Weld Meta l- Chemical reaction
Summary
TLDRThis video script explores the intricacies of welding metallurgy, focusing on chemical reactions, the role of oxygen, and methods for protecting molten metal from atmospheric contamination. The content delves into the mechanisms used to shield the weld from oxygen, such as the use of flux and gases like carbon dioxide. It also explains the importance of controlling oxygen levels to prevent issues like porosity, and highlights the influence of various elements like silicon, manganese, and sulfur on the quality of the weld. Additionally, the script touches on the impact of solidification and impurities on the weld's toughness and crack formation.
Takeaways
- 😀 Shielding gases like CO2 and flux are used to protect the molten weld pool from atmospheric contamination, preventing oxidation.
- 😀 Oxygen plays a significant role in the chemical reactions during welding, and its entry into the weld pool can cause defects like porosity.
- 😀 Deoxidizers such as silicon, manganese, and aluminum are added to the weld metal to react with oxygen and form non-metallic inclusions, removing oxygen and preventing oxidation.
- 😀 Faster welding speeds can cause elongated crystals to form in the weld, which may lead to defects like cracks.
- 😀 High cooling rates in welding can cause the formation of cracks in the centerline of the weld due to trapped molten metal.
- 😀 Impurities like sulfur can lower the melting temperature of the weld metal, making it more susceptible to cracking during solidification.
- 😀 The presence of nickel in the weld metal increases the risk of sulfur-induced cracking, especially if the sulfur content is high.
- 😀 Proper care and attention to welding techniques are necessary to avoid contamination by impurities like sulfur, ensuring weld quality.
- 😀 The selection of flux types and welding parameters is crucial for controlling oxidation and ensuring the desired properties in the weld.
- 😀 Understanding the impact of elements like sulfur, nickel, and oxygen on the weld is important to prevent defects and achieve strong, reliable joints.
- 😀 Welders should consider the weld speed and solidification conditions, as these factors influence the formation of defects like cracks and porosity in the final weld.
Q & A
What is the role of shielding gases in welding?
-Shielding gases are used to protect the molten weld pool from contamination by atmospheric oxygen, preventing oxidation and improving weld quality.
How does the slag function in welding?
-The slag forms a protective layer over the molten weld pool, preventing oxygen from contaminating the weld metal while it cools and solidifies.
Why is controlling oxygen content crucial in welding?
-High oxygen content in the weld metal can lead to porosity, reduced toughness, and other defects. Therefore, controlling oxygen levels is essential to ensure a high-quality weld.
What is the effect of excess oxygen on the weld metal?
-Excess oxygen can cause the formation of oxides in the weld, which can lead to porosity and a decrease in the mechanical properties, such as toughness and strength.
What are deoxidizers, and how do they work in welding?
-Deoxidizers are elements, such as silicon, manganese, or aluminum, added to the weld pool to bind with oxygen, forming non-metallic inclusions that prevent oxidation.
How do basic fluxes help in controlling oxygen content?
-Basic fluxes have a potential to transfer oxygen from the molten weld metal to form non-metallic inclusions, thus lowering the oxygen content in the weld metal.
What problems can arise from high oxygen levels in the weld?
-High oxygen levels in the weld metal can lead to porosity, reduced toughness, and an increased risk of crack formation in the solidified weld.
How does the welding speed affect crystal growth in the weld?
-The welding speed influences the direction and structure of crystal growth in the weld metal. Faster speeds lead to elongated crystals, while slower speeds may result in more uniform, finer crystal structures.
What are the risks of impurities such as sulfur in the weld metal?
-Impurities like sulfur can lower the melting temperature of the weld metal, making it prone to cracking, particularly if the sulfur content is high.
What is the relationship between welding speed and the likelihood of cracking in the weld?
-Higher welding speeds can increase the chances of cracking, particularly along the centerline of the weld, due to the rapid solidification and shrinkage of the molten metal.
