What is an End of Arm Tool (EOAT) in a Robot?
Summary
TLDRThis video introduces the concept of end-of-arm tools on 6-axis robots, explaining their functions and applications. It covers the different ways these tools are powered, including electricity, pneumatics, and hydraulics, and emphasizes the importance of proper maintenance and cable routing. The video also explores various types of end-of-arm tools, such as pick and place tools, vacuum systems, spray guns, welding guns, and vision inspection cameras, highlighting their use in tasks like palletizing, painting, welding, and quality control. Overall, it demonstrates how 6-axis robots streamline repetitive tasks in industrial settings.
Takeaways
- 😀 End-of-arm tools (EOAT) are essential components that connect a 6-axis robot to the work being done, also known as end effectors, grippers, or claws.
- 😀 Regular maintenance of the EOAT connection to the robot is important to avoid equipment damage or potential worker injury.
- 😀 EOATs can be powered by electricity, pneumatics, or hydraulics, depending on the task and requirements.
- 😀 Auxiliary axes, or servo motors, can be part of EOATs to grip and move objects for specific tasks.
- 😀 Routing cables properly in a 6-axis robot is essential to prevent damage to wires and ensure smooth operation.
- 😀 Some 6-axis robots use fixed EOATs, while others have changeable tools for performing multiple tasks, such as cutting and sanding wood.
- 😀 The flexibility of changeable EOATs helps to make robots more economical when performing various tasks.
- 😀 Pick and place EOATs are used for transporting objects, either using a claw or a vacuum device to securely grip and move items.
- 😀 Foam vacuum end-of-arm tools are useful for palletizing, allowing robots to pick up and arrange objects of different sizes and shapes.
- 😀 Welding robots use welding guns as EOATs to precisely weld metal pieces together, with control via discrete I/O to adjust the weld length.
Q & A
What is an end-of-arm tool on a 6-axis robot?
-An end-of-arm tool, also known as an end effector or gripper, is the part of the robot that physically connects the robot to the work being done. It can be used for tasks like gripping, moving, or manipulating objects.
What are some common names for an end-of-arm tool?
-End-of-arm tools are often referred to as end effectors, claws, grippers, or robot tools, depending on the specific application.
How is an end-of-arm tool attached to the robot?
-The end-of-arm tool is attached to the robot via the faceplate, and the connection is secured with hardware. It’s important to check the tightness of this hardware regularly to prevent damage or injury.
What types of power systems are used for end-of-arm tools?
-End-of-arm tools can be powered by electricity (e.g., servo motors), pneumatics (compressed air), or hydraulics, depending on the task and the required force.
Why is it important to route cables and lines properly in a 6-axis robot?
-Proper cable routing is essential to prevent damage when the robot moves. Some robots feature mounting places or hollow spots to safely run cables, avoiding issues like wires being pulled or crushed.
What is the difference between fixed and changeable end-of-arm tools?
-Fixed end-of-arm tools are permanently attached to the robot, while changeable tools can be swapped out depending on the task. For example, a robot could switch from a saw to a sander as needed for different parts of a process.
How does a vacuum foam end-of-arm tool work in palletizing?
-A vacuum foam end-of-arm tool uses a vacuum to temporarily hold objects, such as boxes, on the tool. It is particularly useful for picking up variously sized objects and arranging them on a pallet in an organized way.
What are some applications of spray end-of-arm tools in robots?
-Spray end-of-arm tools are used in applications like vehicle painting, where the robot controls the spray gun to apply paint uniformly. The robot’s movements and paint flow are precisely controlled for a consistent finish.
How do welding end-of-arm tools function on 6-axis robots?
-Welding end-of-arm tools are mounted with welding guns that allow the robot to weld metal parts together. These guns are controlled via discrete I/O to ensure the weld length is accurate and consistent.
How can vision inspection tools enhance robot applications?
-Vision inspection tools, such as cameras, allow robots to perform quality assurance tasks by capturing images of parts to verify if they meet specifications. Robots can also combine vision with pick and place operations to track and move defective parts from a production line.
