Key Factors in Plant Layout Selection
Summary
TLDRThis video from PGK Kadam Academy delves into the critical factors for selecting an optimal plant layout, emphasizing its role in fostering an efficient, safe production environment. Key considerations include product and process requirements, equipment specifications, material flow, workforce ergonomics, safety protocols, and sustainability practices. The video outlines how careful planning can enhance productivity, minimize costs, and ensure compliance with industry regulations. By integrating advanced technologies and lean principles, businesses can create adaptable layouts that support growth and continuous improvement in manufacturing operations.
Takeaways
- 😀 Consider product and process requirements to tailor the plant layout to specific production needs.
- 🔧 Assess equipment and machinery specifications to ensure optimal spacing and maintenance access.
- 📦 Design efficient material flow and handling processes to minimize bottlenecks and ensure smooth transitions.
- 👷 Prioritize workforce considerations, including safety, ergonomics, and appropriate workspaces for employees.
- 📏 Evaluate space utilization and constraints, accounting for building structure and potential future expansions.
- ⚠️ Implement safety measures and environmental considerations, including hazardous materials handling and fire safety.
- 💰 Account for cost and budget considerations, balancing initial investments with expected returns.
- 📜 Ensure compliance with regulatory and industry standards to meet safety and quality requirements.
- 🔄 Integrate technology and automation into the layout to enhance productivity and data-driven optimization.
- 🌱 Incorporate sustainable manufacturing practices to reduce the environmental footprint and enhance resource efficiency.
Q & A
What are the key factors to consider when selecting a plant layout?
-Key factors include product and process requirements, equipment and machinery considerations, material flow and handling, workforce and personnel considerations, space utilization, safety and environmental considerations, cost and budget considerations, regulatory compliance, quality management, technology integration, ergonomics, sustainable practices, and continuous improvement.
Why is it important to assess production volume and market demand?
-Assessing production volume and market demand helps determine the layout capacity needed to meet expected output and ensure the facility can respond to market needs effectively.
What considerations should be made regarding equipment and machinery in plant layout design?
-Considerations include the size and shape of the equipment, power requirements, maintenance needs, and ensuring that there is adequate spacing for safe and efficient operations.
How can material flow be optimized in a plant layout?
-Material flow can be optimized by designing efficient receiving areas, planning smooth movement of materials between production stages, and ensuring adequate storage space for finished goods.
What role does workforce safety play in plant layout design?
-Workforce safety is paramount; incorporating safety features and ergonomic design principles can help prevent accidents and injuries, promoting a healthier work environment.
What should be considered regarding space utilization?
-Consider the total available area, layout constraints, vertical space for equipment, and future growth plans to ensure effective space utilization.
What are some safety and environmental considerations for a plant layout?
-Implementing proper storage for hazardous materials, designing evacuation routes, ensuring fire safety systems are in place, and complying with environmental regulations are crucial safety and environmental considerations.
How do cost and budget considerations affect plant layout design?
-Cost considerations involve evaluating initial investments, operating expenses, expected ROI, and conducting cost-benefit analyses to justify design decisions based on financial impact.
What is the significance of regulatory compliance in plant layout?
-Regulatory compliance ensures that the plant layout meets industry standards and local building codes, which is essential for legal operation and safety.
How can technology integration enhance productivity in plant layouts?
-Integrating technology, such as automation and data-driven optimization systems, can streamline operations, improve precision, and enhance overall productivity.
Outlines
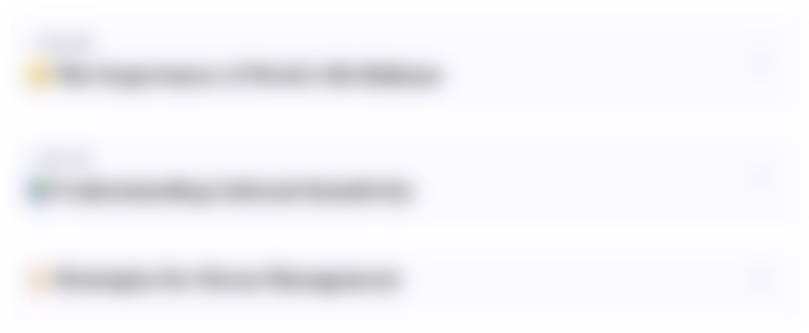
Этот раздел доступен только подписчикам платных тарифов. Пожалуйста, перейдите на платный тариф для доступа.
