Forming Processes- Sheet Metal Stamping Dies and Processes
Summary
TLDRThe video script covers the essential aspects of sheet metal forming, emphasizing the importance of formability in manufacturing. It details various operations, such as cutting, bending, and drawing, and highlights key factors that influence formability, including ductility, die design, and press speed. The script explains common die operations like shearing, blanking, hole punching, and trimming, and explores different forming processes, such as drawing, bending, and hemming. It also discusses techniques to prevent defects like buckling and wrinkling during forming, ensuring high-quality production of metal parts, including automotive and aerospace components.
Takeaways
- 😀 Formability is crucial for sheet metal applications, allowing the material to deform into complex shapes without defects.
- 😀 Deformation types involved in sheet metal forming include bending, stretching, and drawing, with part shape playing a key role in determining formability.
- 😀 Other factors influencing formability include metal ductility, die design, stamping press type, press speed, lubrication, and feeding mechanisms.
- 😀 The two main types of dies in sheet metal operations are cutting dies and forming dies.
- 😀 Cutting processes include shearing, blanking, hole punching, and trimming, with shearing being the most common operation.
- 😀 Blanking involves cutting a complete perimeter around a shape to form a workpiece blank, with subsequent operations often needed.
- 😀 Punching cuts a slug from sheet metal stock to create holes, requiring proper clearance between the punch and die to avoid material damage.
- 😀 The die-cut edge of the sheet metal has both burnished and rough areas, with the quality of the cut varying based on material hardness.
- 😀 Forming operations like drawing, bending, and flanging change the shape of sheet metal, and require careful control of forces to avoid defects like buckling or thinning.
- 😀 The blank holder in drawing operations controls metal flow, preventing wrinkling while allowing enough metal to flow into the die cavity.
- 😀 Bending, flanging, and hemming are all used to shape metal parts, adding rigidity, providing fastening surfaces, and joining sheet metal pieces.
Q & A
What is the primary manufacturing requirement in sheet metal applications?
-The primary requirement is good formability, which is the sheet metal's ability to deform into intricate shapes without defects.
What types of deformation are typically involved in sheet metal forming operations?
-The main types of deformation include bending, stretching, and drawing.
What factors influence the formability of sheet metal?
-Formability is influenced by ductility, die design, the stamping press, press speed, lubrication, feeding mechanisms, and monitoring systems and controls.
What are the most common types of dies used in sheet metal operations?
-The two most common types of dies are cutting dies and forming dies.
What is the shearing process in sheet metal manufacturing?
-Shearing is a process by which large sheets of material are cut into smaller sections, typically for use in later operations.
What is blanking in sheet metal operations, and what does it produce?
-Blanking is a form of shearing that cuts sheet metal stock around the perimeter of a shape to create a workpiece blank, often for subsequent operations.
How does hole punching work in sheet metal, and why is clearance important?
-Hole punching involves cutting a slug from the sheet metal to produce a hole. Proper clearance between the punch and die is critical to ensure clean cuts and prevent material issues.
What is the purpose of a trimming die in sheet metal forming?
-A trimming die is used to remove excess scrap metal from the workpiece after it has been formed.
What is the drawing process in sheet metal forming, and what challenges does it present?
-Drawing shapes a flat metal blank by forcing it into a die cavity with a punch. Challenges include preventing wrinkling, thinning, or fracturing of the metal, which requires careful control of punch force and blank holder pressure.
What are the different types of hems used in sheet metal forming, and when are they applied?
-The four basic types of hems are flat hem (for materials with high ductility), teardrop hem (for materials with less ductility), open hem, and rope hem (used for joining sheet metal parts). Each is used based on the material and application.
