How to Safely Isolate Machinery Onboard Ship? (Lock-Out Tag-Out System)
Summary
TLDRThis maritime training video outlines the critical lockout and tag out system for safely isolating machinery on ships during maintenance. It emphasizes the importance of administrative control through warning tags and physical prevention methods like lockout devices. The video demonstrates correct procedures, documentation, and authorization processes for electrical, hydraulic, and other pressurized systems, ensuring safety and compliance with regulations.
Takeaways
- 🔒 The lockout and tag out system is a crucial safety measure to control machinery on board a ship when it is switched off for repair or maintenance.
- 📝 A tag out system is an administrative control that involves placing warning tags on the means of machine or power isolation to inform others that the machinery is being worked on and should not be restarted.
- 🚫 Violation of the lockout and tag out rules should be met with severe disciplinary action and retraining to ensure the safety protocol is strictly followed.
- 📜 The tag must include the name of the person who placed it, the reason for isolation, the date, and contact details, and should be recorded in the logbook upon completion of work.
- ⚠️ Operating machinery on a ship carries inherent risks, and safety measures are essential to prevent injury or death when machinery is being serviced.
- 🚫 Inadequate safety measures, such as using loose pieces of paper for isolation, are unacceptable and do not meet the required safety standards.
- 🔌 When machinery is being serviced, it must be effectively isolated from its power source, and a warning tag must be placed at the point of connection to prevent accidental reactivation.
- 🔐 Physical preventive methods, such as lockout provisions on switches and valves, are essential to ensure that machinery cannot be reconnected to its power source during maintenance.
- 🔑 The lockout and tag out procedure must be authorized, especially in planned maintenance or shipyard repair work, within the framework of a recognized safety system like permit to work.
- 👥 In situations where multiple engineers work on the same equipment, each must place their own lockout device and tag, ensuring that isolation is only removed by the person who applied it.
- 📋 The lockout tag out record sheet is vital for documenting the equipment being worked on, the locking devices and tags used, their locations, applicators, and installation dates, ensuring traceability and accountability.
Q & A
What is the primary purpose of the lockout and tag out system on board a ship?
-The primary purpose of the lockout and tag out system is to ensure safety during repair or maintenance by controlling machinery that has been switched off, preventing it from being reactivated accidentally.
What does the tag out system represent in terms of safety measures?
-The tag out system represents the administrative control of the lockout and tag out system, involving placing a warning tag on the machinery or power isolation to inform others that the system is being worked on and should not be reactivated.
What should be included on a warning tag in a lockout and tag out system?
-A warning tag should include the name of the person who placed it, the reason for the isolation, the date it was placed, and additional information such as department and contact details.
What are the consequences of violating the lockout and tag out rules?
-Violation of the lockout and tag out rules can result in severe disciplinary action and retraining for the individual responsible.
Why is it necessary to record the lockout and tag out safety system in the logbook?
-Recording the lockout and tag out system in the logbook ensures that there is a documented record of when and by whom the machinery was isolated and when it was safe to reactivate, enhancing traceability and accountability.
What are the potential hazards of machinery that has been switched off for maintenance or repair?
-The potential hazards include the risk of someone restarting the machinery unaware that it is being worked on, which can lead to damage, injury, or even death.
What is considered an inadequate method for enforcing a major safety measure in the context of the script?
-An inadequate method mentioned in the script is the reliance on handwritten pieces of paper loosely attached to the means of energy isolation.
What is the golden rule when it comes to warning tags in the lockout and tag out system?
-The golden rule is that if you did not place the tag yourself, you must not remove it.
What is the second tier of safety in the lockout and tag out system?
-The second tier of safety is the physical prevention system, which involves locking the isolating device in the shut-off position, removing the key, and placing a warning tag on the device.
What is required for a lockout and tag out procedure in the case of planned maintenance or shipyard repair work?
-A lockout and tag out procedure must be determined within the framework of a recognized safety system such as a permit to work, authorized by the chief engineer and the superintendent.
What steps should be taken before starting work on isolated equipment?
-Before starting work, verify that the equipment has been disconnected from all energy sources, isolated, and locked out, and use the appropriate test method to confirm the system is no longer energized.
How should multiple engineers working on the same equipment handle the lockout and tag out system?
-Each engineer should place their own lockout device and tag on the isolator, to be removed only by themselves after their job has been completed.
What is the final step in the lockout and tag out process after completing the work?
-The final step is to clear the lockout action by recording completion on the lockout tag out record sheet and re-energizing the equipment safely.
