Bridge Designer 2016 Tutorial
Summary
TLDRThis tutorial introduces users to Bridge Designer 2016 software, guiding them through the process of designing and optimizing a steel truss highway bridge. It covers key stages, from setting up design requirements and selecting deck elevation to drawing structural models and testing bridge loads. The tutorial emphasizes the iterative nature of engineering design, showcasing how to balance cost and performance through decisions like member sizing, material selection, and bridge geometry adjustments. By the end, users will gain a practical understanding of bridge design and optimization techniques used by engineers.
Takeaways
- 😀 The Bridge Designer 2016 software is designed to introduce engineering concepts through the process of designing a steel truss highway bridge.
- 😀 The design process starts with creating a new project, where you will set up the project parameters like bridge type and loading requirements.
- 😀 One of the key decisions is choosing the deck elevation, as lowering the deck may reduce span but increase excavation costs.
- 😀 Engineering design often involves trade-offs. Minimizing the bridge cost may increase excavation and vice versa, requiring a balanced approach.
- 😀 The software provides different types of supports (e.g., arch supports, piers) and materials, each impacting cost and structure stability.
- 😀 Starting with a template (like the Warren Through Truss) ensures that your design is structurally sound and ready to handle load testing.
- 😀 You can design the bridge by drawing joints (connection points for steel bars) and members (steel bars themselves), which will form the truss structure.
- 😀 After creating the structure, you can run a load test to see how it performs under weight and truck loading. If it fails, the software identifies weak points.
- 😀 Optimization involves reducing the size of over-engineered members that are stronger than necessary, to decrease costs while maintaining structural integrity.
- 😀 The software allows you to experiment with materials, member sizes, and even geometric configurations (e.g., adding arches) to optimize the design and minimize costs.
Q & A
What is the primary purpose of the Bridge Designer 2016 software?
-The primary purpose of Bridge Designer 2016 is to introduce users to engineering through the design of a steel truss highway bridge. It allows users to create and optimize a bridge design while considering factors like cost and structural integrity.
Why is the deck elevation an important factor in bridge design?
-The deck elevation is important because it affects both the span length of the bridge and the excavation cost. A lower deck elevation reduces the span length but increases excavation costs, whereas a higher deck elevation reduces excavation but increases the span length.
How does the software calculate the site cost of the bridge?
-The site cost is automatically calculated by the software based on the chosen deck elevation and support configuration. It includes factors such as the excavation cost and the cost of concrete supports (abutments).
What trade-off do engineers face when minimizing the bridge's cost?
-Engineers face a trade-off between minimizing bridge cost and site cost. Lowering the deck elevation to reduce the span length leads to higher excavation costs, while increasing the deck elevation reduces excavation costs but increases the bridge cost due to a longer span.
What is the benefit of using a template in Bridge Designer 2016?
-Using a template provides a stable starting point for beginners. It ensures the initial design is structurally sound, which can then be optimized for cost and strength later in the process.
What does the software’s load test feature do?
-The load test feature simulates the bridge being subjected to its own weight and a specified truck load. This test helps identify if any parts of the structure fail under load, allowing for further adjustments to ensure the bridge can safely carry the load.
How does the software help users identify structural weaknesses in the bridge?
-After running a load test, the software visually highlights which members of the bridge have failed by color-coding them. Red indicates compression (squashing), blue indicates tension (stretching), and intensity of the colors shows how heavily loaded each member is.
Why does the software suggest reducing the size of certain members during optimization?
-The software suggests reducing the size of members that are underused or too strong for the given load. This helps to reduce material costs without compromising the bridge's structural integrity.
What is the role of material choice in optimizing a bridge design?
-Choosing stronger materials, like high-strength low-alloy steel or quenched and tempered steel, can allow for smaller members, thus reducing material costs. However, these materials are more expensive, so engineers must balance cost savings with the strength benefits they offer.
How does the geometric configuration of the truss affect its load distribution?
-The geometric configuration, such as the shape of the truss, affects how load is distributed across the structure. For example, adding an arch shape can change the way forces are applied to the bridge and may allow for further optimization in the design.
