LEGO Bricks In The Making
Summary
TLDRThis video takes viewers through the meticulous process of creating LEGO bricks, from the arrival of raw plastic granulate to the final packaging of completed sets. It highlights the advanced technology and precision involved in molding and assembling the colorful bricks, including the use of high-tech machines, automated vehicles, and detailed quality control. With a focus on sustainability, efficiency, and innovation, the video reveals the journey of LEGO elements, ensuring that they meet the highest standards before reaching shelves around the world for both children and adults to enjoy.
Takeaways
- 😀 The LEGO brick, first molded in 1949, is an iconic invention that remains compatible with bricks from decades ago due to precision engineering.
- 😀 LEGO bricks are produced in over 50 different colors, with raw plastic granulate being mixed and dyed before being molded into bricks.
- 😀 High-tech injection molding machines operate 24/7 to produce LEGO elements, heating plastic to temperatures between 230-310°C to create the familiar brick shape.
- 😀 The molding process involves high pressure, reaching up to 29,000 psi, far higher than a car tire's pressure, to ensure the perfect shape and durability.
- 😀 Plastic waste from molding is recycled immediately to maintain efficiency and minimize waste in the production process.
- 😀 Molds used for LEGO production are highly precise and must be regularly cleaned and maintained to ensure the quality and compatibility of the bricks.
- 😀 Automatic Guided Vehicles (AGVs) have been part of the production process since 1987, helping automate the transport of filled boxes and increasing efficiency.
- 😀 Each LEGO element is carefully tracked using barcodes, allowing for precise inventory management and ensuring the right components are packed into the boxes.
- 😀 LEGO minifigures are produced separately and can be created at a rate of over 7,000 torsos per hour, contributing to the production of over half a billion minifigures annually.
- 😀 In the packaging process, counting machines ensure that the correct number of elements is placed in each bag, guaranteeing consistency across sets.
- 😀 After packaging, LEGO boxes are sealed, stacked, and shipped worldwide, ultimately reaching stores where consumers can enjoy building their creative sets.
Q & A
How long has LEGO been producing bricks with the same high precision?
-LEGO has been producing bricks with high precision for over 50 years, ensuring that bricks from different decades can still fit together perfectly.
What is the significance of the precision in LEGO's manufacturing process?
-The precision ensures that every LEGO brick, regardless of when it was produced, can fit together seamlessly with others. This consistency is a key factor in LEGO's success.
How are the different types of LEGO bricks produced with such precision?
-LEGO uses high-tech injection molding machines that operate 24/7. The molds are carefully designed and regularly maintained to ensure the exact specifications for each brick.
What happens to the raw material when it arrives at the LEGO factory?
-The raw plastic granulate is offloaded from trucks and stored in tall silos. It is then transported through pipes into the molding area, where it is transformed into LEGO elements.
What role do the high-tech injection molding machines play in LEGO's production?
-The injection molding machines are responsible for heating the plastic granulate, mixing it with dye, and molding it under extreme pressure to create the desired LEGO elements.
What temperatures are required for molding LEGO bricks?
-The plastic granulate is heated to temperatures between 230 and 310 degrees Celsius before being molded into bricks.
How does LEGO ensure that its bricks maintain high quality and precision?
-LEGO employs rigorous quality control measures, including temperature tests, molding tests, and regular mold maintenance, to ensure the durability and precision of each brick.
What is the role of AGVs (Automatic Guided Vehicles) in LEGO's factory?
-AGVs are robots that help move full boxes of LEGO elements from the molding machines to the conveyor system, ensuring smooth and automated transportation within the factory.
How are LEGO minifigures produced?
-LEGO minifigures are produced separately, with a machine capable of producing over 7,000 torsos per hour. More than half a billion minifigures are produced annually.
What happens after LEGO bricks are molded and packaged?
-After being packaged, LEGO boxes are shipped to distribution centers and then sent to stores worldwide, where they are available for customers to purchase and use in building creative sets.
Outlines
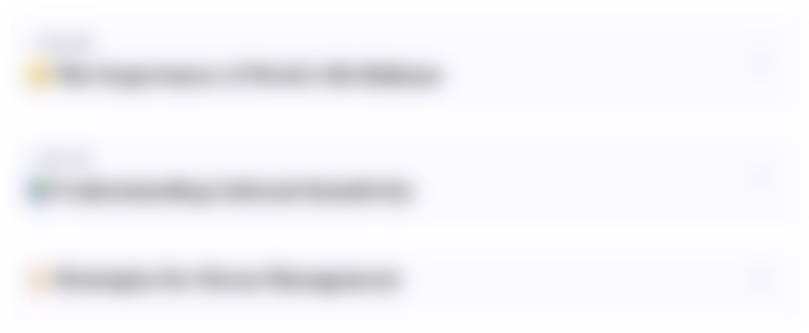
Этот раздел доступен только подписчикам платных тарифов. Пожалуйста, перейдите на платный тариф для доступа.
