Maintenance Management Overview
Summary
TLDRThe video script emphasizes the importance of scheduling maintenance work weekly and documenting it to improve operational efficiency. It highlights the need for better parts management, including predictive usage, cost control, and consignment stock for frequently replenished items. Effective communication between the supply chain and maintenance teams, along with labor utilization and resource planning, are key to reducing downtime and enhancing production and safety.
Takeaways
- 📅 Regularly scheduled maintenance work is essential and should be planned on a weekly basis.
- 📝 A documented work schedule is produced each week, which is a best practice for maintenance planning.
- 🔍 The work schedule is developed by identifying all authorized and uncompleted maintenance orders, as well as predictive and preventative maintenance work due within the next four scheduling periods.
- 💰 Good planning helps improve parts management and control the cost of spare parts, including safety spares, critical spares, and on-demand orders.
- 🔑 Better parts usage predictions are needed to manage the warehousing costs and to understand the cost implications of not having a part when needed.
- 🚫 Identifying opportunities for consignment stock can improve parts availability for frequently depleted and replenished small parts, which may not be cost-effective to track in detail.
- 🗣️ Improving communication between the supply chain and maintenance departments through documentation and history of issues can lead to better collaboration and problem-solving.
- 🤝 Weekly meetings between the supply chain and maintenance teams can help align goals and improve communication for a more efficient operation.
- 👷♂️ Good planning also helps control labor costs by ensuring labor utilization is optimized and workers are not idle due to waiting for parts.
- 🛠️ Streamlining labor and equipment constraints, such as missing or wrong equipment, can enhance the efficiency of maintenance operations.
- 🔮 Future forecasting based on schedules and planning allows for better resource allocation, ensuring the right number of people with the necessary skills are available for upcoming tasks.
Q & A
What is the primary purpose of scheduling maintenance work on a weekly basis?
-The primary purpose is to ensure that maintenance tasks are planned and documented, which helps in following best practices and improving overall work efficiency.
How is a work schedule developed according to the script?
-A work schedule is developed by identifying all authorized and uncompleted maintenance orders, predictive and preventative maintenance work due within the next four scheduling periods, and budgeted major work.
What is the relationship between good planning and parts management?
-Good planning helps improve parts management by ensuring better scheduling and control over the cost of spare parts, whether they are safety spares, critical spares, or ordered on demand.
Why is it important to have better parts usage predictions?
-Better parts usage predictions are important for controlling the cost of spare parts and for identifying opportunities for consignment stock, which can lead to cost savings and improved parts availability.
What is the significance of identifying opportunities for consignment stock?
-Identifying opportunities for consignment stock is significant because it allows for the efficient management of small parts that are frequently depleted and replenished, without the need for detailed tracking, which may not be cost-effective.
How can communication between the supply chain and maintenance departments be improved?
-Communication can be improved by documenting and maintaining a history of issues, having weekly meetings between the supply chain and maintenance departments, and aligning goals to ensure the site runs smoothly and production is maintained.
What is the role of labor utilization in maintenance work?
-Labor utilization is crucial in maintenance work to ensure that workers are not idle due to waiting for parts or equipment, thereby streamlining labor constraints and avoiding productivity losses.
How can good planning help in controlling labor costs?
-Good planning helps in controlling labor costs by ensuring that labor requirements are well-forecasted and organized, preventing idle time and optimizing the use of available workforce.
What is the importance of resource planning in maintenance scheduling?
-Resource planning is important as it allows for the efficient utilization of available equipment and the better organization and scheduling of maintenance tasks, which can prevent equipment blockages and improve overall maintenance efficiency.
How does the script suggest improving parts availability?
-The script suggests improving parts availability by enhancing communication between the supply chain and maintenance, using documented history of issues to inform improvements, and considering consignment stock for frequently used parts.
What is the impact of not having a required part when equipment breaks down?
-Not having a required part when equipment breaks down can lead to production losses, increased downtime, and potential safety risks, emphasizing the importance of effective parts management and planning.
Outlines
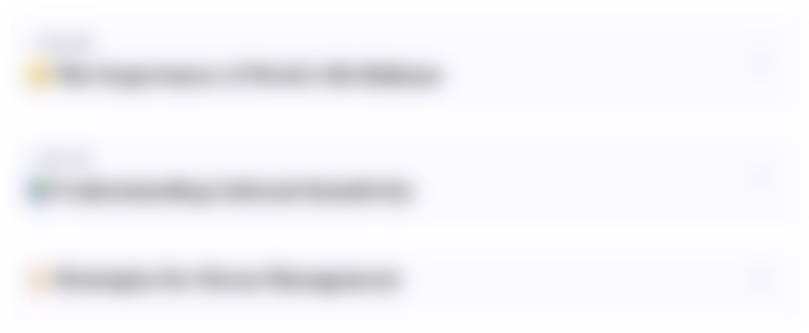
This section is available to paid users only. Please upgrade to access this part.
