Telecurso 2000 Manutenção 01 Introdução a manutenção
Summary
TLDRThis Teleclass module introduces the essential role of maintenance in modern industrial production. It explores the evolution of maintenance through history, from its origins in the 15th century to its critical role during World War II and in post-war industrial advancements. The video explains different types of maintenance such as routine, preventive, corrective, and predictive maintenance, highlighting their importance for operational efficiency, cost control, and customer satisfaction. It also covers the concept of Total Preventive Maintenance (TPM) and encourages active participation in exercises to deepen understanding of the topic.
Takeaways
- 😀 Maintenance is a crucial part of production that ensures machines and equipment run smoothly, supporting overall product quality and efficiency.
- 😀 The concept of maintenance has evolved significantly throughout history, with roots tracing back to the 15th century and becoming vital during the Industrial Revolution and World War II.
- 😀 Globalization has heightened the importance of maintenance, as it ensures minimal defects, on-time production, and cost-effective operations in a competitive global market.
- 😀 The main objective of maintenance is to ensure that a company can meet its goals, such as producing high-quality products on time and within budget.
- 😀 The modern definition of maintenance includes regular technical care to keep machines, equipment, and facilities in good working order, focusing on conservation, adequacy, restoration, replacement, and prevention.
- 😀 Routine maintenance involves regular inspections and upkeep to prevent machine failure and ensure smooth operation, while periodic services follow scheduled plans for specific maintenance tasks.
- 😀 The ideal maintenance approach keeps everything functioning continuously without compromising on production goals, but it must also remain cost-effective to avoid affecting the final product's price and competitiveness.
- 😀 Both machine operators and specialized maintenance personnel share responsibility for maintenance tasks to avoid production stoppages and ensure continued operations.
- 😀 Corrective maintenance is required when unplanned issues, such as broken belts or equipment malfunctions, occur unexpectedly during production.
- 😀 Planned maintenance includes categories like preventive maintenance, predictive maintenance, and TPM (Total Preventive Maintenance), each focusing on preventing issues before they happen and maintaining equipment in optimal condition.
- 😀 Predictive maintenance uses data like vibration analysis to monitor equipment wear and detect potential problems before they affect production.
- 😀 Total Preventive Maintenance (TPM), a Japanese approach, empowers operators to take ownership of their machines and maintain them proactively, improving overall equipment efficiency.
Q & A
What is the main objective of maintenance in modern production?
-The main objective of maintenance is to ensure that machines and equipment operate smoothly, minimizing disruptions and enabling companies to meet production targets, reduce costs, and satisfy customers in a globalized economy.
How did the concept of maintenance evolve historically?
-The concept of maintenance began in the 15th century with mechanical machines, evolving significantly during the Industrial Revolution. Maintenance became essential during World War II for military machinery, and post-war reconstruction in countries like Japan and Germany further emphasized its importance for industrial advancement.
What are the key components of maintenance in modern production?
-Modern maintenance involves conservation, adequacy, restoration, replacement, and prevention to keep machines, equipment, and facilities in full working order, preventing failures and poor production performance.
What is the difference between routine maintenance and periodic services?
-Routine maintenance is done regularly, often daily, to ensure machines remain operational, while periodic services follow a scheduled plan to inspect and maintain machinery at predetermined intervals.
How does preventive maintenance contribute to production efficiency?
-Preventive maintenance involves taking proactive measures to keep machines running smoothly, reducing the likelihood of unexpected breakdowns and helping to maintain production schedules without costly disruptions.
What is corrective maintenance and when is it necessary?
-Corrective maintenance is unplanned and occurs when machines break down unexpectedly, requiring immediate repair to restore functionality and minimize downtime.
What is predictive maintenance, and how does it differ from preventive maintenance?
-Predictive maintenance is based on monitoring a machine's condition, using data such as vibrations and noise, to predict potential issues before they occur. Unlike preventive maintenance, which is scheduled, predictive maintenance relies on analyzing equipment's current state to anticipate problems.
What is TPM (Total Preventive Maintenance), and why is it significant?
