Value added analysis | Value added process vs Non value added | Value Added vs Non Value added Lean
Summary
TLDRThis video explains the importance of focusing on value-added activities in business, highlighting that only 5% of actions typically add value while 95% are non-value-added. It differentiates between essential and non-essential non-value-added activities and uses the 8 wastes of lean manufacturing (DOWNTIME) to illustrate examples, ultimately urging viewers to optimize their processes.
Takeaways
- 📈 Focus on adding value to activities or processes for a successful venture or business.
- 🔢 A staggering 95% of activities are non-value-added, with only 5% being value-added.
- 💡 Value can be defined as something the customer is willing to pay for.
- 📋 Activities can be categorized into value-added, non-value-added but essential, and non-value-added and non-essential.
- 🛑 Value-added activities increase the worth of the product or service from the customer's perspective.
- ⚠️ Non-value-added but essential activities include purchasing, HR, compliance, and R&D testing, which are necessary but don't add value to the product or service.
- 🚫 Non-value-added and non-essential activities can be immediately eliminated and include rework, delays, and unnecessary handling of materials.
- 📊 The 8 wastes of lean manufacturing, represented by the acronym DOWNTIME, are major areas of non-value-added activities.
- 🏦 An example of analyzing a process is given with John's visit to the bank, where most of the time spent is on non-value-added activities.
- ⏱️ The time spent on value-added activities is minimal compared to non-value-added activities in most processes.
- 🔑 The key takeaway is to identify and focus on reducing non-value-added activities to improve efficiency and customer value.
Q & A
What is the primary focus for running a successful venture or business according to the video?
-The primary focus is to add value to all activities or processes, with only about 5% of activities being value-added.
How can value be defined in the context of business activities?
-Value can be defined as something that the customer is willing to pay for.
What are the three categories of activities mentioned in the video?
-The three categories are value-added activities, non-value-added but essential activities, and non-value-added and non-essential activities.
What are value-added activities in the context of business operations?
-Value-added activities are those that increase the worth of the product or service from the customer's perspective.
What are non-value-added but essential activities and why are they necessary?
-Non-value-added but essential activities are those that do not add value to the product or service and customers are not willing to pay for them, but they are necessary due to business requirements or legal regulations.
What are non-value-added and non-essential activities and why should they be eliminated?
-Non-value-added and non-essential activities do not add any value to the product or service and are not required by business operations. They should be eliminated to improve efficiency.
What is the significance of the 95% non-value-added activities in business operations?
-The significance is that most of the activities (95%) do not add value and customers are only willing to pay for the 5% that do add value, indicating a need for efficiency improvement.
What is the acronym DOWNTIME and how does it relate to non-value-added activities?
-DOWNTIME stands for Defects, Overproduction, Waiting, Non-utilized Talent, Transportation, Inventory, Motion, and Excess production. It represents the biggest area of non-value-added activities in lean manufacturing.
How does the video use the example of John visiting a bank to illustrate value-added and non-value-added activities?
-The example shows that most of John's time (95 minutes) is spent on non-value-added activities like driving, waiting in a queue, and filling forms, while only 5 minutes are spent on the value-added activity of completing the cash transaction.
What is the implication of the video's message for business management?
-The implication is that businesses should focus on identifying and reducing non-value-added activities to increase efficiency and customer value.
What steps can be taken to improve the value-added nature of business activities?
-Businesses can analyze their processes to identify and eliminate non-value-added activities, focus on activities that customers are willing to pay for, and optimize essential but non-value-added activities to reduce their impact on overall operations.
