Part A explained - Tunnel Cable Bracket
Summary
TLDRIn this video, the speaker provides an overview of a level three engineering paper focused on redesigning a tunnel bracket that supports high-voltage insulated cables. The bracket is attached to a metal support inside a tunnel, and the current design uses low-carbon steel with a painted finish. The speaker explores the mechanical aspects, material considerations, and potential risks, including the impact of cable movement, corrosion, and the durability of the painted finish. Key challenges include ensuring the bracket’s strength, shock absorption, and minimizing risks associated with electrocution and cable wear.
Takeaways
- 😀 The tunnel bracket is used to support high-voltage electrical cables in a tunnel environment.
- 😀 The bracket is mechanically attached to a metal support, likely using nuts, bolts, or machine screws.
- 😀 The bracket is machined from low carbon steel, which is tough but not very hard and prone to wear over time.
- 😀 The number of brackets needed depends on the length of the tunnel, and they are typically manufactured in batches of thousands.
- 😀 A risk associated with the current design is the potential for electrocution or shock, especially during installation.
- 😀 The movement of the cable over time (due to vibration, atmospheric pressure, or passing vehicles/trains) could lead to insulation damage or wear.
- 😀 The low carbon steel used for the bracket has a painted finish, but this may not be durable enough to withstand wear, particularly in the hole where the cable passes.
- 😀 When the insulation on the cable is damaged, it could lead to electrical hazards, so minimizing this risk is crucial in the design.
- 😀 Consideration should be given to alternative materials that are less brittle and more shock absorbent than low carbon steel.
- 😀 The painted finish on the steel may not be durable enough for the bracket's long-term use, leading to concerns about the protective coating wearing away from the cable passage hole.
Q & A
What is the primary function of the tunnel bracket described in the video?
-The tunnel bracket is designed to mechanically support high-voltage insulated electrical cables running the length of a tunnel.
What materials are used to make the bracket, and why is low-carbon steel chosen?
-The bracket is machined from low-carbon steel, which is chosen for its toughness and reduced brittleness. It also has relatively low hardness, making it less prone to cracking under stress.
What is the potential risk associated with the high-voltage cables in the tunnel?
-The major risk is electrocution or electrical shock, particularly to individuals installing or working with the cables.
How might the movement of the cables within the tunnel affect the bracket's design?
-The movement and vibration of the cables could cause damage to the insulation over time, potentially leading to electrical hazards or failure of the cable's integrity.
What concerns are there about the durability of the painted finish on the steel bracket?
-The painted finish on the steel bracket may wear away due to the constant movement of the cables, which could compromise the cable's fit within the bracket and potentially cause damage to the insulation.
Why is the bracket designed to be machined in batches of thousands?
-The bracket is mass-produced in batches of thousands because the number of brackets needed depends on the length of the tunnel, which can be quite long, requiring a large quantity of parts.
What kind of mechanical attachment is used to secure the bracket to the tunnel support?
-The bracket is likely attached using mechanical fasteners such as nuts, bolts, or machine screws, or possibly using socket cap-style devices.
What role does the insulation of the cable play in the bracket's design considerations?
-The insulation of the electrical cable is crucial because it prevents electrical hazards. The bracket must protect the cable from movement that could cause the insulation to tear or wear away, potentially leading to electrocution risks.
What environmental factors could influence the movement of the cables in the tunnel?
-Factors such as vibration from vehicles or trains passing through the tunnel, atmospheric pressure, and potential air currents could all cause the cables to move, increasing the risk of wear on the insulation.
What improvements might be considered for the bracket to reduce the risk of cable insulation wear?
-Improvements could include using shock-absorbing materials, designing the bracket with better resistance to vibration, using corrosion-resistant materials, and ensuring that the internal surface of the bracket remains smooth and durable to prevent wear on the cable insulation.