-TPM is a Japanese maintenance model that emphasizes the idea that operators should be responsible for maintaining their machines. It promotes a proactive approach to maintenance, ensuring that equipment is always in optimal condition to prevent breakdowns and improve efficiency.
How does maintenance affect the competitiveness of a product?
-Efficient maintenance helps keep production running smoothly, minimizing downtime and defects, which in turn ensures products are produced at a competitive price. If maintenance costs are too high, it can negatively impact the final product's price and competitiveness.
What role do machine operators play in the maintenance process?
-Machine operators are responsible for performing routine maintenance tasks, such as regular inspections and basic upkeep, to ensure that machines continue functioning properly and avoid costly breakdowns. They are integral to maintaining production efficiency.
Outlines
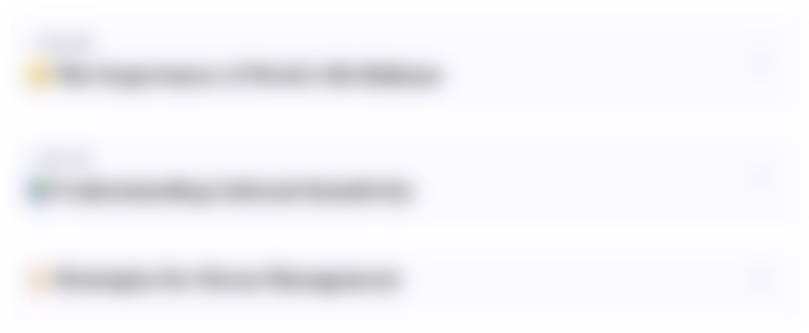