Upgrade NowMindmap
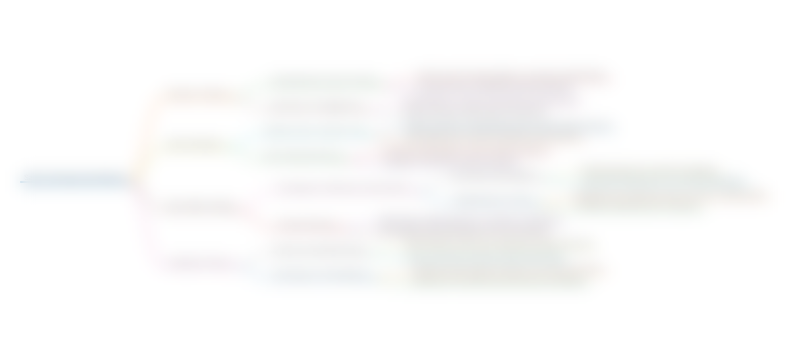
This section is available to paid users only. Please upgrade to access this part.
Upgrade NowKeywords
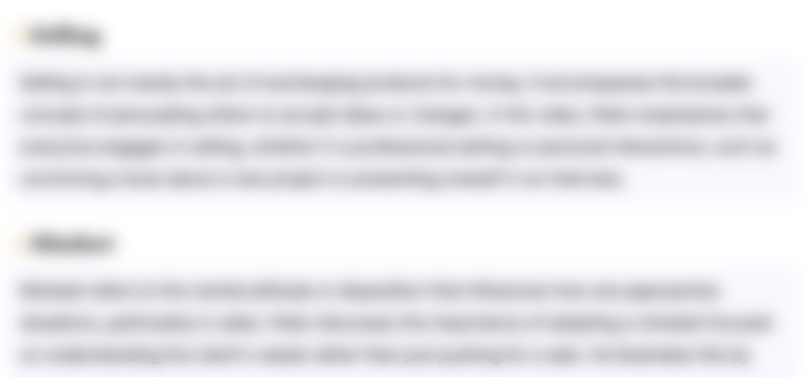
This section is available to paid users only. Please upgrade to access this part.
Upgrade NowHighlights
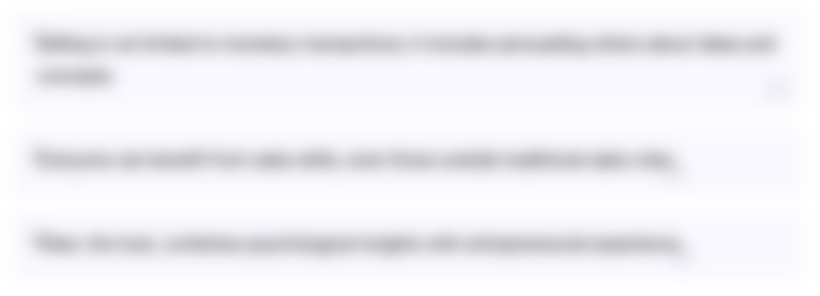
This section is available to paid users only. Please upgrade to access this part.
Upgrade NowTranscripts
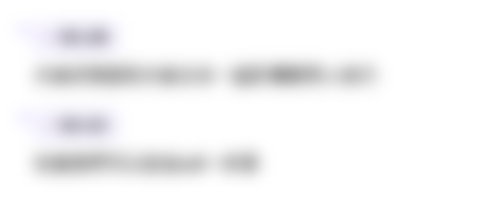
This section is available to paid users only. Please upgrade to access this part.
