The Green Curve
Summary
TLDRThe 'green curve' molding technology developed by Influx revolutionizes plastic part production by offering faster cycle times, improved part quality, and material flexibility. Unlike conventional methods, it uses adaptive pressure control for a more consistent fill and less scrap. The process ensures efficient thermal transfer, reduces defects, and can handle a variety of materials, including recycled ones, without manual adjustments. With benefits in sustainability, design flexibility, and productivity, this technology is an advanced solution for manufacturers seeking higher efficiency and quality in molding.
Takeaways
- 😀 The Influx process offers a new way to mold plastic parts more efficiently, providing significant advantages over conventional methods.
- 😀 Key benefits of the Influx molding technology include improved productivity, reduced cycle times, less scrap, and better overall part quality.
- 😀 Material and design flexibility are major advantages of the Influx process, allowing for cost savings and greater freedom in part design.
- 😀 Sustainability is a key aspect of the Influx process, helping molders reduce waste and improve environmental impact.
- 😀 Unlike traditional methods, the Influx process uses a pressure sensor at the machine nozzle to control the molding process more precisely, ensuring consistent results.
- 😀 The Influx technology operates at significantly lower pressures compared to conventional molding, offering a safer and more controlled environment.
- 😀 Despite slower mold filling, the Influx process actually results in shorter cycle times due to better control and less material waste.
- 😀 The process eliminates hesitation in material flow, ensuring that the flow front remains consistent throughout the mold, preventing defects.
- 😀 Packing material during the filling process, rather than in a separate phase, helps avoid defects such as shrinkage, warping, and surface blemishes.
- 😀 The Influx system adapts in real time to changes in material properties, such as viscosity or temperature, ensuring the process remains stable and efficient.
- 😀 The technology allows for flexible adaptation to recycled or variable materials, which improves sustainability by making these materials easier to work with.
Q & A
What is the 'green curve' process, and how does it differ from conventional molding?
-The 'green curve' process is an adaptive molding technology developed by Influx. Unlike conventional molding, which uses high-pressure injection and rapid filling, the green curve technology uses a pressure sensor to control and maintain a consistent, lower pressure throughout the filling and packing phases. This slower, more controlled approach leads to better part quality and reduced waste.
How does the green curve technology improve molding cycle time despite slower filling speeds?
-Although the green curve process fills the mold more slowly than conventional methods, it results in faster cycle times overall. This is because the material is packed during the filling phase, reducing the need for additional packing after filling, which helps shorten the total cycle time.
What are the main advantages of the green curve technology?
-The main advantages of the green curve technology are increased productivity, faster cycle times, reduced scrap, improved part quality (both aesthetic and dimensional consistency), material and design flexibility, and sustainability benefits.
Why is material and design flexibility important in the green curve process?
-Material flexibility is important because it allows manufacturers to use a variety of materials, including recycled plastics, which can reduce the cost of production. Design flexibility enables more innovative and complex part designs that are difficult or impossible to achieve using conventional molding methods.
How does the green curve process help with sustainability in plastic molding?
-The green curve process supports sustainability by allowing manufacturers to use recycled materials without compromising quality. The technology adapts in real time to variations in material properties, ensuring that even recycled or mixed materials can be used effectively, reducing waste and promoting more sustainable practices.
What role does the pressure sensor play in the green curve molding process?
-The pressure sensor plays a critical role by monitoring the pressure during the filling and packing stages. It provides real-time data that allows the system to adjust the process dynamically, ensuring consistent pressure and optimal filling conditions throughout the entire mold cavity, which improves part quality and reduces defects.
What is the significance of maintaining a constant pressure during the filling process?
-Maintaining a constant pressure during the filling process ensures that the material flows consistently through the mold cavity, preventing issues such as premature freezing or separation from the mold surfaces. This results in a more uniform and high-quality part, with fewer defects like warping or hazing.
How does the green curve process handle material viscosity changes?
-The green curve process adapts to changes in material viscosity by adjusting the driving pressure in real time. If the viscosity increases, the system increases the pressure to maintain the same flow velocity. Conversely, if the viscosity decreases, the pressure is reduced. This ensures that the part quality remains consistent regardless of changes in material properties.
Can the green curve process handle material blending, and if so, how?
-Yes, the green curve process can handle material blending. The system adapts in real time to variations in material composition, such as when different materials are mixed together. This allows for seamless blending of materials with different properties without the need for manual adjustments, ensuring consistent part quality throughout the molding process.
What is the role of adaptive control in the green curve molding process?
-Adaptive control is key to the green curve technology. It enables the process to respond to changes in mold resistance or material properties in real time. By continuously adjusting the pressure and screw velocity based on real-time data from the pressure sensor, the system maintains optimal conditions for part filling and packing, ensuring high-quality parts and minimizing defects.
