Calibrate Your XY & Z Steps For Dimensional Accuracy of Your 3D Prints
Summary
TLDRThis video walks viewers through the process of calibrating a 3D printer for dimensional accuracy, specifically focusing on an Ender 3. After covering essential steps like e-step calibration and flow rate adjustment, the tutorial demonstrates two methods for fine-tuning print dimensions: using a dial indicator for high accuracy or measuring printed parts directly, which is less precise but still effective. By printing and measuring a 40mm calibration cube, users adjust the printer's steps per millimeter, repeating the process until the desired accuracy is achieved. The video emphasizes the importance of calibration for optimal print quality and consistency.
Takeaways
- 😀 Ensure your e-steps and flow rate are calibrated before calibrating for dimensional accuracy to avoid flawed results.
- 😀 There are two methods for calibrating dimensional accuracy: using dial indicators (more accurate) and measuring printed parts (less accurate but still useful).
- 😀 Many 3D printing enthusiasts don't have dial indicators, so measuring printed parts is a practical alternative.
- 😀 The 40mm calibration cube is a common test part used for dimensional accuracy checks; scaling it up to 200% gives a more accurate result.
- 😀 Always measure the printed part along the X, Y, and Z axes to get accurate results for dimensional calibration.
- 😀 Use the formula (current steps × expected size) ÷ measured size to calculate new steps per millimeter for each axis.
- 😀 It's important to update and save the new steps per millimeter after recalculating them to ensure accuracy.
- 😀 If the first print doesn't meet the expected dimensions, recalibrate and reprint until the measurements are within acceptable tolerance ranges.
- 😀 Always store your settings after adjusting steps per millimeter; failure to do so means your changes will be lost after turning off the printer.
- 😀 A well-calibrated printer should produce parts with dimensions that are within a reasonable tolerance, like the final results of 40.06mm (X), 40.01mm (Y), and 40.08mm (Z).
Q & A
What is the first step in calibrating a 3D printer for dimensional accuracy?
-The first step is to ensure that the e-steps and flow rate are properly calibrated. Without this, any dimensional accuracy adjustments may produce flawed results.
What are the two methods of calibrating dimensional accuracy on a 3D printer?
-The two methods are: Method 1, which uses a dial indicator to measure travel distance on each axis (most accurate), and Method 2, which involves measuring the dimensions of a printed part and adjusting the steps based on those measurements (less accurate).
Why is using a dial indicator considered more accurate for calibration?
-Using a dial indicator directly measures the exact movement of the printer's axes, providing more precise data for calibration compared to measuring printed parts, which may have slight variations.
What is the advantage of using the printed part method for calibration?
-The printed part method is more accessible because it doesn't require specialized tools like a dial indicator. It relies on measuring the dimensions of a printed calibration part, which is practical for most 3D printing enthusiasts.
How does the calibration process work with the printed part method?
-First, you print a calibration part (like a 40mm cube), then measure its dimensions (X, Y, Z) using calipers. Using those measurements, you calculate the new steps per millimeter for each axis and update the printer's settings accordingly.
What formula is used to calculate the new steps per millimeter for each axis?
-The formula is: (Current steps * Expected size) / Measured size. This is applied to each axis to adjust the steps and achieve the desired dimensional accuracy.
How do you ensure the printer settings are saved after adjustments?
-After adjusting the steps per millimeter, you need to go back to the main menu and select 'store settings' to ensure the new configurations are saved. If not saved, the settings will be lost when the printer is powered off.
What should you do if the initial calibration results are outside of an acceptable tolerance range?
-If the measurements are outside the acceptable range, you should recalculate the steps per millimeter using the new measurements and update the printer's settings accordingly. Reprint the calibration part to check the results again.
Why is it important to print the calibration cube at 40mm rather than 20mm?
-Printing the cube at 40mm increases the accuracy of the calibration because larger parts provide more reliable measurements. The larger the part, the more accurate the results tend to be, though it will take longer to print.
What should you do if the printer is not producing the desired dimensions even after recalibration?
-If recalibration doesn't result in the desired dimensions, you should repeat the calibration process, carefully measuring and recalculating the steps per millimeter. It may take two or more iterations to achieve perfect dimensional accuracy.
