Compressors Part 1 - Aircraft Gas Turbine Engines #05
Summary
TLDRThis script discusses the mechanics of gas turbine engines, focusing on the two primary compressor types: axial flow and centrifugal. It explains how these compressors, driven by a turbine, increase engine efficiency by compressing air before combustion. The axial flow compressor, capable of higher compression ratios and greater air intake, is more suitable for modern engines despite the centrifugal's historical prevalence. The script also delves into the principles of each compressor, detailing the conversion of kinetic energy to pressure and the challenges of maintaining efficiency across varying engine speeds, including the risks of stall and surge.
Takeaways
- 🔧 To enhance the efficiency of gas turbine engines, air must be compressed before fuel is added and combustion occurs.
- ⚙️ There are two main types of compressors used in engines: axial flow and centrifugal flow.
- 🔩 The centrifugal compressor was initially preferred due to its robustness and ease of manufacturing.
- 📉 However, the centrifugal compressor has limitations, such as lower air intake capacity and compression ratios compared to axial flow compressors.
- ⏫ Axial flow compressors can achieve higher compression ratios and are more suitable for large, modern engines.
- 🔄 The centrifugal compressor works by converting the kinetic energy of the air into pressure through an impeller and diffuser.
- 🌀 In a centrifugal compressor, approximately 50% of the pressure rise occurs in the impeller and the other 50% in the diffuser.
- 🚫 The use of more than two centrifugal compressor stages in series is not feasible due to high tip speeds and centrifugal loading.
- 🌐 The axial flow compressor consists of multiple stages with rotor and stator blades, converting air velocity into pressure incrementally.
- 🔁 Modern engines may use a combination of centrifugal and axial compressors, or multiple spools, to achieve high compression ratios.
- 💨 Efficient operation across the entire speed range of a compressor is challenging due to the interdependent relationship between compression ratio and engine RPM.
Q & A
What is the purpose of compressing air before it is fed into a gas turbine engine?
-The purpose of compressing air before it is fed into a gas turbine engine is to increase the efficiency of the engine. The compressed air is mixed with fuel and burned in the combustion chambers, and the subsequent expansion in the turbines drives the engine.
What are the two types of compressors used in gas turbine engines?
-The two types of compressors used in gas turbine engines are the axial flow compressor and the centrifugal compressor.
Why was the centrifugal compressor the compressor of choice in early gas turbine engines?
-The centrifugal compressor was the compressor of choice in early gas turbine engines because it is more robust than the axial flow compressor and is easier and cheaper to manufacture.
What are the disadvantages of the centrifugal compressor compared to the axial flow compressor?
-The centrifugal compressor has disadvantages such as a lower capacity to intake air and a lower achievable compression ratio compared to the axial flow compressor, which makes it less efficient in large modern engines.
How does the axial flow compressor differ from the centrifugal compressor in terms of air intake?
-The axial flow compressor can intake a far greater mass of air than the centrifugal compressor when both have the same frontal cross-sectional area.
What is the role of the turbine assembly in a gas turbine engine?
-The turbine assembly converts the pressure, velocity, and heat of the gases passing through the turbine into mechanical energy, which is used to drive the impeller of the compressor at high speed.
How does the diffuser section in a centrifugal compressor contribute to the compression process?
-The diffuser section in a centrifugal compressor is a system of stationary divergent ducts that convert the kinetic energy of the airstream into potential energy, or pressure.
What is the typical compression ratio for a single stage centrifugal compressor?
-A very efficient single stage centrifugal compressor would have a compression ratio in the region of four to one, meaning the outlet pressure is four times greater than its inlet pressure.
Why is it not feasible to use more than two centrifugal compressor stages in series?
-It is not feasible to use more than two centrifugal compressor stages in series due to excessive impeller tip speeds and extreme centrifugal loading, which prohibit efficient operation of a third stage.
How does the axial flow compressor achieve the conversion of kinetic energy into pressure energy?
-The axial flow compressor achieves the conversion of kinetic energy into pressure energy through a series of stages, each consisting of a row of rotor blades followed by a row of stator vanes, which increase the air pressure by converting kinetic energy into pressure energy.
What is the significance of the air annulus in an axial flow compressor?