Outlines
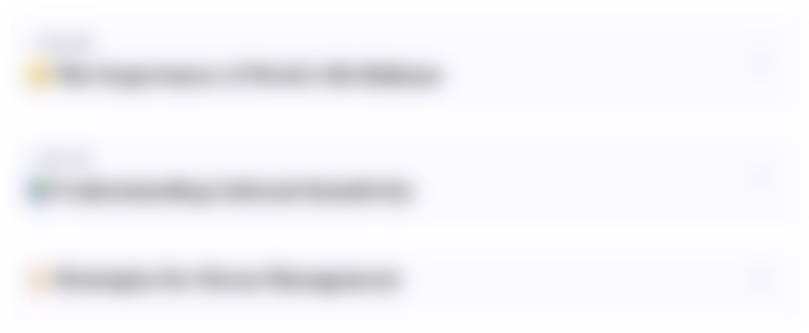
Этот раздел доступен только подписчикам платных тарифов. Пожалуйста, перейдите на платный тариф для доступа.
Перейти на платный тарифMindmap
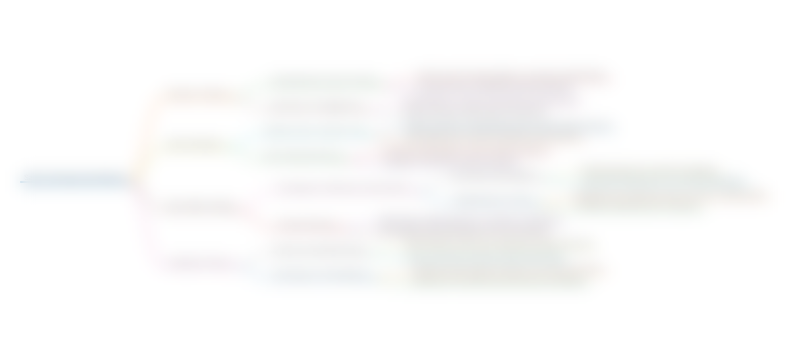
Этот раздел доступен только подписчикам платных тарифов. Пожалуйста, перейдите на платный тариф для доступа.
Перейти на платный тарифKeywords
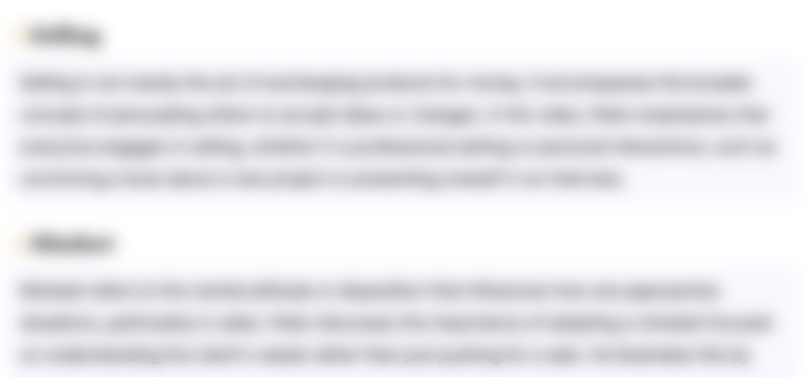
Этот раздел доступен только подписчикам платных тарифов. Пожалуйста, перейдите на платный тариф для доступа.
Перейти на платный тарифHighlights
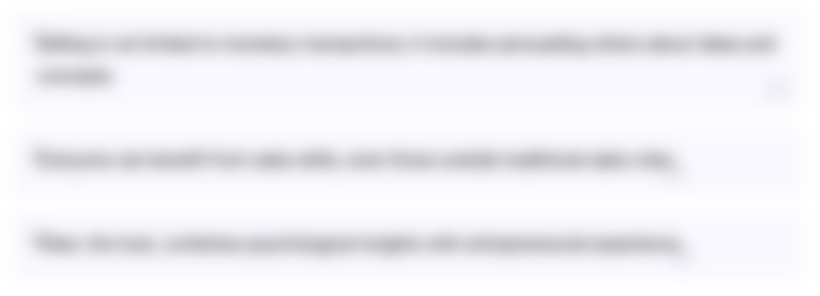
Этот раздел доступен только подписчикам платных тарифов. Пожалуйста, перейдите на платный тариф для доступа.
Перейти на платный тарифTranscripts
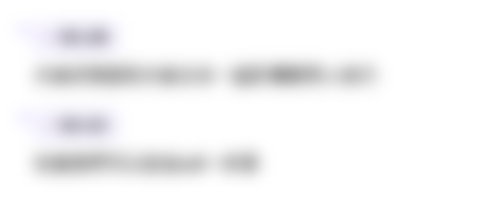
Этот раздел доступен только подписчикам платных тарифов. Пожалуйста, перейдите на платный тариф для доступа.
