Battery driven Electric vehicle with regenerative Braking operation | Electric vehicle Simulation |
Summary
TLDRThis video tutorial explores a Matlab simulation model for a battery-driven electric vehicle with regenerative braking. It covers the model's components like the battery, bidirectional DC-DC converter, and DC motor, controlled by a speed control method with a PID controller. The simulation demonstrates energy regeneration during braking, where the DC motor acts as a generator, sending energy back to the battery. The tutorial also shows how the system responds to speed changes, illustrating the increase in battery SOC and voltage due to regenerative braking.
Takeaways
- 🔋 The simulation model demonstrates the operation of a battery-driven electric vehicle using regenerative braking in MATLAB.
- ⚡ The setup consists of a battery, bi-directional DC-DC converter, and a DC motor, with speed control managed by a PID controller.
- 🚗 During motoring, the battery supplies power to the DC motor, but during braking, the energy is reversed and stored in the battery.
- 🔄 Regenerative braking converts the motor's negative torque into energy, which is then sent back to the battery, reversing the current flow.
- 📊 The system measures and tracks key metrics like battery voltage, current, state of charge (SOC), motor speed, and torque.
- 🏎 The initial speed is set at 120 radians per second, with a constant torque of 10 Newton meters during motoring operation.
- 🔧 In the simulation, the speed is reduced from 120 to 50 radians per second to simulate the regenerative braking process.
- 🔋 When braking is applied, the DC motor acts as a generator, and the current direction changes from positive to negative as energy flows back to the battery.
- 🔍 The simulation demonstrates how the SOC of the battery increases during regenerative braking, and the voltage also rises due to energy being transferred back to the battery.
- 🔔 The video concludes by explaining how regenerative braking helps improve the energy efficiency of electric vehicles and invites viewers to subscribe to the channel for more content.
Q & A
What components are included in the electric vehicle model discussed in the script?
-The model consists of a battery, bi-directional DC-DC converter, and a DC motor, with the battery controlled via a speed control method.
How does the regenerative braking system work in this model?
-During braking, the energy from the DC motor is reversed and stored in the battery through the bi-directional DC-DC converter. The current direction reverses when the speed is reduced.
What role does the PID controller play in the system?
-The PID controller compares the speed of the DC motor with a reference value and processes the signal to generate the appropriate pulse to control the MOSFET and motor operation.
What happens to the current during regenerative braking?
-During regenerative braking, the current direction reverses, and the motor generates power that is stored in the battery. This changes the current from a positive value to a negative one.
What changes occur in the battery's state of charge (SOC) during braking?
-The SOC of the battery increases during regenerative braking as energy is stored back into the battery.
How is the reference speed manipulated in the model?
-The reference speed is initially set to 120 radians per second. After a set time, it is reduced to 50 radians per second to simulate braking and observe the regenerative process.
What is the rated voltage and speed of the DC motor used in the simulation?
-The DC motor is rated at 240 volts with a rated speed of 10,750 RPM and 5 horsepower (HP).
How does the torque behave during the motoring and braking operations?
-During motoring, the torque is maintained at around 10-11 Nm. During braking, the torque switches to a negative value, indicating energy regeneration.
What happens to the battery voltage during regenerative braking?
-The battery voltage increases during regenerative braking as the motor returns energy to the battery.
What is the purpose of simulating the model at different speed conditions?
-Simulating at different speeds, especially with braking scenarios, helps demonstrate the concept of energy regeneration and how the system stores energy back into the battery.
Outlines
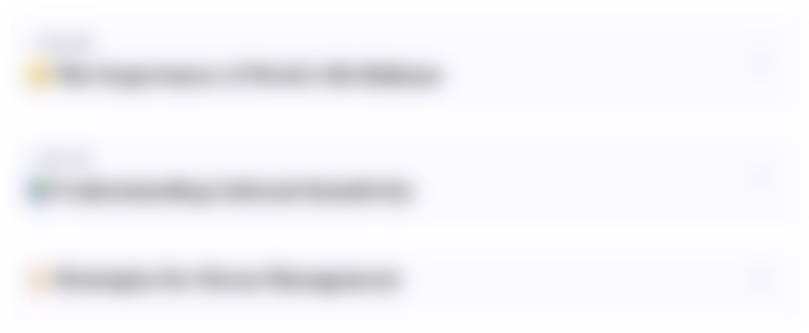
Этот раздел доступен только подписчикам платных тарифов. Пожалуйста, перейдите на платный тариф для доступа.