Outlines
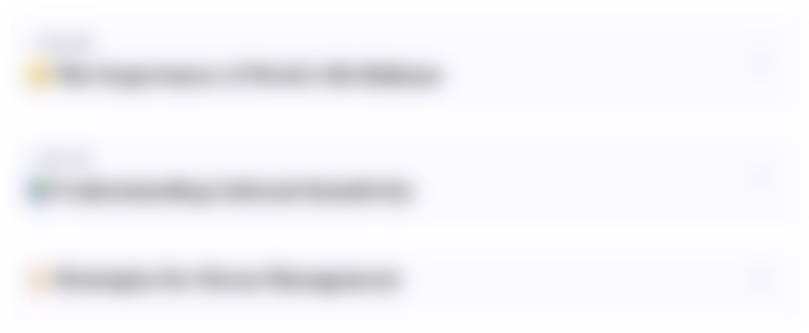
このセクションは有料ユーザー限定です。 アクセスするには、アップグレードをお願いします。
今すぐアップグレードMindmap
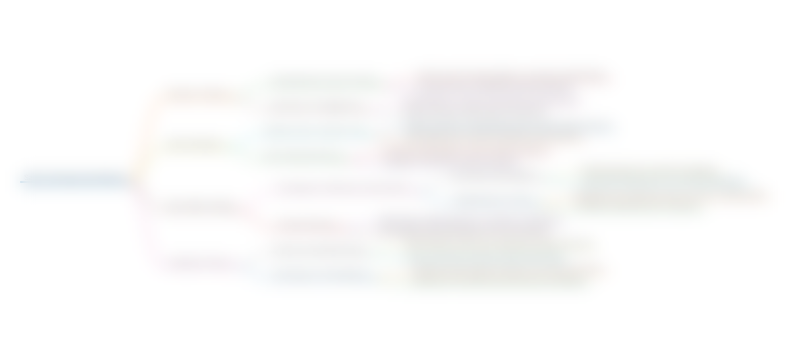
このセクションは有料ユーザー限定です。 アクセスするには、アップグレードをお願いします。
今すぐアップグレードKeywords
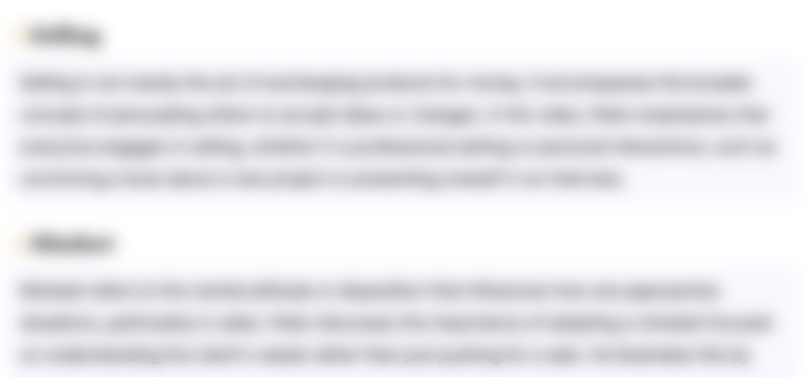
このセクションは有料ユーザー限定です。 アクセスするには、アップグレードをお願いします。
今すぐアップグレードHighlights
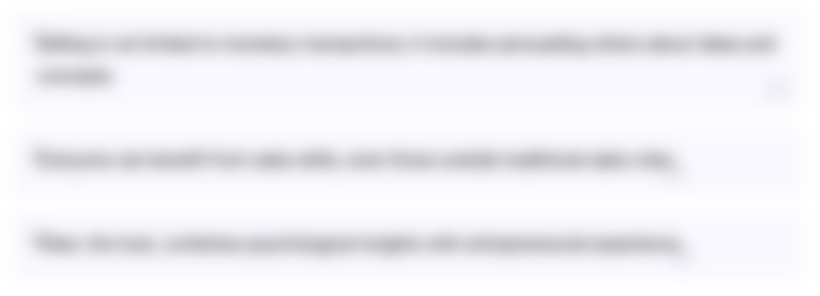
このセクションは有料ユーザー限定です。 アクセスするには、アップグレードをお願いします。
今すぐアップグレードTranscripts
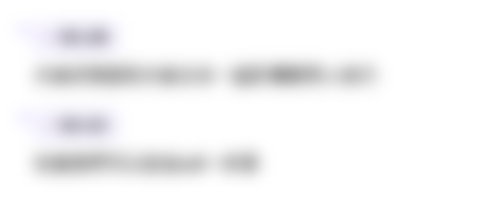
このセクションは有料ユーザー限定です。 アクセスするには、アップグレードをお願いします。
今すぐアップグレード関連動画をさらに表示
5.0 / 5 (0 votes)