#34 Free Lean Six Sigma Green Belt | DMAIC detailed
Summary
TLDRThis video explains the D-MAKE process (Define, Measure, Analyze, Improve, Control) for structured problem-solving. It delves into each stage with a focus on selecting the right tools, such as SIPOC diagrams, benchmarking, root cause analysis, and statistical process control. The process emphasizes the importance of data-driven decisions, team involvement, and an iterative approach to identify causes, implement solutions, and measure improvements. The video also highlights how various problem-solving approaches share common principles, encouraging scientific thinking and collaboration for continuous improvement.
Takeaways
- 😀 Define the problem clearly with a problem statement, a problem charter, and a selected team. Tools like surveys, questionnaires, and CYPOC diagrams are helpful.
- 😀 The Measure stage involves gathering facts and quantifying data, with tools like benchmarking, process sigma calculations, and hypothesis testing.
- 😀 Analyzing the problem requires identifying the root causes using tools like root cause analysis, five whys, and Pareto diagrams to rank the causes.
- 😀 The Improve stage focuses on implementing solutions with tools such as brainstorming, design of experiments, QFD (Quality Function Deployment), and simulation tools.
- 😀 Control the process by ensuring that improvements are maintained through process sigma calculation, customer surveys, and statistical process control charts.
- 😀 The DMAIC process (Define, Measure, Analyze, Improve, Control) is a structured approach that encourages data-driven decisions and scientific thinking.
- 😀 A key feature of problem-solving is the iterative nature of diverging (brainstorming ideas) and converging (prioritizing ideas into solutions) multiple times.
- 😀 Tools should be chosen based on the nature of the problem, not arbitrarily. The right tool must support the goals of each stage.
- 😀 The DMAIC process shares similarities with other structured problem-solving approaches like A3 and PDCA cycles, all emphasizing team involvement and systematic steps.
- 😀 To uncover improvement opportunities, measure differences in processes (e.g., benchmarking between offices or competitors) to identify gaps and solutions.
- 😀 The goal of problem-solving is to find and address the most significant causes to ensure that improvements stick and prevent recurrence.
Q & A
What does DMAIC stand for, and how is it related to problem-solving?
-DMAIC stands for Define, Measure, Analyze, Improve, and Control. It is a structured approach used for problem-solving, which is similar to collaborative problem-solving or A3 problem solving, emphasizing a data-driven and iterative process.
What is the role of the 'Define' phase in the DMAIC process?
-The 'Define' phase involves defining the problem through a problem statement, creating a project charter that outlines the scope, and selecting the team members. This phase is critical for setting clear objectives and identifying the project boundaries.
Which tools can be used in the 'Define' phase to clarify the scope of a project?
-Tools such as surveys or questionnaires can gather the voice of the customer, flow charts, and SIPOC diagrams (Supplier, Input, Process, Output, Customer) help identify the scope and boundaries of the project. SIPOC diagrams provide a high-level overview of the entire value stream from supplier to customer.
What is the purpose of the 'Measure' phase in DMAIC?
-The 'Measure' phase focuses on quantifying and gathering factual data about the current process. This involves tools like benchmarking, process sigma calculations, and hypothesis testing to measure current performance and identify areas for improvement.
How does benchmarking help in the 'Measure' phase?
-Benchmarking compares your process to others, either internally or with competitors, to identify performance gaps. It can be used to assess differences in process performance, helping to uncover areas that need improvement.
What tools are typically used in the 'Analyze' phase to understand the causes of the problem?
-In the 'Analyze' phase, tools like root cause analysis, the 5 Whys method, and Pareto diagrams are used to identify and rank the causes of a problem, ensuring that the most significant causes are addressed first.
Why is the 'Improve' phase critical in the DMAIC process?
-The 'Improve' phase is crucial because it involves implementing solutions to address the root causes identified in the 'Analyze' phase. Tools such as brainstorming, design of experiments, and simulation can help identify and implement the most effective solutions.
What role does simulation play in the 'Improve' phase?
-Simulation tools, such as discrete event simulation, help optimize processes by analyzing factors like batch sizes, factory layouts, or process flows. These simulations provide insights into potential improvements before making real-world changes.
How does the 'Control' phase ensure the sustainability of improvements?
-The 'Control' phase ensures that improvements are sustained by monitoring key performance indicators (KPIs), re-running customer surveys, and using statistical process control charts. This helps to track the continued impact and verify that the process improvements are stable.
