High Pressure Processing Alberta
Summary
TLDRIn this high-pressure processing (HPP) demonstration, Dana Pierce walks viewers through the inner workings of an HPP machine. The process begins with loading product canisters into the pressure vessel, which is secured by a yoke and plugs to withstand immense pressure. Water fills the vessel to create pressure up to 87,000 psi. The demonstration highlights how different products, like juices, salad dressings, and meats, are processed, maintaining packaging integrity and enhancing safety. The video underscores the efficiency of HPP in food preservation, showcasing both successful and failed packaging tests.
Takeaways
- ⚙️ The demonstration takes place at a high-pressure processing facility, highlighting the internal mechanisms of the machine.
- 🔧 The machine's pressure vessel is a key component, where the canisters are loaded, and the vessel moves into the working position to process the products.
- 🛠️ The yoke is a thick piece of metal surrounding the pressure vessel, designed to withstand over 4,000 tons of pressure, crucial for holding the vessel's plugs and water in place.
- 💧 Once the plugs are secured, water fills the vessel, and pressure is increased to 87,000 psi (600 mega Pascals), maintained for 180 seconds to complete the high-pressure process.
- 🔊 A loud noise marks the end of the pressure cycle, as water drains from the vessel and the canisters are pushed out to make room for the next batch.
- 🚚 After the pressure process, the products undergo downstream processing, where excess moisture is shaken off, and the products are dried before packaging.
- 📦 The high-pressure method can process a variety of products, such as juices, salad dressings, and pepperoni, without compromising packaging integrity.
- 🥩 The process denatures proteins, causing raw products like chicken to appear cooked even though they remain uncooked.
- 🍓 Some products, like fruits with fragile skins, can have issues with integrity during high-pressure processing, but using water as a buffer helps maintain product quality.
- ✅ High-pressure processing offers efficiency in handling certain product types and ensures safety by removing pathogens, while also identifying packaging failures early.
Q & A
What is the purpose of the high-pressure processing (HPP) demonstration in the video?
-The purpose of the demonstration is to showcase how high-pressure processing (HPP) works, using a specialized machine to process food products under extremely high pressure to ensure safety and quality.
What are the main components of the high-pressure processing machine?
-The machine has three main components: the pressure vessel, the yoke, and the plugs. The yoke surrounds the pressure vessel and holds the plugs in place, allowing the machine to achieve high pressure.
Why is the yoke an important component in the machine?
-The yoke is crucial because it is built to withstand over 4,000 tons of pressure. It holds the plugs in place when the vessel is pressurized, ensuring the high-pressure environment needed for processing.
How does the high-pressure process work in the machine?
-The process begins by loading the product into the pressure vessel. Water fills the vessel, and the pressure is increased to 87,000 psi. This pressure is maintained for a set amount of time before the vessel is drained, and the product is unloaded.
What is the role of water in the high-pressure process?
-Water fills the pressure vessel and helps to create the high-pressure environment needed to process the food. It acts as a medium that transmits pressure evenly across the product inside the vessel.
What happens to the product after it undergoes high-pressure processing?
-After processing, the product is unloaded from the machine and sent for downstream processing. This includes shaking off excess moisture and drying the product before final packaging.
Why are certain packaging materials, such as plastic bottles, able to withstand high pressure?
-Plastic bottles can withstand high pressure due to their geometry and material properties. Even after being compressed, the bottles return to their original shape without damaging the packaging.
What types of products are unsuitable for high-pressure processing?
-Products with air pockets, such as styrofoam or certain types of fresh fruits and vegetables, may not withstand high-pressure processing because the air inside can be compressed and damage the product.
How does high-pressure processing affect the color of meat products like chicken breast?
-High-pressure processing can cause protein denaturation in meat, changing its color. Although the chicken breast may appear fully cooked after the process, it remains raw.
What is one advantage of high-pressure processing in terms of product quality control?
-One advantage of high-pressure processing is that it can help identify packaging or product failures, such as a broken seal or compromised packaging, which can improve overall product safety and quality.