Outlines
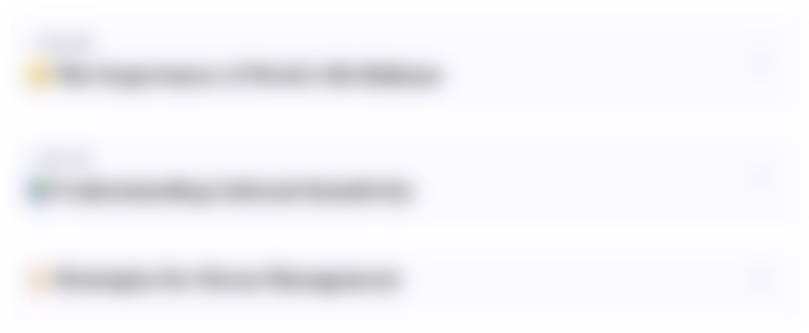
このセクションは有料ユーザー限定です。 アクセスするには、アップグレードをお願いします。
今すぐアップグレードMindmap
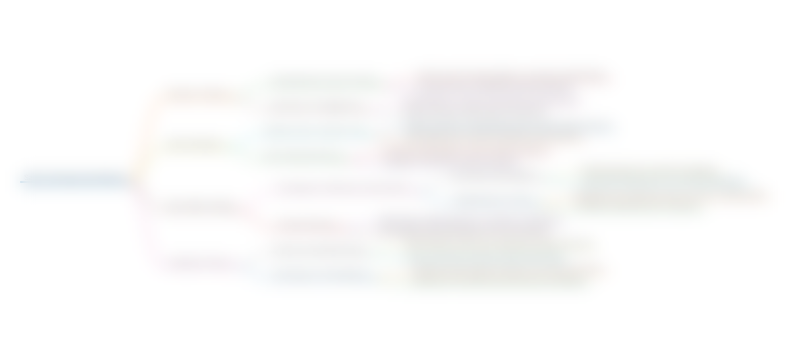
このセクションは有料ユーザー限定です。 アクセスするには、アップグレードをお願いします。
今すぐアップグレードKeywords
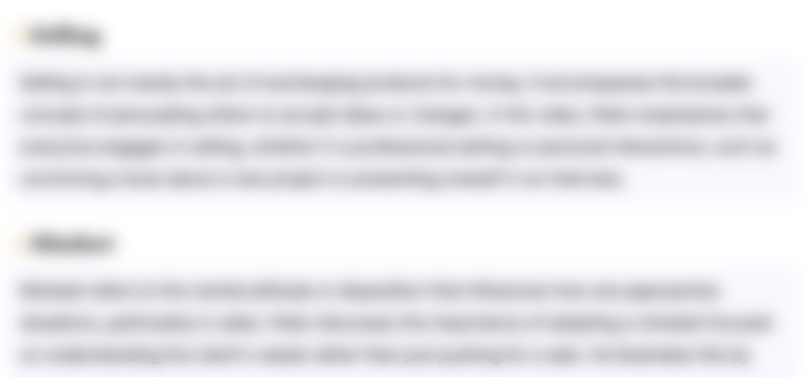
このセクションは有料ユーザー限定です。 アクセスするには、アップグレードをお願いします。
今すぐアップグレードHighlights
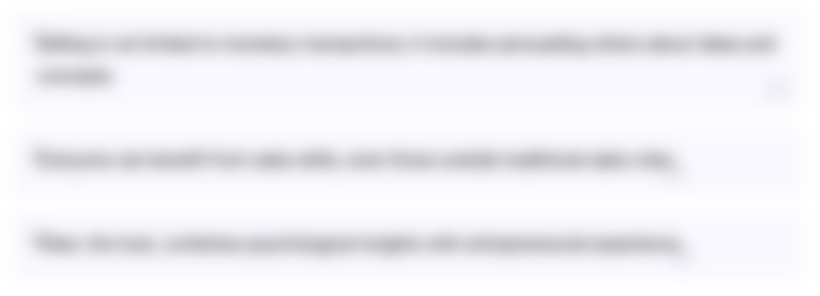
このセクションは有料ユーザー限定です。 アクセスするには、アップグレードをお願いします。
今すぐアップグレードTranscripts
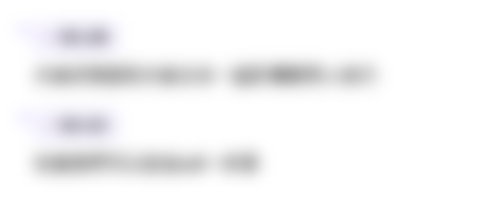
このセクションは有料ユーザー限定です。 アクセスするには、アップグレードをお願いします。
今すぐアップグレード5.0 / 5 (0 votes)