America Needs 3 Million Homes. Can 3D Printers Help? | Big Business | Business Insider
Summary
TLDRThe video explores 3D-printed homes as a potential solution to the housing shortage, highlighting the technology's ability to reduce construction time and costs. Companies like SQ4D and Icon are leading the charge, with SQ4D's first 3D-printed home in Long Island and Icon's ambitious project of 100 homes in Texas. Despite the promise, challenges remain, including scaling production, material consistency, and public acceptance. The technology offers a more resilient and potentially cost-effective alternative to traditional wood construction, but requires further development and standardization to become mainstream.
Takeaways
- 🏠 3D printing technology is being invested in heavily to address the housing shortage, with the potential to construct homes faster and more cost-effectively.
- 📈 The number of 3D printed homes remains low in comparison to traditional construction, with less than 100 built in the US last year out of 1.5 million total homes.
- 🛠️ Daily challenges are faced in the 3D printing process, indicating that the technology is not yet perfected and requires ongoing adjustments and problem-solving.
- 💰 3D printed homes can be more cost-effective, requiring fewer workers and eliminating the need for separate crews for different construction stages.
- ⏱️ The construction time for 3D printed homes is significantly reduced, with the potential to complete a house in 16 days versus the traditional method which takes months.
- 🔄 The material mix for 3D printing is sensitive to environmental conditions, requiring adjustments based on temperature and humidity to prevent issues like cracking.
- 🛡️ 3D printed homes can offer benefits such as reduced waste and increased resistance to common housing issues like fires, weather damage, mold, and termites.
- 📊 The cost of building a 3D printed home is estimated to be about 30% cheaper than traditional stick-built homes, providing a financial incentive for adoption.
- 🏗️ Scaling up 3D printed home production is challenging due to strict building regulations and the lack of widespread standards for 3D-printed structures.
- 📚 The history and performance of 3D printed homes over time are still being studied, as the material and construction methods are relatively new to the industry.
- 🌐 Public perception and acceptance of 3D printed homes are gradually improving, with early adopters viewing them as a form of living art and a conversation starter.
Q & A
What is the primary purpose of using 3D printing technology in home construction?
-The primary purpose of using 3D printing technology in home construction is to help solve the housing shortage and potentially cut building time in half.
How many houses were built using 3D printing technology in the US last year, according to the script?
-Fewer than 100 houses were built using 3D printing technology in the US last year, out of 1.5 million total homes.
What is the estimated cost saving of building a 3D printed home compared to a traditionally built home of the same size?
-SQ4D claims that a 3D printed home is about 30% cheaper than a stick-built home of similar size.
What is the role of Kristen Henry in the context of the script?
-Kristen Henry is the chief technology officer at SQ4D, a company that built the first 3D home listed for sale in the US.
How does the 3D printing process for home construction impact the number of workers needed on-site?
-Most of the job in 3D printing a home can be done by just three people: one operating the printer, another controlling the mix, and a third monitoring the site as a chief safety officer.
What are some of the challenges faced in the 3D printing construction process?
-Challenges include the need for daily adjustments to the concrete mix based on temperature, winds, and humidity, and the lack of widespread building code standards for 3D-printed structures.
How does the 3D printed home construction process compare to traditional methods in terms of speed?
-If everything goes right, most of the house structure can be done in just 16 days using 3D printing, which is three times faster than traditional lumber and drywall construction.
What is the estimated cost to build a 1,400-square-foot 3D printed home as mentioned in the script?
-The total cost to build a 1,400-square-foot 3D printed home was about $132,000.
What is the current status of 3D printed homes in terms of adoption and public perception?
-While there is excitement and interest in 3D printed homes, the adoption rate is still low, and public perception is mixed, with some skepticism due to the novelty of the technology.
What are some of the factors that could potentially slow down the scaling up of 3D printed home production?
-Factors include strict building regulations, the need for specialized concrete mixes that can be expensive and hard to come by, and the difficulty in finding trained personnel for 3D printing construction.
What is the significance of Icon's project in Georgetown, Texas, in the context of 3D printed homes in the US?
-Icon's project in Georgetown is significant as it represents the US's biggest neighborhood of 3D homes, with the company aiming to print 100 houses, demonstrating the potential for scalability and cost-effectiveness of 3D printed home construction.