Outlines
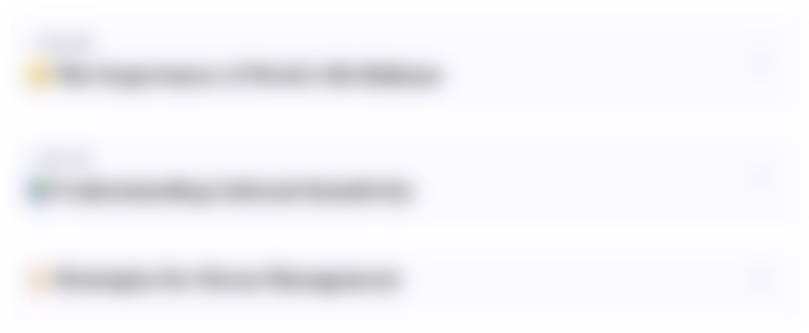
このセクションは有料ユーザー限定です。 アクセスするには、アップグレードをお願いします。
今すぐアップグレードMindmap
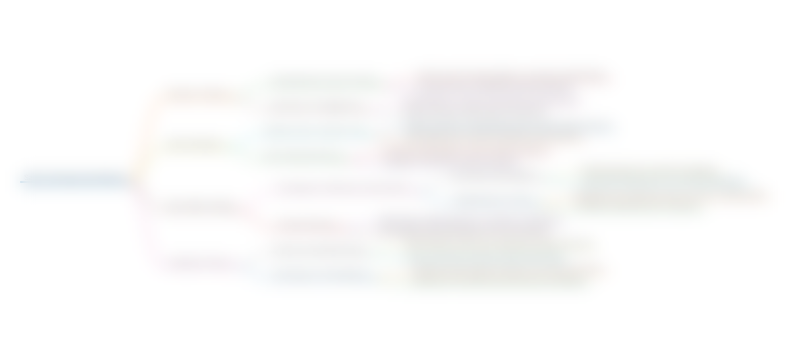
このセクションは有料ユーザー限定です。 アクセスするには、アップグレードをお願いします。
今すぐアップグレードKeywords
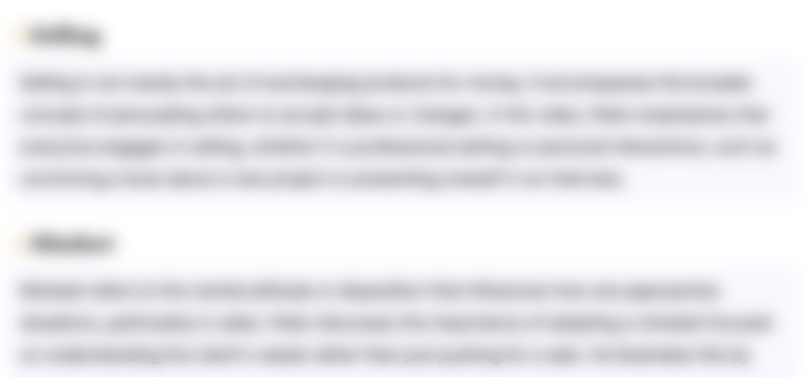
