How Do Robot Arms Work?
Summary
TLDRIn this video, Corey Alice explains how robotic arms function, focusing on their kinematics, types of movements, and control systems. He covers the six axes of a typical articulated robot arm and differentiates between point-to-point and path-controlled movements. The video delves into forward and inverse kinematics, illustrating how the robot calculates its movements based on the tool's desired position. Corey also explores motion planning, the integration of PLCs (Programmable Logic Controllers), and different control architectures, shedding light on the communication between robots and PLCs to achieve precise and efficient automation tasks.
Takeaways
- 😀 Robot arms typically have six degrees of freedom (DOF), allowing for movement in six different directions.
- 😀 Each joint in a robot arm is powered by a motor, with modern robots using electric motors, and older models using hydraulic or pneumatic systems.
- 😀 The six joints of an articulated robot arm are typically: Base swing (S axis), shoulder (L axis), elbow (U axis), forearm rotation (R axis), wrist bend (B axis), and wrist rotation (T axis).
- 😀 Point-to-point movement means the robot moves from one position to another without focusing on the path taken, ideal for simple tasks.
- 😀 Path-controlled movement requires the robot to follow a specific path, important for tasks like welding where precision is crucial.
- 😀 Motion planning or path planning is the process that takes commands and translates them into geometric paths, determining the robot's movements.
- 😀 Forward kinematics involves calculating the position of the tool based on known joint positions.
- 😀 Inverse kinematics works in reverse, calculating the necessary joint movements to achieve a desired tool position.
- 😀 Robot programming involves translating high-level commands (like G-code) into motion plans that can be interpreted by the robot's path planner.
- 😀 Communication between a robot and a PLC (Programmable Logic Controller) is crucial for synchronizing operations and controlling the robot through various industrial protocols (Ethernet IP, PROFINET, etc.).
- 😀 Some robot systems integrate both the robot controller and PLC functions into one system, offering benefits like streamlined communication and control.
Q & A
What are the six degrees of freedom in a robot arm, and why are they important?
-The six degrees of freedom (DOF) in a robot arm refer to the six axes that the robot can move along, allowing it to perform a variety of motions. These include the ability to move in different directions (up/down, left/right, forward/backward) and rotate at each joint. This flexibility is essential for performing complex tasks like welding or cutting, where precise control over movement is needed.
What is the difference between point-to-point and path control movements in robotics?
-Point-to-point movements focus on moving from one specific point to another, without concern for the trajectory the robot takes in between. Path control movements, on the other hand, require the robot to follow a specific, predefined path, which is crucial in applications like welding where the exact path of the tool is important.
How does forward kinematics help in robot movement?
-Forward kinematics is used to calculate the position of the robot's end effector (or tool center point) based on the known positions of all the robot's joints. It allows us to determine where the tool is in space when we know the angles and positions of the joints, facilitating precise control of the robot.
What is the purpose of inverse kinematics in robot motion planning?
-Inverse kinematics is the process of calculating the necessary joint positions (angles) to reach a specific point in space for the end effector. Given the desired position of the tool, inverse kinematics allows the system to determine how to move the joints in aggregate to achieve that position.
What is motion planning in robotics?
-Motion planning, or path planning, is the process of determining the trajectory or sequence of movements a robot must follow to perform a task. It involves calculating both the geometric path and ensuring that the robot's movements are safe and efficient.
How do robots interpret code to move their arms?
-Robots interpret code through a system that converts human-readable commands (like G-code) into machine instructions. These instructions are processed by a path planner, which calculates the geometric path the robot should follow, taking into account tool compensation and velocity before generating the necessary motor movements.
Why is tool compensation important in robot motion?
-Tool compensation adjusts the robot's movement to account for the size and orientation of the tool being used. This ensures that the robot’s end effector reaches the correct point, even if the tool's geometry changes, or the tool is offset from the robot's center.
What role does the robot controller play in robot movement?
-The robot controller interprets the code and communicates with the robot's hardware, directing the motors to achieve the desired movement. It ensures the motion is executed according to the programmed commands, whether the robot is performing point-to-point or path-controlled movements.
How do robots communicate with a PLC in an automation system?
