Introduction to Inventory Management - Part 1
Summary
TLDRThe video discusses the importance of inventory management in financial management, emphasizing its role in converting resources into revenue. It outlines different types of inventory, such as raw materials, work-in-progress, and finished goods, while highlighting the costs associated with maintaining inventory, including purchase, ordering, holding, and shortage costs. The video also touches on the need to manage inventories effectively to meet demand, prevent losses, and stay competitive in the market. The speaker explains independent and dependent demand in relation to inventory management, offering insights into cost-saving strategies.
Takeaways
- 📦 Inventory management is crucial in financial management because it helps convert resources into cash, although it is not easily converted into quick cash.
- 🔄 Inventory is considered a physical resource that can be sold or transformed into a more valuable state, making it an essential asset.
- 🏭 Types of inventories include raw materials, purchased parts, finished goods, work-in-progress items, and tools, often seen in manufacturing setups.
- ⏳ Managing inventory involves determining how many units to order and when to order, considering associated costs and timing.
- 🎯 The main reasons for keeping inventories are to stabilize production, take advantage of price discounts, meet demand, prevent loss of orders, and stay competitive.
- 📈 Independent demand refers to finished goods, while dependent demand relates to parts needed to produce other products.
- ⚙️ Inventory control ensures that the right quantities of good quality items are available when needed in different departments.
- 💸 Inventory costs include purchase costs, ordering costs, holding (carrying) costs, and shortage costs, all of which need to be managed.
- 🚚 Purchase cost covers the expenses of acquiring and moving inventory through the logistics system, including transportation.
- 🏬 Holding cost involves storage, service, risk, and capital costs, while shortage cost arises when there isn't enough inventory, leading to potential business losses.
Q & A
Why is inventory management important in financial management?
-Inventory management is crucial because it directly impacts a company's liquidity and operational efficiency. Managing inventory ensures that businesses can convert physical resources into cash while minimizing costs and meeting customer demand.
What is the difference between current ratio and quick ratio in the context of inventory?
-The current ratio includes inventory because it is part of current assets, but the quick ratio excludes inventory since it is not easily converted into cash without significant effort.
What are the main types of inventories mentioned in the transcript?
-The main types of inventories are raw materials, purchased parts and supplies, finished goods, work in process (partially completed products), and tools and equipment.
What is meant by 'work in process' inventory?
-'Work in process' refers to partially completed products that are in the production stages but not yet finished goods ready for sale.
What are the reasons for keeping inventory?
-Inventory is maintained to stabilize production, take advantage of price discounts, meet demand during replenishment periods, prevent loss of orders, and keep up with changing market conditions.
What is the difference between independent demand and dependent demand?
-Independent demand refers to finished goods like computers that can be sold directly. Dependent demand refers to components or raw materials required to make other products, such as the motherboard in a computer.
What are the key functions of inventory in a business?
-The functions of inventory include meeting anticipated demand, smoothing production requirements, decoupling operations, protecting against stock-outs, taking advantage of order cycles and quantity discounts, and hedging against price increases.
What are the four main categories of inventory costs?
-The four main categories of inventory costs are purchase costs, ordering costs, holding (or carrying) costs, and shortage costs.
What does 'holding cost' entail?
-Holding cost includes the expenses associated with storing inventory, such as storage fees, insurance, and the risk of deterioration. It also includes the cost of capital tied up in the inventory.
What is 'shortage cost' and when does it occur?
-Shortage cost arises when there is insufficient inventory to meet demand, leading to additional expenses like urgent material purchases, premium transportation charges, or loss of business due to stock-outs.
Outlines
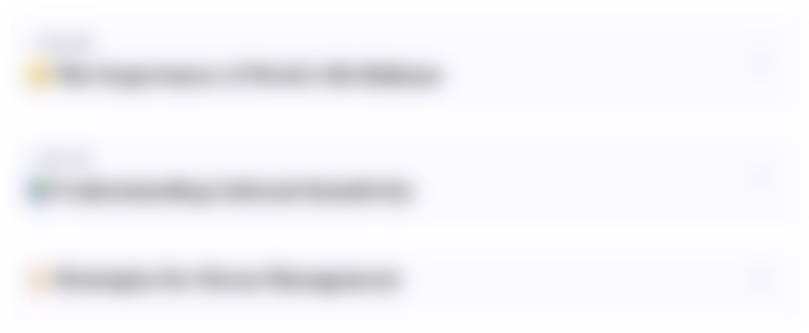
Этот раздел доступен только подписчикам платных тарифов. Пожалуйста, перейдите на платный тариф для доступа.