What is the key takeaway from the speaker regarding structured problem-solving approaches?
-The key takeaway is that, regardless of the specific problem-solving approach used (such as DMAIC, A3, or PDCA), they all emphasize the importance of using data to make decisions, involving a team, following a structured approach, and continuously improving through iterative cycles.
Outlines
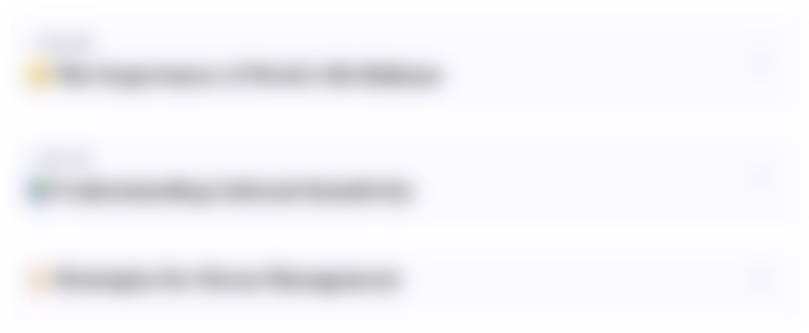
このセクションは有料ユーザー限定です。 アクセスするには、アップグレードをお願いします。
今すぐアップグレードMindmap
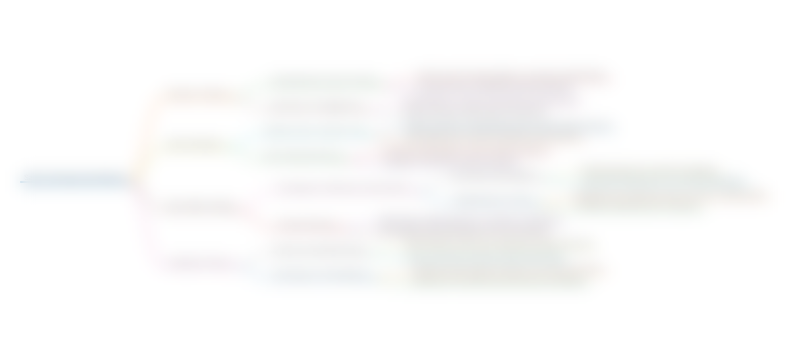
このセクションは有料ユーザー限定です。 アクセスするには、アップグレードをお願いします。
今すぐアップグレードKeywords
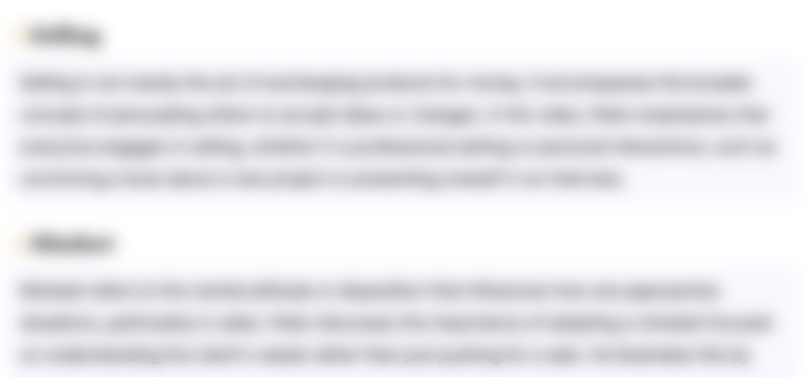
このセクションは有料ユーザー限定です。 アクセスするには、アップグレードをお願いします。
今すぐアップグレードHighlights
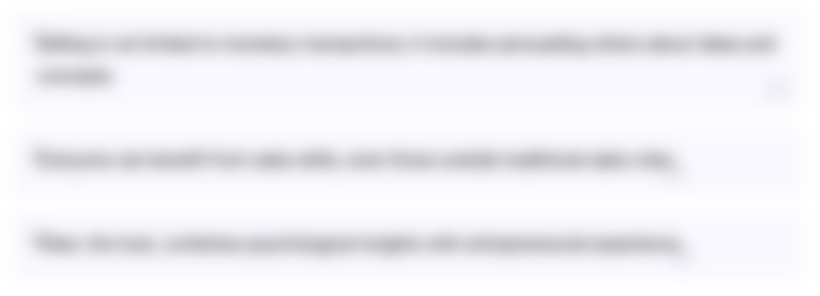