-The air annulus is the space between the rotor drum and the compressor outer casing. It is significant because it helps maintain the axial velocity of the air reasonably constant as it passes through the compressor, which is necessary as the air is compressed into a smaller volume and its density increases.
What is the phenomenon called 'stall' in the context of compressors, and what can it lead to?
-Stall is a partial breakdown of the airflow through the engine, caused by a reduction in axial velocity to a point where turbulent airflow occurs. If not checked, it may lead to a condition called 'surge', which is a total breakdown of the airflow through the engine, potentially causing the airflow to instantaneously reverse its direction.
Outlines
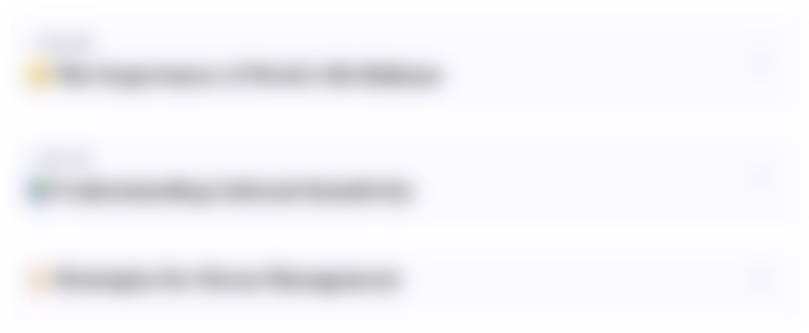
Этот раздел доступен только подписчикам платных тарифов. Пожалуйста, перейдите на платный тариф для доступа.
Перейти на платный тарифMindmap
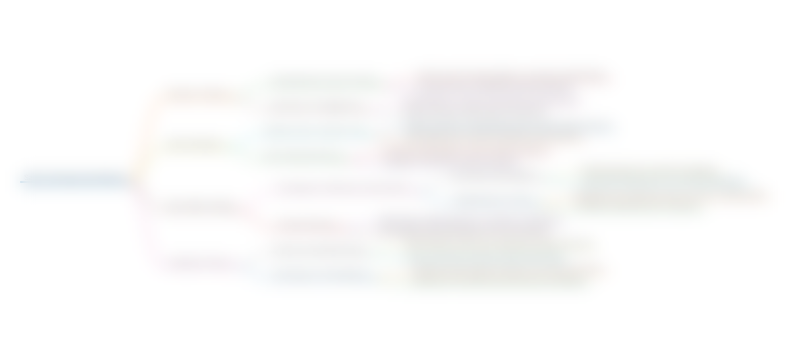
Этот раздел доступен только подписчикам платных тарифов. Пожалуйста, перейдите на платный тариф для доступа.
Перейти на платный тарифKeywords
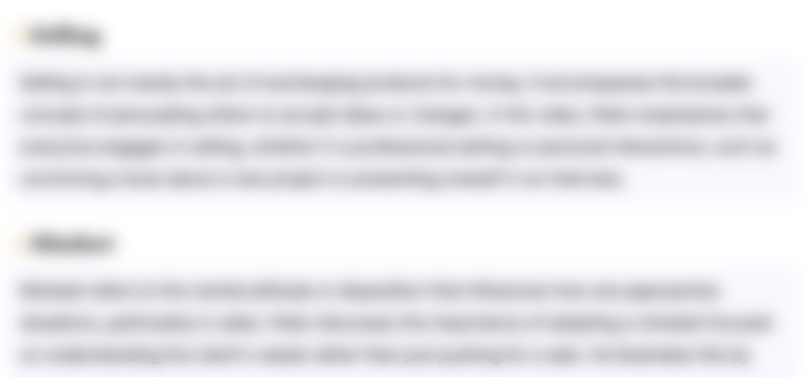
Этот раздел доступен только подписчикам платных тарифов. Пожалуйста, перейдите на платный тариф для доступа.