Перейти на платный тарифMindmap
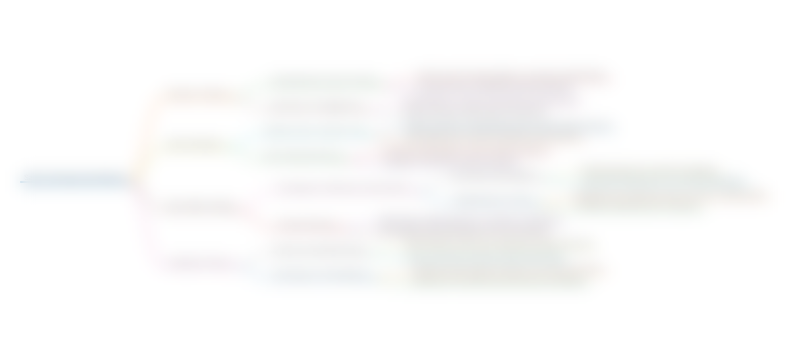
Этот раздел доступен только подписчикам платных тарифов. Пожалуйста, перейдите на платный тариф для доступа.
Перейти на платный тарифKeywords
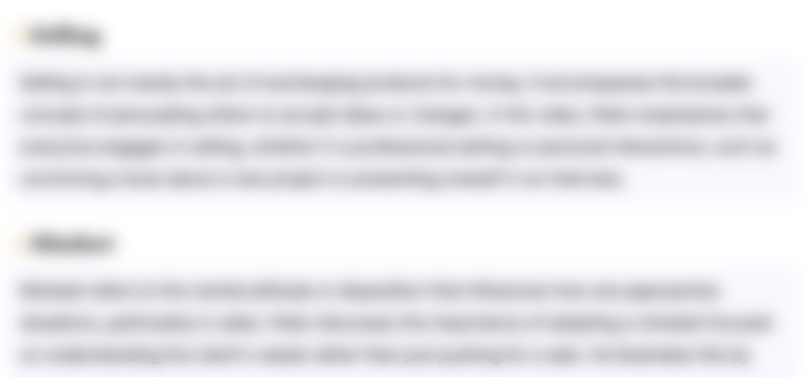
Этот раздел доступен только подписчикам платных тарифов. Пожалуйста, перейдите на платный тариф для доступа.
Перейти на платный тарифHighlights
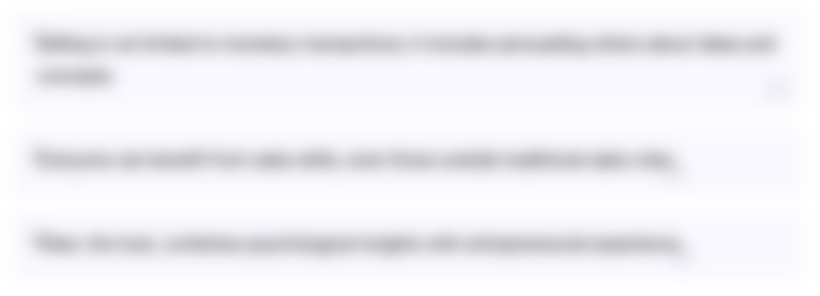
Этот раздел доступен только подписчикам платных тарифов. Пожалуйста, перейдите на платный тариф для доступа.
Перейти на платный тарифTranscripts
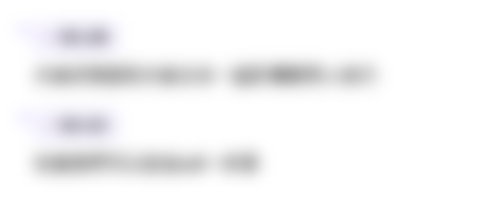
Этот раздел доступен только подписчикам платных тарифов. Пожалуйста, перейдите на платный тариф для доступа.
