DC motor PID speed control
Summary
TLDRThis video guides viewers through the process of controlling DC motor speed with precision. It starts by explaining basic PWM control, followed by using encoders to measure speed. Two methods of calculating motor speed are explored, highlighting their limitations. A low-pass filter is applied to smooth the speed measurements. The video also demonstrates how to implement a PI (Proportional-Integral) control loop for accurate speed regulation, showcasing practical issues like overshooting and steady-state errors. Through hands-on examples, the tutorial offers in-depth insights into motor control, speed measurement, and troubleshooting common issues in real-time applications.
Takeaways
- 😀 DC motors are widely used in applications from garage door openers to robotics, but their speed can be difficult to control accurately using simple PWM methods.
- 😀 To achieve more precise speed control, a magnetic encoder and microcontroller (such as Arduino) are used to measure and adjust motor speed in real-time.
- 😀 The first method of speed measurement counts the encoder pulses in fixed time intervals, but it is less accurate at low speeds due to discrete pulses.
- 😀 The second method measures the time between encoder pulses, providing more accurate speed data, but it can introduce challenges at very low speeds when interrupts stop triggering.
- 😀 Encoder pulses are used to estimate motor speed, with real-world applications requiring conversion from encoder counts to standard units like rotations per minute (RPM).
- 😀 A low-pass filter can be used to reduce high-frequency noise in speed data, making the measurements smoother and more reliable.
- 😀 Implementing a low-pass filter with a cutoff frequency of 25 Hz helps to remove unwanted high-frequency oscillations from the motor speed data.
- 😀 PID (Proportional-Integral-Derivative) control is introduced for more precise motor speed regulation, though only the Proportional-Integral (PI) terms are used in this case for simplicity.
- 😀 The proportional controller adjusts the motor voltage based on the error between the target and actual speed, with the gain (Kp) determining the response size.
- 😀 The integral term (Ki) is added to the controller to eliminate steady-state errors, and tuning both Kp and Ki is crucial for achieving stable control.
- 😀 Speed control challenges include jitter at low speeds, overshooting at high Kp values, and issues with zero velocity measurement using time-based speed methods.
- 😀 Implementing the low-pass filter and carefully tuning the PI controller allows for more stable, accurate motor speed control without unnecessary oscillations.
Q & A
What is the primary limitation of using a PWM motor driver for speed control of a DC motor?
-The primary limitation of using a PWM motor driver for speed control is that the speed is imprecise and can vary depending on the loading conditions of the motor.
How does an encoder help in controlling the speed of a DC motor more accurately?
-An encoder helps by providing precise feedback on the motor’s position, allowing a microcontroller to calculate speed more accurately. This enables closed-loop control, which compensates for loading conditions and maintains consistent motor speed.
What are the two methods for computing motor speed from encoder readings?
-The two methods for computing motor speed are: (1) Counting encoder triggers over a fixed time interval, which is coarse but works better for high speeds; (2) Measuring the time elapsed between triggers, which provides smoother and more accurate speed measurements.
Why is the second method of speed computation considered more accurate than the first method?
-The second method is more accurate because it measures the time between encoder triggers, allowing for a smoother, continuous estimate of speed. This reduces the error caused by the discrete nature of encoder readings.
What is the main disadvantage of the second method of speed computation when the motor stops?
-The main disadvantage is that when the motor stops, the encoder stops triggering, making it impossible to measure zero velocity, which complicates the control of the motor at very low or zero speeds.
What role does the low-pass filter play in speed measurement?
-The low-pass filter removes high-frequency oscillations caused by the discrete nature of the encoder's measurements, smoothing out the speed readings and providing a more accurate representation of the motor’s speed.
What is a PI controller, and how is it used to control motor speed?
-A PI (Proportional-Integral) controller adjusts the motor speed based on the difference between the target speed and the current speed (error). The proportional term reacts to the error, and the integral term helps eliminate steady-state error, improving overall control precision.
What problem did the author encounter when testing the PI controller with the motor?
-The author encountered issues with overshooting and jittering when the proportional gain (Kp) was too high. This led to instability in the motor speed, causing the system to oscillate around the target speed.
How does increasing the integral gain (Ki) in the PI controller affect motor speed control?