Перейти на платный тарифMindmap
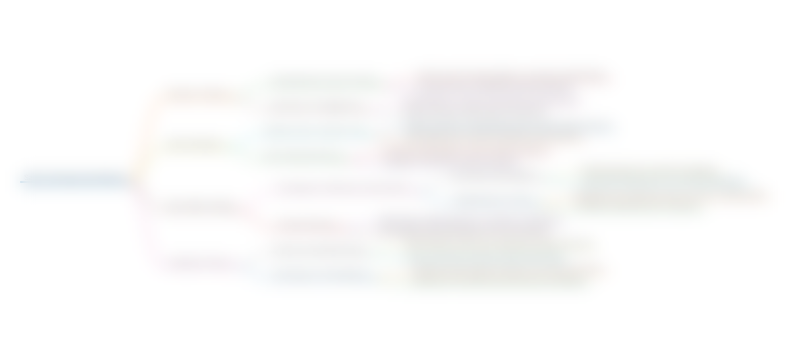
Этот раздел доступен только подписчикам платных тарифов. Пожалуйста, перейдите на платный тариф для доступа.
Перейти на платный тарифKeywords
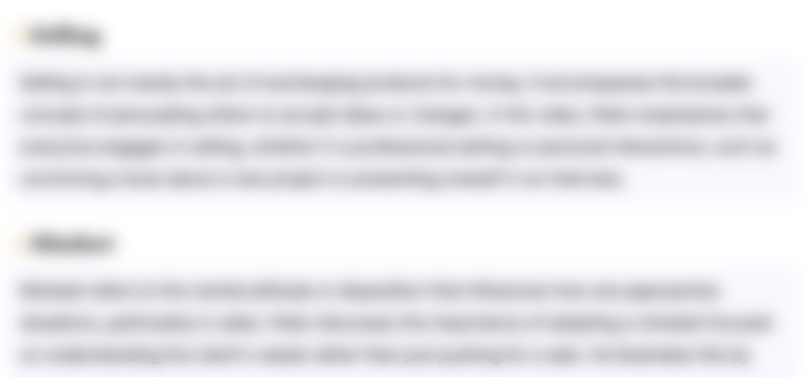
Этот раздел доступен только подписчикам платных тарифов. Пожалуйста, перейдите на платный тариф для доступа.
Перейти на платный тарифHighlights
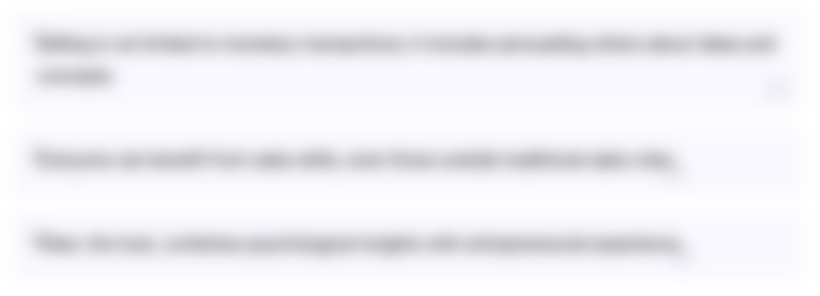
Этот раздел доступен только подписчикам платных тарифов. Пожалуйста, перейдите на платный тариф для доступа.
Перейти на платный тарифTranscripts
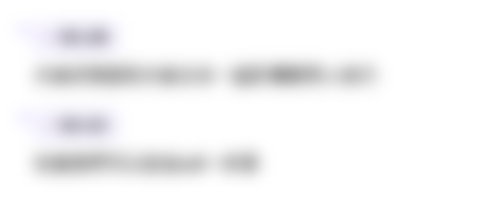
Этот раздел доступен только подписчикам платных тарифов. Пожалуйста, перейдите на платный тариф для доступа.