Перейти на платный тарифHighlights
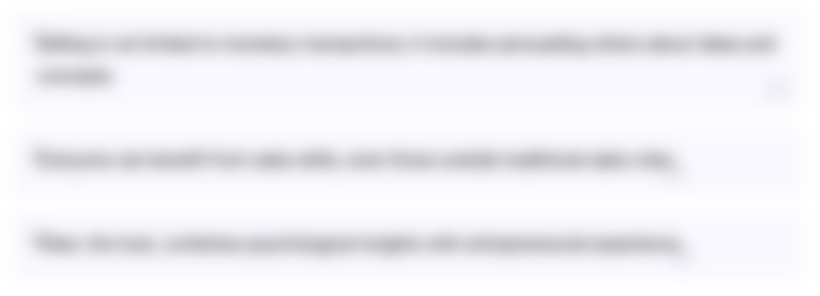
Этот раздел доступен только подписчикам платных тарифов. Пожалуйста, перейдите на платный тариф для доступа.
Перейти на платный тарифTranscripts
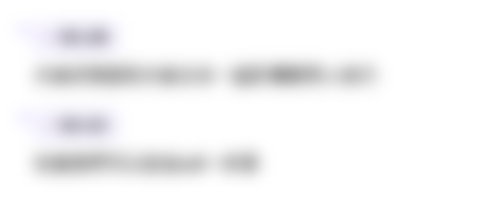
