How a Industrial Pneumatic Systems Works And The Five Most Common Elements Used
Summary
TLDRThis video explains how industrial pneumatic systems work, focusing on five common components used to automate processes, such as moving products or pressing them together. The system starts with a compressor that generates compressed air, which is cleaned and dried through an air preparation unit (FRL). The pressure is regulated to control force, and directional control valves guide the air to actuators, which convert the compressed air into motion. The actuator extends and retracts as needed to perform tasks like moving products or assembling components. Pneumatics provide versatile solutions in industrial automation.
Takeaways
- 🔧 Pneumatic systems are widely used in industrial settings to automate repetitive processes, primarily for creating motion.
- 💨 A compressor is the starting point in pneumatic systems, generating energy by compressing air from the atmosphere.
- 🌀 Compressed air is dried and cleaned to prevent harmful particulates like rust and dirt from damaging the system.
- ⚙️ The air preparation unit, or FRL, consists of a filter, regulator, and lubricator, which prepare the compressed air for use.
- 💧 The bulk liquid separator removes moisture through centrifugal force, while filters further clean the air of debris and moisture.
- 📏 A regulator adjusts the air pressure, controlling how much force the system generates depending on the desired application.
- 🔀 Directional control valves route the compressed air, enabling motion by shifting between different pathways.
- 🧲 A solenoid coil in the valve is controlled by a PLC, creating a magnetic field that shifts the valve to control airflow.
- 🔄 Actuators, like cylinders, convert the compressed air into motion, with the rod moving in response to air pressure.
- 📦 Pneumatic systems are commonly used to move products or press components together in industrial applications.
Q & A
What is the main purpose of pneumatic systems in industrial settings?
-The main purpose of pneumatic systems in industrial settings is to create motion that performs work, such as moving products or clamping pieces together in repetitive processes.
How does the compressor in a pneumatic system work?
-The compressor draws in atmospheric air, compresses it into a smaller space, and generates the energy needed to power the system in the form of compressed air.
What is the role of the air preparation unit in a pneumatic system?
-The air preparation unit, or FRL (Filter, Regulator, and Lubricator), dries and cleans the compressed air to remove moisture and particulates, ensuring that these do not clog the moving parts of the system.
Why is it necessary to adjust the air pressure in a pneumatic system?
-Adjusting the air pressure allows the system to control the amount of force generated. Higher pressure results in more force, while lower pressure generates less force, depending on the system's requirements.
How does the directional control valve function in directing air flow?
-The directional control valve uses internal pathways and a spool to direct compressed air to different working ports, depending on the position of the spool, which is controlled by a PLC or other control signals.
What role does the programmable logic controller (PLC) play in pneumatic systems?
-The PLC sends electrical signals to control the position of the directional control valve, which directs the compressed air flow to different working ports to achieve desired motion.
What happens when the solenoid coil in the valve receives a signal from the PLC?
-When the solenoid coil receives a signal, it creates a magnetic field that pulls a plunger, which in turn allows pilot pressure to move the spool in the valve, changing the direction of air flow.
What is the purpose of the actuator in a pneumatic system?
-The actuator, often a cylinder, converts the energy from compressed air into mechanical motion, typically to move or push objects as part of the industrial process.
How does the system achieve retraction of the actuator?
-Retraction is achieved by reversing the direction of compressed air through the directional control valve, which then pushes the piston back in the opposite direction, retracting the actuator rod.
What types of tasks can pneumatic actuators be used for in industrial applications?
-Pneumatic actuators can be used for tasks such as moving products from one place to another or pressing and clamping components together in an assembly process.