-Increasing the integral gain (Ki) helps reduce steady-state error, making the controller more effective at reaching and maintaining the target speed. However, it needs to be balanced carefully to avoid introducing instability.
What issue does the low-pass filter address in the motor control system?
-The low-pass filter addresses the issue of high-frequency noise and oscillations that result from the discrete encoder measurements. By smoothing the speed data, the filter helps achieve a more stable and accurate control of the motor speed.
Outlines
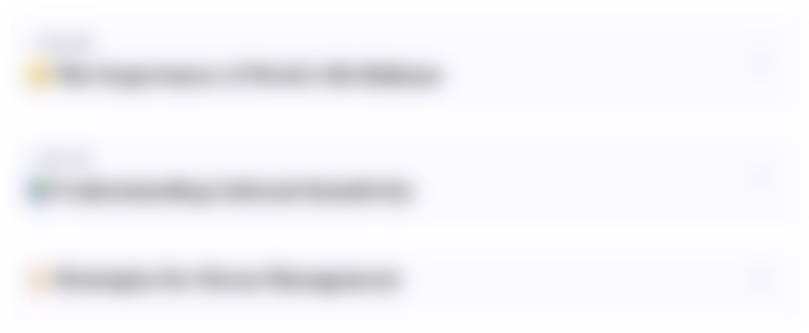
Этот раздел доступен только подписчикам платных тарифов. Пожалуйста, перейдите на платный тариф для доступа.
Перейти на платный тарифMindmap
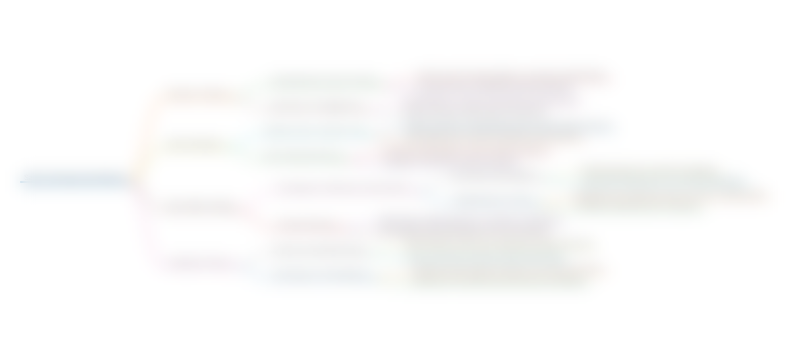
Этот раздел доступен только подписчикам платных тарифов. Пожалуйста, перейдите на платный тариф для доступа.
Перейти на платный тарифKeywords
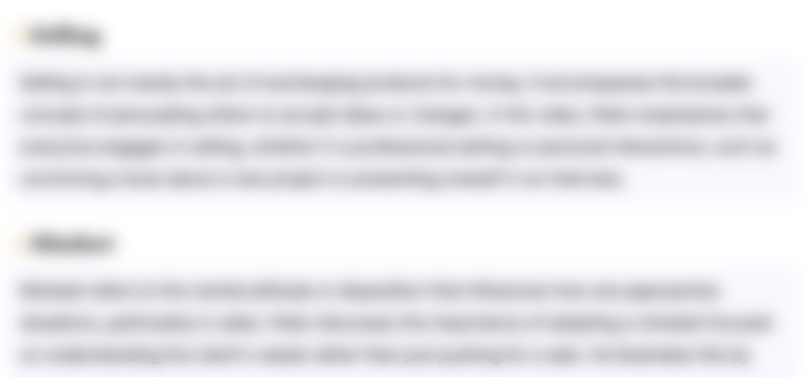
Этот раздел доступен только подписчикам платных тарифов. Пожалуйста, перейдите на платный тариф для доступа.