Перейти на платный тарифПосмотреть больше похожих видео
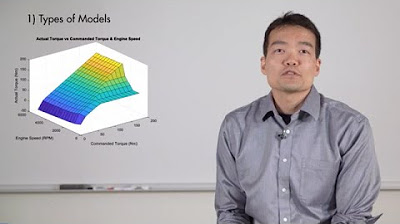
Developing HEV Control Systems
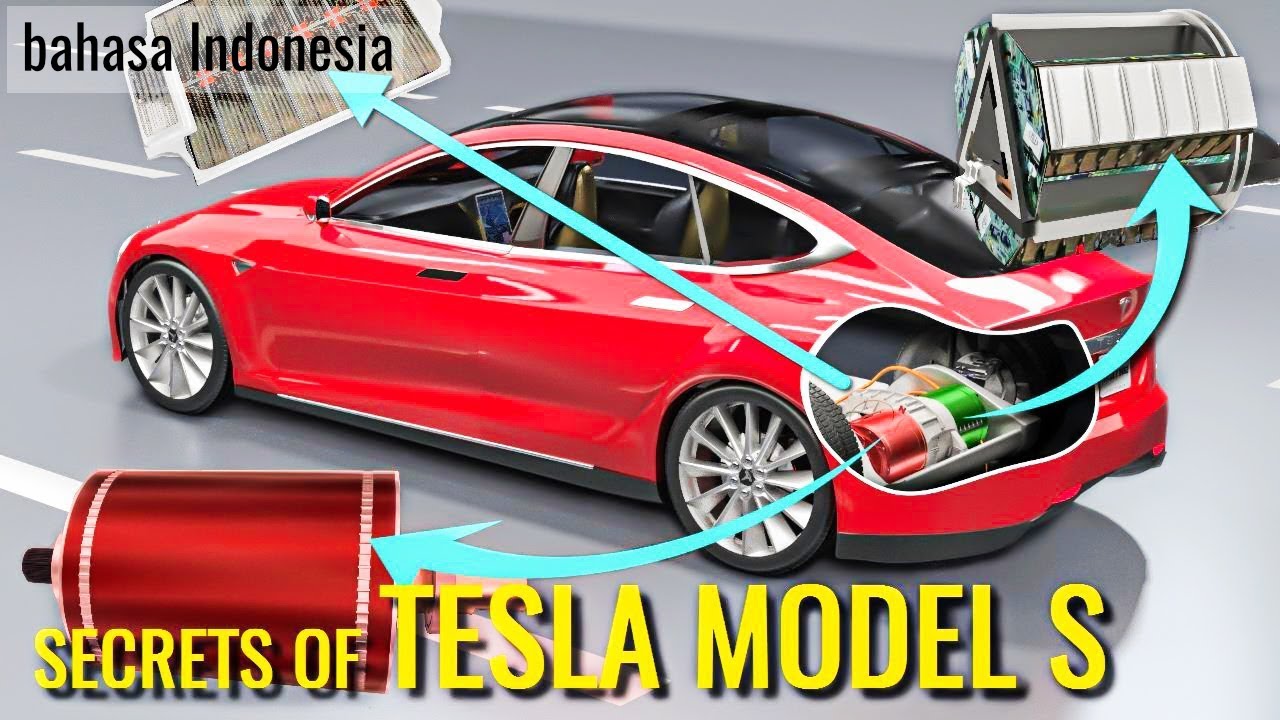
Bagaimana cara kerja mobil listrik?