Outlines
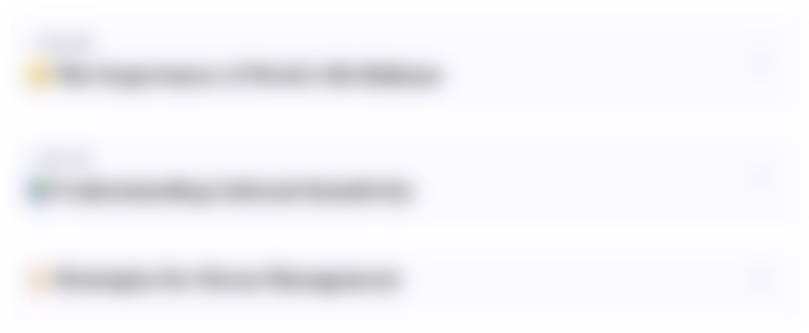
Этот раздел доступен только подписчикам платных тарифов. Пожалуйста, перейдите на платный тариф для доступа.
Перейти на платный тарифMindmap
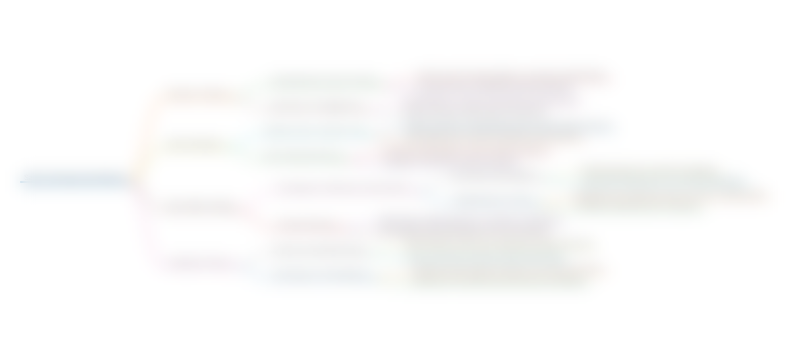
Этот раздел доступен только подписчикам платных тарифов. Пожалуйста, перейдите на платный тариф для доступа.
Перейти на платный тарифKeywords
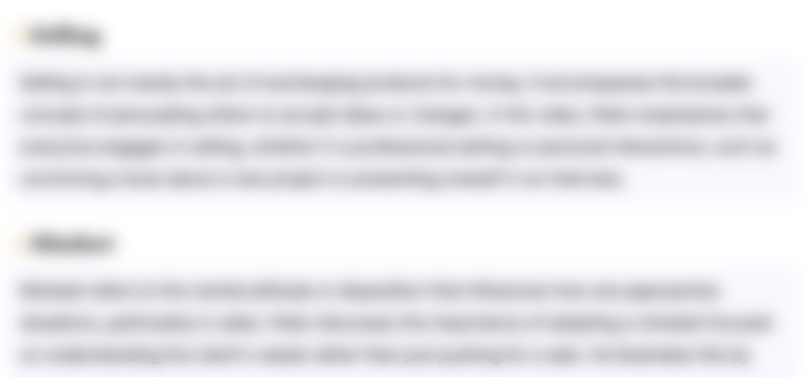
Этот раздел доступен только подписчикам платных тарифов. Пожалуйста, перейдите на платный тариф для доступа.
Перейти на платный тарифHighlights
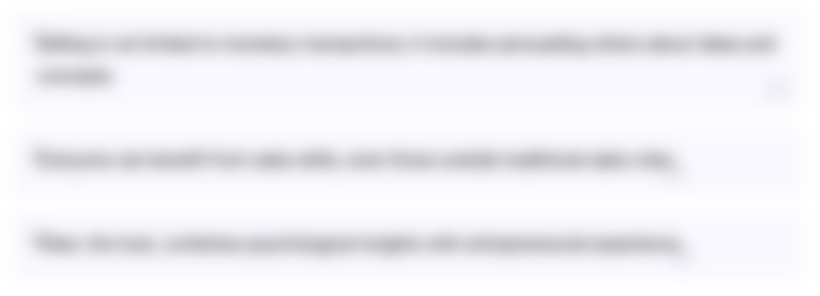
Этот раздел доступен только подписчикам платных тарифов. Пожалуйста, перейдите на платный тариф для доступа.