Outlines
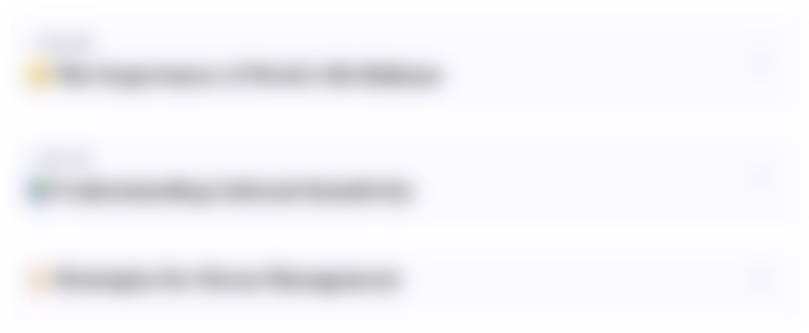
Этот раздел доступен только подписчикам платных тарифов. Пожалуйста, перейдите на платный тариф для доступа.
Перейти на платный тарифMindmap
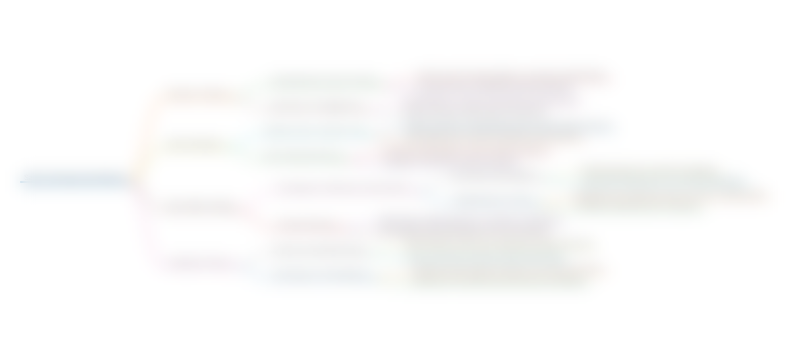
Этот раздел доступен только подписчикам платных тарифов. Пожалуйста, перейдите на платный тариф для доступа.
Перейти на платный тарифKeywords
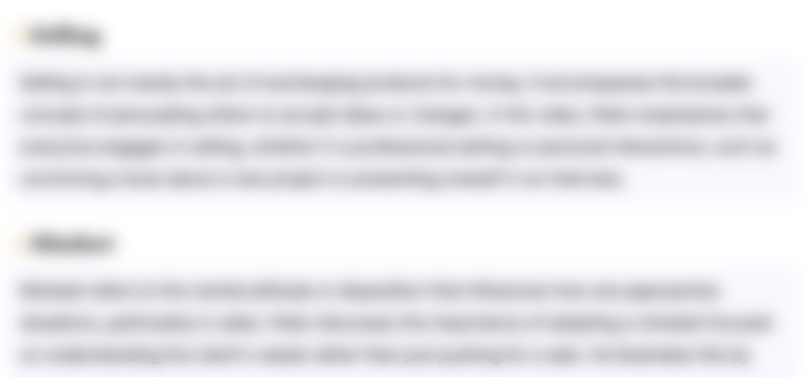
Этот раздел доступен только подписчикам платных тарифов. Пожалуйста, перейдите на платный тариф для доступа.
Перейти на платный тарифHighlights
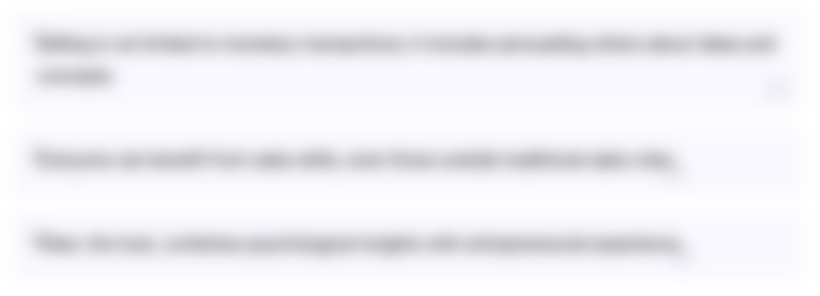
Этот раздел доступен только подписчикам платных тарифов. Пожалуйста, перейдите на платный тариф для доступа.
Перейти на платный тарифTranscripts
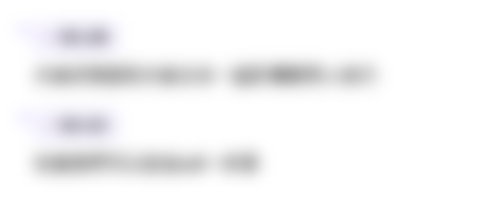
Этот раздел доступен только подписчикам платных тарифов. Пожалуйста, перейдите на платный тариф для доступа.
Перейти на платный тарифПосмотреть больше похожих видео
5.0 / 5 (0 votes)