Outlines
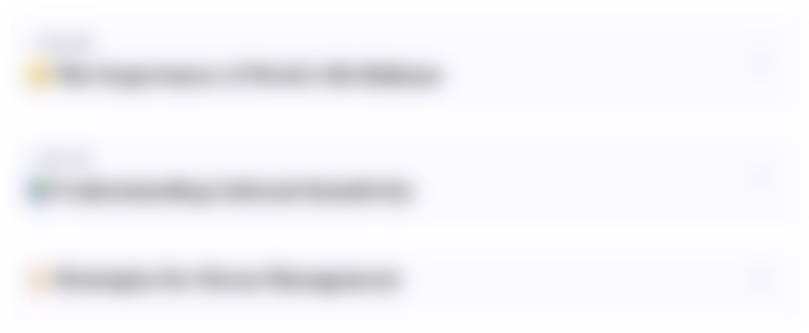
Этот раздел доступен только подписчикам платных тарифов. Пожалуйста, перейдите на платный тариф для доступа.
Перейти на платный тарифMindmap
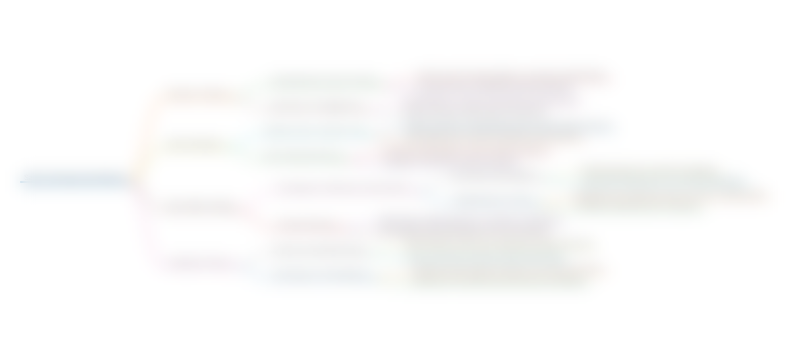
Этот раздел доступен только подписчикам платных тарифов. Пожалуйста, перейдите на платный тариф для доступа.
Перейти на платный тарифKeywords
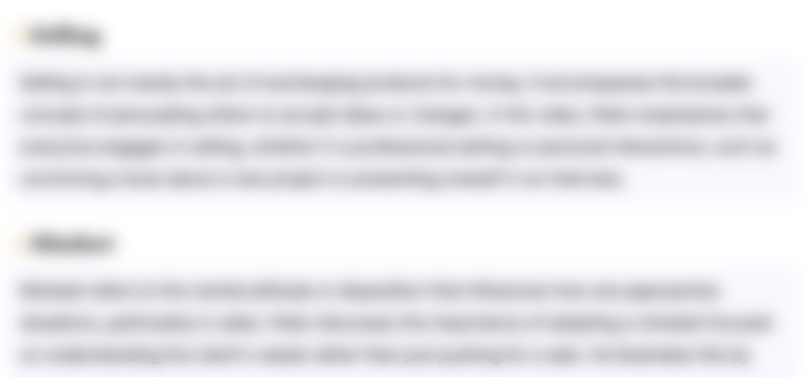
Этот раздел доступен только подписчикам платных тарифов. Пожалуйста, перейдите на платный тариф для доступа.
Перейти на платный тарифHighlights
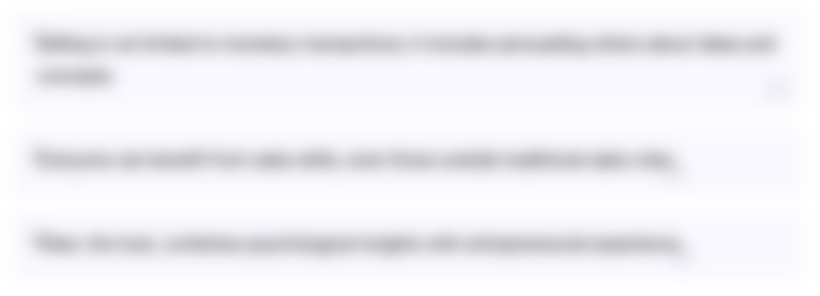
Этот раздел доступен только подписчикам платных тарифов. Пожалуйста, перейдите на платный тариф для доступа.
Перейти на платный тарифTranscripts
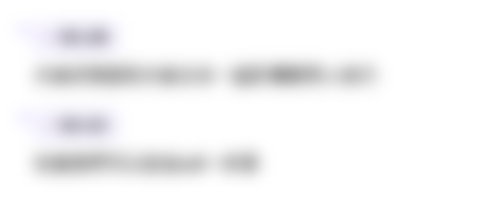
Этот раздел доступен только подписчикам платных тарифов. Пожалуйста, перейдите на платный тариф для доступа.
Перейти на платный тариф5.0 / 5 (0 votes)