このセクションは有料ユーザー限定です。 アクセスするには、アップグレードをお願いします。
今すぐアップグレードTranscripts
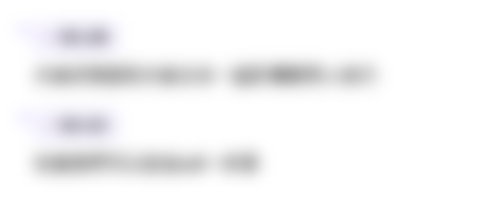
このセクションは有料ユーザー限定です。 アクセスするには、アップグレードをお願いします。
今すぐアップグレード関連動画をさらに表示
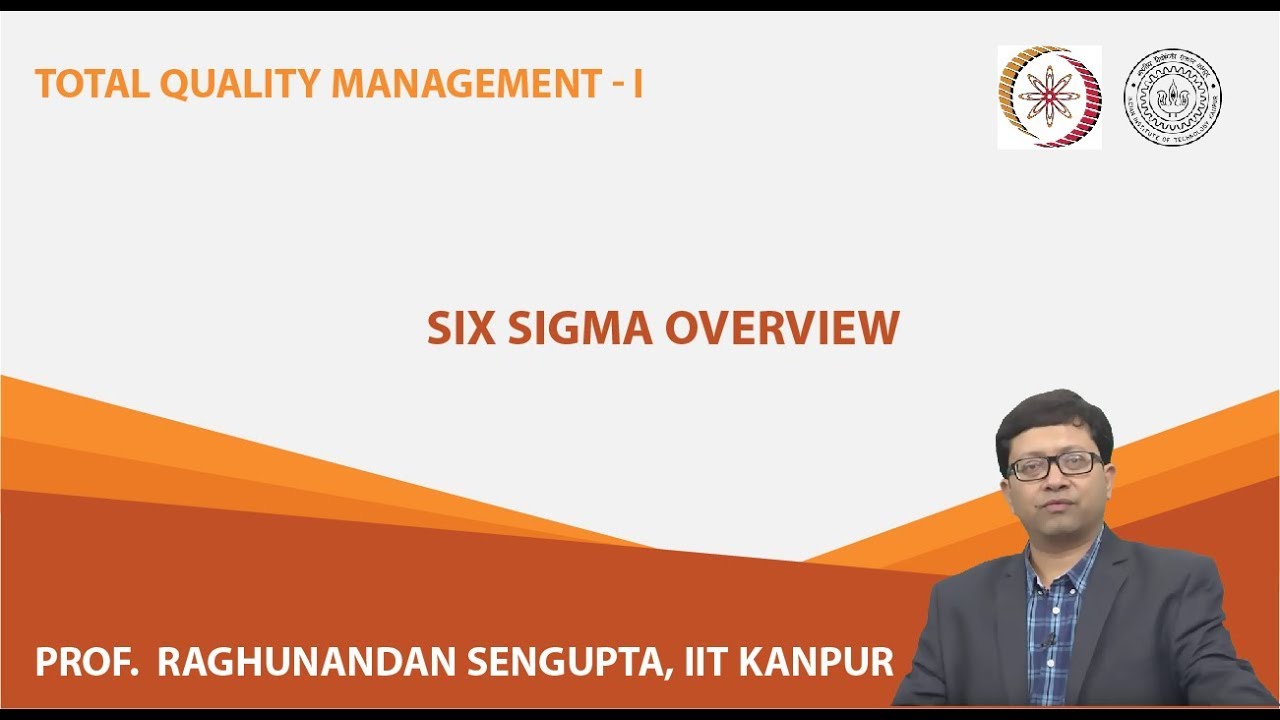
Six Sigma Overview
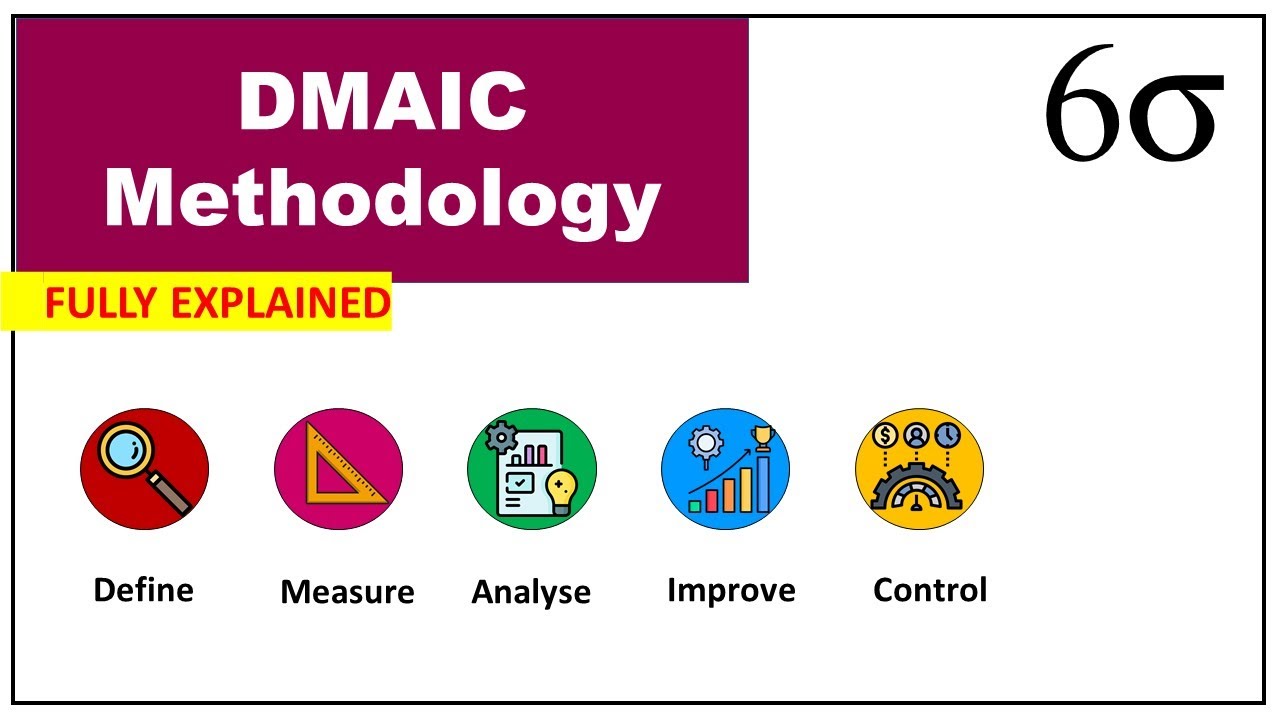
DMAIC Methodology in Six Sigma | Improve Your Processes