Перейти на платный тарифTranscripts
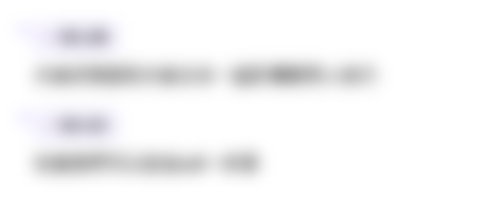
Этот раздел доступен только подписчикам платных тарифов. Пожалуйста, перейдите на платный тариф для доступа.
Перейти на платный тарифПосмотреть больше похожих видео
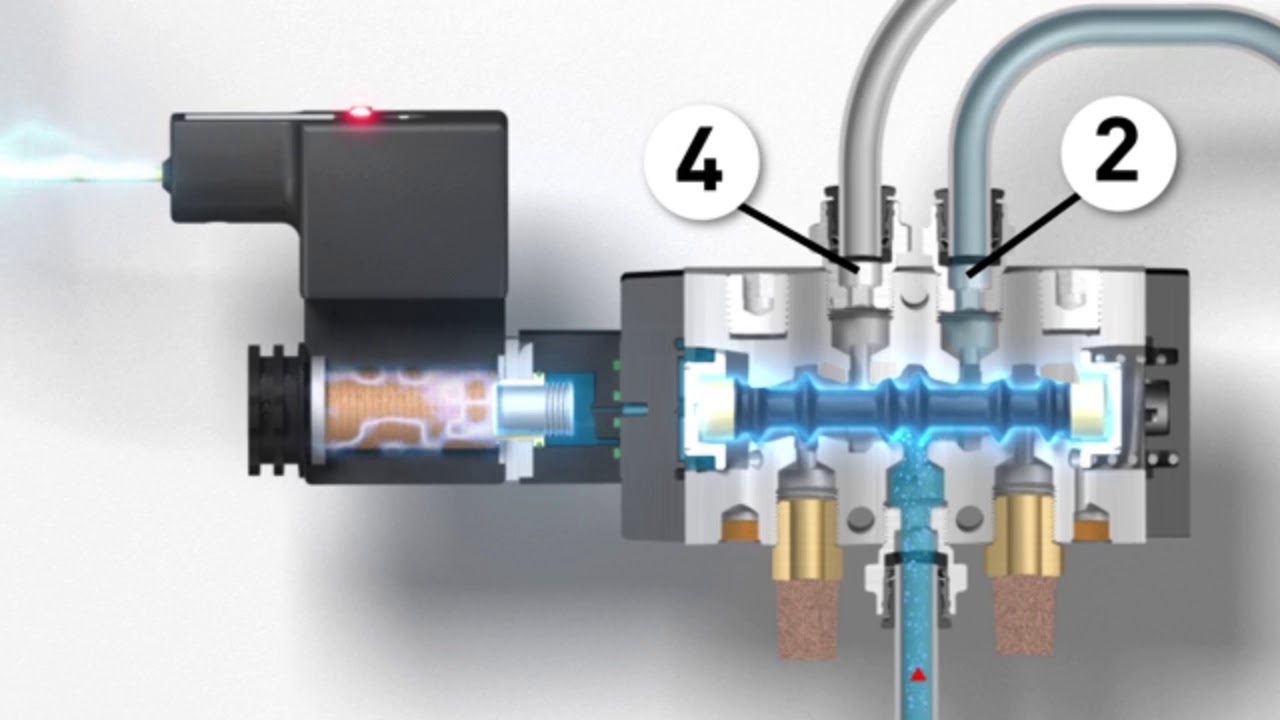
Neumática Industrial, ¿Cómo Trabaja un Sistema Neumático?