-Robots communicate with a PLC (Programmable Logic Controller) through various protocols, such as Ethernet/IP, Powerlink, or serial communication. The PLC often serves as a high-level controller, sequencing the robot’s tasks and sending commands to the robot controller, which then executes the movements.
What is the difference between traditional robot controllers and machine-centric robotics systems?
-Traditional robot systems typically use separate controllers for the robot and the PLC, which communicate via a field bus. In machine-centric robotics, both the PLC and the robot controller are integrated into one system, simplifying communication and software management by consolidating everything into a single ecosystem.
Outlines
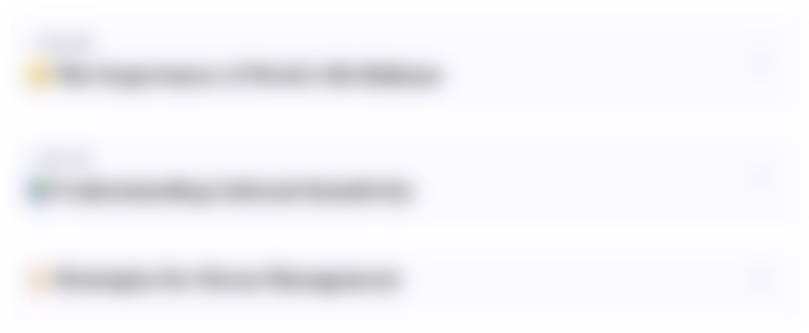
Этот раздел доступен только подписчикам платных тарифов. Пожалуйста, перейдите на платный тариф для доступа.
Перейти на платный тарифMindmap
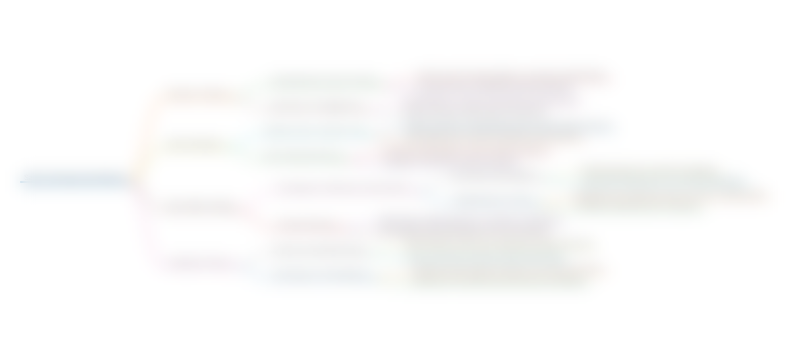
Этот раздел доступен только подписчикам платных тарифов. Пожалуйста, перейдите на платный тариф для доступа.
Перейти на платный тарифKeywords
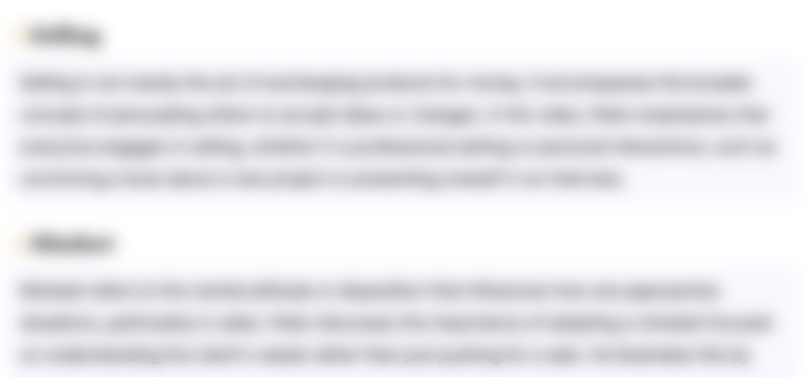
Этот раздел доступен только подписчикам платных тарифов. Пожалуйста, перейдите на платный тариф для доступа.
