Video Pembelajaan mapel Pemeliharaan dan Perbaikan Peralatan Elektronika Industri Fase F
Summary
TLDRThis video focuses on the importance of Standard Operating Procedures (SOPs) in the maintenance and repair of industrial electronic equipment. It explains the principles, functions, and benefits of SOPs, highlighting their role in ensuring legal compliance, improving work efficiency, and preventing task overlap. The video also covers equipment documentation, including work orders, maintenance history, and trouble report cards. Additionally, it discusses tools used in workshops and the significance of planned maintenance for cost efficiency and equipment longevity. Ultimately, the video emphasizes the importance of systematic procedures in maintaining high operational standards.
Takeaways
- ๐ SOPs (Standard Operating Procedures) provide guidelines for operational activities in companies and organizations.
- ๐ The purpose of SOPs includes helping workers understand tasks, facilitating adaptation for new employees, and achieving company targets.
- ๐ SOPs create standardization, prevent overlapping tasks, and help improve performance by offering clear, legal guidelines.
- ๐ Equipment documents, such as work orders, are crucial for managing and tracking maintenance and repair activities.
- ๐ The maintenance history book keeps records of all maintenance work and can be referred to for future repairs or audits.
- ๐ Trouble report cards contain detailed records of equipment damages, repairs, and performance evaluations.
- ๐ Proper workshop work tools, such as mechanical tools and electrical test instruments, are essential for efficient maintenance and repairs.
- ๐ A well-structured work implementation plan, including planned maintenance, helps minimize costs and optimize repair schedules.
- ๐ Routine repairs are more cost-effective than emergency repairs, and planned maintenance allows for better equipment adjustments.
- ๐ Safety, efficiency, and cost management are key components when carrying out maintenance tasks and evaluations.
Q & A
What is the main purpose of Standard Operating Procedures (SOPs) in industrial maintenance?
-The main purpose of SOPs in industrial maintenance is to provide implementation guidelines for operational activities, ensuring tasks are performed efficiently, effectively, and safely.
What are the key functions of Standard Operating Procedures (SOPs)?
-The key functions of SOPs include serving as a legal basis for operations, providing a reference or guideline for employees, offering detailed work instructions, and ensuring standardized performance across tasks.
What are the principles to follow when creating an SOP?
-The principles for creating an SOP include ensuring it is easy to understand for all involved, making it efficient and effective, and ensuring it provides legal certainty in case of violations.
What are the benefits of using SOPs in industrial operations?
-The benefits of SOPs include preventing overlapping tasks, creating standardization for performance evaluation, improving overall performance, and providing evidence that the organization is well-managed and efficient.
What documents are typically included in the SOP for maintenance and repair activities?
-Documents typically included are work orders, maintenance history books, back notes, and performance evaluations of maintenance activities, all of which provide essential details about work requests, actions taken, and equipment status.
How is a work request converted into a work order in the SOP?
-A work request, once signed by management, becomes a work order. This work order details the maintenance or repair activities to be performed, including the history and background of the equipment.
What is the purpose of a trouble report card in SOPs?
-A trouble report card is a document that records information about work done on equipment, including service repairs, damages, causes of failure, repair actions, and the costs and time involved.
What are some common mechanical tools used in the maintenance workshop?
-Common mechanical tools in the workshop include screwdrivers, pliers, keys, spanners, hammers, saws, soldering irons, and attractors, which are essential for performing various maintenance tasks.
What electrical test tools are used in the maintenance workshop?
-Electrical test tools used in the workshop include multimeters, analog and digital frequency meters, and water testers, which help in testing and diagnosing electrical issues.
What are the advantages of planned maintenance over unplanned maintenance?
-Planned maintenance offers advantages such as lower costs, fewer unexpected repairs, better equipment adjustments according to schedule, and more predictable budgeting for maintenance activities.
