5S O QUE É (KAIZEN | Conheça a Metodologia da QUALIDADE TOTAL)
Summary
TLDRThe 5S methodology is a simple yet powerful management tool that helps businesses of all sizes organize their operations, increase productivity, and ensure a safer work environment. Originating in Japan, it is based on five key principles: Seiri (Sense of Use), Seiton (Sense of Organization), Seiso (Sense of Cleanliness), Seiketsu (Sense of Standardization), and Shitsuke (Sense of Discipline). By implementing these principles, companies can streamline their processes, reduce waste, and promote continuous improvement. This video explains how 5S works, its advantages, and provides practical steps to apply it effectively in any business.
Takeaways
- 😀 The 5S methodology is a management tool aimed at organizing businesses to achieve total quality and improved efficiency.
- 😀 It was developed in Japan after World War II to help restructure the country and is applicable to businesses of all sizes.
- 😀 The 5S methodology is based on five principles, each with a Japanese term: Seiri (Sort), Seiton (Set in order), Seiso (Shine), Seiketsu (Standardize), and Shitsuke (Sustain).
- 😀 Seiri (Sort) focuses on eliminating unnecessary items from the workspace, leaving only the essentials to optimize space and resources.
- 😀 Seiton (Set in order) emphasizes organizing the workspace to make it easy to find and access everything, improving productivity.
- 😀 Seiso (Shine) involves maintaining cleanliness in the workplace, with shared responsibility for cleanliness and personal hygiene.
- 😀 Seiketsu (Standardize) aims to make the 5S practices part of the company culture, ensuring they are followed consistently every day.
- 😀 Shitsuke (Sustain) encourages discipline and continuous improvement, with regular evaluations to keep the practices effective and integrated.
- 😀 The 5S methodology improves productivity, safety, and employee motivation by creating a well-organized and clean environment.
- 😀 Implementing 5S involves creating a committee, evaluating critical areas, applying the principles step-by-step, and conducting regular assessments to maintain progress.
Q & A
What is the 5S methodology?
-The 5S methodology is a management tool aimed at organizing and optimizing workplace efficiency, productivity, and safety. It is based on five key pillars—Seiri, Seiton, Seiso, Seiketsu, and Shitsuke—that guide businesses to maintain discipline and improve overall operations.
How does the 5S methodology improve productivity?
-By focusing on organization, eliminating waste, and standardizing processes, the 5S methodology creates a more efficient work environment. This allows employees to focus on essential tasks, reduces time spent searching for resources, and streamlines workflows, thus boosting productivity.
What are the five pillars of the 5S methodology?
-The five pillars of the 5S methodology are: 1) Seiri (Sort) - eliminate unnecessary items, 2) Seiton (Set in Order) - organize the workspace, 3) Seiso (Shine) - maintain cleanliness, 4) Seiketsu (Standardize) - establish standards, and 5) Shitsuke (Sustain) - foster discipline and continuous improvement.
Why was the 5S methodology developed?
-The 5S methodology was developed in Japan after World War II to help the country rebuild and restructure. It was designed to improve organizational efficiency and productivity, which were critical to economic recovery and growth.
What does 'Seiri' (Sort) involve in the 5S methodology?
-Seiri, or 'Sort', involves eliminating unnecessary items from the workspace, ensuring that only essential tools, equipment, and materials remain. This reduces clutter and improves efficiency by freeing up space and resources.
What is the importance of the 'Seiton' (Set in Order) pillar?
-'Seiton' focuses on organizing the workspace to enhance productivity. By clearly defining spaces for tools, documents, and equipment, employees can easily access what they need, leading to smoother workflows and reduced time spent searching for items.
How does 'Seiso' (Shine) contribute to the success of the 5S methodology?
-'Seiso' emphasizes cleanliness in the workplace, ensuring that the environment is tidy and hygienic. This is not just about maintaining a clean physical space but also ensuring that everything is in good working order, contributing to safety and overall morale.
What is the role of 'Seiketsu' (Standardize) in the 5S process?
-'Seiketsu' involves standardizing the processes and practices across the organization to maintain the 5S system. By establishing clear guidelines, routines, and expectations, businesses can ensure that the first three pillars (Seiri, Seiton, Seiso) are consistently applied and maintained.
How does 'Shitsuke' (Sustain) ensure long-term success with 5S?
-'Shitsuke' focuses on discipline, making the 5S practices a part of the company culture. This pillar encourages continuous improvement and ensures that employees remain committed to maintaining the system through regular evaluations, training, and reinforcement.
What are the main benefits of implementing the 5S methodology in a business?
-The 5S methodology offers several key benefits: it increases productivity by streamlining workflows, improves safety by reducing workplace hazards, enhances employee motivation through a more organized environment, and fosters continuous improvement that leads to higher quality and better overall performance.
What are the practical steps to apply the 5S methodology in a business?
-To apply 5S, businesses should: 1) Create a committee to lead the process, 2) Evaluate critical areas in need of improvement, 3) Implement the 5S pillars in order, and 4) Regularly evaluate and adjust the practices to ensure sustained success and adherence.
How can businesses evaluate their progress after implementing the 5S methodology?