Перейти на платный тарифHighlights
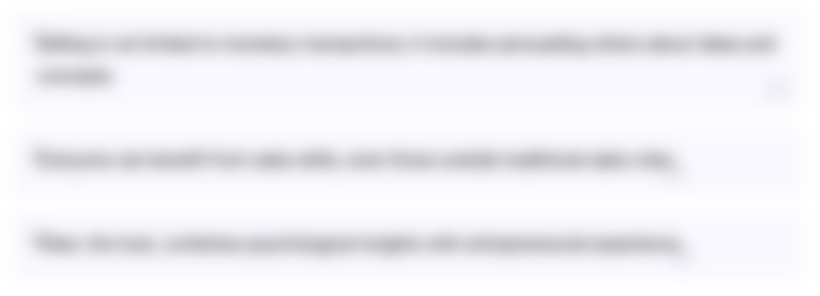
Этот раздел доступен только подписчикам платных тарифов. Пожалуйста, перейдите на платный тариф для доступа.
Перейти на платный тарифTranscripts
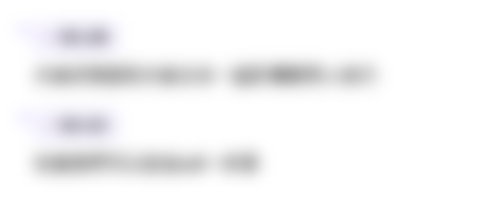