Tutorial Elektopneumatik : pengenalan komponen dan cara instalasi sistem elektro-pneumatik
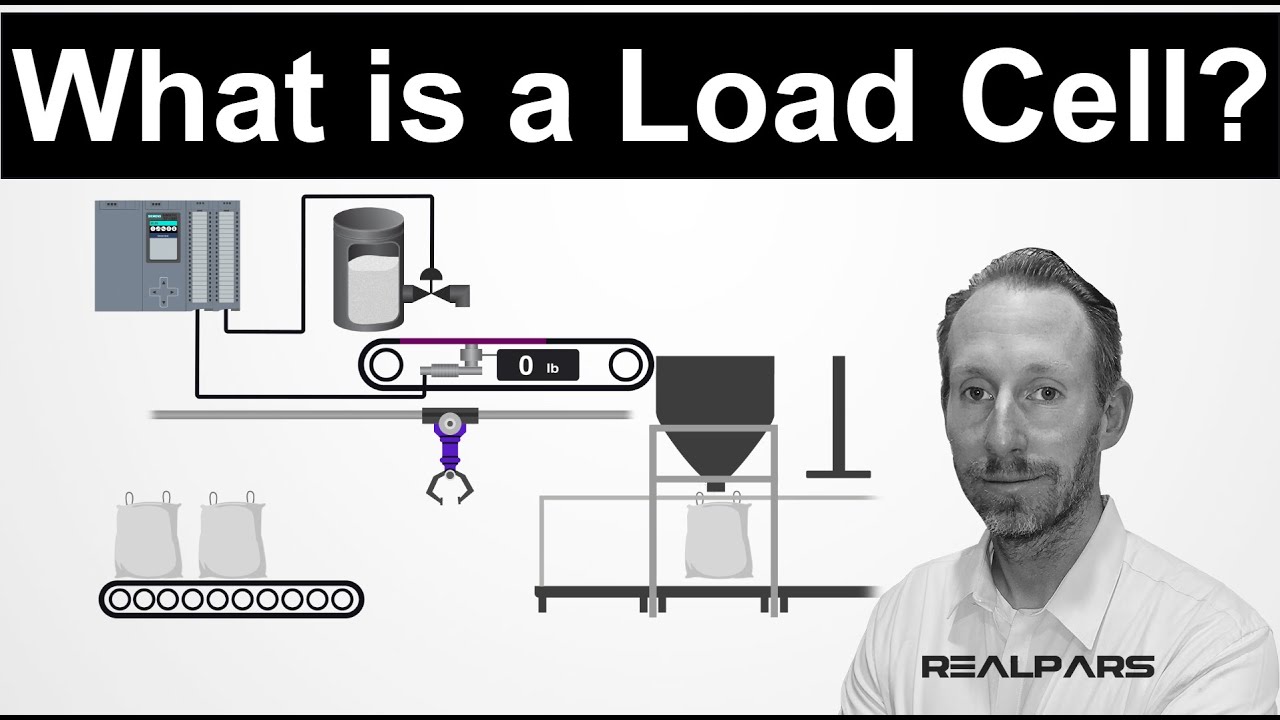
What is a Load Cell?