-Businesses can evaluate their progress by establishing mechanisms for regular feedback and assessment. This includes checking if the 5S principles are being followed, identifying areas for improvement, and making necessary adjustments to maintain and enhance the effectiveness of the methodology.
Outlines
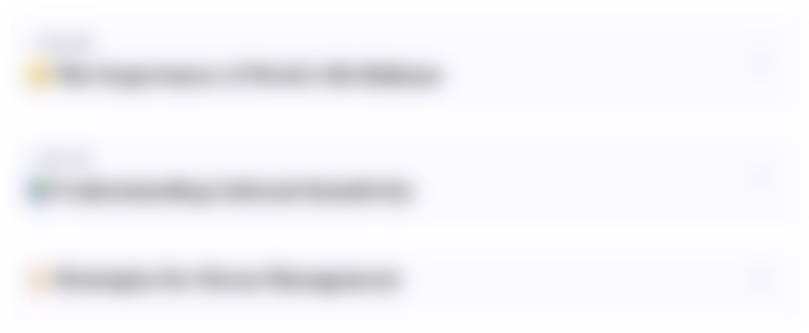
Этот раздел доступен только подписчикам платных тарифов. Пожалуйста, перейдите на платный тариф для доступа.
Перейти на платный тарифMindmap
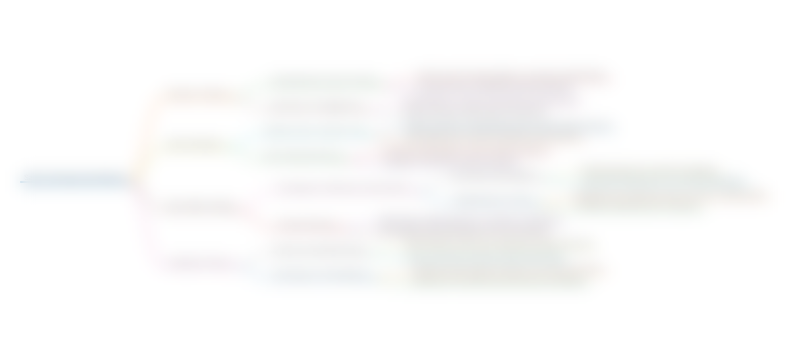
Этот раздел доступен только подписчикам платных тарифов. Пожалуйста, перейдите на платный тариф для доступа.
Перейти на платный тарифKeywords
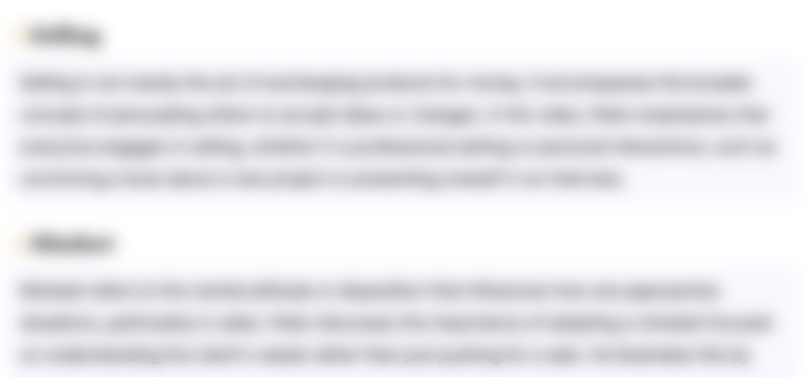
Этот раздел доступен только подписчикам платных тарифов. Пожалуйста, перейдите на платный тариф для доступа.
Перейти на платный тарифHighlights
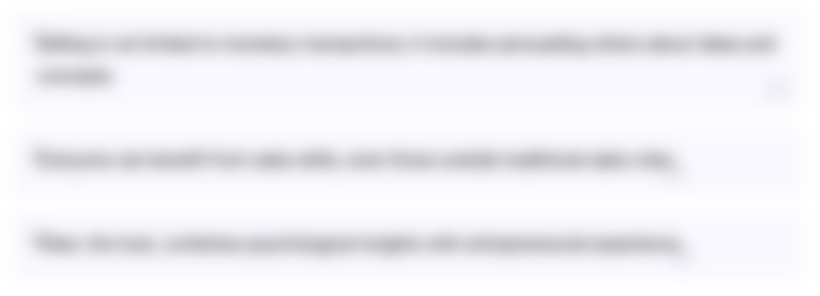
Этот раздел доступен только подписчикам платных тарифов. Пожалуйста, перейдите на платный тариф для доступа.
Перейти на платный тарифTranscripts
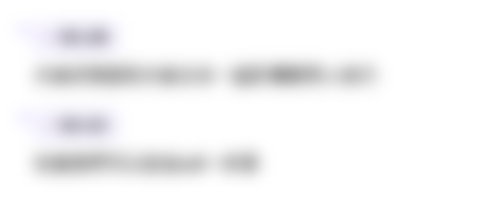
Этот раздел доступен только подписчикам платных тарифов. Пожалуйста, перейдите на платный тариф для доступа.
Перейти на платный тарифПосмотреть больше похожих видео
5.0 / 5 (0 votes)