Outlines
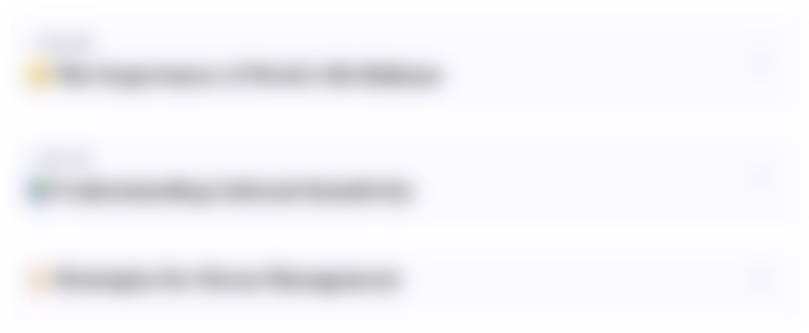
Этот раздел доступен только подписчикам платных тарифов. Пожалуйста, перейдите на платный тариф для доступа.
Перейти на платный тарифMindmap
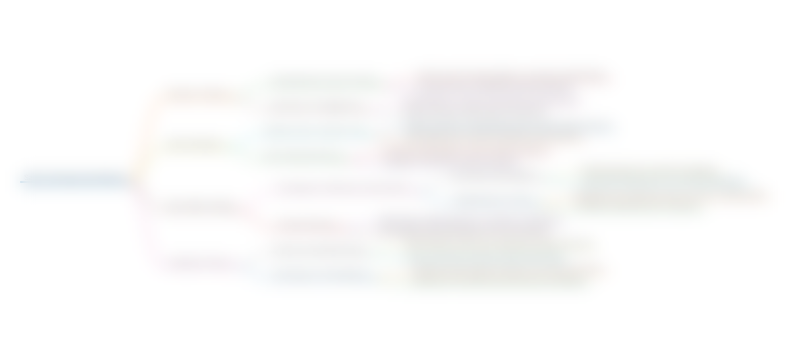
Этот раздел доступен только подписчикам платных тарифов. Пожалуйста, перейдите на платный тариф для доступа.
Перейти на платный тарифKeywords
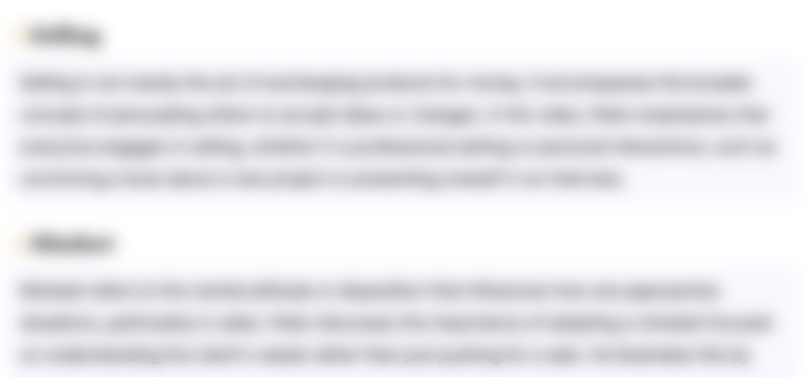
Этот раздел доступен только подписчикам платных тарифов. Пожалуйста, перейдите на платный тариф для доступа.
Перейти на платный тарифHighlights
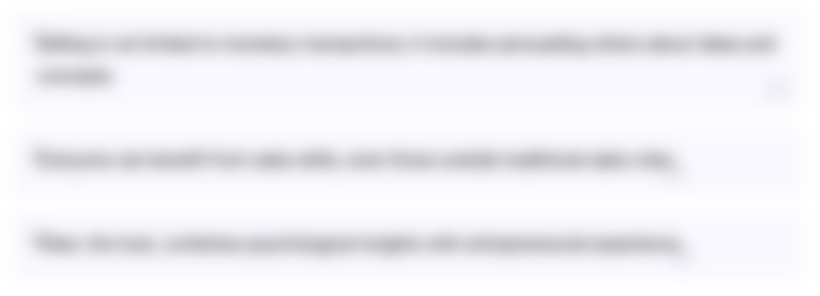
Этот раздел доступен только подписчикам платных тарифов. Пожалуйста, перейдите на платный тариф для доступа.
Перейти на платный тарифTranscripts
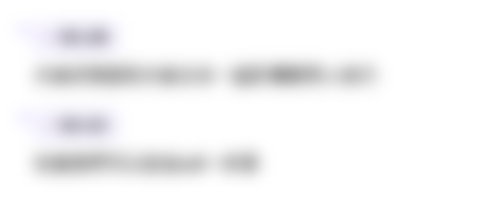
Этот раздел доступен только подписчикам платных тарифов. Пожалуйста, перейдите на платный тариф для доступа.
