PID Controller Explained
Summary
TLDRThis educational video by RealPars dives into the world of PID Controllers, explaining their evolution from single-station devices to their integral role in modern industrial processes. It contrasts PID with basic ON/OFF control, highlighting the importance of PID's Proportional, Integral, and Derivative settings in maintaining process stability. The video also covers the critical process of Controller Tuning, illustrating how PID parameters can be adjusted for optimal performance in various applications, and touches on auto-tuning capabilities in modern controllers.
Takeaways
- 🔧 The video is sponsored by RealPars, promoting PLC programmers' education.
- 📈 The script discusses the evolution of PID Controllers from single-station devices to their modern applications.
- 🔄 PID Controllers are preferred over ON/OFF Controllers in industrial processes due to their ability to reduce fluctuation around the setpoint.
- 🏠 The script uses home temperature control as an analogy to explain the concept of ON/OFF control.
- 📊 The video illustrates the ineffectiveness of ON/OFF control in maintaining a stable process variable, as seen in the temperature plot.
- 💧 An example of tank level control is provided to demonstrate the need for more refined control than ON/OFF.
- 🔄 PID stands for Proportional, Integral, and Derivative, which are the three components of a PID Controller that adjust process variables.
- 🔄 Each PID component (P, I, D) contributes uniquely to the controller output, allowing for precise process control.
- 🔧 The video explains the role of a PID Controller in a feedback control loop, emphasizing its ability to maintain process stability.
- 🛠️ Controller Tuning is highlighted as a critical activity, involving the adjustment of P, I, and D values to meet specific process needs.
- 🔧 The script mentions both manual and auto-tuning methods for optimizing PID Controller settings, with the latter being more practical in many cases.
Q & A
What is a PID Controller and why is it important in industrial processes?
-A PID Controller is a type of feedback controller that uses a combination of proportional, integral, and derivative actions to control a process variable. It is important in industrial processes because it can maintain a process variable close to a desired setpoint more effectively than simple ON/OFF controllers, which are not suitable for precise control.
What is the difference between ON/OFF Control and PID Control?
-ON/OFF Control, also known as Bang-Bang Control, only has two output states and switches abruptly between them, causing the controlled variable to oscillate around the setpoint. PID Control, on the other hand, can provide a continuous range of outputs, allowing for smoother and more precise control, reducing the oscillation around the setpoint.
Can you explain the role of the Proportional (P), Integral (I), and Derivative (D) components in a PID Controller?
-The Proportional component produces an output proportional to the current error, the Integral component produces an output proportional to the accumulated error over time, and the Derivative component produces an output proportional to the rate of change of the error. These components work together to adjust the process variable towards the setpoint.
What is the purpose of the thermostat in the home temperature control example?
-The thermostat in the home temperature control example acts as an ON/OFF controller. It measures the room temperature and turns the furnace ON or OFF to maintain the temperature close to the setpoint, illustrating a simple form of feedback control.
Why is ON/OFF control not suitable for industrial processes or motion control?
-ON/OFF control is not suitable for industrial processes or motion control because it can cause significant fluctuations around the setpoint, which is often unacceptable in these applications due to the need for precise control and minimal deviation from the desired values.
How does a PID Controller handle the issue of fluctuation around the setpoint seen in ON/OFF control?
-A PID Controller handles the issue of fluctuation by continuously adjusting the output signal based on the error signal, which is the difference between the process variable and the setpoint. This allows for finer control and reduces the oscillation around the setpoint.
What is Controller Tuning and why is it important?
-Controller Tuning is the process of adjusting the P, I, and D values of a PID Controller to achieve the desired response for a specific process. It is important because the correct settings can vastly differ between processes due to their unique characteristics and requirements.
How does a PID Controller fit into a feedback control loop?
-A PID Controller fits into a feedback control loop by comparing the process variable (PV) from a sensor with the setpoint. Based on this comparison, it produces an output signal that operates the final control element to adjust the process variable towards the setpoint.
What is the significance of the Error Signal in the context of a PID Controller?
-The Error Signal is the difference between the process variable and the setpoint. It is significant because it drives the PID Controller's calculation of the output signal, which in turn determines how the controller adjusts the process variable.
How do modern PID Controllers differ from the stand-alone devices used in the past?
-Modern PID Controllers are often integrated into PLCs (Programmable Logic Controllers) or DCS (Distributed Control Systems) and are created within the control logic using block commands. In contrast, stand-alone PID controllers were used to control one loop and required a control room with multiple devices mounted on panels.
What are some methods for tuning a PID Controller?
-There are manual methods for tuning a PID Controller that involve observing the process response to setpoint changes, such as increasing the setpoint change until the process reaches steady-state oscillation. Additionally, most modern controllers have Autotuning capability, where the controller learns the process response and suggests PID settings.