Этот раздел доступен только подписчикам платных тарифов. Пожалуйста, перейдите на платный тариф для доступа.
Перейти на платный тарифПосмотреть больше похожих видео
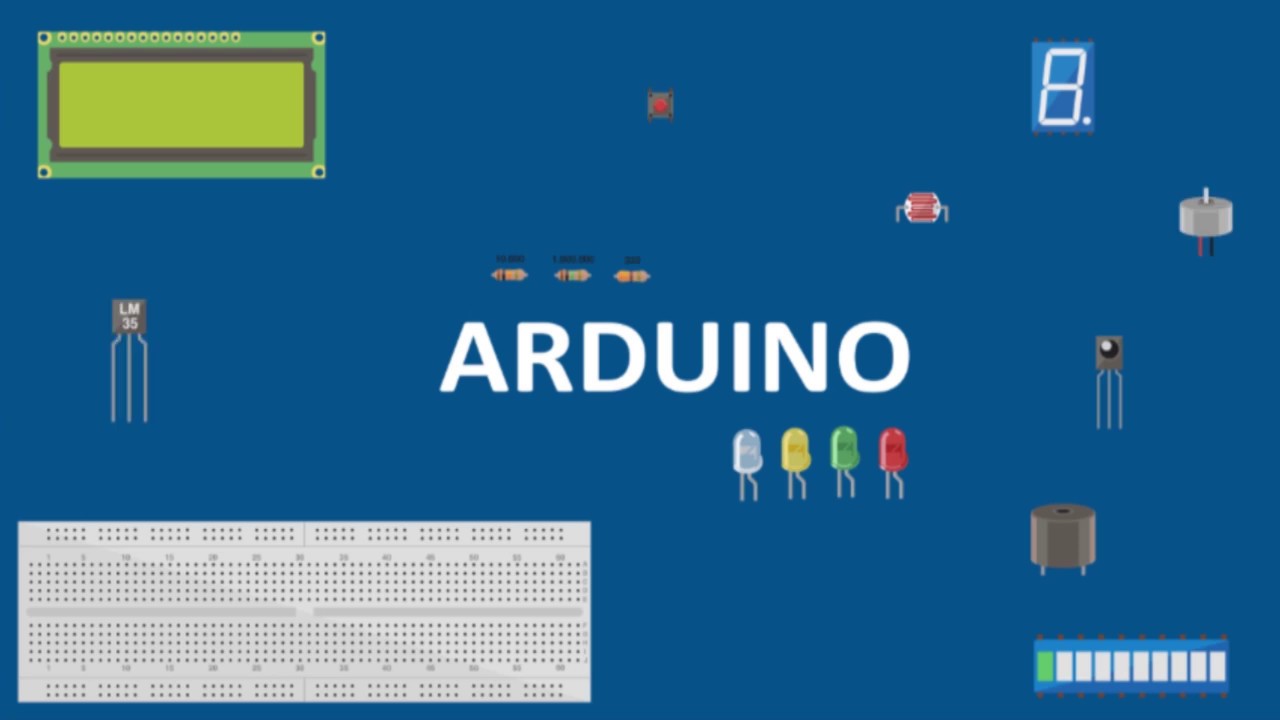
Arduino - Aula 23 - Experimento 9 - Motor com potenciômetro