Перейти на платный тарифПосмотреть больше похожих видео
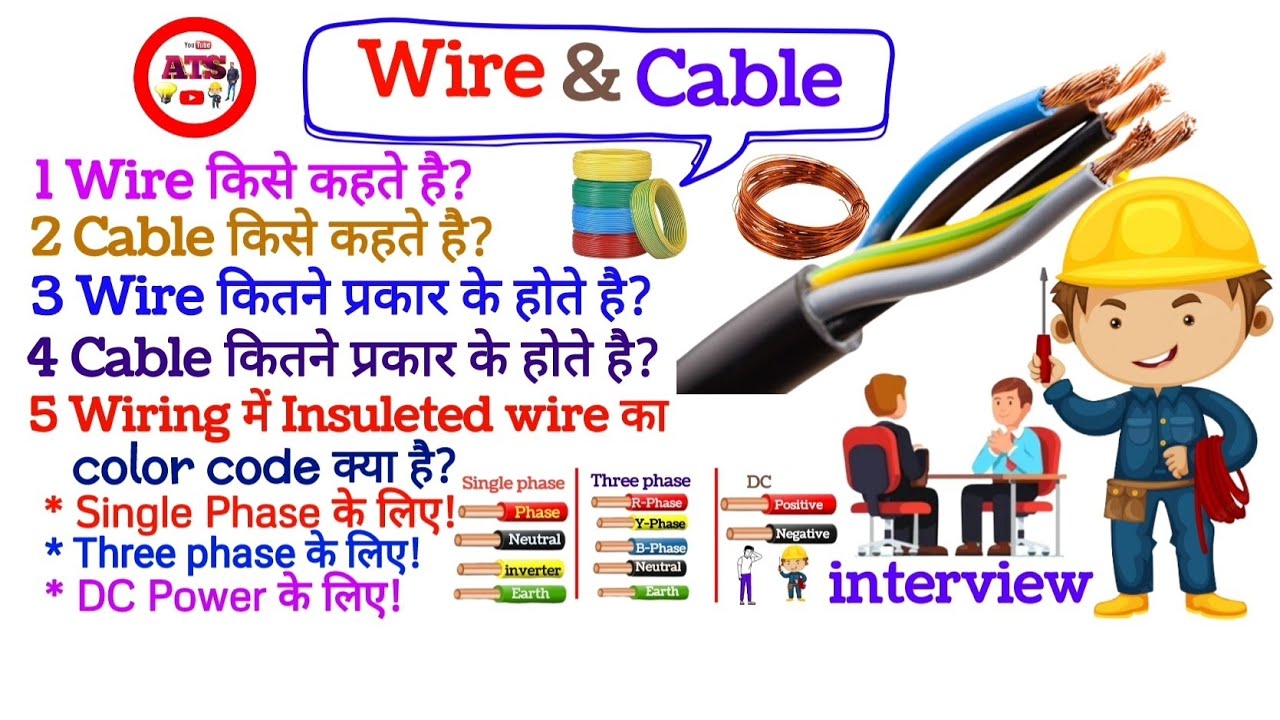
Type of cable & wire, wire and cable different, Wire color code in India interview Question & Answer

