Liane Okdinawati: Strategic Capacity (Part 1)
Summary
TLDRThis video on operation management introduces key concepts of capacity in production and services. The instructor explains that capacity refers to the maximum output of goods and services over a specific time under normal working conditions. Factors influencing capacity include market demand, seasonal variations, and resource availability. The video highlights different methods for measuring capacity, such as input-output analysis and operational strategies. By providing examples from various industries, the instructor emphasizes the importance of accurately assessing capacity to meet market needs effectively. Viewers can expect further discussions on capacity strategies in subsequent videos.
Takeaways
- 😀 Capacity is defined as the maximum output an organization can produce within a specific time frame under normal working conditions.
- 😀 Understanding capacity is crucial for managing the production of goods and services effectively.
- 😀 There are three essential components of operation management: capacity, people, and processes.
- 😀 Market demands and seasonal variations play significant roles in determining capacity requirements.
- 😀 Measuring capacity can be done through input or output methods, depending on the context and industry.
- 😀 Examples of capacity include the number of passengers a train can carry or the number of rooms in a hotel.
- 😀 A simple formula to measure capacity is: Capacity = Time Available / Time Required.
- 😀 Companies must consider both maximum output and actual long-term capacity when making operational decisions.
- 😀 Input-based approaches measure capacity by assessing available resources, while output-based approaches focus on finished products.
- 😀 Effective capacity management is essential for ensuring that an organization can meet market needs efficiently.
Q & A
What are the three key considerations in operation management when discussing production of goods and services?
-The three key considerations are capacity, the workforce (men), and the resources (materials).
How is capacity defined in the context of production?
-Capacity is defined as the amount of a resource (like equipment, labor, or materials) available to produce output within a specific time period under normal working conditions.
What factors affect the decisions regarding capacity?
-Decisions related to capacity are influenced by market demand, seasonal variations, and timing issues.
What are the two main methods companies use to measure capacity?
-Companies measure capacity using either input-output analysis or a combination of both.
Can you provide an example of measuring capacity based on input?
-An example of measuring capacity by input is in a hotel, where the number of available rooms determines capacity.
How can capacity be measured based on output?
-Capacity based on output can be measured by the number of finished units produced in a manufacturing process, such as the amount of textiles produced.
What is a simple formula to calculate capacity?
-A simple formula to calculate capacity is: Capacity = Time Available / Time Required per Unit.
What is the difference between maximum output capacity and effective capacity?
-Maximum output capacity refers to the highest output possible without downtime, while effective capacity accounts for real-world factors like downtime and inefficiencies.
Why is it important to accurately measure capacity?
-Accurate measurement of capacity is crucial for effective operational planning and ensuring that production can meet market demands.
What will be discussed in the next video related to capacity?
-The next video will focus on capacity strategies.
Outlines
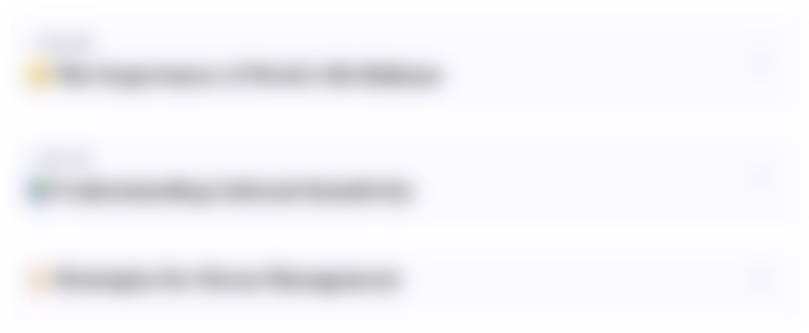
このセクションは有料ユーザー限定です。 アクセスするには、アップグレードをお願いします。
今すぐアップグレードMindmap
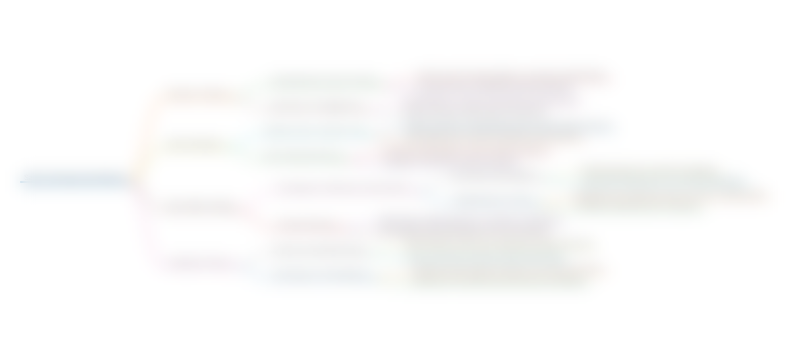
このセクションは有料ユーザー限定です。 アクセスするには、アップグレードをお願いします。
今すぐアップグレードKeywords
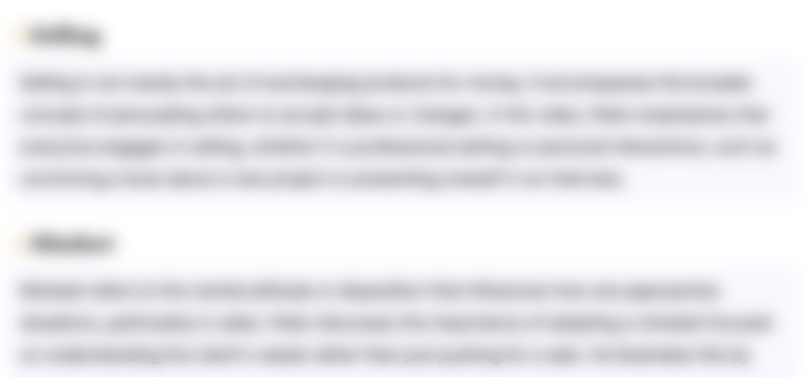
このセクションは有料ユーザー限定です。 アクセスするには、アップグレードをお願いします。
今すぐアップグレードHighlights
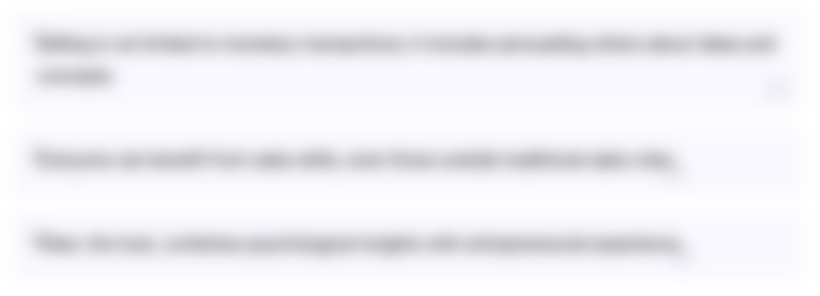
このセクションは有料ユーザー限定です。 アクセスするには、アップグレードをお願いします。
今すぐアップグレードTranscripts
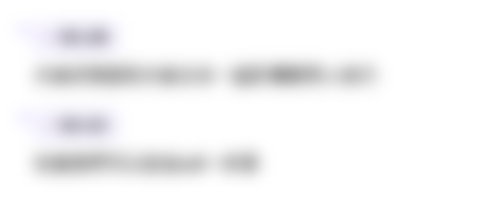
このセクションは有料ユーザー限定です。 アクセスするには、アップグレードをお願いします。
今すぐアップグレード5.0 / 5 (0 votes)