Этот раздел доступен только подписчикам платных тарифов. Пожалуйста, перейдите на платный тариф для доступа.
Перейти на платный тарифПосмотреть больше похожих видео

01 ATPL Training Gas Turbine Engines #01 Introduction Part 1
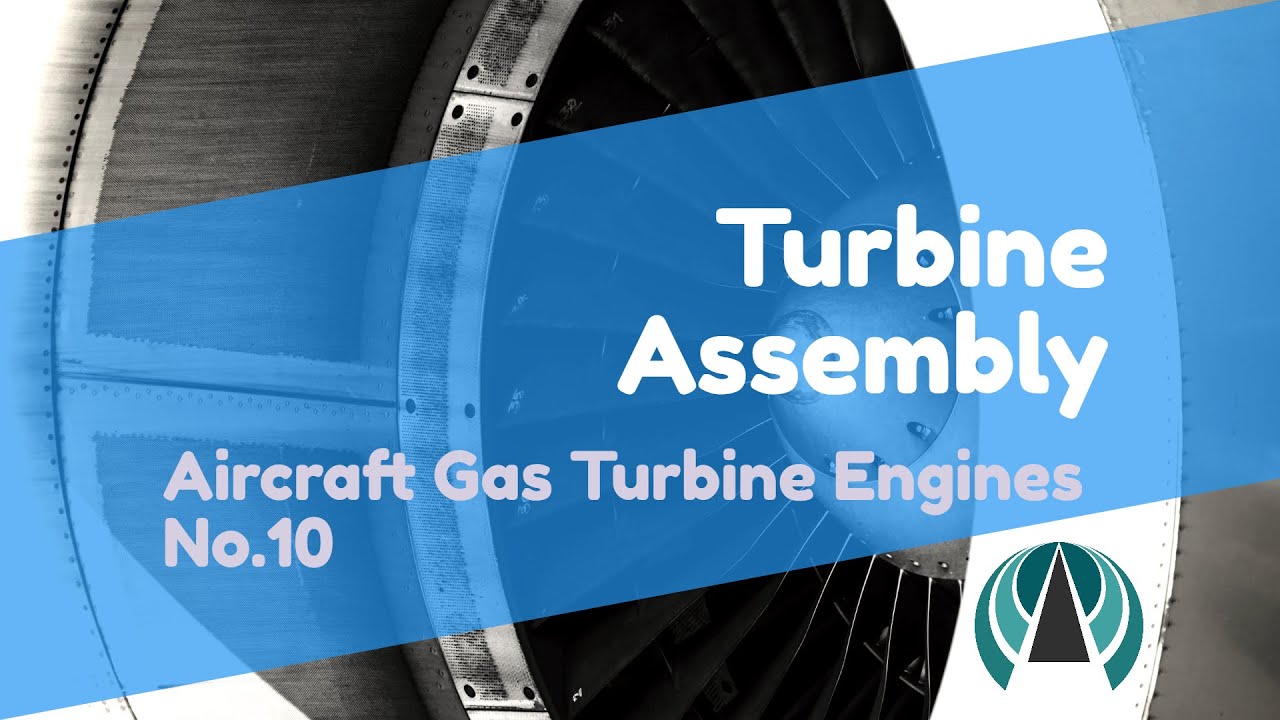
Turbine Assembly - Aircraft Gas Turbine Engines #10
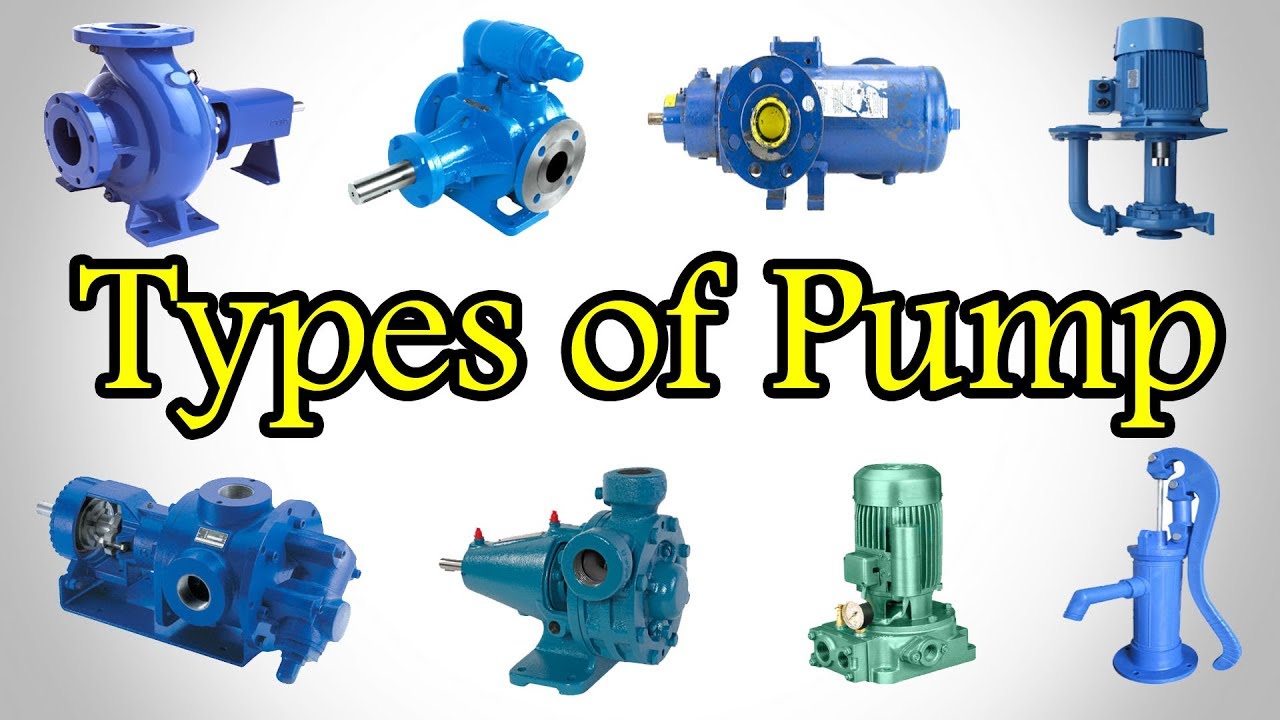
Pumps Types - Types of Pump - Classification of Pumps - Different Types of Pump
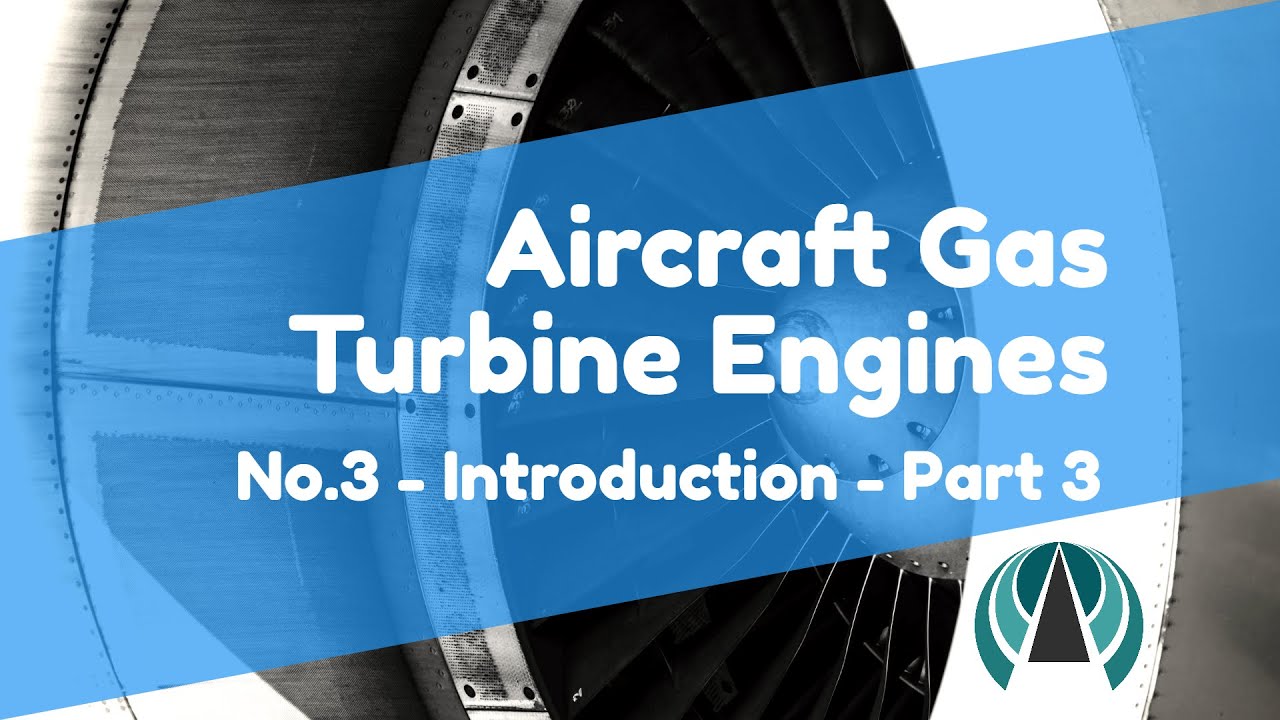