Upgrade NowBrowse More Related Video
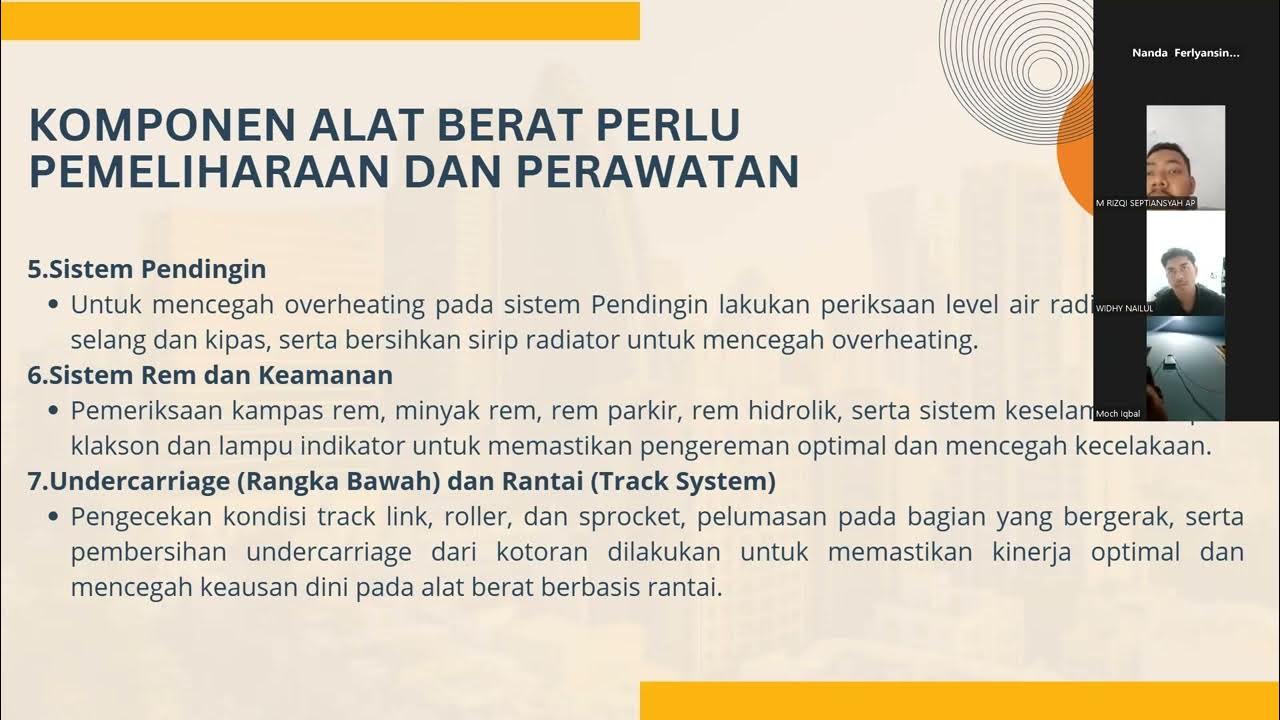
Video Presentasi Kelompok 7 Pemeliharaan dan Perawatan pada Alat Berat
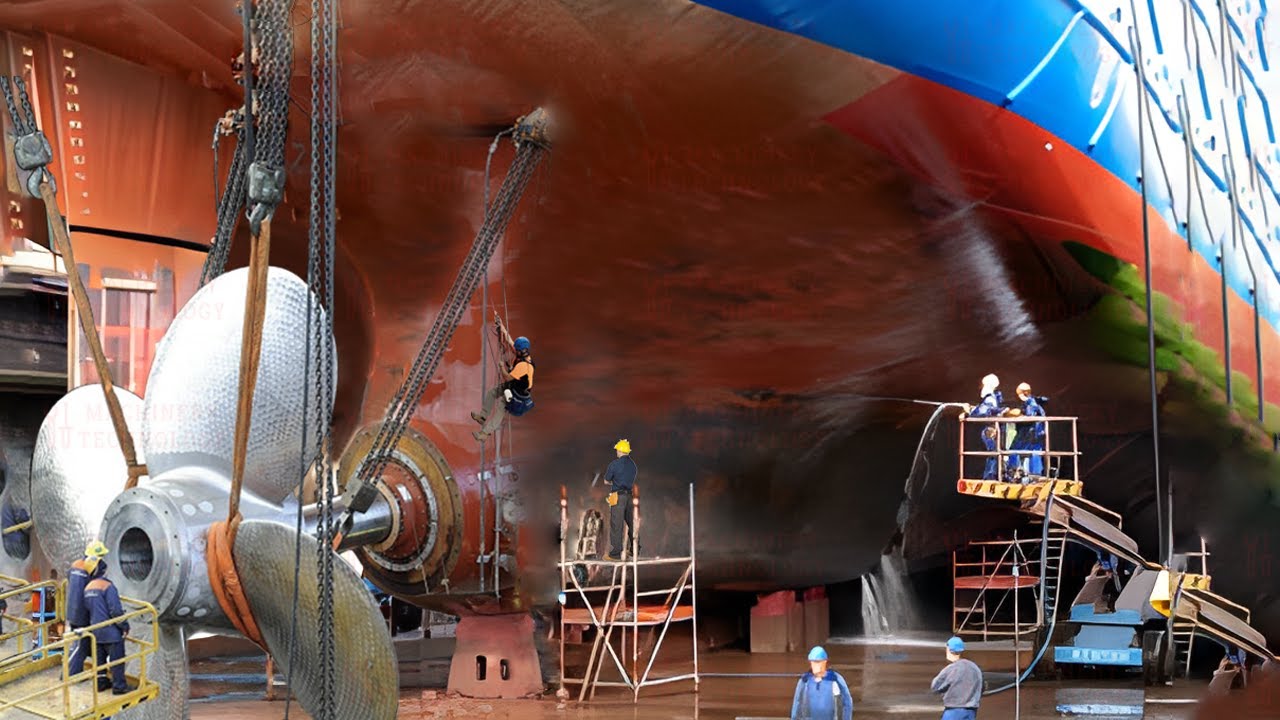
Amazing Process Of Maintaining And Repairing Ships - Satisfying Ship Maintenance Techniques