Outlines
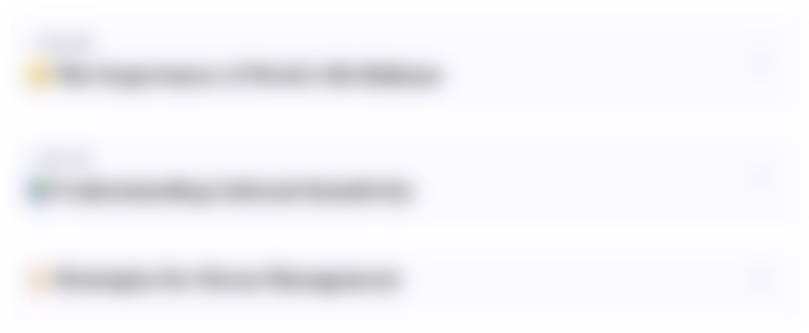
This section is available to paid users only. Please upgrade to access this part.
Upgrade NowMindmap
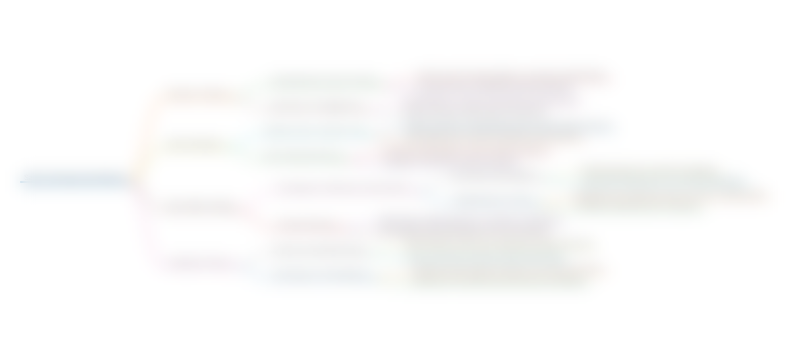
This section is available to paid users only. Please upgrade to access this part.
Upgrade NowKeywords
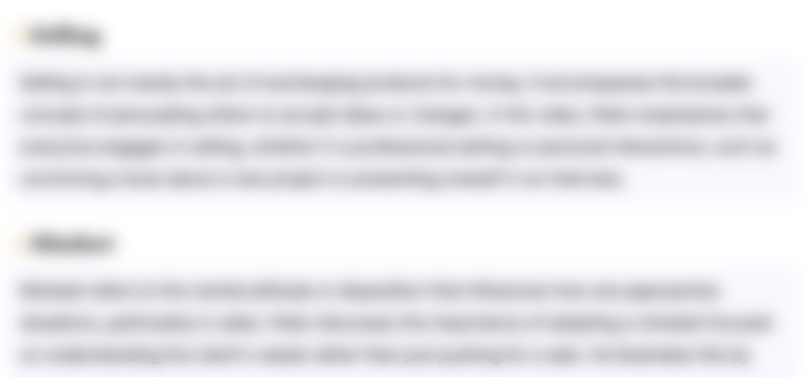
This section is available to paid users only. Please upgrade to access this part.
Upgrade NowHighlights
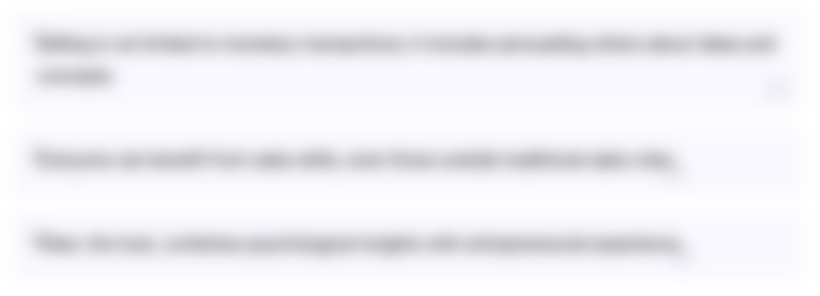
This section is available to paid users only. Please upgrade to access this part.
Upgrade NowTranscripts
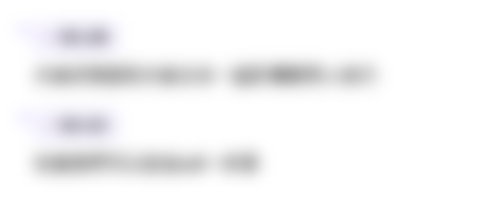
This section is available to paid users only. Please upgrade to access this part.
Upgrade Now5.0 / 5 (0 votes)