Перейти на платный тарифMindmap
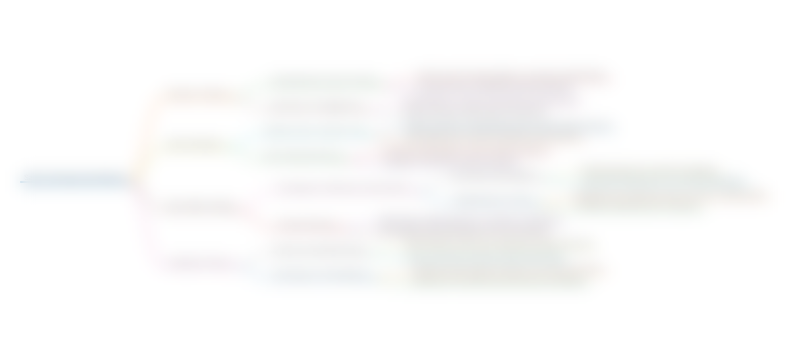
Этот раздел доступен только подписчикам платных тарифов. Пожалуйста, перейдите на платный тариф для доступа.
Перейти на платный тарифKeywords
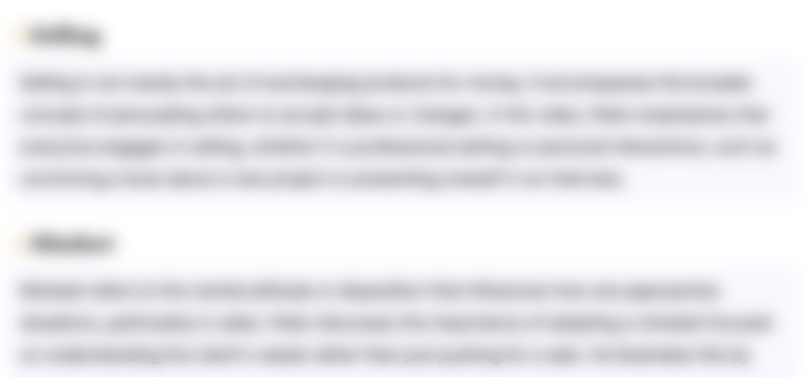
Этот раздел доступен только подписчикам платных тарифов. Пожалуйста, перейдите на платный тариф для доступа.
Перейти на платный тарифHighlights
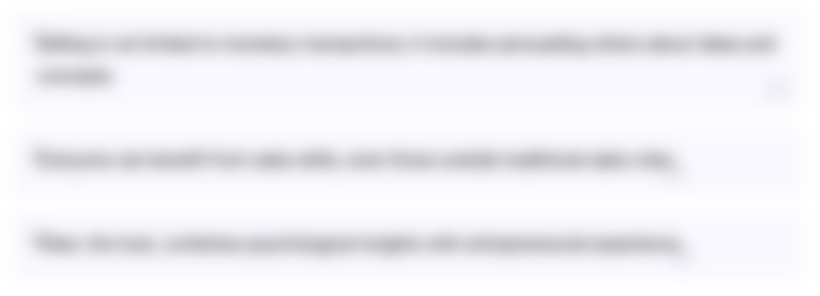
Этот раздел доступен только подписчикам платных тарифов. Пожалуйста, перейдите на платный тариф для доступа.
Перейти на платный тарифTranscripts
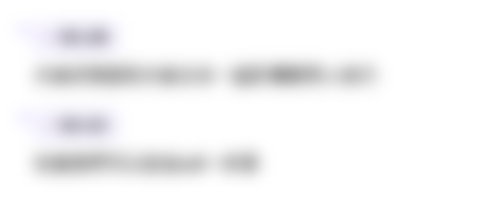
Этот раздел доступен только подписчикам платных тарифов. Пожалуйста, перейдите на платный тариф для доступа.