Video Pembelajaan mapel Pemeliharaan dan Perbaikan Peralatan Elektronika Industri Fase F

O que é PCM?🔩PLANEJAMENTO E CONTROLE DA MANUTENÇÃO | Modular Cursos

Maintenance Management System
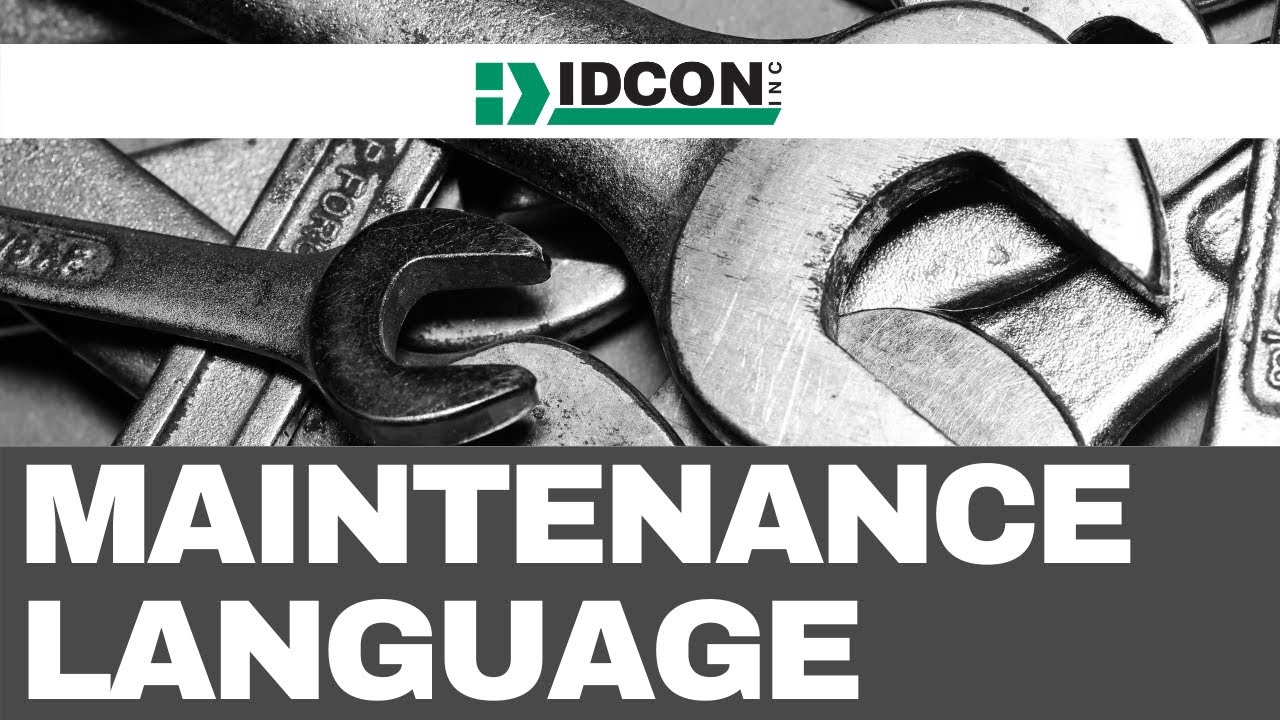
Maintenance Language
5.0 / 5 (0 votes)