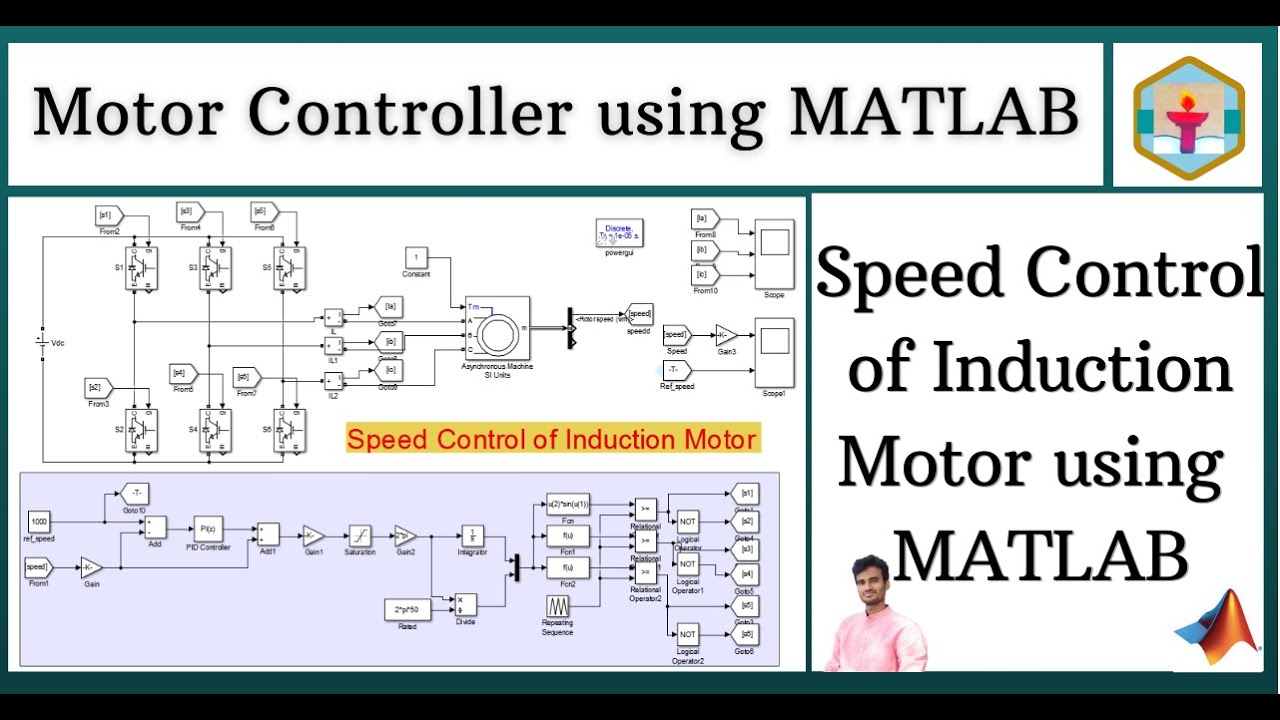
MATLAB simulation on speed control of induction motor | Scalar Control of induction motor

chocolate temp 2
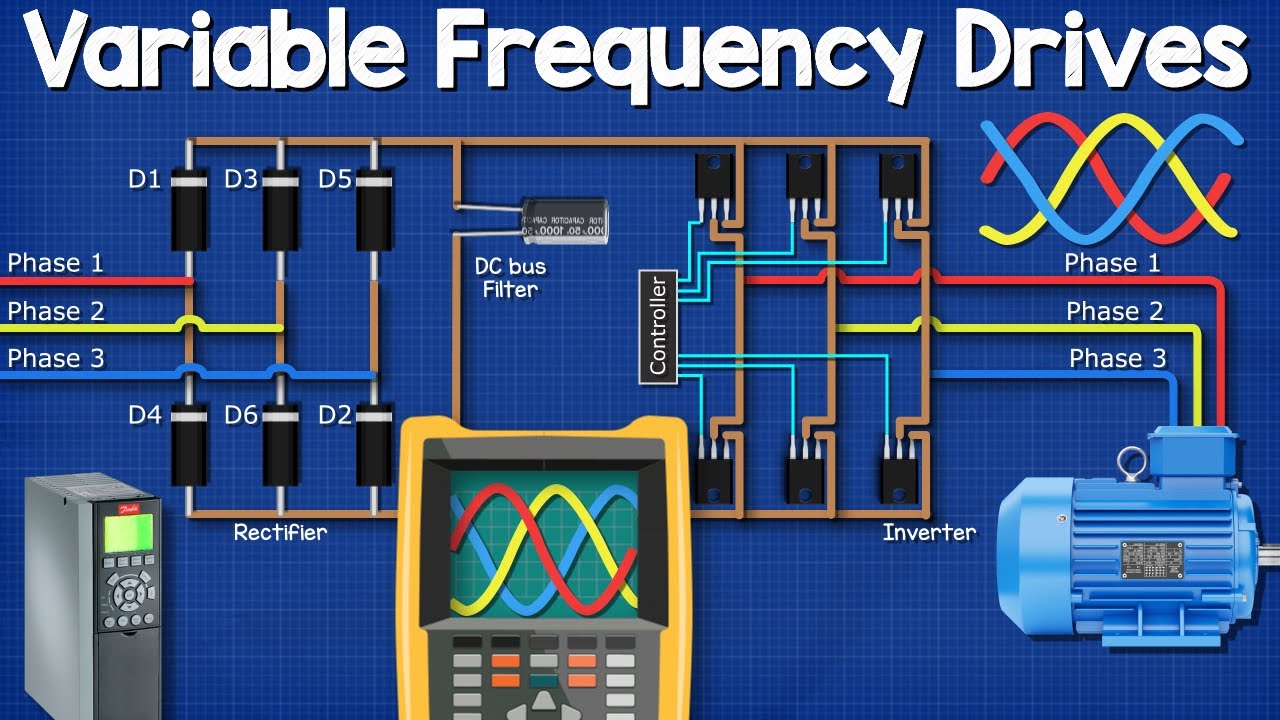
Variable Frequency Drives Explained - VFD Basics IGBT inverter