Outlines
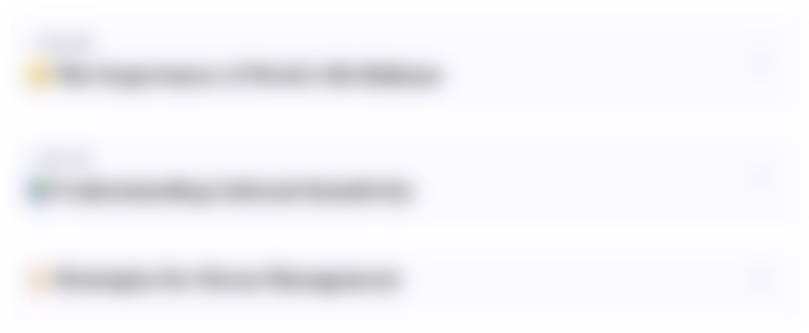
このセクションは有料ユーザー限定です。 アクセスするには、アップグレードをお願いします。
今すぐアップグレードMindmap
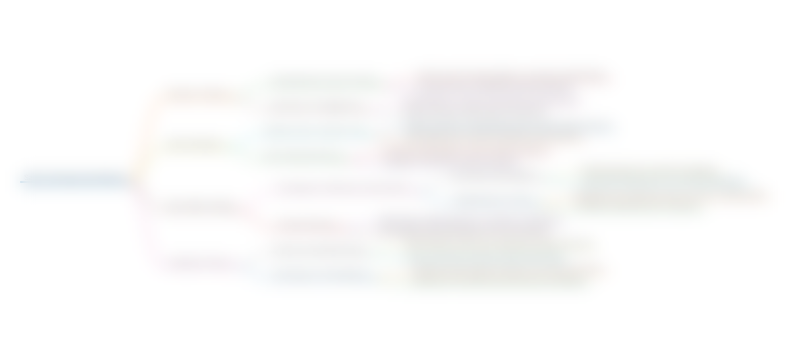
このセクションは有料ユーザー限定です。 アクセスするには、アップグレードをお願いします。
今すぐアップグレードKeywords
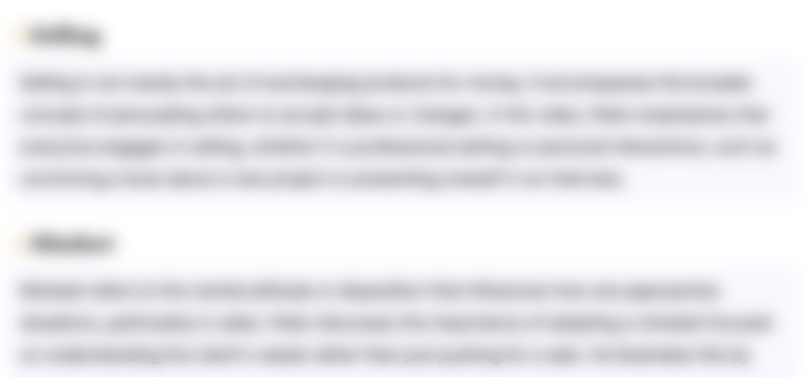
このセクションは有料ユーザー限定です。 アクセスするには、アップグレードをお願いします。
今すぐアップグレードHighlights
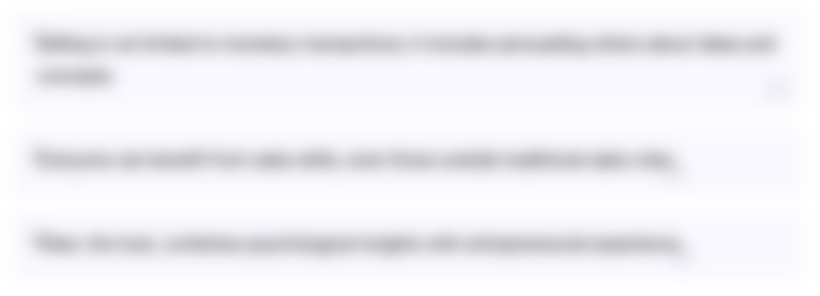
このセクションは有料ユーザー限定です。 アクセスするには、アップグレードをお願いします。
今すぐアップグレードTranscripts
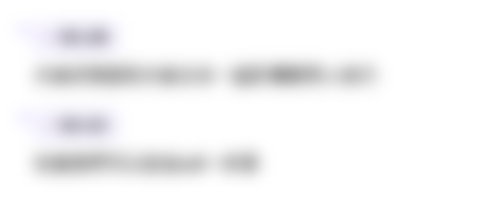
このセクションは有料ユーザー限定です。 アクセスするには、アップグレードをお願いします。
今すぐアップグレード5.0 / 5 (0 votes)