Outlines
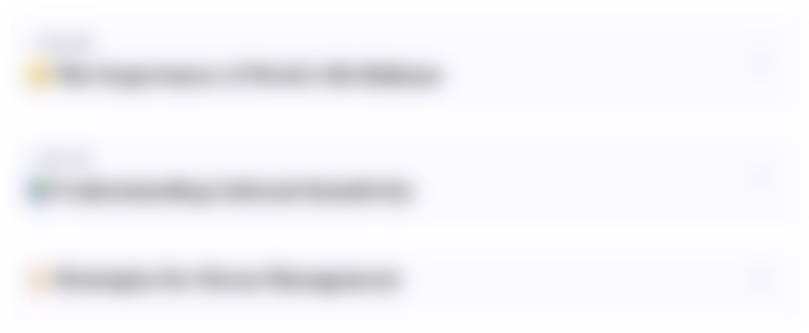
このセクションは有料ユーザー限定です。 アクセスするには、アップグレードをお願いします。
今すぐアップグレードMindmap
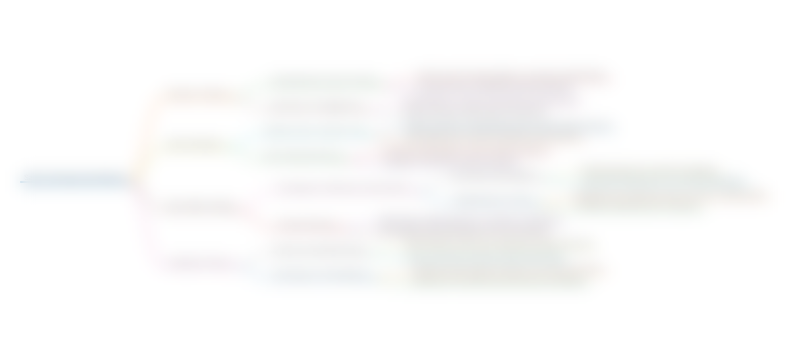
このセクションは有料ユーザー限定です。 アクセスするには、アップグレードをお願いします。
今すぐアップグレードKeywords
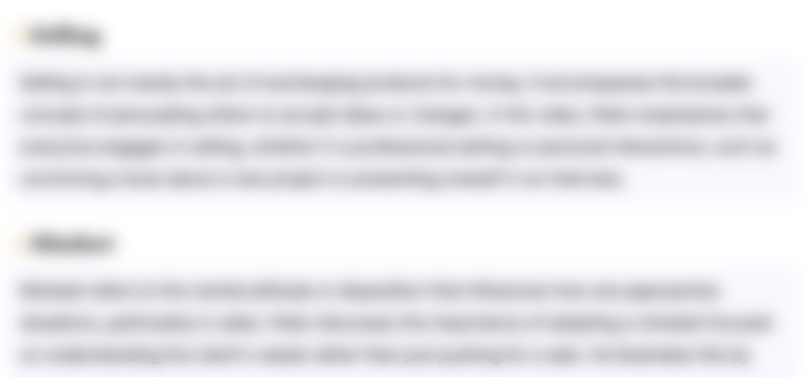
このセクションは有料ユーザー限定です。 アクセスするには、アップグレードをお願いします。
今すぐアップグレードHighlights
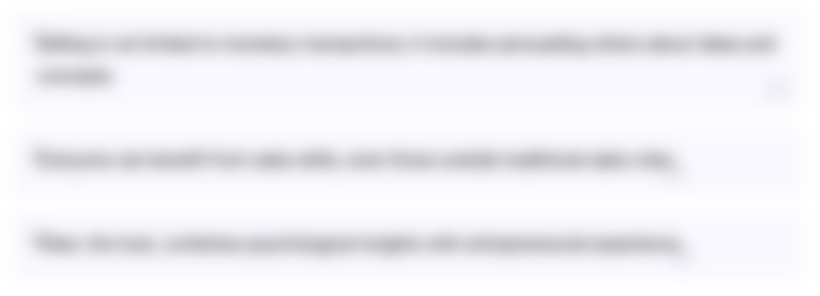
このセクションは有料ユーザー限定です。 アクセスするには、アップグレードをお願いします。
今すぐアップグレードTranscripts
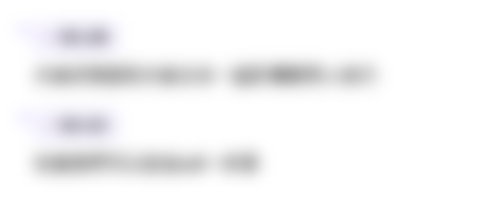
このセクションは有料ユーザー限定です。 アクセスするには、アップグレードをお願いします。
今すぐアップグレード関連動画をさらに表示
5.0 / 5 (0 votes)