Concept of process validation in the pharmaceutical industry
Summary
TLDRThis video explains the critical process validation steps in the pharmaceutical industry, emphasizing the importance of ensuring that manufacturing processes consistently produce high-quality products. It covers key stages such as process design, qualification, and continued verification, alongside approaches like prospective, concurrent, and retrospective validation. The video outlines the essential steps in process validation, including developing a validation master plan, preparing protocols, and managing changes. By adhering to these procedures, pharmaceutical companies can maintain product safety, efficacy, and compliance with regulatory standards like the FDA, ensuring robust, high-quality manufacturing processes.
Takeaways
- 😀 Process validation ensures pharmaceutical manufacturing processes and products meet strict quality standards.
- 😀 Validation is crucial when adopting new manufacturing formulas or methods to guarantee consistent product quality.
- 😀 In tablet production, process validation ensures the final product meets specified active ingredient content (e.g., 500 mg ± 2%).
- 😀 The validation process includes several key stages: process design, process qualification, and continued process verification.
- 😀 Key stages of tablet production—formulation, raw material procurement, blending, granulation, compression, and packaging—require validation.
- 😀 Prospective validation ensures that a process, equipment, or system will function as intended before it is used in production.
- 😀 Concurrent validation involves monitoring and testing samples throughout the production process to ensure control.
- 😀 Retrospective validation relies on historical data and performance records to confirm that a process has consistently met quality standards.
- 😀 A validation master plan outlines the approach and scope for validating each element of the manufacturing process.
- 😀 Worst-case and challenge tests help define the limits and robustness of the manufacturing process to ensure reliability under real-world conditions.
- 😀 Pharmaceutical companies must strictly follow regulatory guidelines, such as those from the FDA, and maintain comprehensive GMP documentation.
Q & A
What is the primary purpose of process validation in the pharmaceutical industry?
-The primary purpose of process validation is to ensure that pharmaceutical manufacturing processes consistently produce products that meet the required quality standards, including safety, efficacy, and stability.
When is process validation required during the manufacturing process?
-Process validation is required when adopting a new manufacturing formula or method of preparation to demonstrate that the process consistently yields products of the desired quality.
Can you give an example of a product where process validation would be necessary?
-For example, when manufacturing paracetamol tablets with a label claim of 500 mg, the manufacturing process must be validated to ensure that all tablets fall within a 2% variance, i.e., between 490 mg and 510 mg.
What are the critical steps in the tablet manufacturing process where validation is required?
-Validation is required in the following steps: tablet formulation, raw material procurement and testing, blending and granulation, tablet compression, and packaging.
What are the three stages of process validation?
-The three stages of process validation are: Stage 1 - Process Design, Stage 2 - Process Qualification, and Stage 3 - Continued Process Verification.
What is the difference between prospective validation and concurrent validation?
-Prospective validation involves pre-planned scientific tests to establish that a process will perform as intended. Concurrent validation, on the other hand, involves testing samples during routine production to demonstrate that the process is consistently in a state of control.
What is retrospective validation and when is it used?
-Retrospective validation involves reviewing and analyzing historical data and process performance to establish confidence that a process can consistently produce products of the desired quality. It is typically used for established processes with historical data.
What are the essential steps to be followed during process validation?
-The essential steps are: developing a validation master plan, preparing process validation protocols, identifying prerequisites, selecting the validation approach, conducting worst-case and challenge tests, determining a matrix or family approach, performing validation testing, documenting activities, and managing changes.
What does the worst-case testing in process validation involve?
-Worst-case testing involves deliberately challenging the process by simulating changes or adverse conditions to define the process's robustness and tolerance limits, ensuring reliability under real-world conditions.
Why is it important to manage changes during the process validation phase?
-Managing changes is critical because any change impacting product quality or process reproducibility must be evaluated for its effect on the validation status and product stability, ensuring that the process remains within control and compliant with regulatory standards.
Outlines
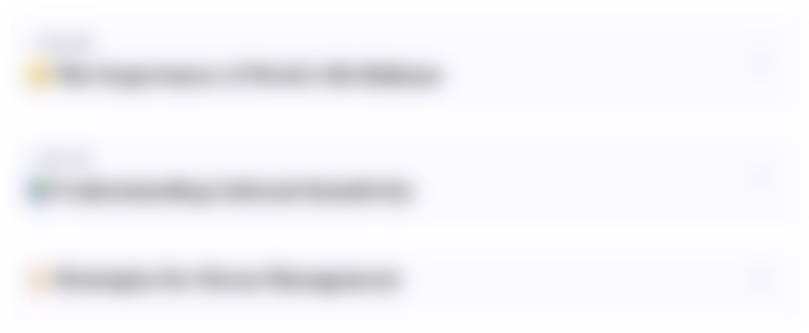
このセクションは有料ユーザー限定です。 アクセスするには、アップグレードをお願いします。
今すぐアップグレードMindmap
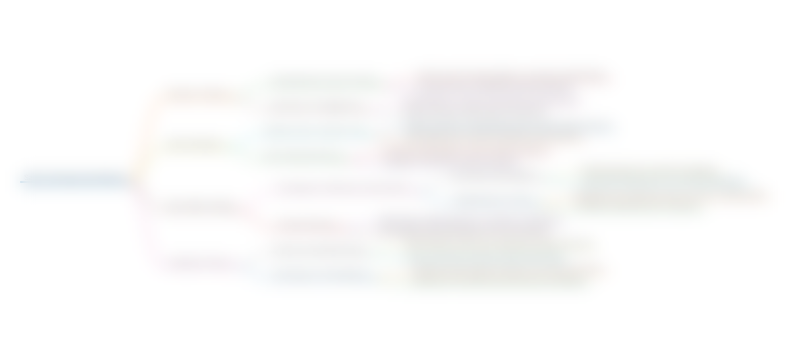
このセクションは有料ユーザー限定です。 アクセスするには、アップグレードをお願いします。
今すぐアップグレードKeywords
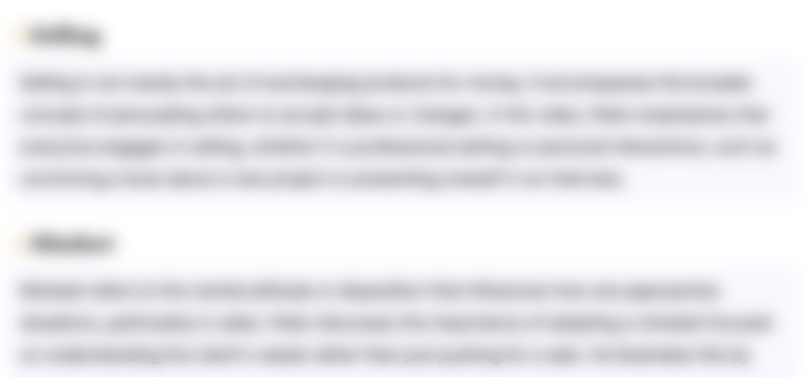
このセクションは有料ユーザー限定です。 アクセスするには、アップグレードをお願いします。
今すぐアップグレードHighlights
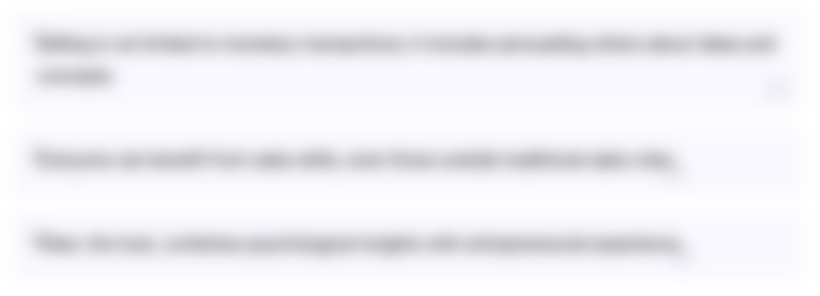
このセクションは有料ユーザー限定です。 アクセスするには、アップグレードをお願いします。
今すぐアップグレードTranscripts
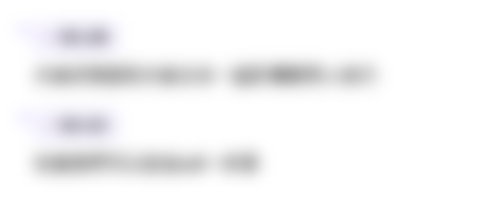
このセクションは有料ユーザー限定です。 アクセスするには、アップグレードをお願いします。
今すぐアップグレード関連動画をさらに表示

