 Quenching and tempering harden the sword, with careful timing in a salt bath to ensure even cooling and maintain the blade's edge.
- 🏺 A unique heat treatment for Japanese katanas involves covering the unsharpened edge with clay to create a curve and enhance flexibility.
- 🛠️ Finishing touches include attaching a guard, pommel, and handle, with materials like leather or wire for grip and aesthetic purposes.
- ✅ The history of sword materials evolved from copper to bronze, then to iron, and finally to steel, with each material advancement improving the sword's durability and performance.
- 🤖 Contemporary sword making incorporates modern machinery and computer-guided lasers, streamlining the process from手工 labor to precision engineering.
Q & A
What is the first step in making a sword according to the script?
-The first step in making a sword is choosing and preparing the raw materials, which are typically steel alloys with precise carbon content.
What is the ideal carbon content percentage in steel for making swords?
-The ideal carbon content in steel for making swords is between 0.6 to 0.9 percent of the total alloy.
How does the process of cementation add carbon to steel?
-Cementation is a process where pieces of steel are placed in a container with high carbon content, and heated to a high temperature for several days, allowing carbon to migrate into the steel.
What is the purpose of normalization in the sword-making process?
-Normalization is a process where the sword is heated and then cooled without hammering, allowing the crystalline structure of the steel disrupted by hammering to return to normal.
What is annealing and how does it prepare the blade for sharpening?
-Annealing is a process where the blade is heated to a high temperature and cooled very slowly, which removes internal stresses and makes the blade soft and easy to sharpen.
How is a sword sharpened in the traditional method?
-In the traditional method, a sword is sharpened using a wet stone, which can be done by hand or with the aid of an electric belt grinder.
What is the purpose of quenching and tempering in the sword-making process?
-Quenching and tempering harden the sword after it has been sharpened. Quenching involves rapid cooling in a quench tank, while tempering involves heating the blade to a lower temperature and quenching it again to achieve the desired hardness.
Why do Japanese swordsmiths cover the unsharpened edge of the sword with clay during heat treatment?
-Japanese swordsmiths cover the unsharpened edge with clay to slow down the cooling on one side, which helps the blade curve and adds flexibility, potentially helping it stay sharper for longer.
What materials were used to make swords before the widespread use of steel?
-Before steel, materials used to make swords included copper, bronze (an alloy of tin and copper), and iron.
How has the method of making swords evolved over time according to the script?
-The method of making swords has evolved from hand-cutting and forging to using modern machinery and computer-guided lasers for more precise and efficient production.
What are the final steps in finishing a sword after it has been sharpened?
-The final steps in finishing a sword include attaching a metal guard, adding a pommel or counterweight, adding clumps or wood to the hilt, and etching the company logo or trademark using electrochemical techniques.
Outlines
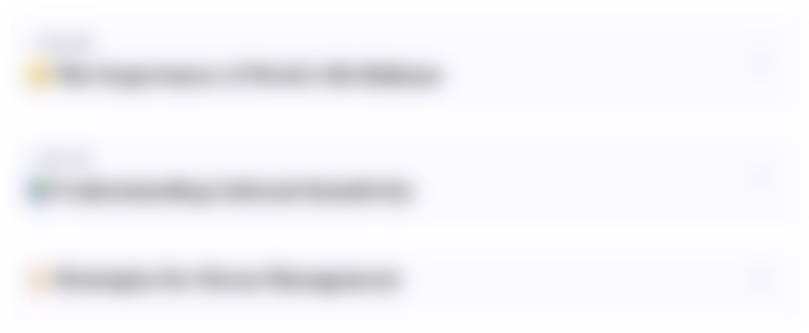
This section is available to paid users only. Please upgrade to access this part.
Upgrade NowMindmap
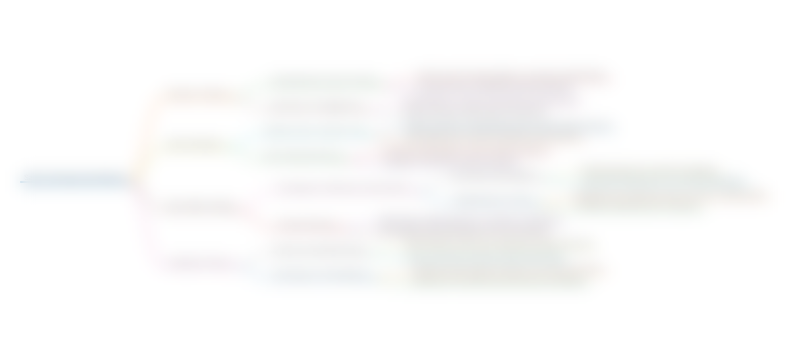
This section is available to paid users only. Please upgrade to access this part.
Upgrade NowKeywords
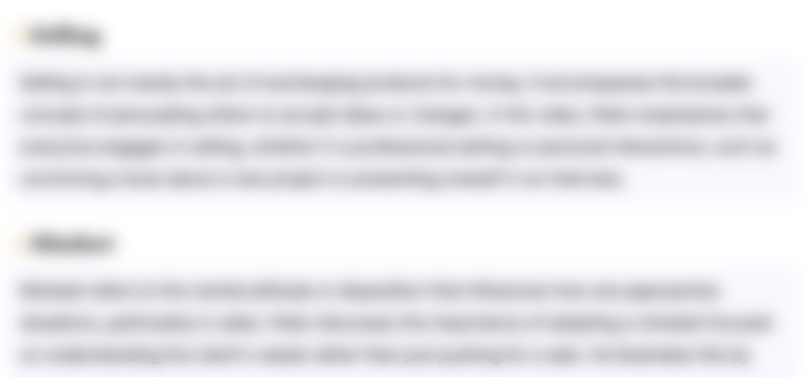
This section is available to paid users only. Please upgrade to access this part.
Upgrade NowHighlights
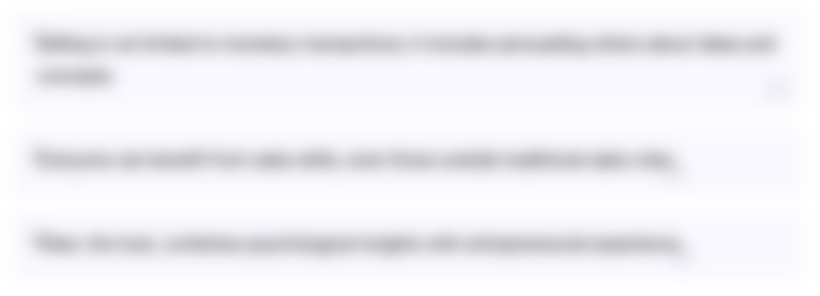
This section is available to paid users only. Please upgrade to access this part.
Upgrade NowTranscripts
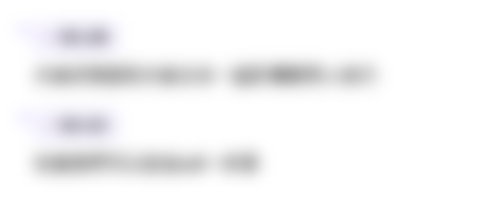
This section is available to paid users only. Please upgrade to access this part.
Upgrade NowBrowse More Related Video