Outlines
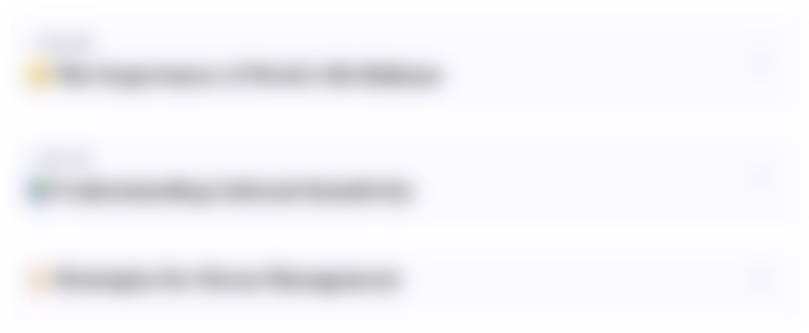
このセクションは有料ユーザー限定です。 アクセスするには、アップグレードをお願いします。
今すぐアップグレードMindmap
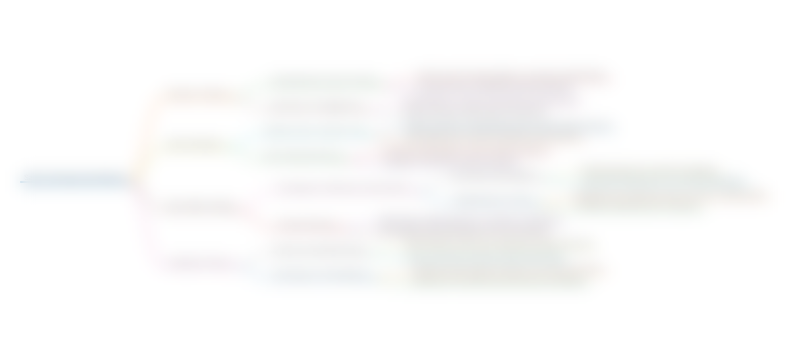
このセクションは有料ユーザー限定です。 アクセスするには、アップグレードをお願いします。
今すぐアップグレードKeywords
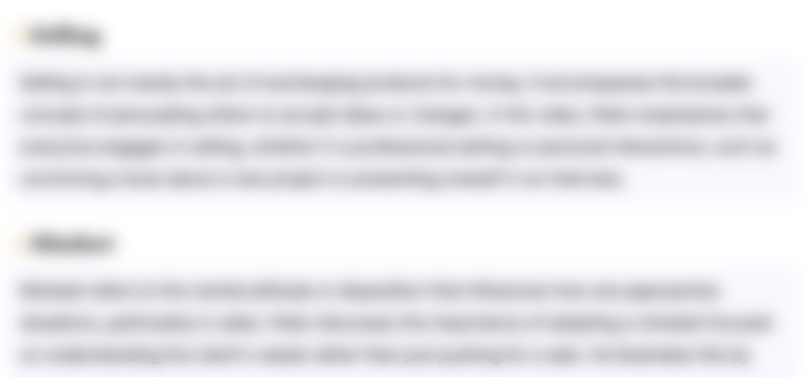
このセクションは有料ユーザー限定です。 アクセスするには、アップグレードをお願いします。
今すぐアップグレードHighlights
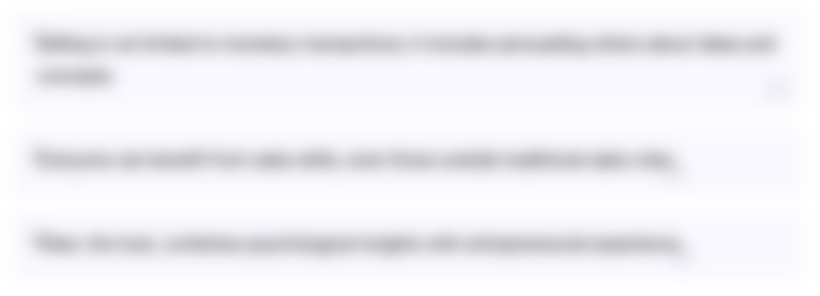
このセクションは有料ユーザー限定です。 アクセスするには、アップグレードをお願いします。
今すぐアップグレードTranscripts
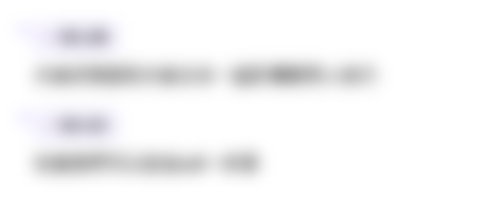
このセクションは有料ユーザー限定です。 アクセスするには、アップグレードをお願いします。
今すぐアップグレード5.0 / 5 (0 votes)