What does IT Support do? | Different escalation levels
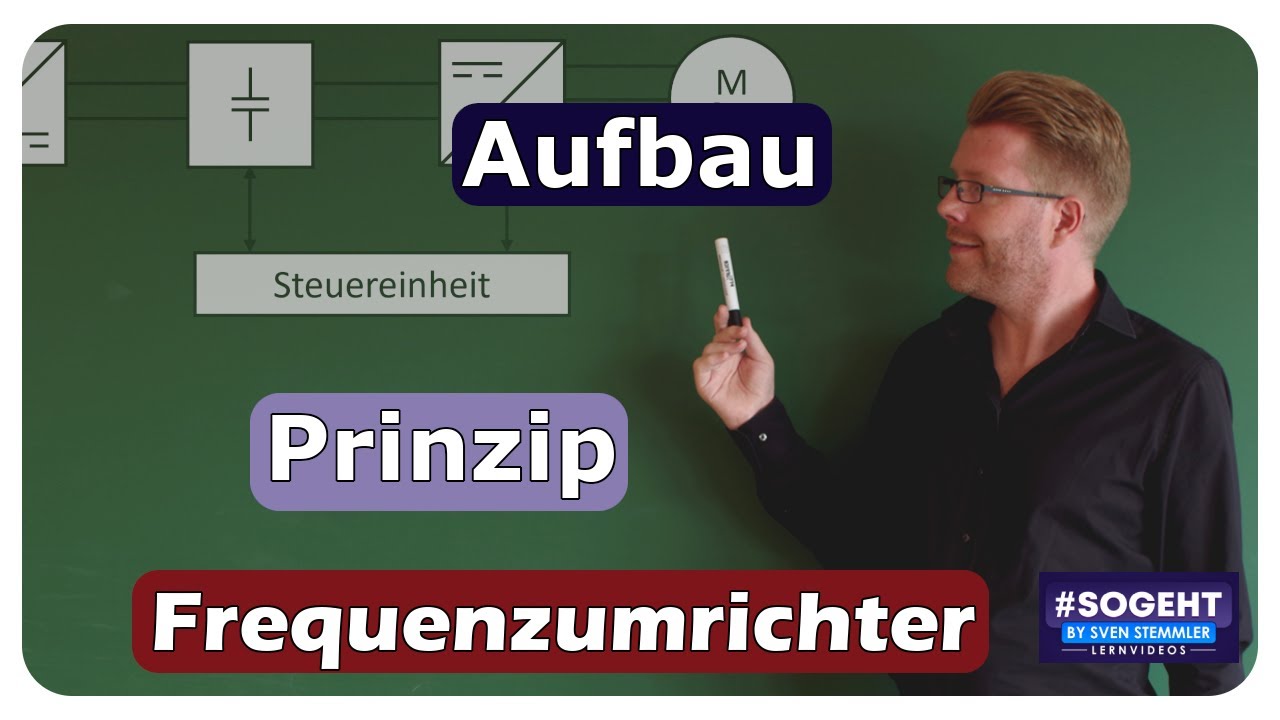
Frequenzumrichter einfach erklärt: Aufbau und Funktionsweise
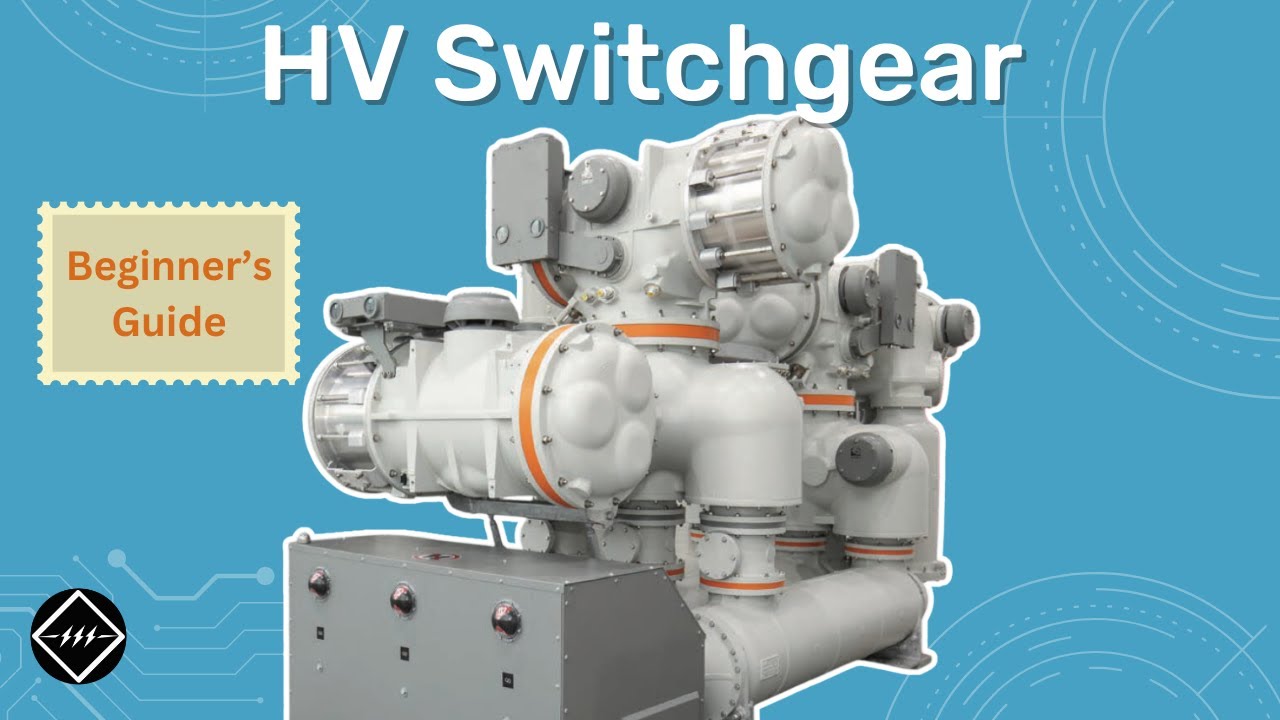