Перейти на платный тарифHighlights
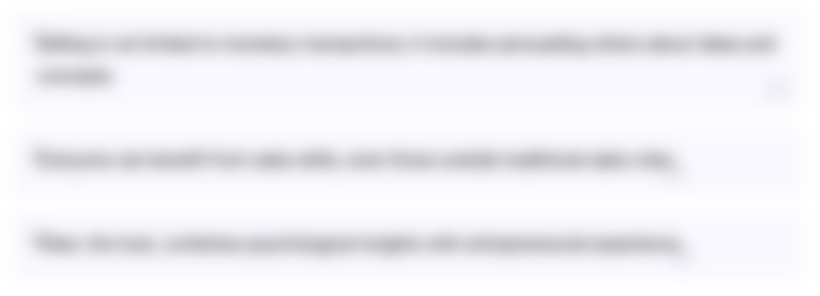
Этот раздел доступен только подписчикам платных тарифов. Пожалуйста, перейдите на платный тариф для доступа.
Перейти на платный тарифTranscripts
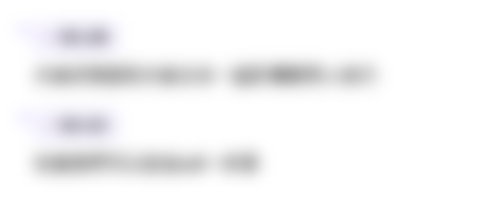
Этот раздел доступен только подписчикам платных тарифов. Пожалуйста, перейдите на платный тариф для доступа.
Перейти на платный тарифПосмотреть больше похожих видео

Industrial Actuators Types of Actuators Actuator Working Principle Actuator Control Methods PLC