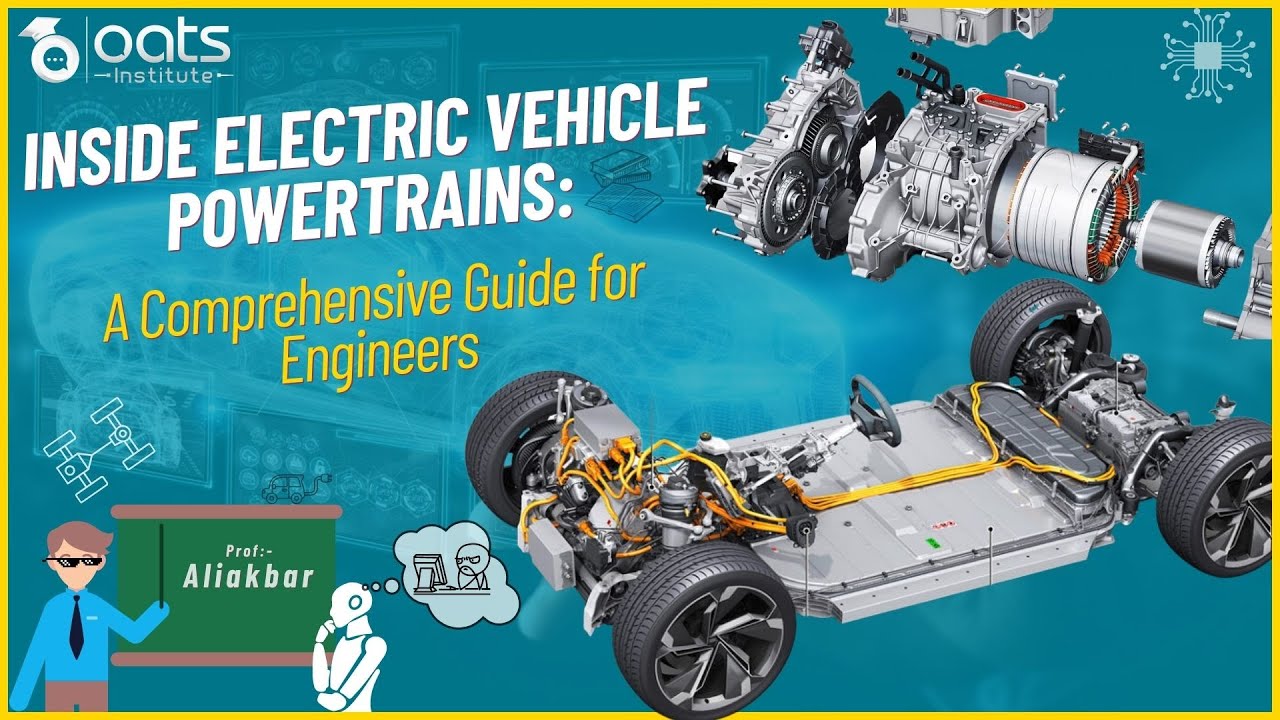
Inside Electric Vehicle Powertrains: A Comprehensive Guide for Engineers
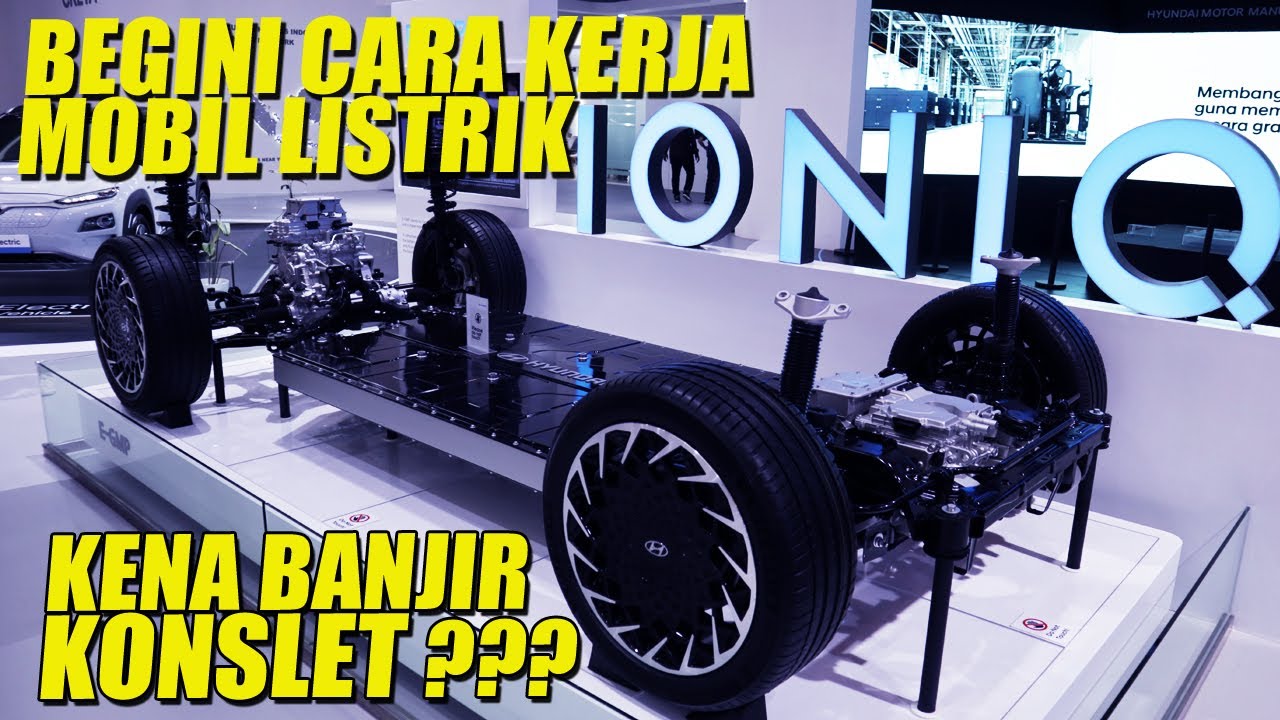
CARA KERJA MOBIL LISTRIK, BISA JADI POWER BANK, SEBERAPA AMAN LEWAT BANJIR ???