Outlines
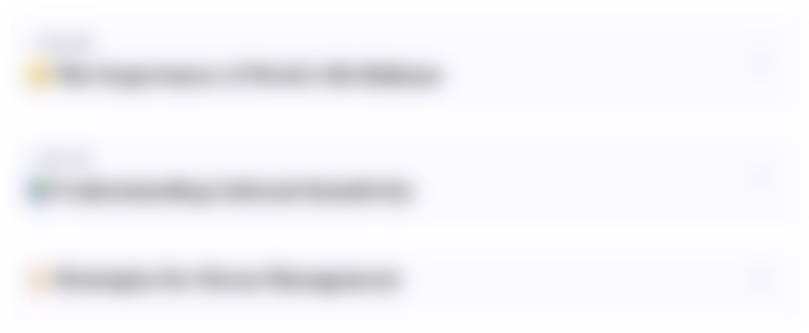
このセクションは有料ユーザー限定です。 アクセスするには、アップグレードをお願いします。
今すぐアップグレードMindmap
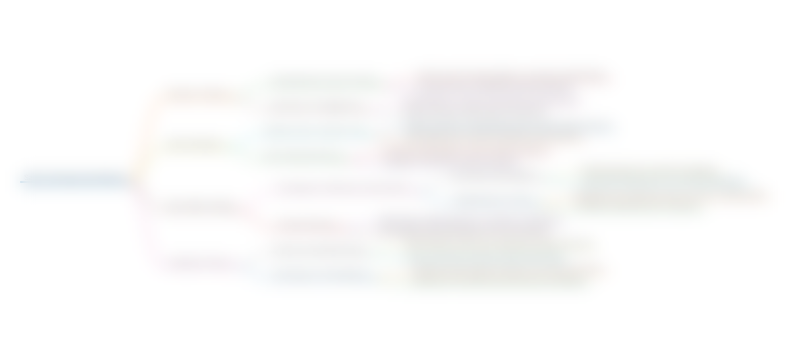
このセクションは有料ユーザー限定です。 アクセスするには、アップグレードをお願いします。
今すぐアップグレードKeywords
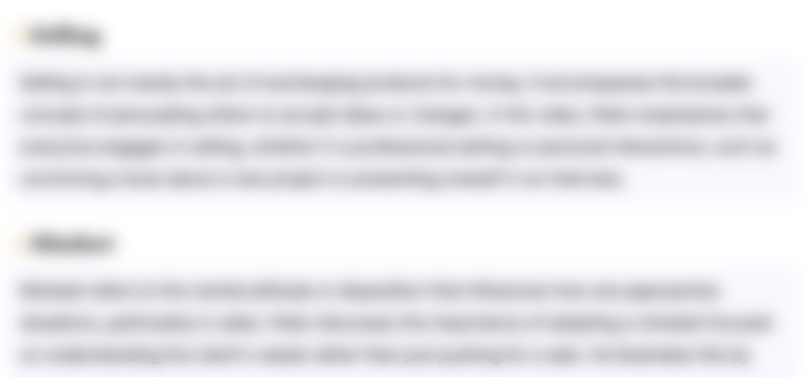
このセクションは有料ユーザー限定です。 アクセスするには、アップグレードをお願いします。
今すぐアップグレードHighlights
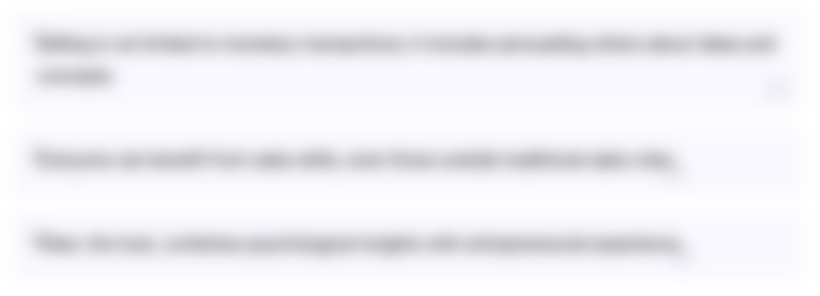
このセクションは有料ユーザー限定です。 アクセスするには、アップグレードをお願いします。
今すぐアップグレードTranscripts
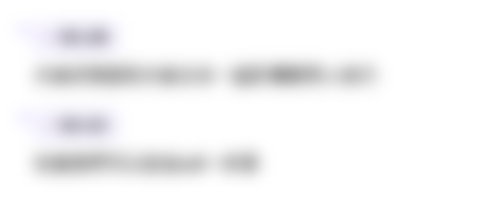
このセクションは有料ユーザー限定です。 アクセスするには、アップグレードをお願いします。
今すぐアップグレード5.0 / 5 (0 votes)