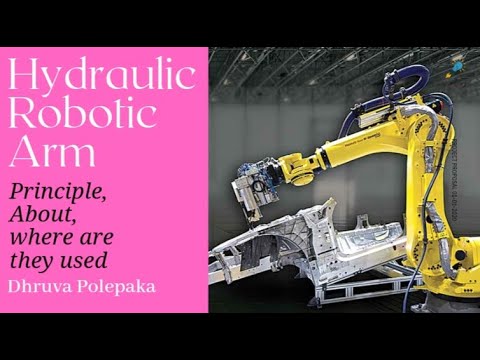
Hydraulic Robotic Arm | Principle, Definition, Uses | Dhruva Polepaka | Dhruva's Thesis

Getaran 2 Derajat Kebebasan

Introducción a la robótica: Posición, orientación y tramas
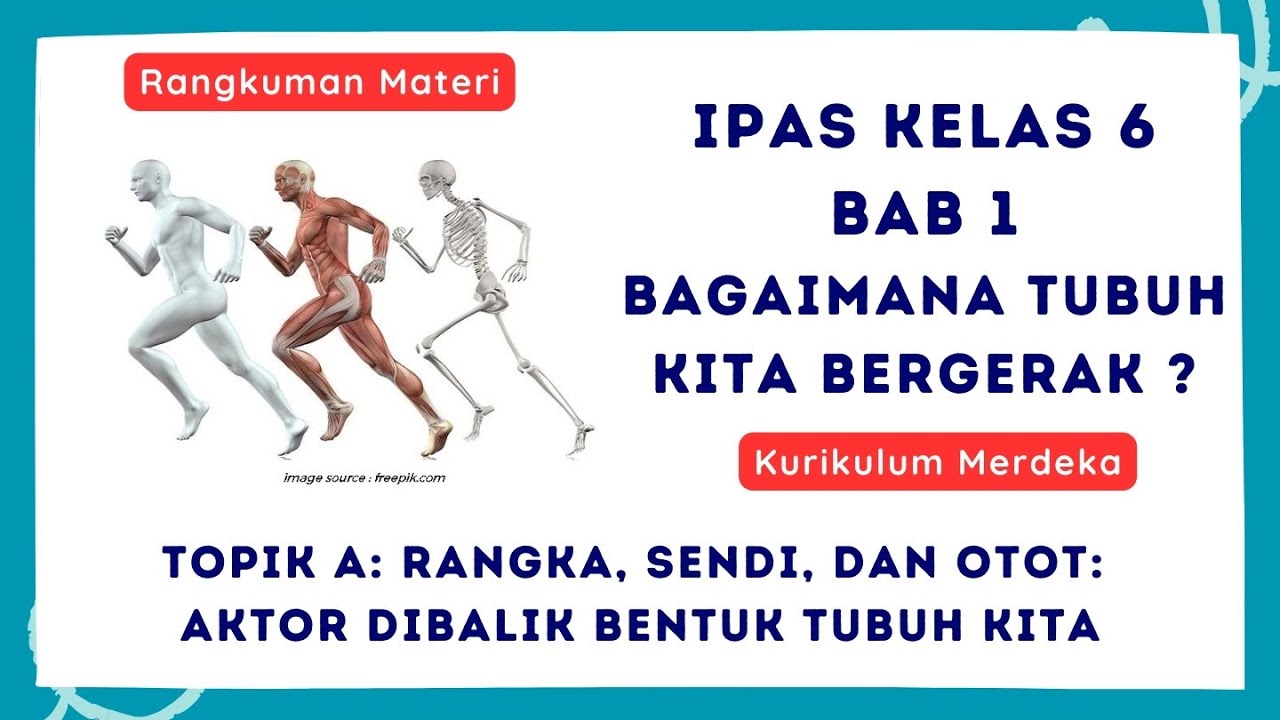
Rangkuman IPAS KELAS 6 BAB 1: Bagaimana Tubuh Kita Bergerak?. Topik A: Rangka, sendi, dan otot
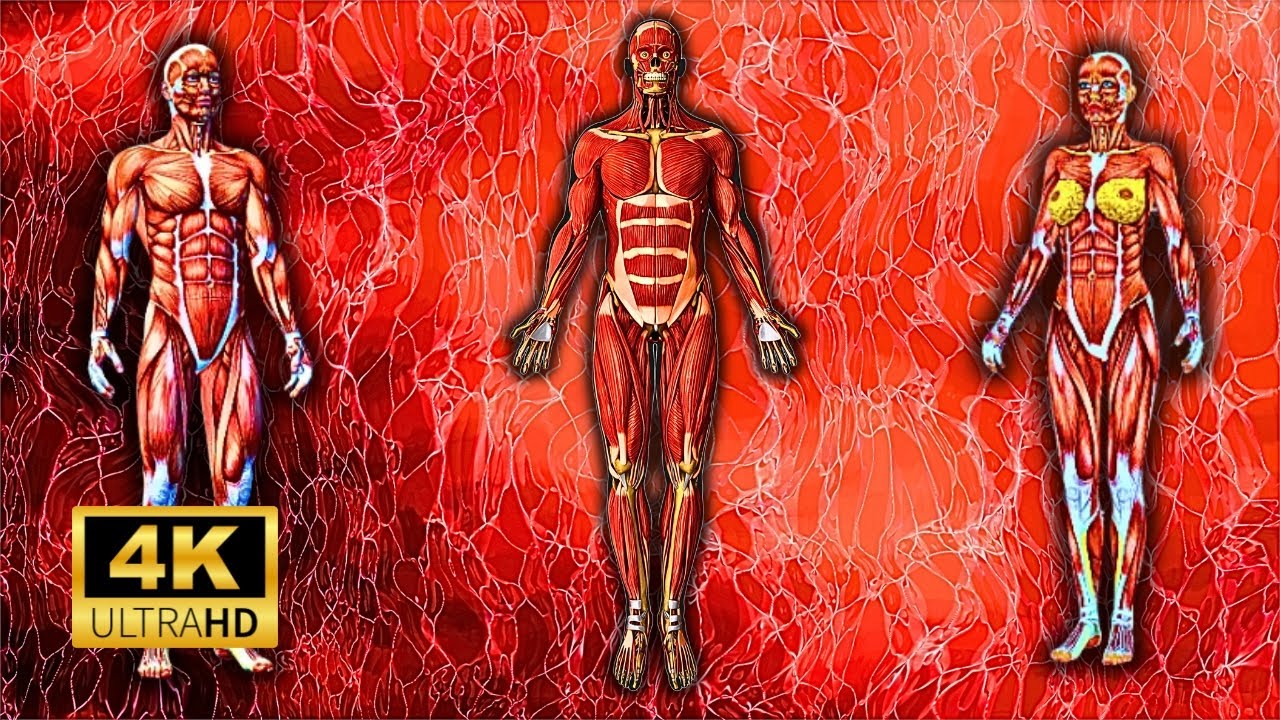
The Muscular System Explained In Less Than 4 Minutes!
5.0 / 5 (0 votes)