Перейти на платный тарифПосмотреть больше похожих видео

Kenapa Harga Lego Makin Mahal Banget? Tapi Makin Laku! Sempat Nyaris Bangkrut | Learning By Googling
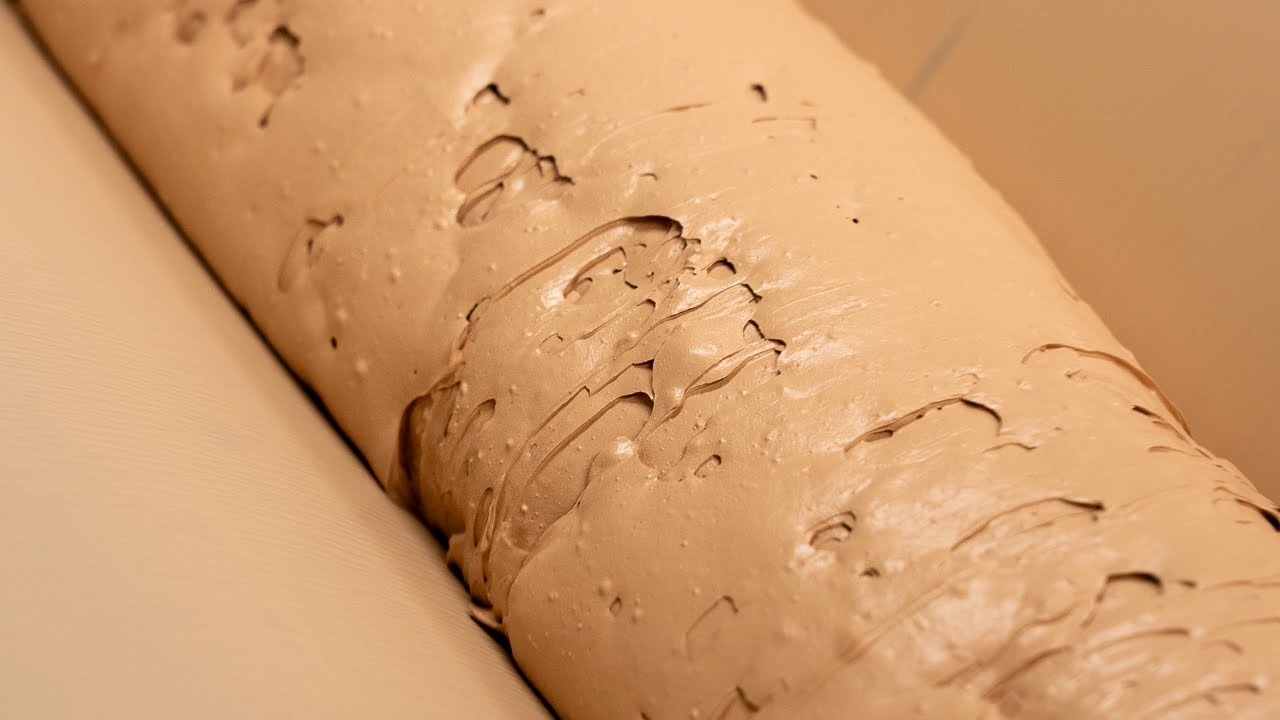
Like Ice Cream! Process of Making Makeup Cushion Foundation. Cosmetic Factory in Korea