Aircraft Gas Turbine Engines #03 - Introduction Part 3
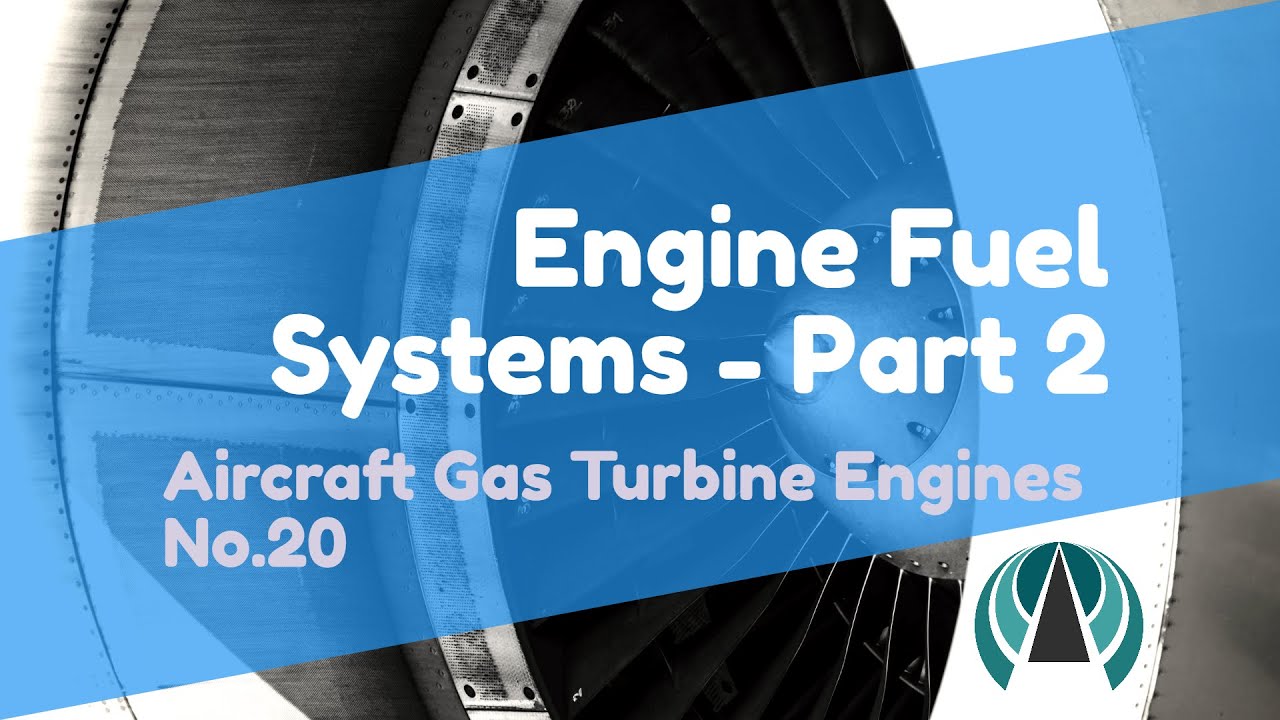
Engine Fuel Systems Part 2 - Aircraft Gas Turbine Engines #20
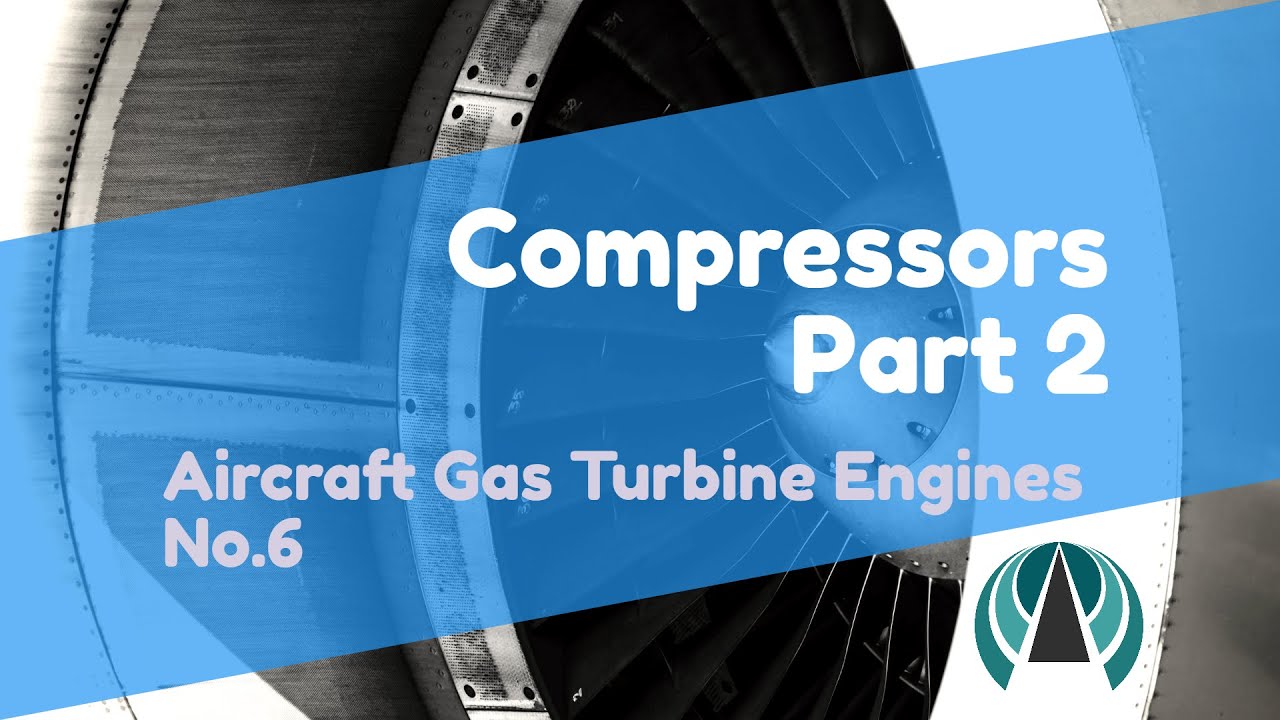
Compressors Part 2 - Aircraft Gas Turbine Engines #06
5.0 / 5 (0 votes)