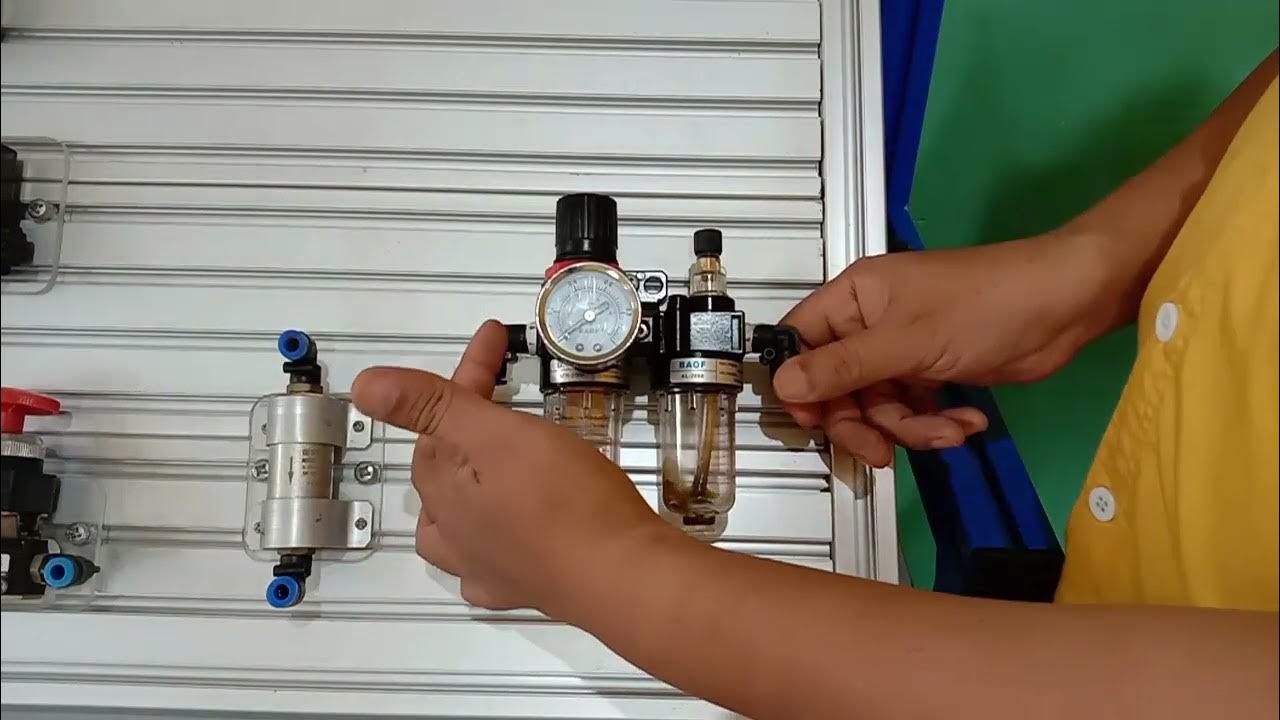
BAGIAN-BAGIAN SYSTEM PNEUMATIC
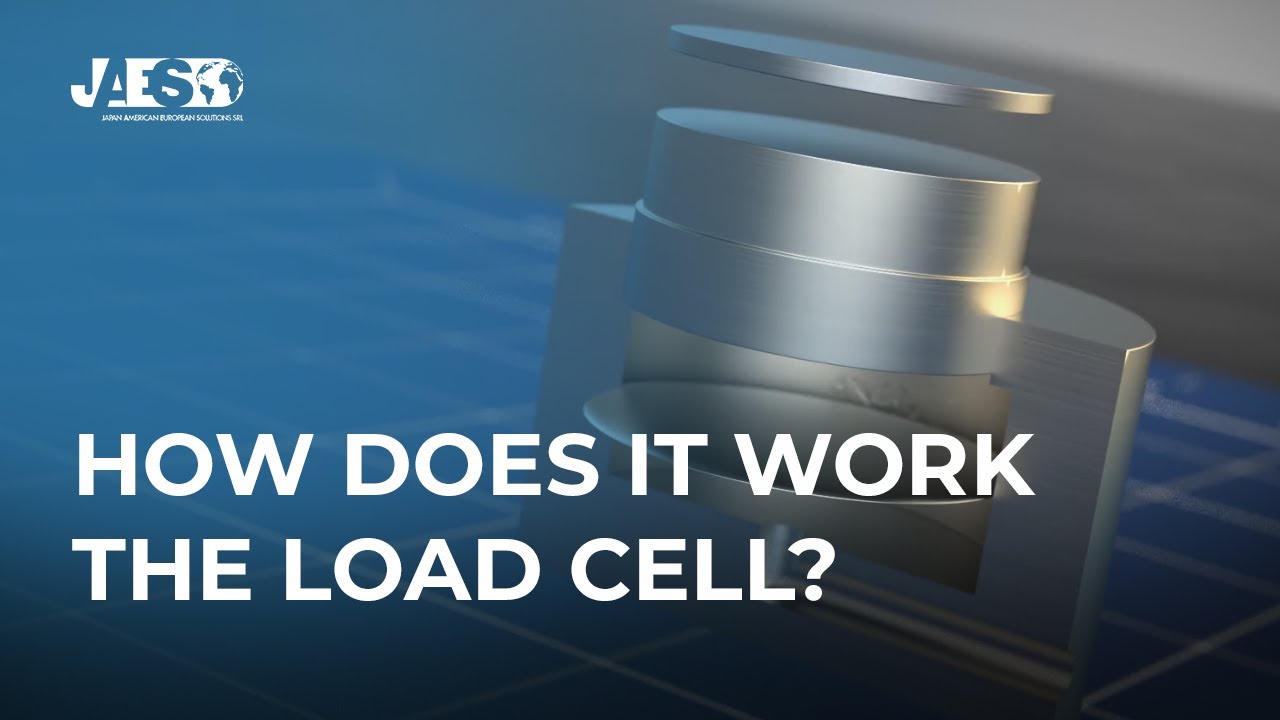
how does it work THE LOAD