Перейти на платный тарифПосмотреть больше похожих видео
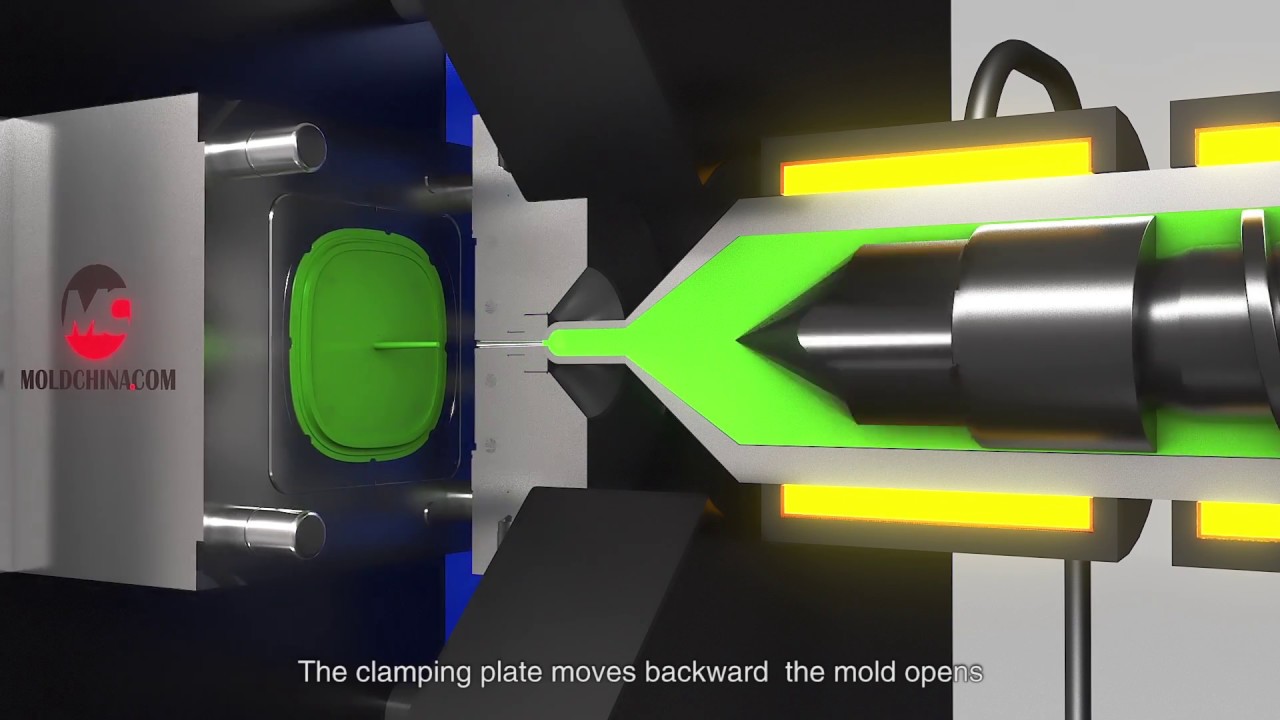
Plastic Injection Molding

Colchão: o que é, para que serve, quando usar e como calcular!
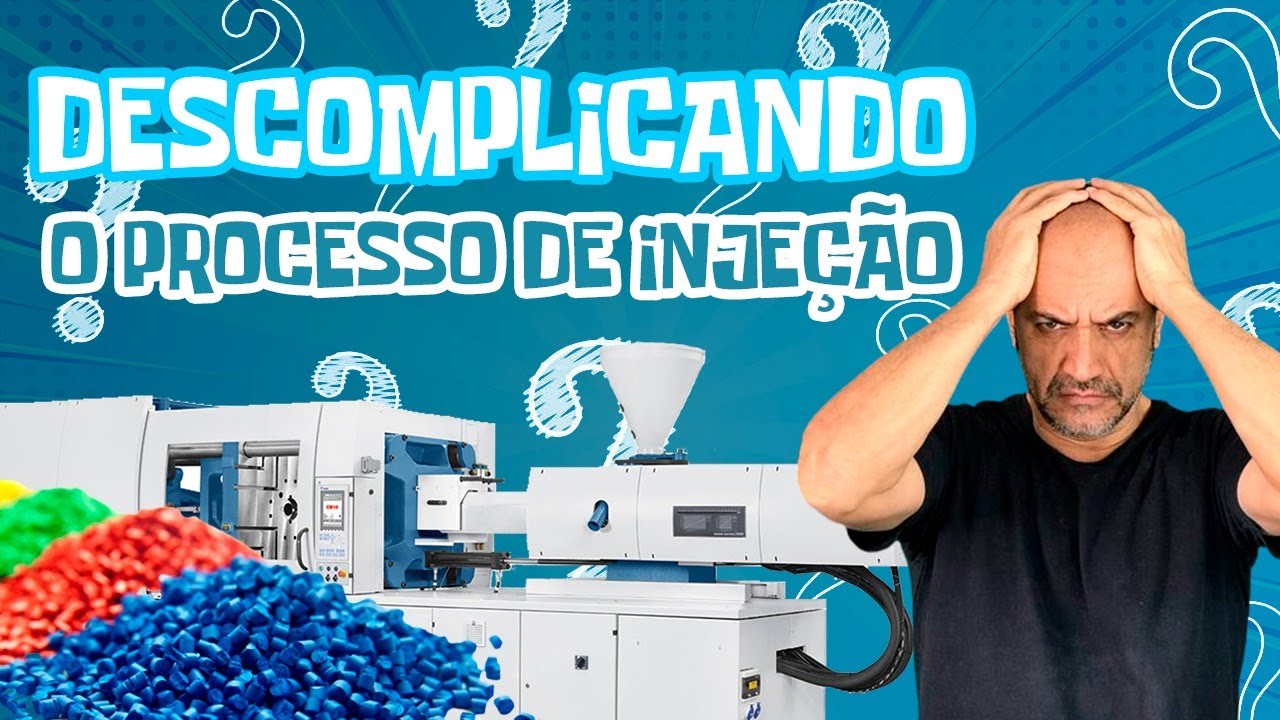
O básico do processo de injeção de plásticos