このセクションは有料ユーザー限定です。 アクセスするには、アップグレードをお願いします。
今すぐアップグレードMindmap
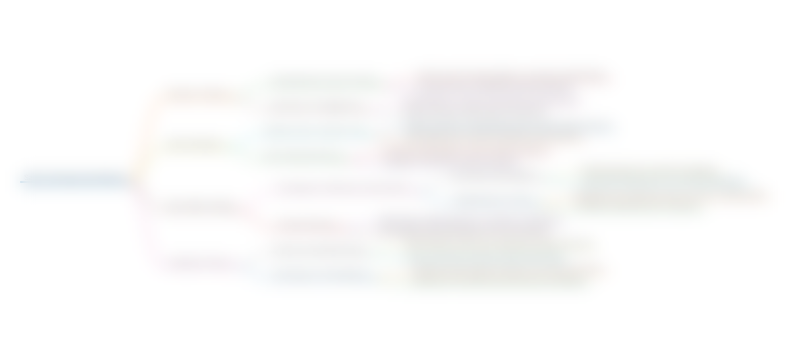
このセクションは有料ユーザー限定です。 アクセスするには、アップグレードをお願いします。
今すぐアップグレードKeywords
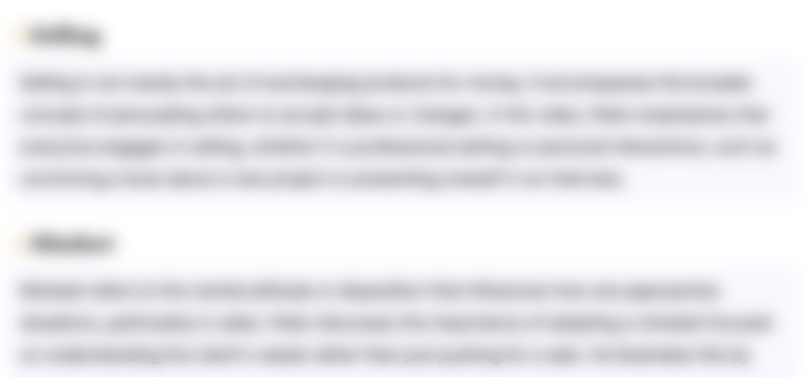
このセクションは有料ユーザー限定です。 アクセスするには、アップグレードをお願いします。
今すぐアップグレードHighlights
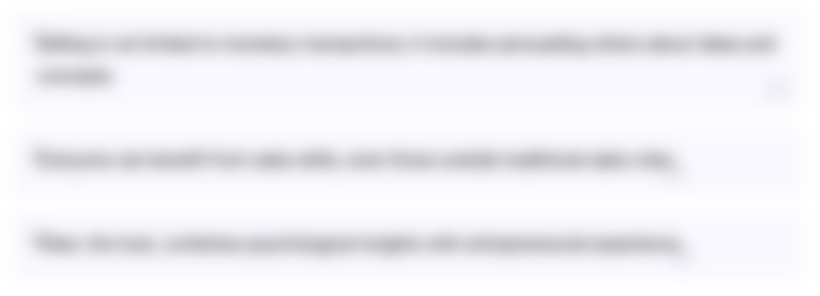
このセクションは有料ユーザー限定です。 アクセスするには、アップグレードをお願いします。
今すぐアップグレードTranscripts
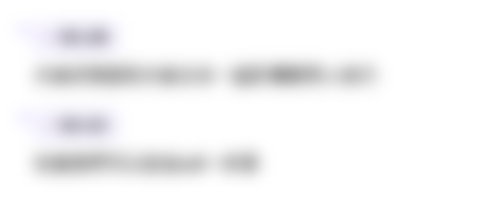
このセクションは有料ユーザー限定です。 アクセスするには、アップグレードをお願いします。
今すぐアップグレード関連動画をさらに表示
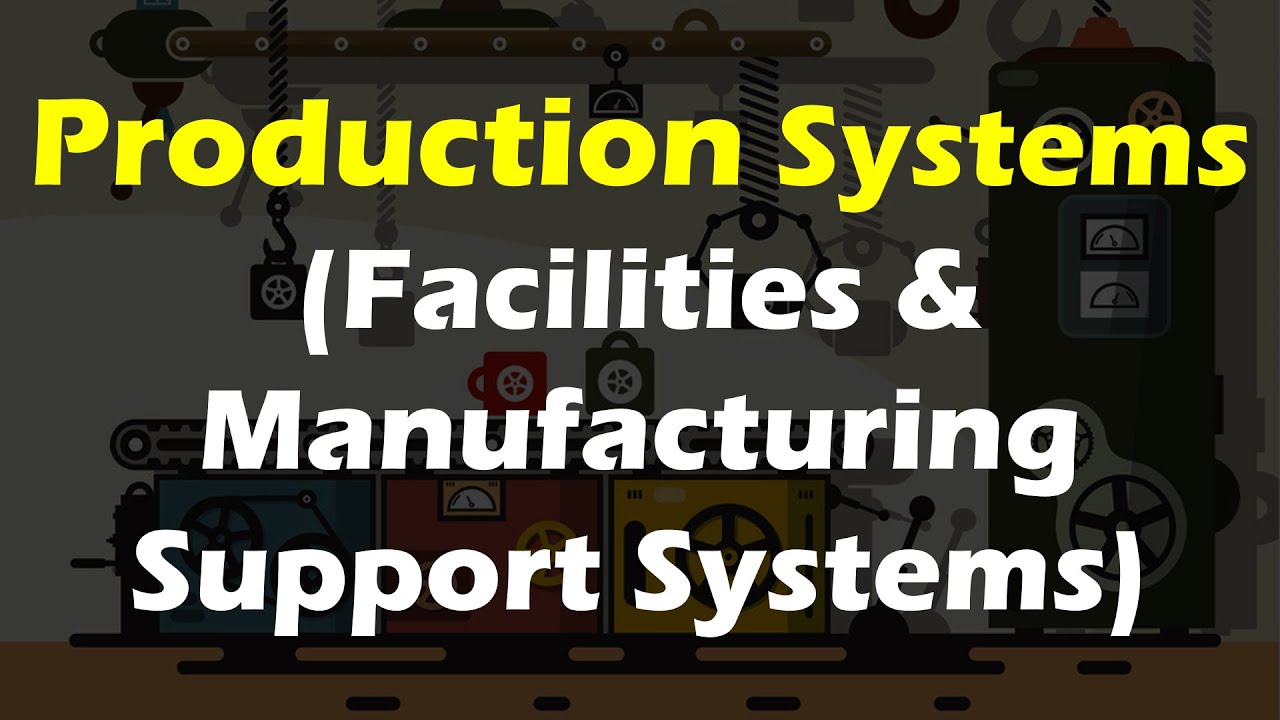