BTF1133 CHAPTER 4 DRYING
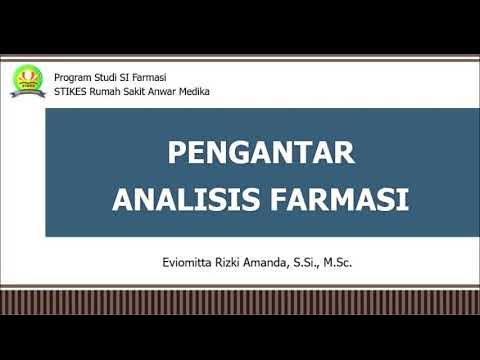
ANALISIS FARMASI II: PENGANTAR ANALISIS FARMASI II

Klasifikasi Ruangan di Industri Farmasi

Pembuatan PULP dan KERTAS - Diagram Alir Proses
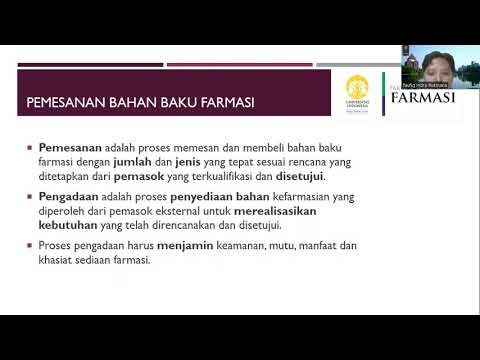
MOOCs Pengelolaan Bahan Baku dan Produk di Industri Farmasi (Sesi 1)

Cara Pembuatan Obat Baik (CPOB) - PRODUKSI // Kelompok 11 PKLI 2021 Farmasi UIN Malang
5.0 / 5 (0 votes)