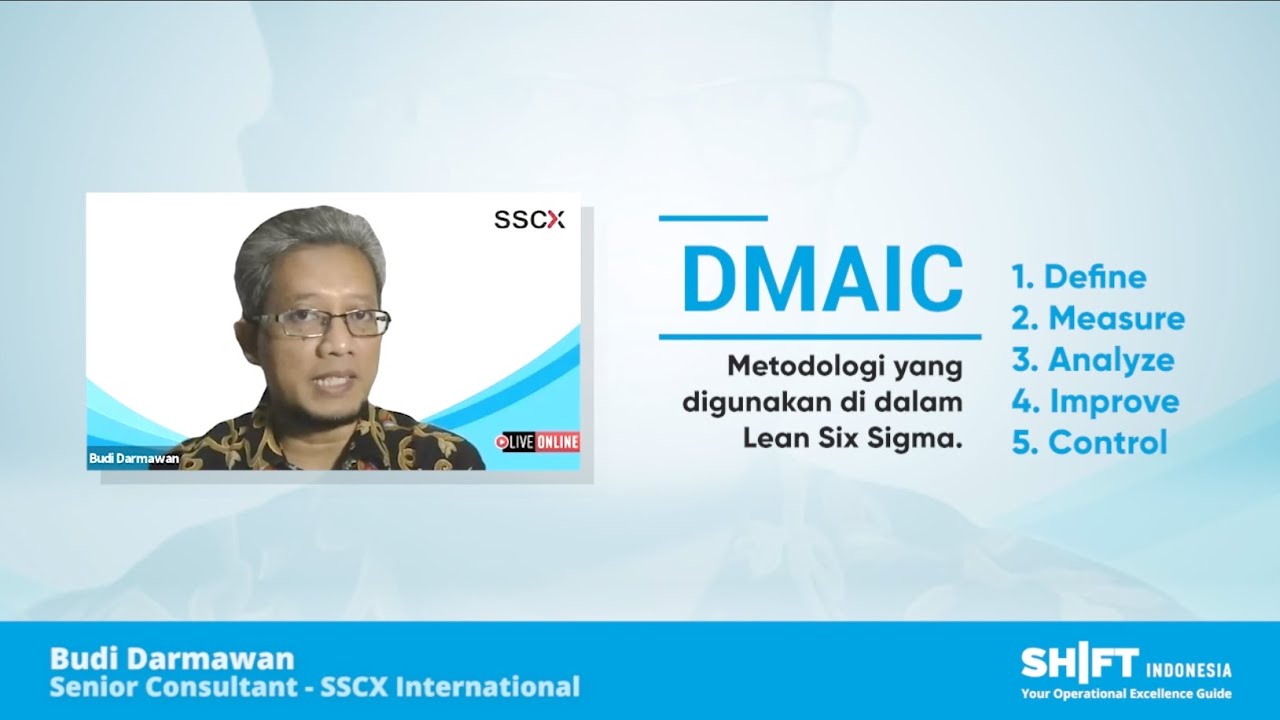
Mengenal 5 Fase di dalam Metodologi DMAIC | SHIFT Indonesia

Tools Metode DMAIC (Define, Measure, Analyse, Improve, Control) Dalam Pengendalian Kualitas
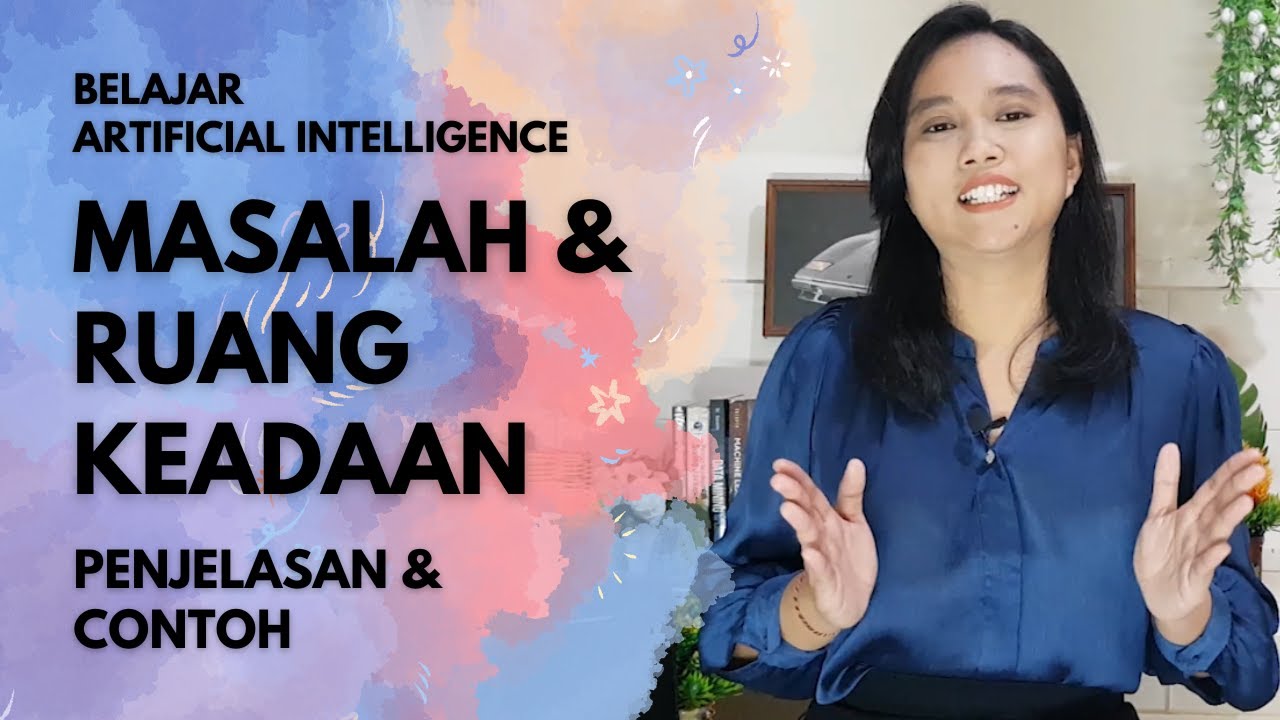
Masalah & Ruang Keadaan Penjelasan dan Contoh | Artificial Intelligence

1. Introduction to the Design Process | Theory
5.0 / 5 (0 votes)