How does an Electric Car work ? | Tesla Model S
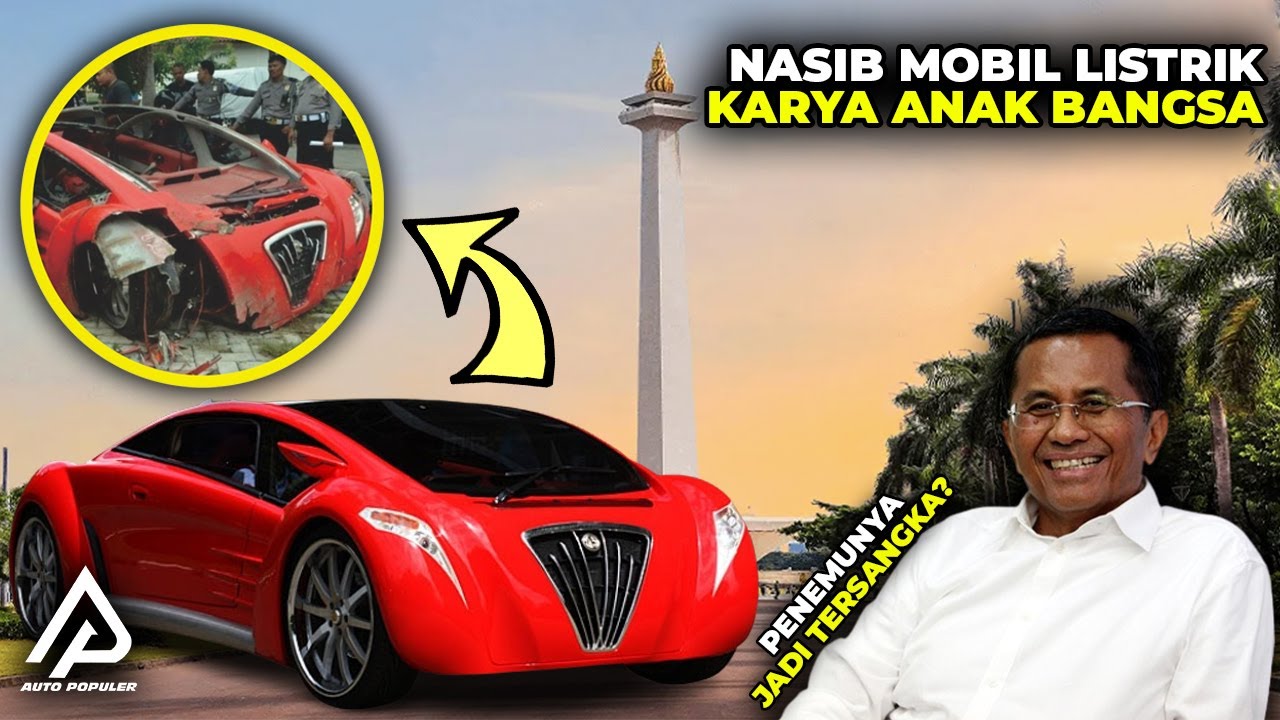
Tak Dihargai Di Negeri Sendiri Hingga Berakhir Jadi Besi Tua!? Nasib Mobil Listrik Produksi Lokal!
5.0 / 5 (0 votes)