Перейти на платный тарифПосмотреть больше похожих видео
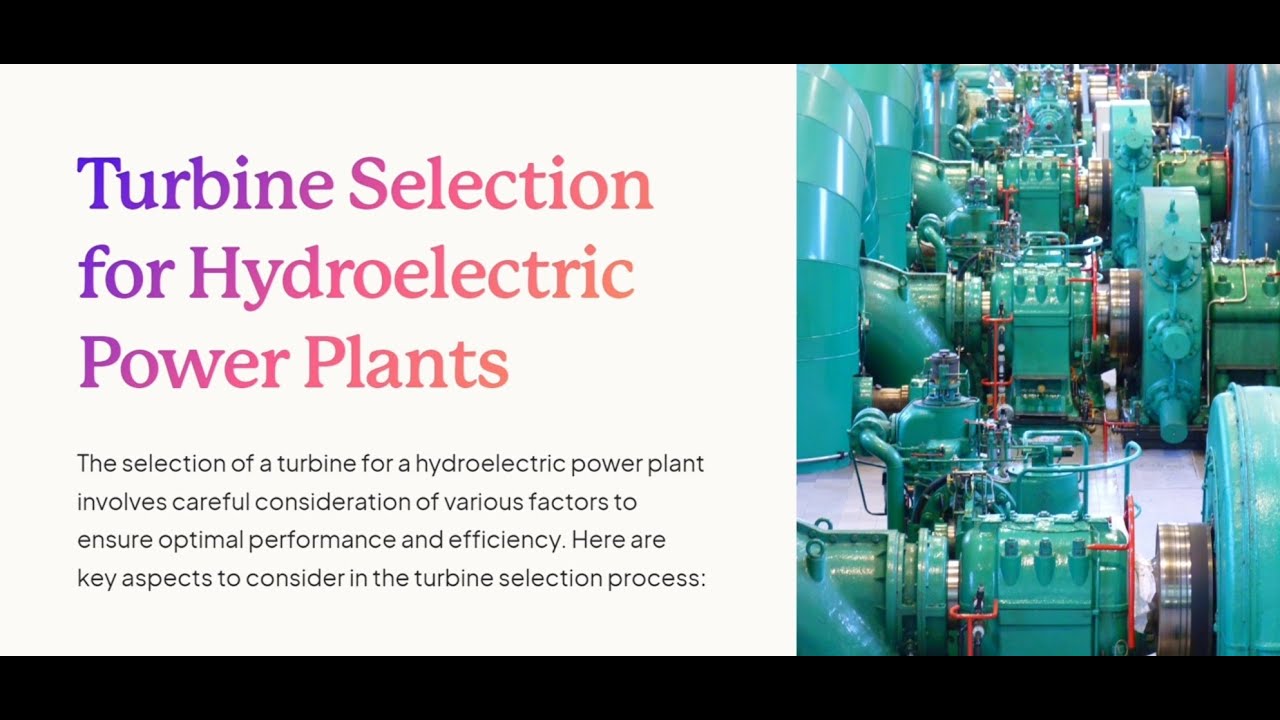
Selection of Turbine for Hydro plant #turbine

Tecnicas de Fertilizacion y Reproduccion Vegetal In Vitro - micropropagación - Juan Gonzalo Angel