Como é feito o tijolo #Boravê com Mari Fulfaro 🔵Manual do Mundo
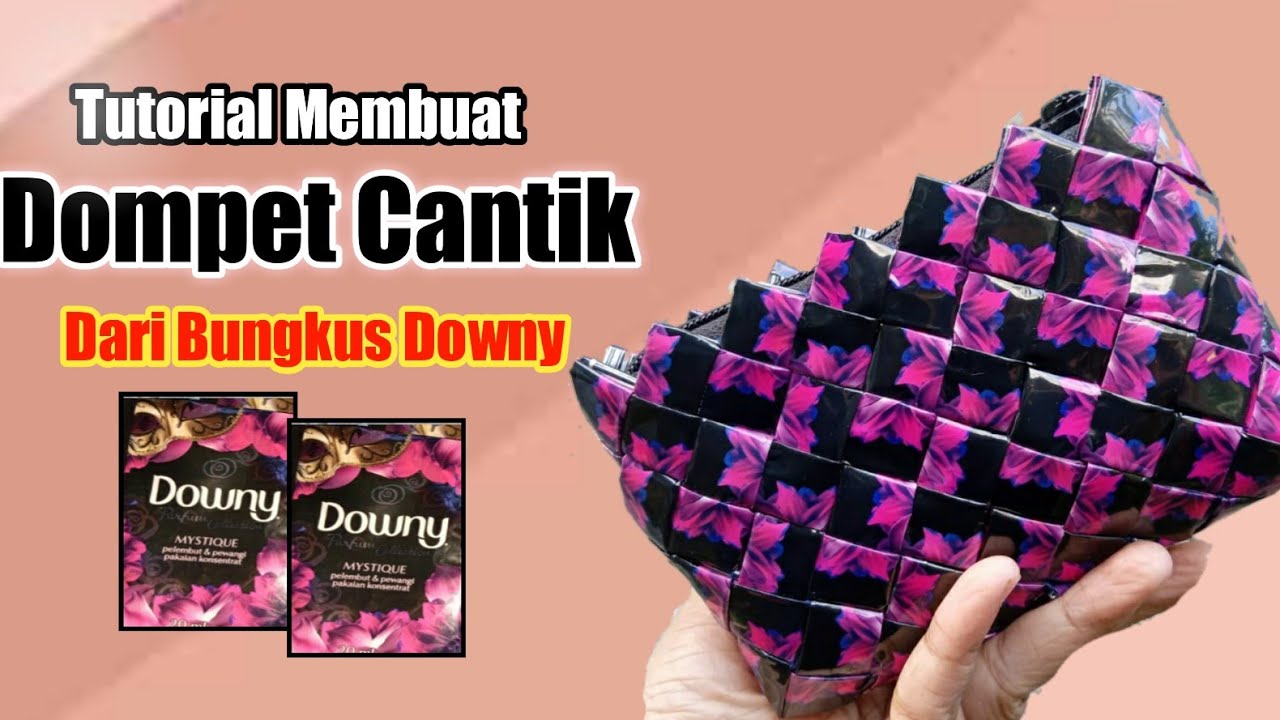
KERAJINAN DOMPET DARI PLASTIK KEMASAN DOWNY
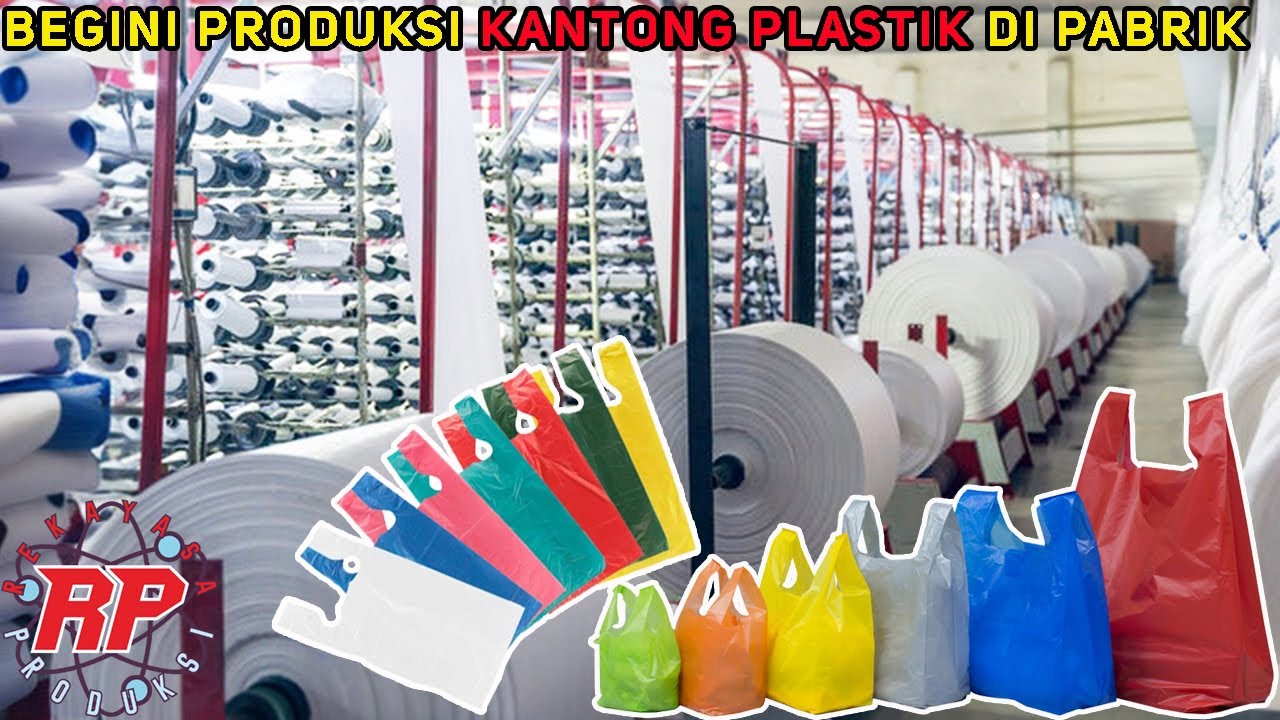
BEGINI PROSES CARA PEMBUATAN KANTONG PLASTIK YANG BIASA KITA PAKAI

Why Lego Isn’t (Just) a Toy Company | WSJ The Economics Of
5.0 / 5 (0 votes)