Production Systems - Facilities & Manufacturing Support Systems
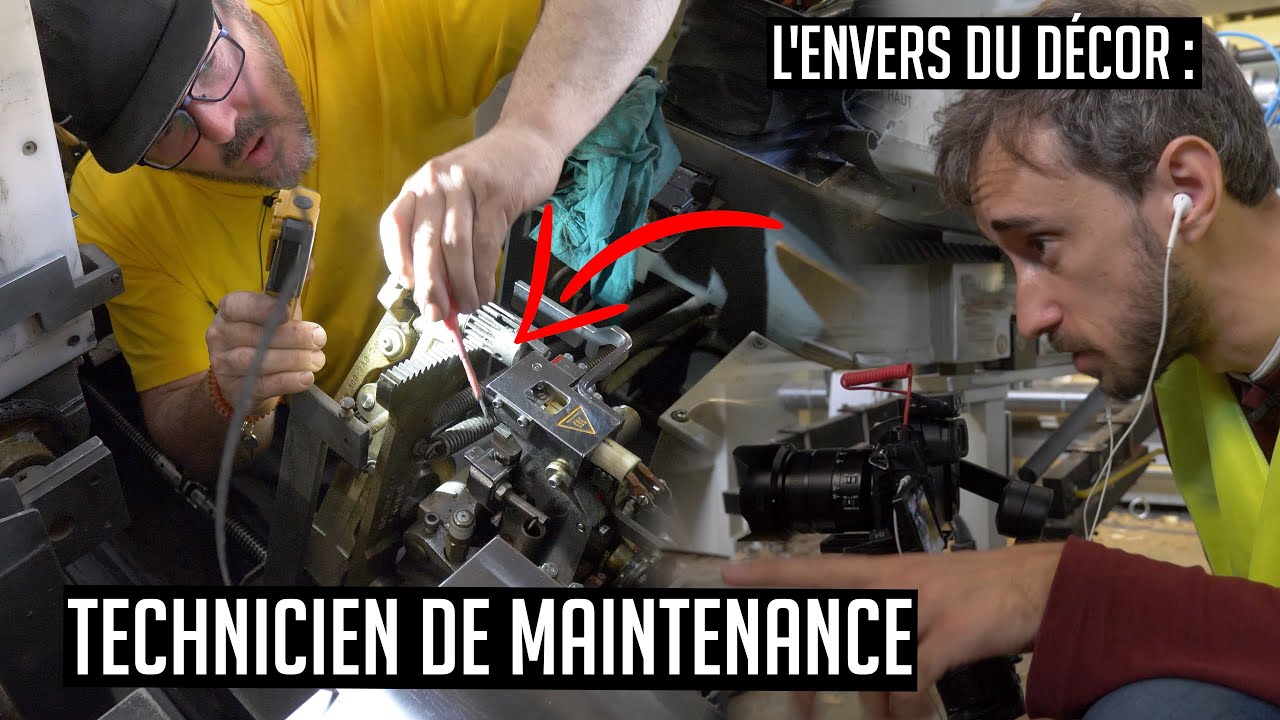
Une journée avec #37 : un technicien de maintenance (découverte métier)
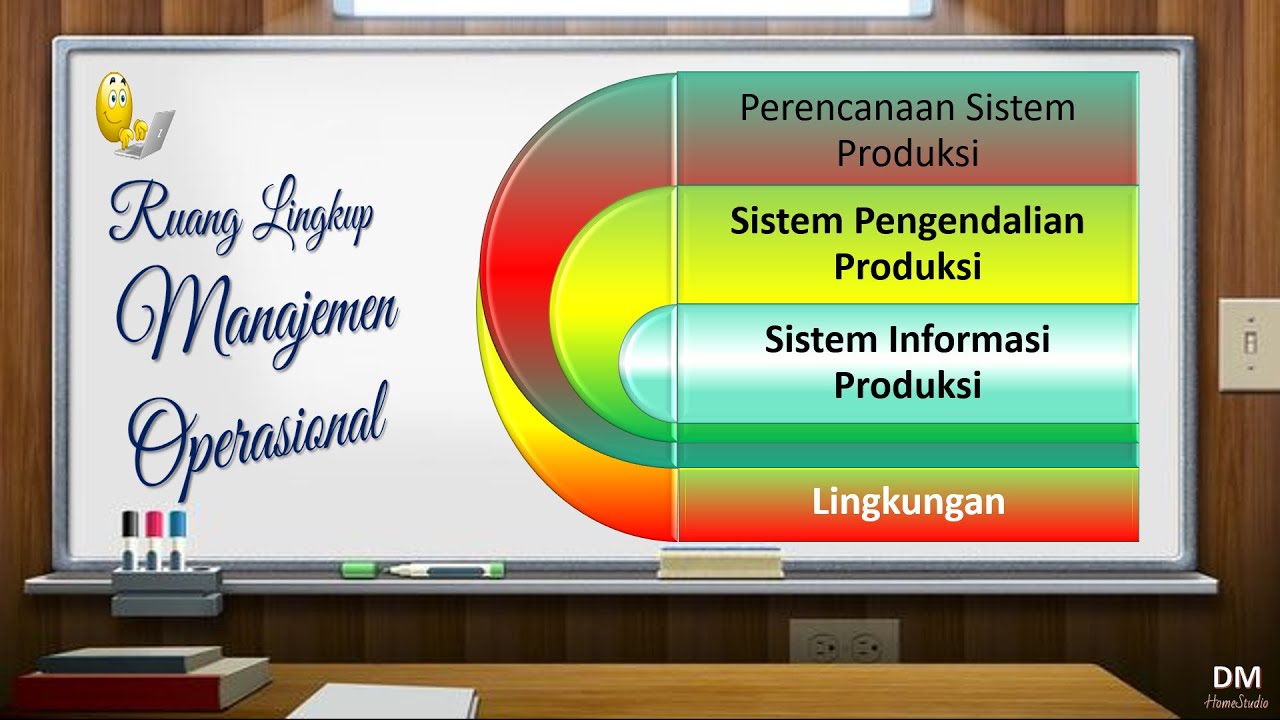
Pengantar Manajemen Operasional
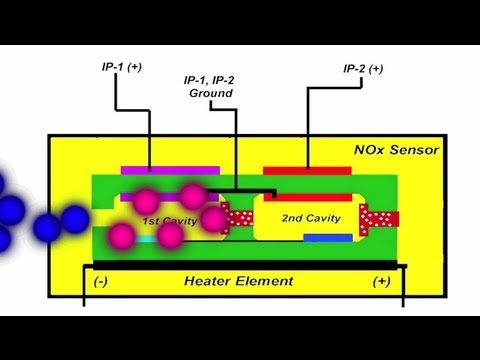
GDI NOx Sensor Operation
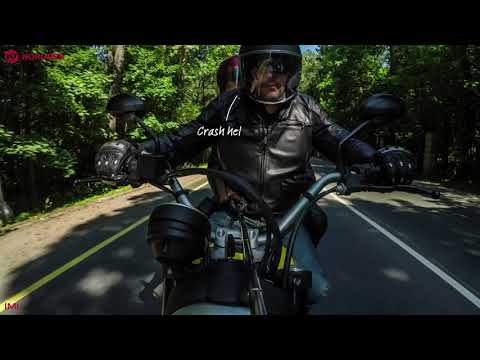
Training Module 2 AIR PREPARATION (FULL)

Digital Transformation OEM Summit 2023 - Athena iServ Keynote Presentation
5.0 / 5 (0 votes)