Thus shaping the future of dies and moulds: With EOS tooling applications

Velocidade de injeção
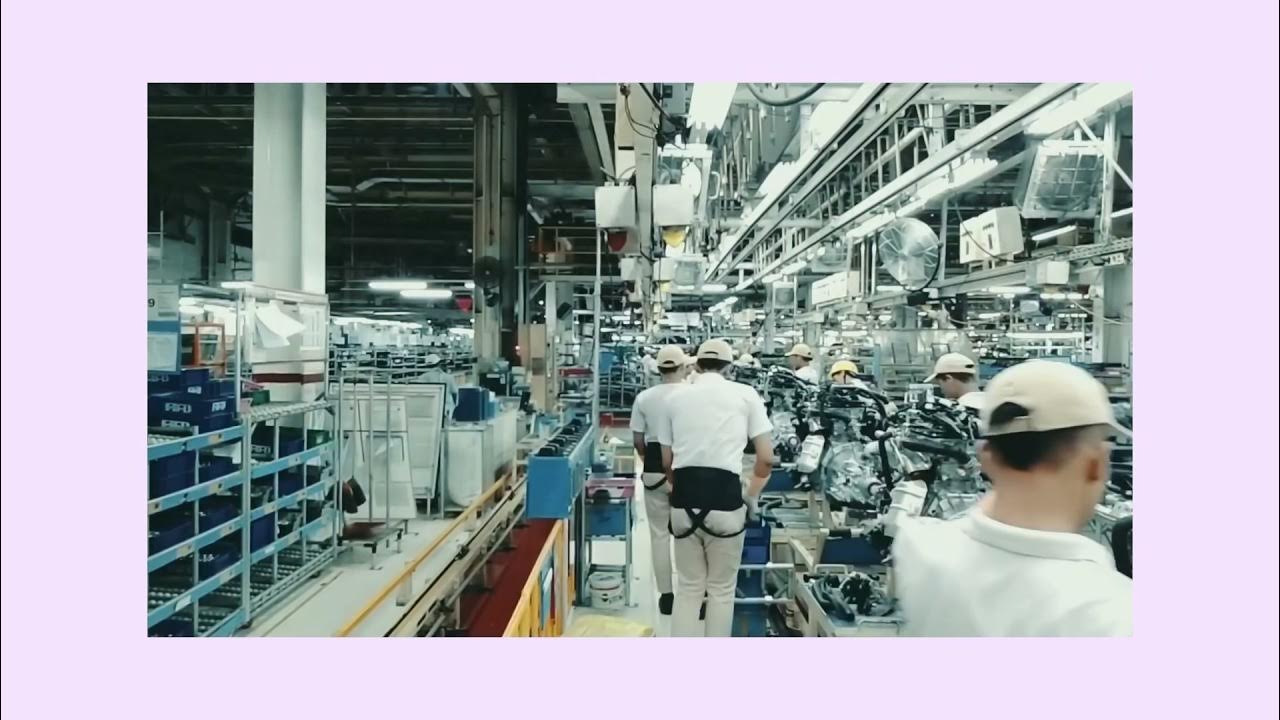
Penerapan Sistem Informasi dan Teknologi Informasi Pada Perusahaan Manufaktur (PT Suzuki)
5.0 / 5 (0 votes)