Dairy Shed Design, Construction Plan Information | Dairy Cow Farming

Lec 19: Plant Layout: Types of Layout
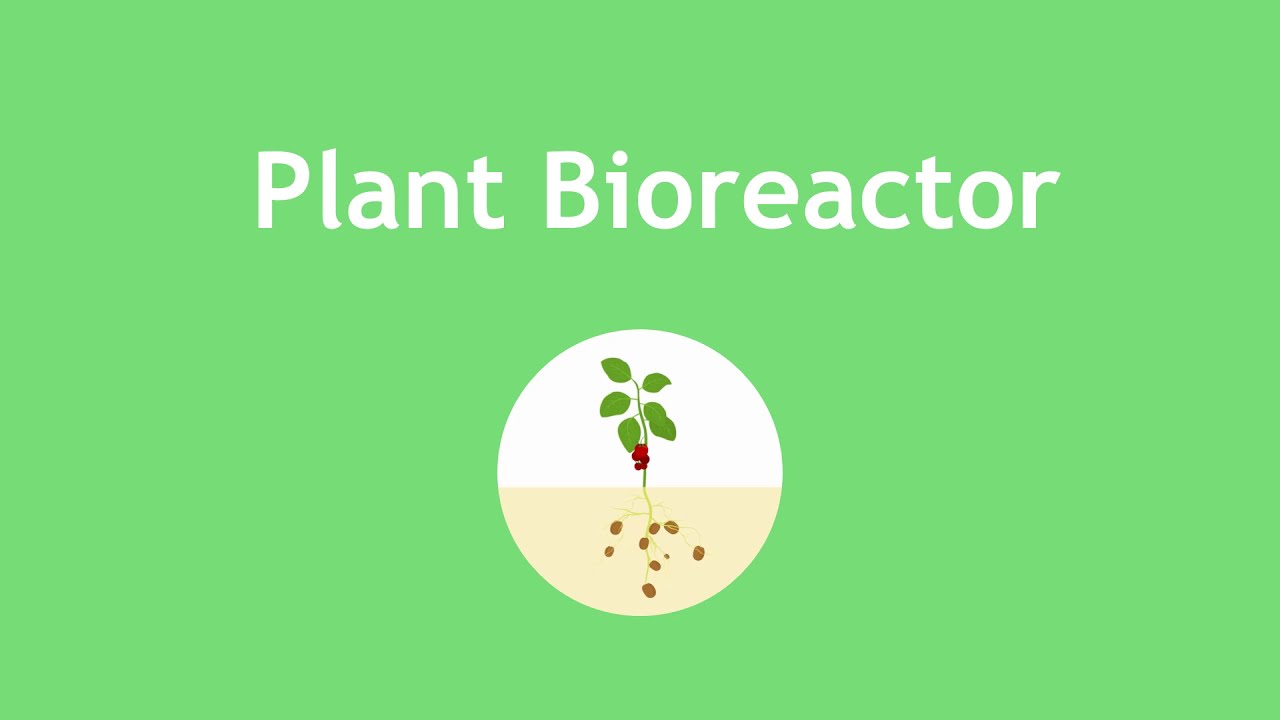
Plant Bioreactor
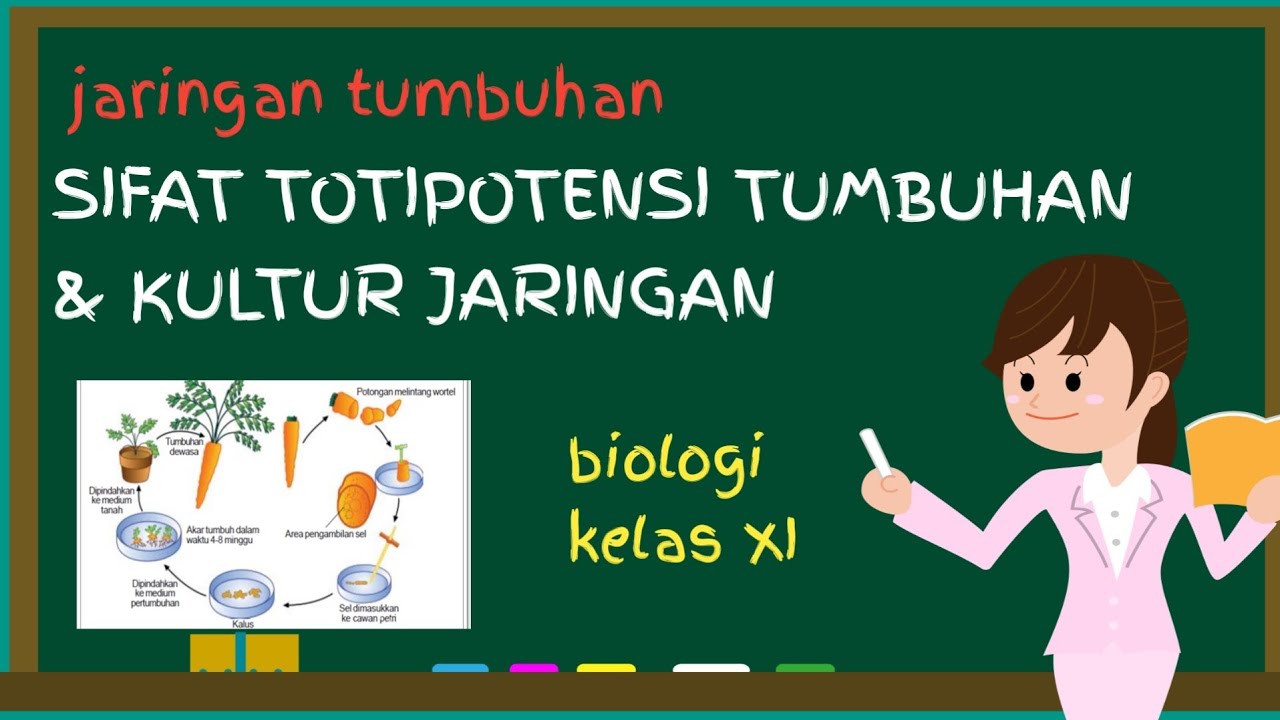
Jaringan Pada Tumbuhan Kelas 11 | Sifat Totipotensi Pada Tumbuhan Dan Kultur Jaringan
5.0 / 5 (0 votes)