High Voltage Switchgear | An Introductory Guide | TheElectricalGuy

ACCEESSFM - Introduction and Aesthetics
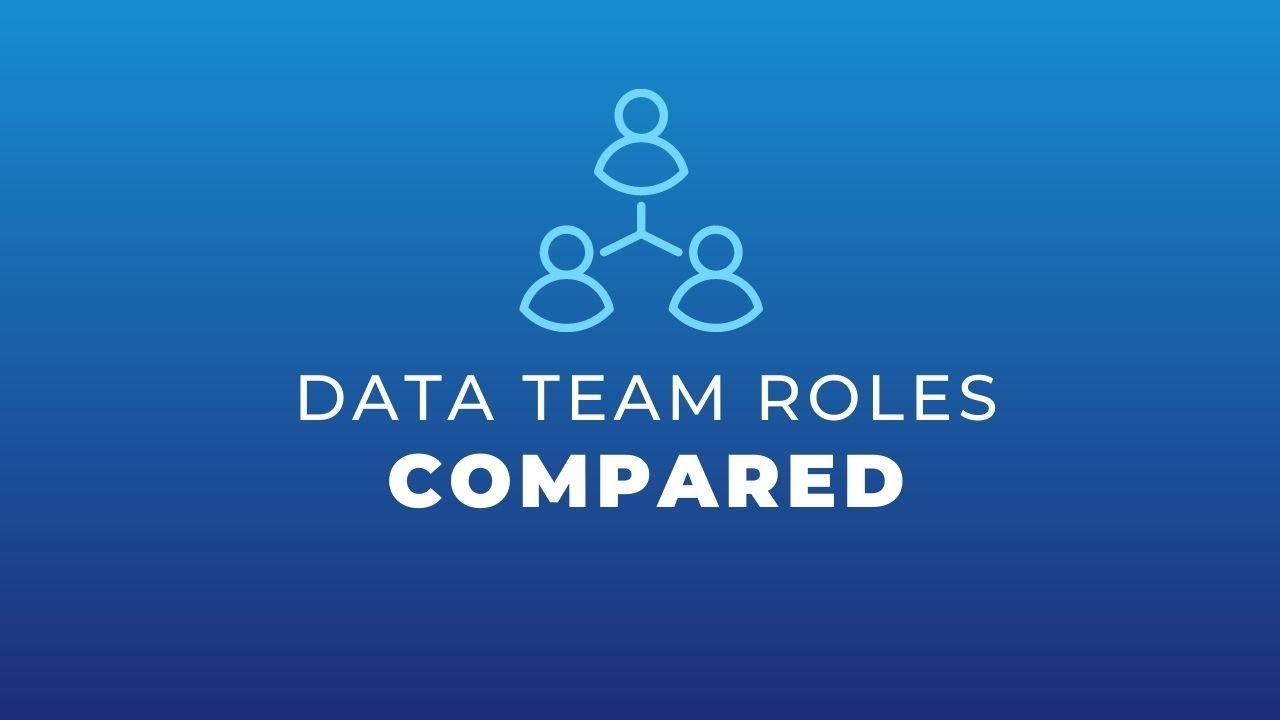
Common Data Team Structures (Engineer vs Analyst vs Scientist)
5.0 / 5 (0 votes)