Managing Your Assets 05 - The Parts You Need, When You Need Them
Summary
TLDRThis video script discusses strategies for managing spare parts and inventory in a manufacturing setting. It highlights the importance of having adequate spares, tracking parts usage, and automating inventory management. The video explores the benefits of Parts Management Agreements (PMAs), which allow parts to be stored on-site without upfront costs, with warranties starting when the parts are used. It also delves into modern Vendor Managed Inventory (VMI) systems, which optimize stock levels based on actual usage, and automated solutions like RFID and smart lockers to streamline inventory processes and improve efficiency.
Takeaways
- 😀 Ensure critical spare parts are always available and have backups ready to minimize manufacturing downtime.
- 😀 Track the condition and stock levels of spare parts in the storeroom to prevent shortages or obsolete components.
- 😀 A shortage of spares or reliance on discontinued parts can significantly increase the risk of extended downtime in manufacturing processes.
- 😀 Consider implementing a Parts Management Agreement (PMA) to avoid upfront costs and only pay for parts when they are used.
- 😀 With PMA, spare parts remain on-site without starting the warranty clock until the parts are put into use, reducing unnecessary expenses.
- 😀 Unused or unneeded parts under a PMA can be returned or moved, further reducing costs and capital investment.
- 😀 Vendor Managed Inventory (VMI) improves spare parts management by tracking actual usage patterns and adjusting inventory levels accordingly.
- 😀 VMI ensures that the right amount of inventory is always available, reducing the need to keep excessive stock on hand.
- 😀 Advanced automation in storeroom management (e.g., RFID tags, smart lockers) can streamline processes and reduce manual errors.
- 😀 Automating storeroom operations helps track parts more efficiently, linking them directly to specific projects or cost centers to improve inventory management.
Q & A
Why is it important to assess the condition and quantity of spare parts in a facility?
-Assessing the condition and quantity of spare parts is crucial to avoid extended downtime. If critical parts are unavailable or in poor condition, it can disrupt operations and cause delays in production, leading to potential losses.
What challenges arise when spare parts are discontinued and no longer available?
-When spare parts are discontinued, it becomes challenging to maintain operations. If these parts are essential and there are no available spares, it can increase the risk of downtime and complicate maintenance strategies.
What is a Parts Management Agreement (PMA), and how does it benefit manufacturers?
-A Parts Management Agreement (PMA) allows manufacturers to keep spare parts on-site at a lower cost without purchasing them upfront. The warranty for these parts only starts when they are used, offering flexibility and cost savings.
How does a PMA differ from traditional spare parts purchasing?
-Unlike traditional purchasing where parts are bought upfront, a PMA allows manufacturers to only pay for parts when they are used, reducing upfront costs and offering flexibility to return unused or unnecessary parts.
What role does Vendor Managed Inventory (VMI) play in spare parts management?
-VMI helps optimize spare parts inventory by tracking actual usage patterns and adjusting stock levels accordingly. It ensures that parts are available when needed without overstocking, reducing storage costs and waste.
How does dynamic inventory management work in VMI systems?
-Dynamic inventory management in VMI systems adjusts inventory levels based on actual usage. Instead of maintaining fixed quantities, it tracks how often parts are used and ensures the right amount is always available, minimizing waste and cost.
What is the advantage of using RFID technology in inventory management?
-RFID technology offers real-time tracking of parts, automating the process of inventory management. It helps ensure parts are correctly accounted for, reduces human error, and provides immediate updates on stock levels.
How can automated lockers improve inventory management in a storeroom?
-Automated lockers enhance inventory management by requiring employees to request parts through a system that logs the part usage and links it to specific projects or cost centers. This reduces errors and ensures proper tracking of parts.
What is the benefit of not having to keep large quantities of parts on-site, as suggested in the VMI approach?
-By not maintaining large quantities of parts on-site, companies can reduce storage costs and minimize waste. VMI allows for parts to be ordered as needed, ensuring efficient inventory levels and freeing up space.
How can a company manage spare parts when a manufacturing line is sold or decommissioned?
-In such cases, parts under a PMA can be removed from the agreement, avoiding unnecessary costs for unused spares. This provides flexibility as parts can be moved out of the agreement once they are no longer needed.