このセクションは有料ユーザー限定です。 アクセスするには、アップグレードをお願いします。
今すぐアップグレードHighlights
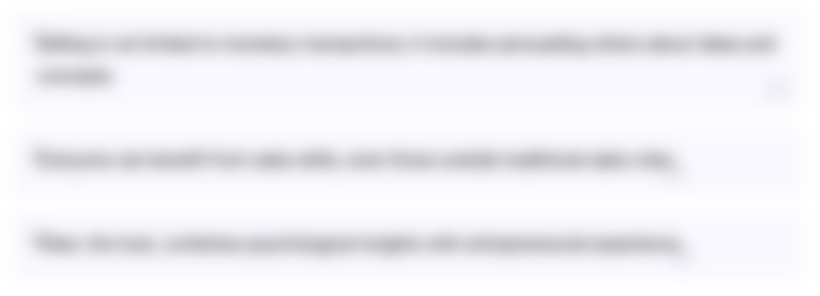
このセクションは有料ユーザー限定です。 アクセスするには、アップグレードをお願いします。
今すぐアップグレードTranscripts
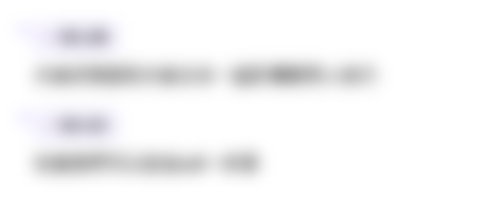
このセクションは有料ユーザー限定です。 アクセスするには、アップグレードをお願いします。
今すぐアップグレード関連動画をさらに表示