Перейти на платный тарифMindmap
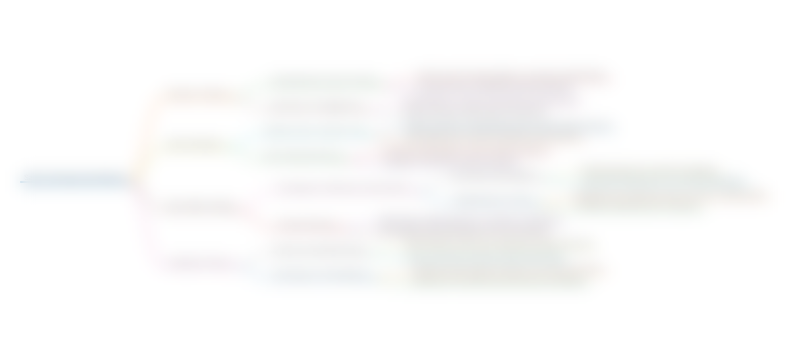
Этот раздел доступен только подписчикам платных тарифов. Пожалуйста, перейдите на платный тариф для доступа.
Перейти на платный тарифKeywords
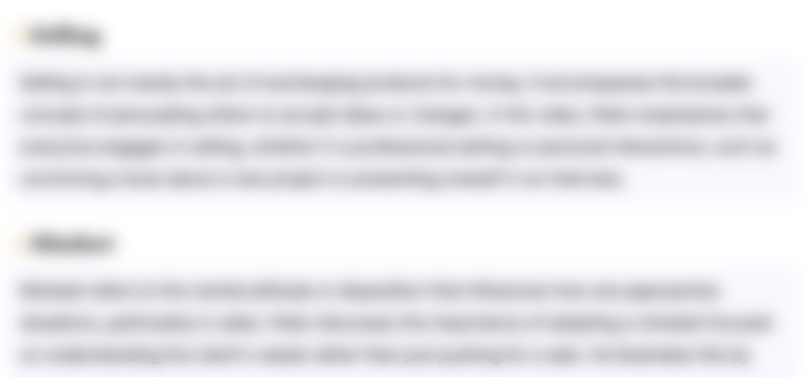
Этот раздел доступен только подписчикам платных тарифов. Пожалуйста, перейдите на платный тариф для доступа.
Перейти на платный тарифHighlights
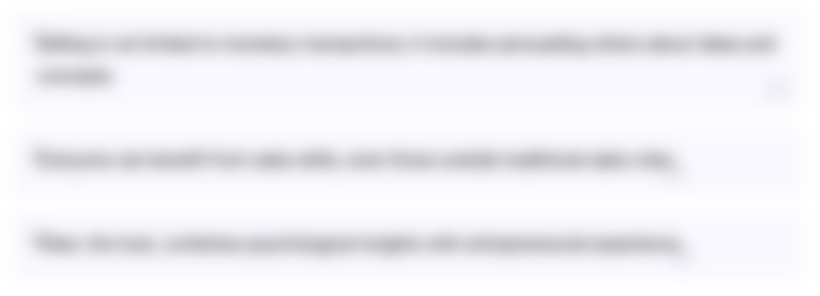
Этот раздел доступен только подписчикам платных тарифов. Пожалуйста, перейдите на платный тариф для доступа.
Перейти на платный тарифTranscripts
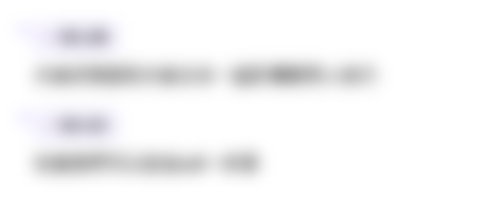