Forging An Ancient Samurai Sword: The Art Of Making A Japanese Katana | BBC Documentary
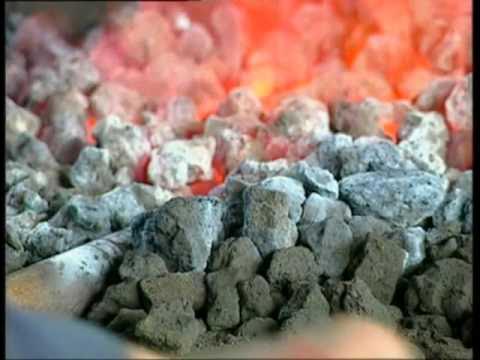
MOTORI CHE PASSIONE RAI 2 GABRIELE GNANI 1/3

Begini Proses Pembuatan KUJANG, Senjata Tradisional Sunda | TAU GAK SIH (08/01/21)
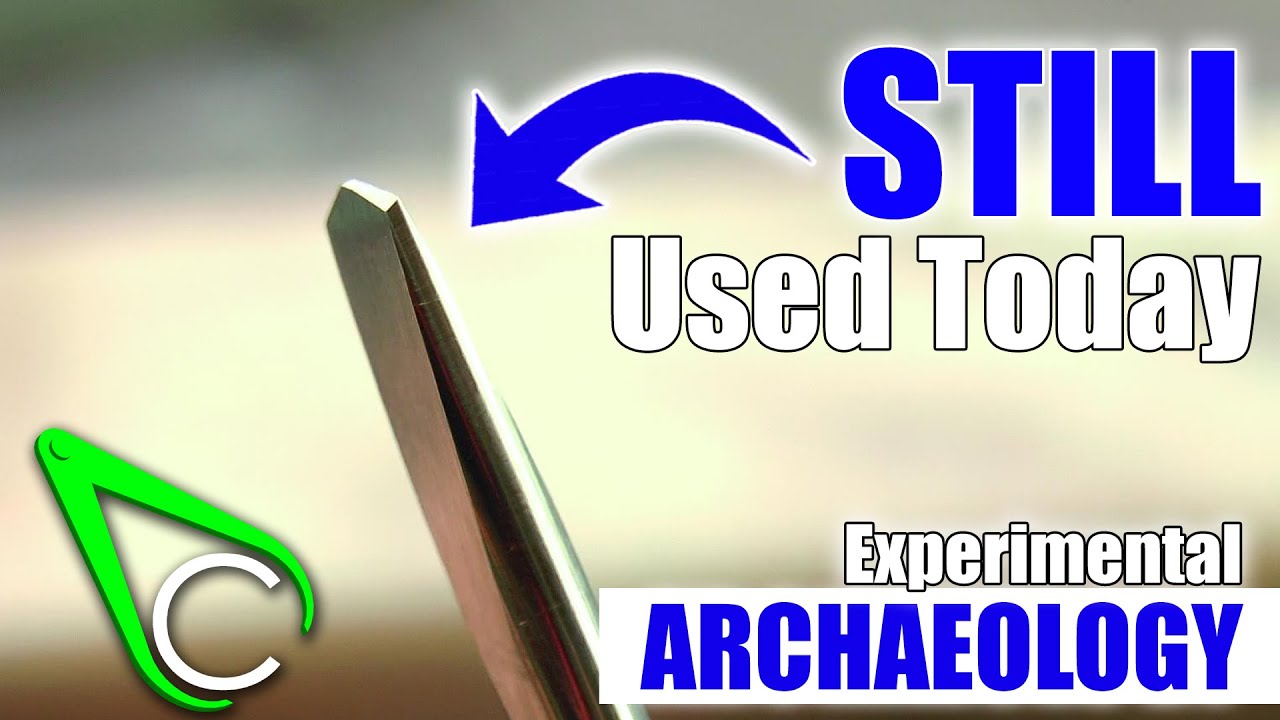
Antikythera Fragment #5 - Ancient Tool Technology - The First Precision Drill Bit

STEEL: From Start to Finish

Making Manuscripts
5.0 / 5 (0 votes)