Bridge Design (and Destruction!) Part 2
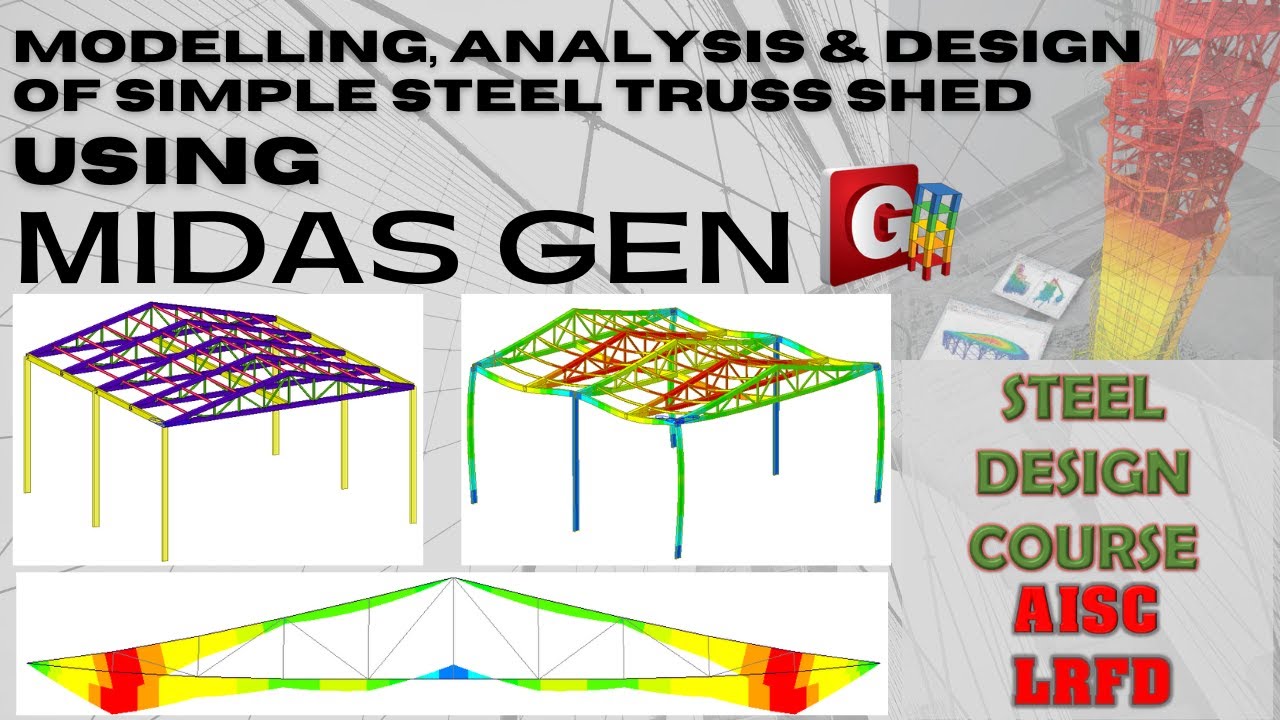
Steel Structures: Analysis/Design Course using MIDAS GEN - SIMPLE STEEL TRUSS SHED (Part 1)
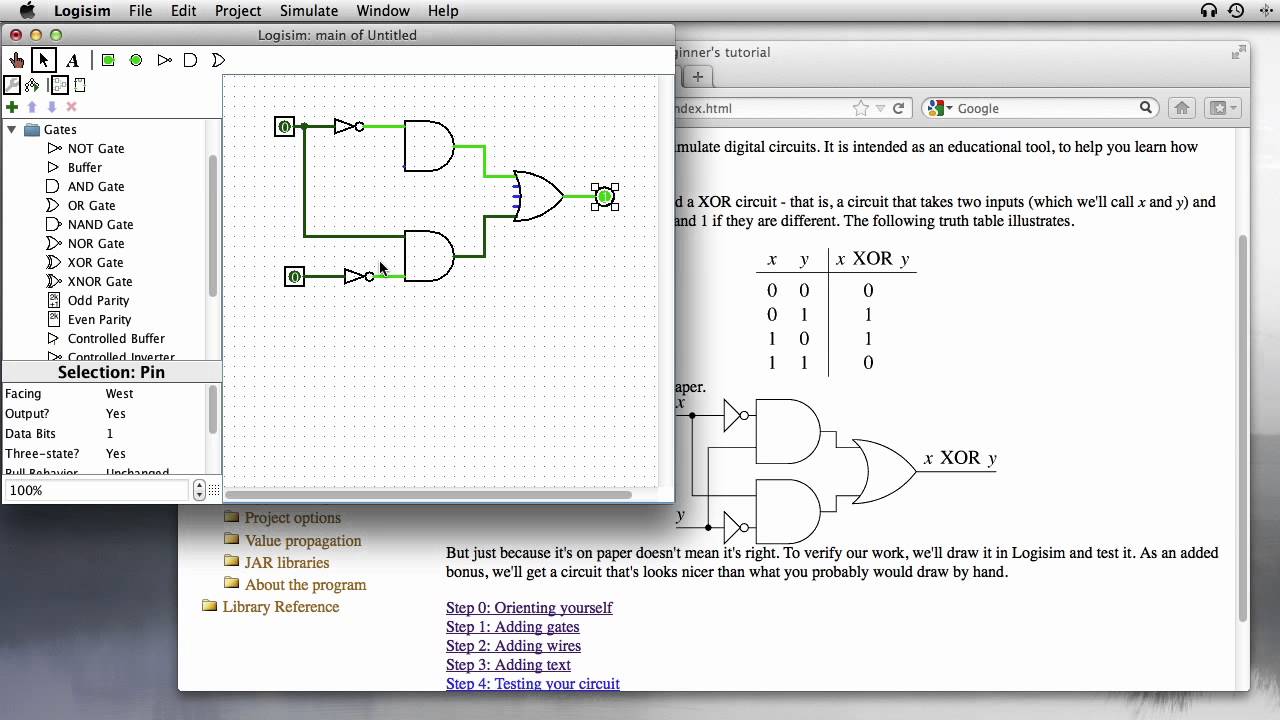
Logisim Beginner's Tutorial
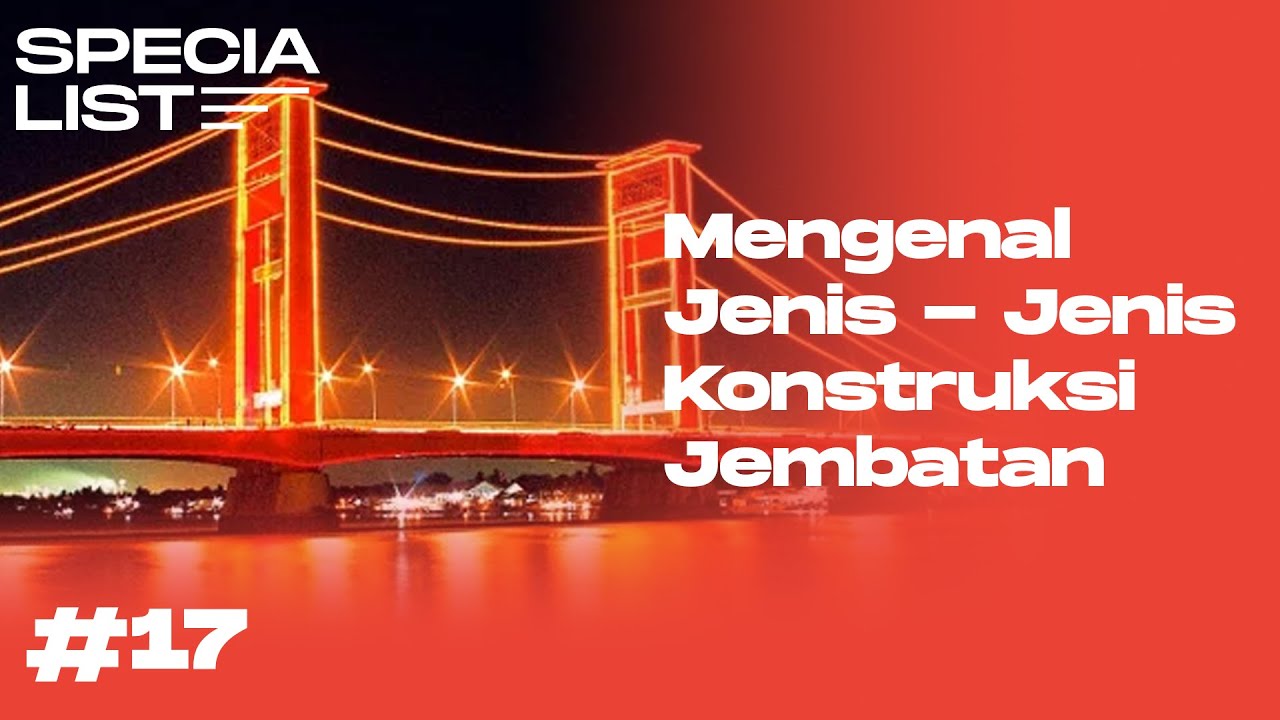