Этот раздел доступен только подписчикам платных тарифов. Пожалуйста, перейдите на платный тариф для доступа.
Перейти на платный тарифПосмотреть больше похожих видео

Inventory management
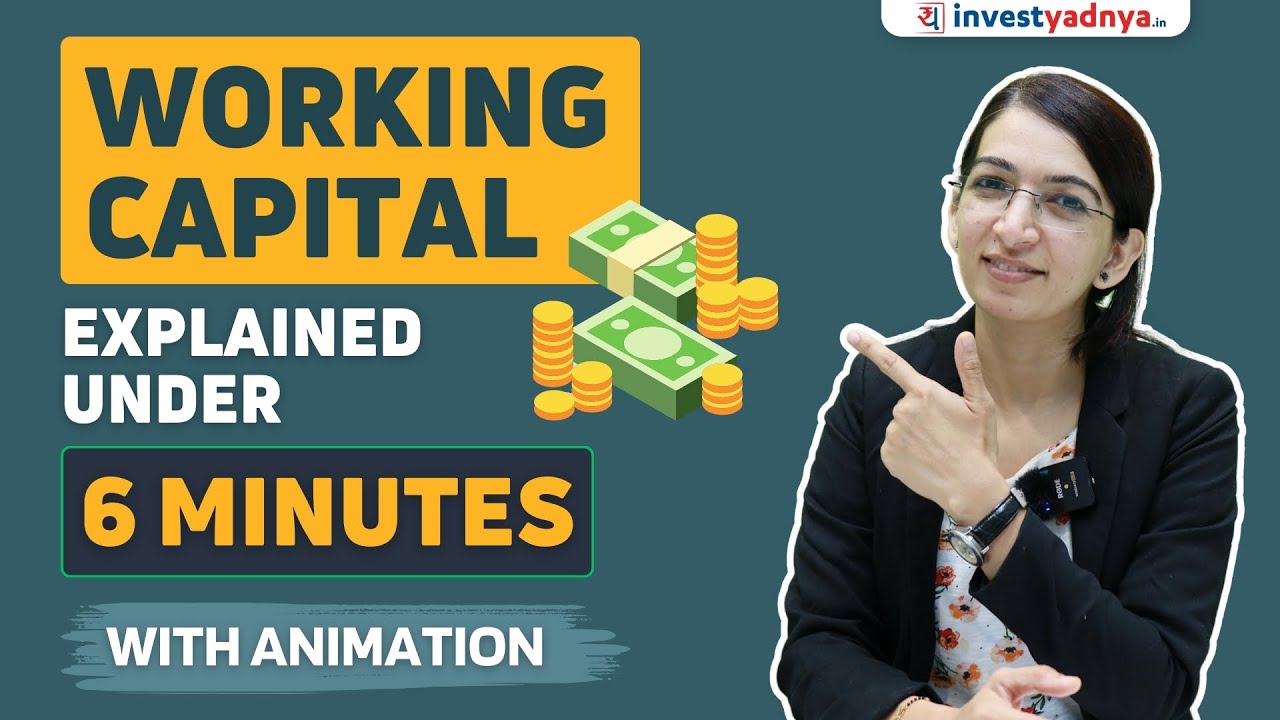
What is Working Capital? Working Capital Explained in Hindi

What is Asset management? Importance of Asset management | Asset management softwares.

MANAJEMEN BADAN USAHA - BADAN USAHA DALAM PEREKONOMIAN INDONESIA MATERI EKONOMI KELAS XI SEMESTER 1

MITSCXX1T314-V030100
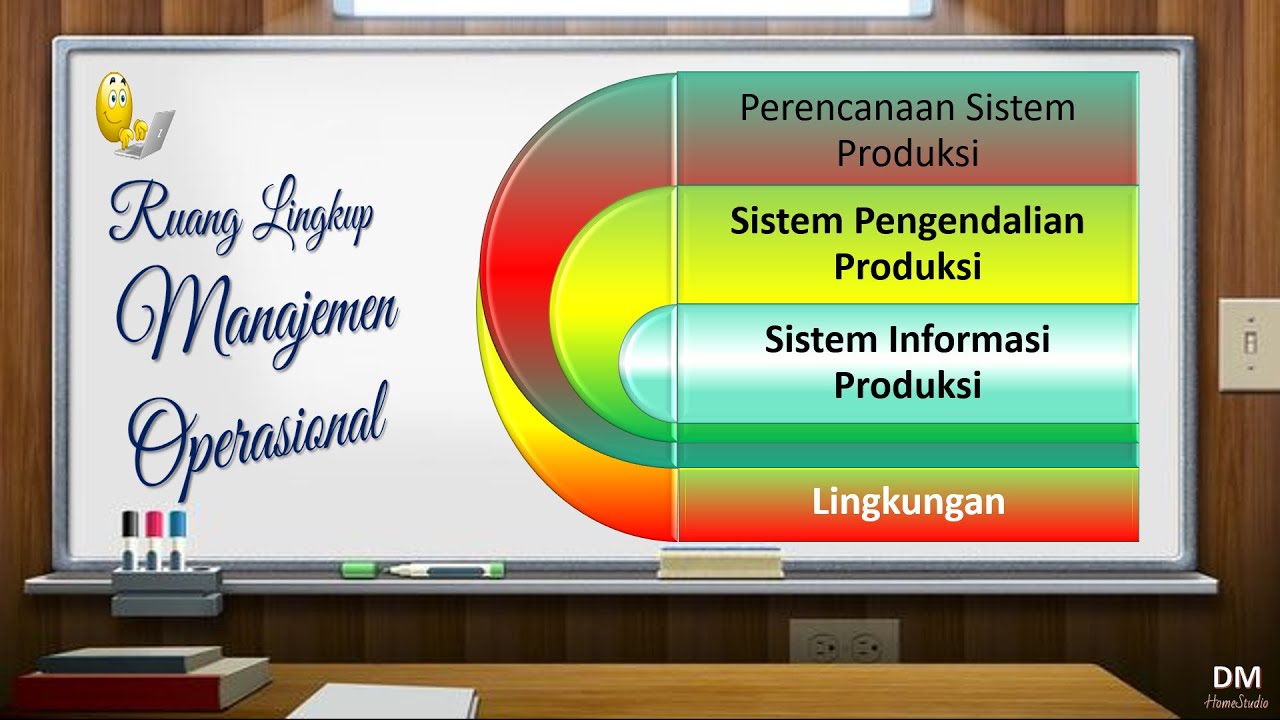
Pengantar Manajemen Operasional
5.0 / 5 (0 votes)