CELL? Hooke's law - strain gauge
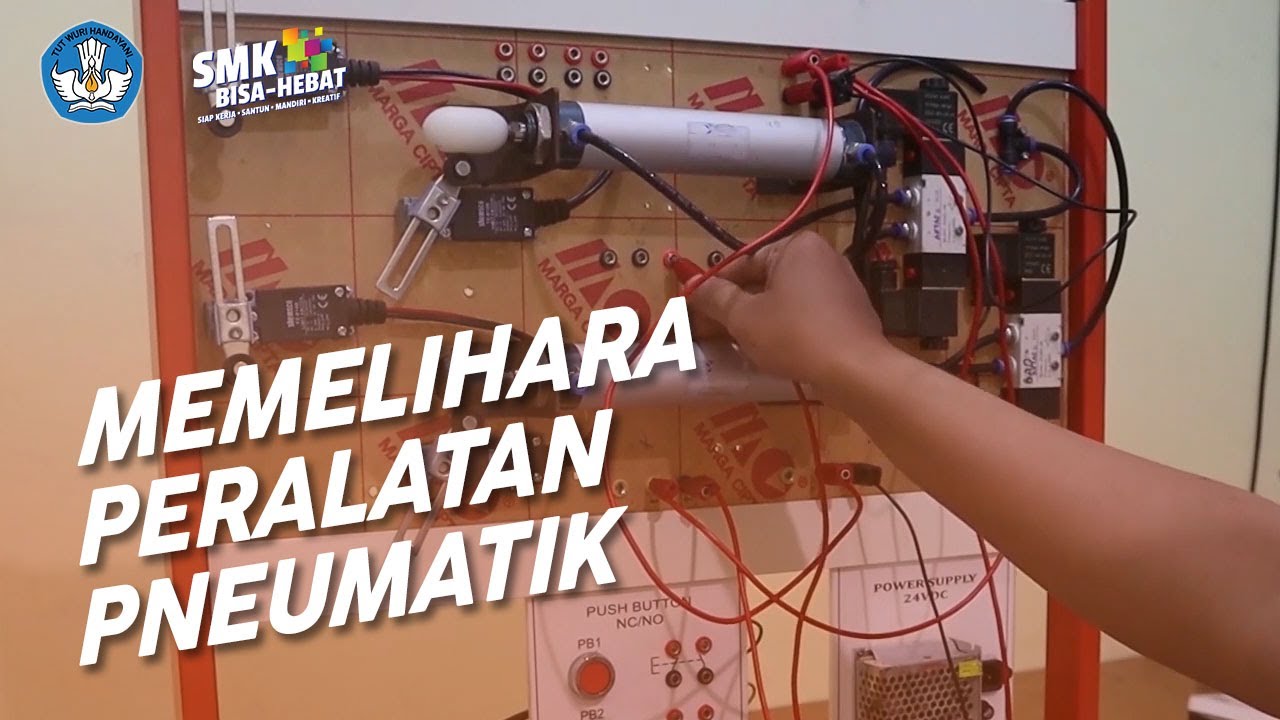
Memelihara Peralatan Pneumatik - Teknik Mekatronika
5.0 / 5 (0 votes)