Mengenal Jenis - Jenis Konstruksi Jembatan Bersama Spesialis Konstruksi | SpeciaLIST#17
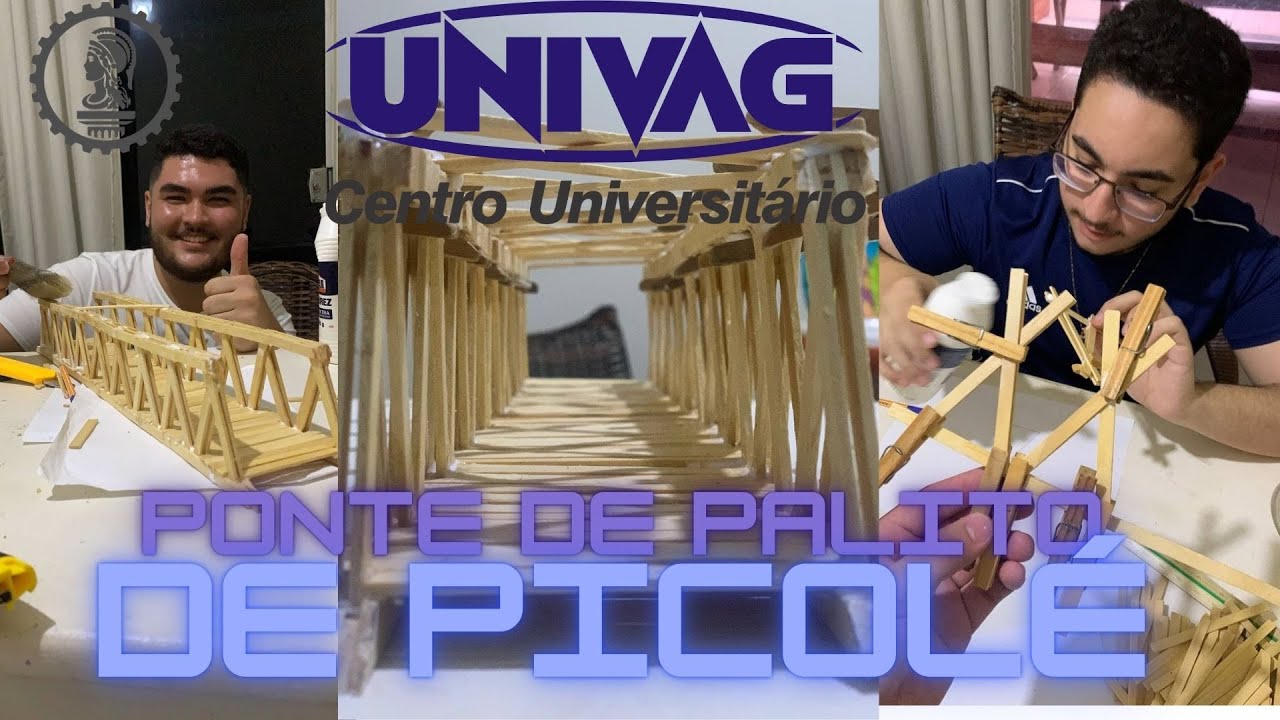
Ponte de Palito de Picolé - Parte 1 - UNIVAG 2021 - Lucas Kenzo - Luiz Gabriel. - Projeto Unificado

Jembatan Wheatstone
5.0 / 5 (0 votes)