Outlines
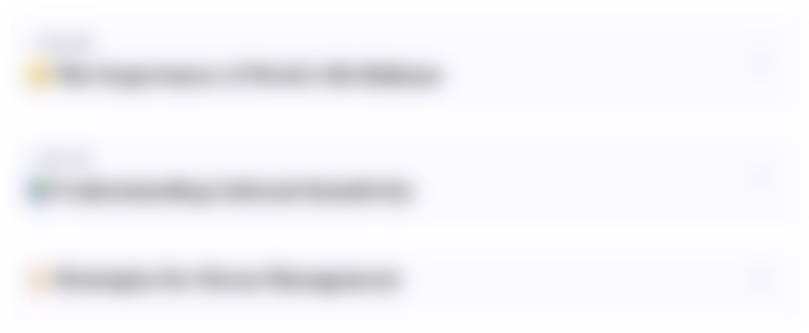
このセクションは有料ユーザー限定です。 アクセスするには、アップグレードをお願いします。
今すぐアップグレードMindmap
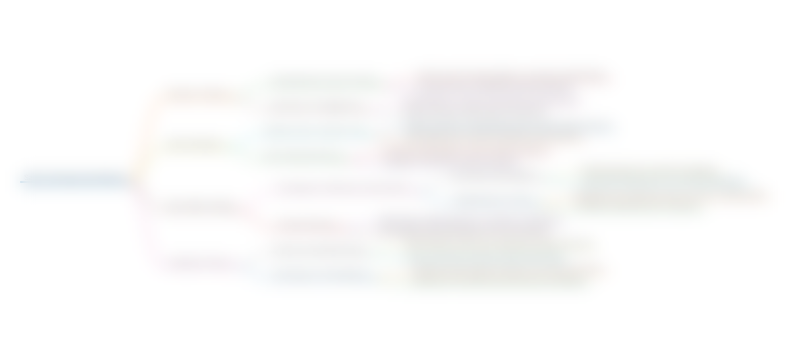
このセクションは有料ユーザー限定です。 アクセスするには、アップグレードをお願いします。
今すぐアップグレードKeywords
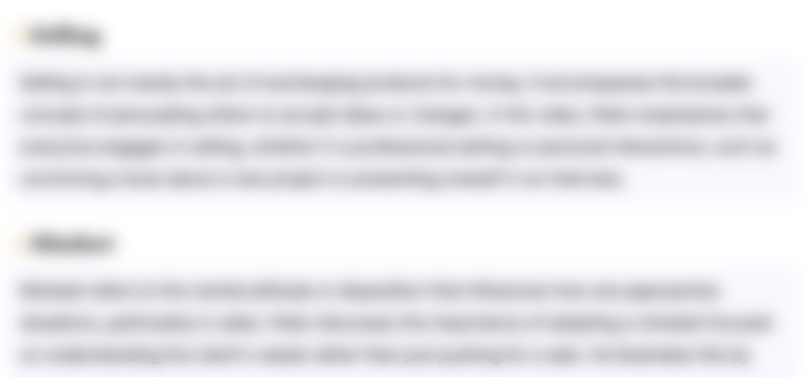
このセクションは有料ユーザー限定です。 アクセスするには、アップグレードをお願いします。
今すぐアップグレードHighlights
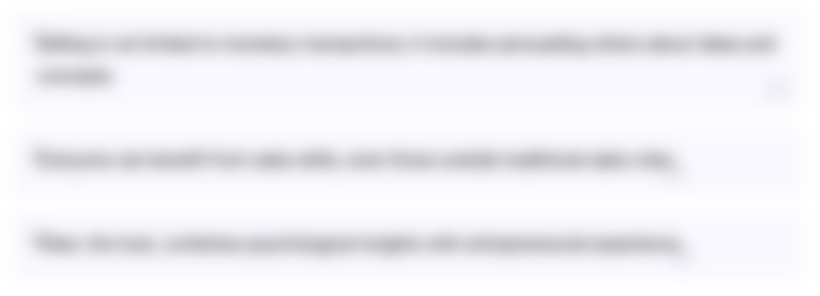
このセクションは有料ユーザー限定です。 アクセスするには、アップグレードをお願いします。
今すぐアップグレードTranscripts
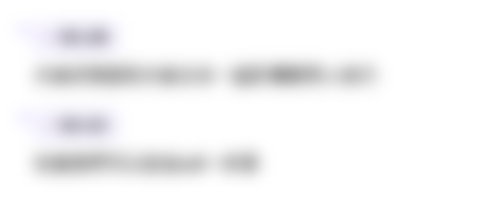
このセクションは有料ユーザー限定です。 アクセスするには、アップグレードをお願いします。
今すぐアップグレード5.0 / 5 (0 votes)