Outlines
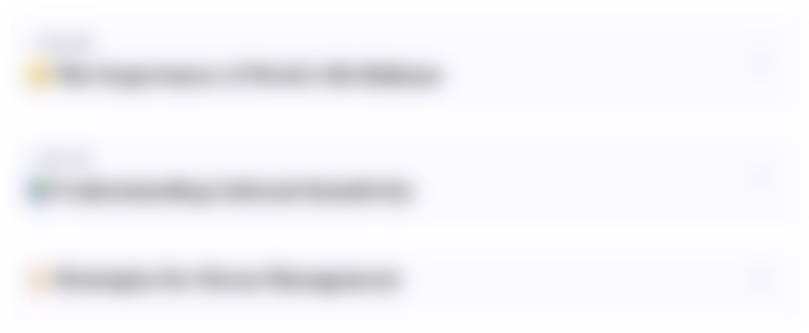
Этот раздел доступен только подписчикам платных тарифов. Пожалуйста, перейдите на платный тариф для доступа.
Перейти на платный тарифMindmap
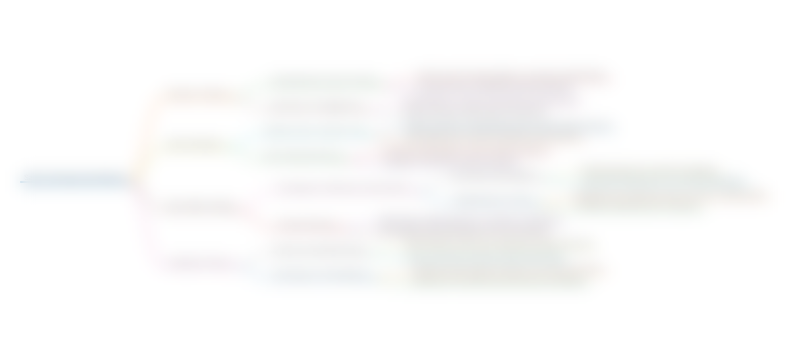
Этот раздел доступен только подписчикам платных тарифов. Пожалуйста, перейдите на платный тариф для доступа.
Перейти на платный тарифKeywords
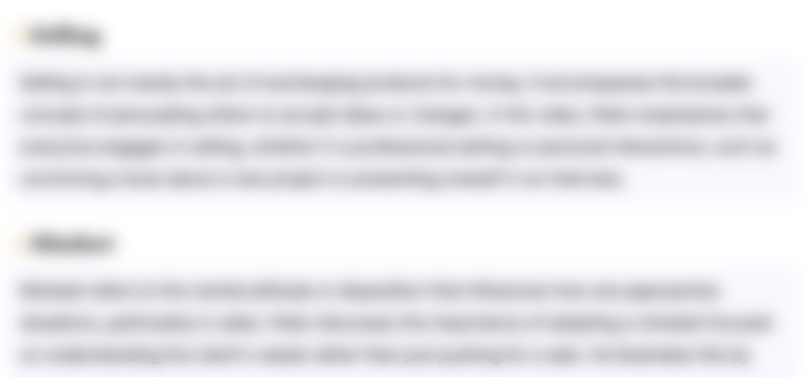
Этот раздел доступен только подписчикам платных тарифов. Пожалуйста, перейдите на платный тариф для доступа.
Перейти на платный тарифHighlights
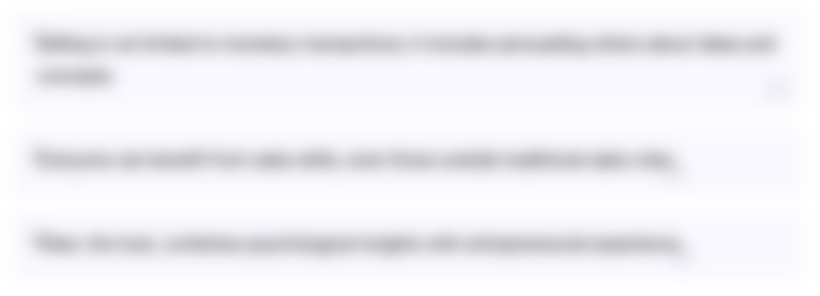
Этот раздел доступен только подписчикам платных тарифов. Пожалуйста, перейдите на платный тариф для доступа.
Перейти на платный тарифTranscripts
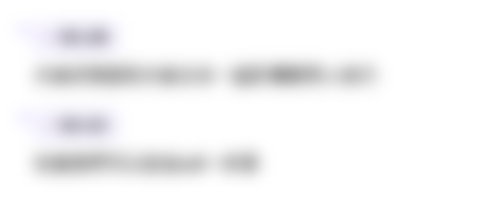
Этот раздел доступен только подписчикам платных тарифов. Пожалуйста, перейдите на платный тариф для доступа.
Перейти на платный тарифПосмотреть больше похожих видео
5.0 / 5 (0 votes)