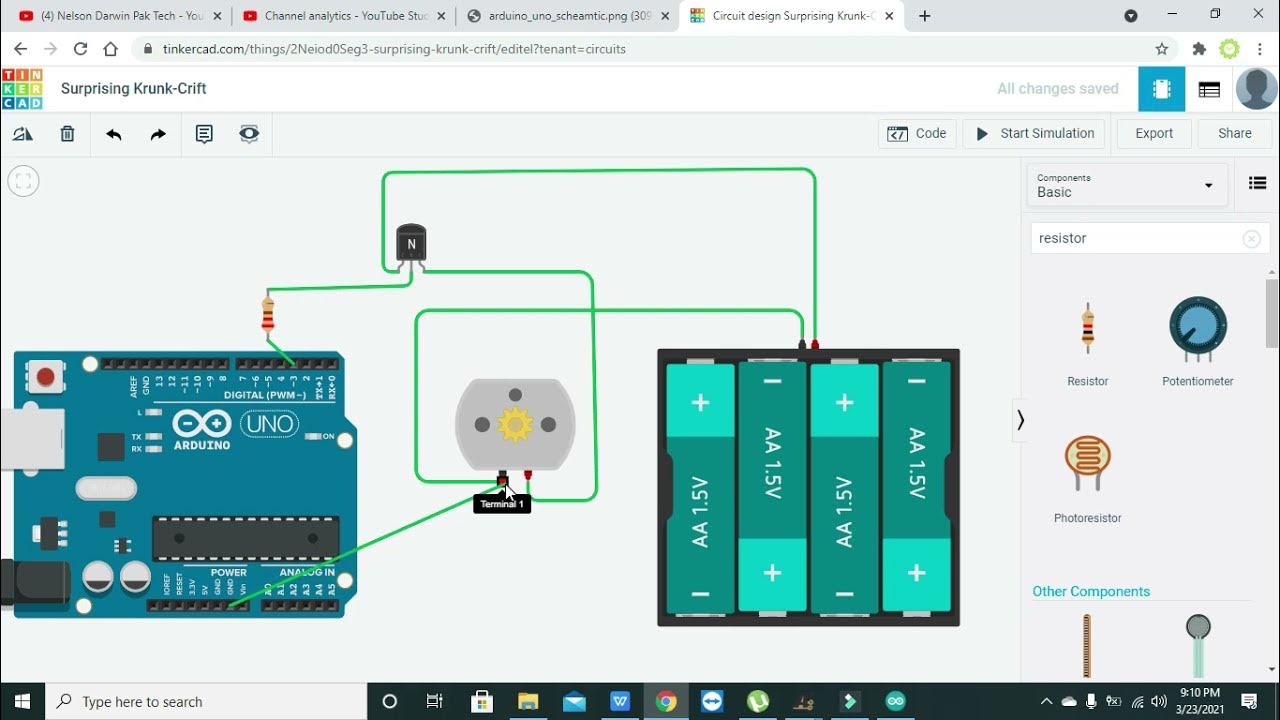
motor speed controller with arduino in tinkercad | motor speed controller with PWM in tinkercad
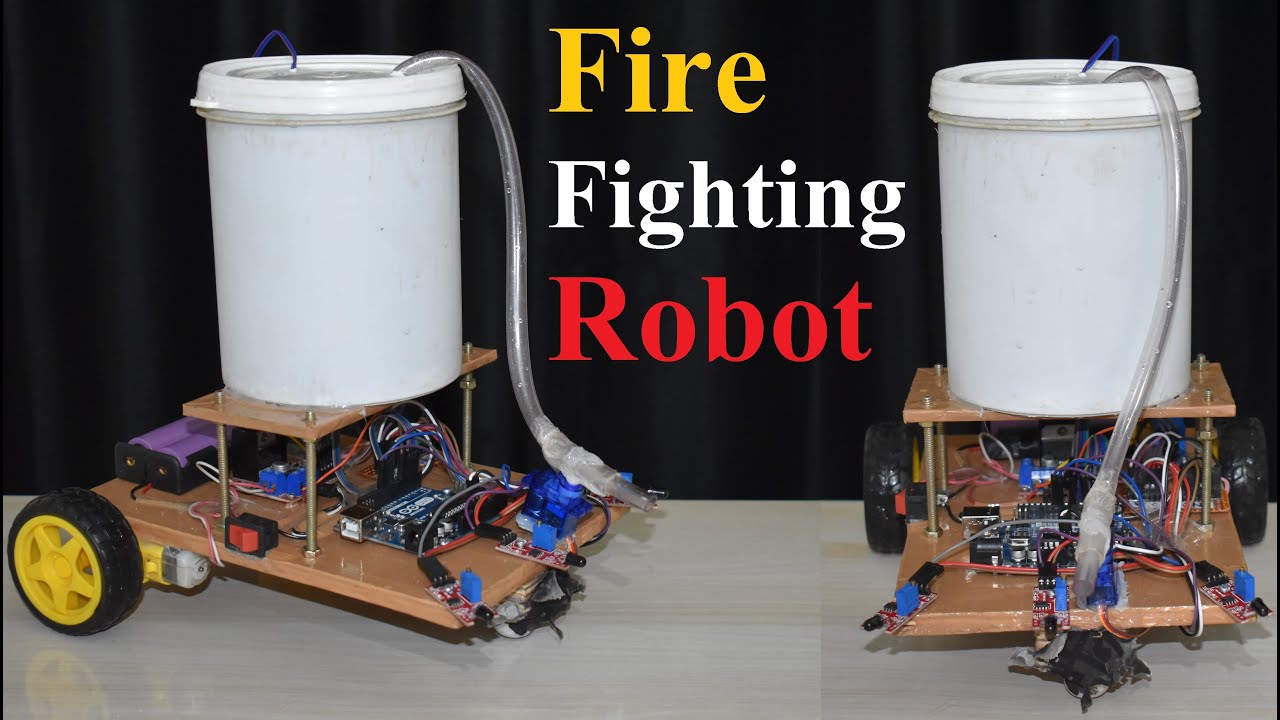
Fire Fighting Robot, Fire Fighting Robotic Car, New Electronics Project #science #shorts
5.0 / 5 (0 votes)