Pengantar Bisnis Sesi 11 Produksi dan Manajemen Operasi
Summary
TLDRThis script discusses production and operations management in a business context. It covers production processes, including continuous and intermittent processes, and the transformation of raw materials into finished goods through manufacturing and assembly. The lecture also touches on operational management issues like facility location, materials classification, inventory control, and quality control. It introduces concepts like Just-In-Time inventory, Material Requirements Planning (MRP), and Enterprise Resource Planning (ERP). The summary also mentions quality control methods such as Six Sigma, statistical quality control, and the Deming cycle.
Takeaways
- 🏭 Production involves using inputs such as land, labor, and capital to generate outputs like goods and services.
- 🔄 There are two types of production processes: continuous (long-term production) and intermittent (short-term, flexible production).
- ⚙️ Manufacturing and assembly are two distinct production processes. Manufacturing changes raw materials physically or chemically, while assembly involves combining components.
- 📍 Facility location is critical, considering factors like labor costs, resource availability, transportation, taxes, and government support.
- 💻 Telecommuting and online collaboration (inter-firm processes) are becoming common for companies working with external suppliers.
- 📦 Just-in-Time (JIT) inventory control minimizes inventory, ensuring materials are delivered exactly when needed, enhancing production efficiency.
- 🛠 Material Requirement Planning (MRP) and Enterprise Resource Planning (ERP) are systems that help manage production schedules and resources effectively.
- 🏅 Quality control methods include Six Sigma, statistical quality control, and Deming's cycle (Plan, Do, Check, Act) to ensure consistency and minimize errors.
- 📊 Statistical process control involves testing product samples at different stages of production to ensure quality standards are met.
- 🤝 Purchasing is responsible for sourcing high-quality materials and negotiating favorable prices with suppliers.
Q & A
What is the main topic discussed in the script?
-The main topic discussed in the script is production and operations management in the context of business.
What are the activities involved in the production process?
-The activities involved in the production process include using production factors or inputs like land, labor, and capital to produce outputs in the form of goods or services through activities such as planning, routing, and scheduling.
What is the difference between continuous and intermittent production processes?
-Continuous production processes occur over a long period and produce goods continuously, while intermittent processes have short production cycles and often adapt to produce different products.
What is meant by 'adding value' in the production process?
-Adding value in the production process refers to transforming raw materials into useful or finished goods, thereby increasing their worth.
What are the two different processes a producer can undertake when producing a good or service?
-The two different processes are manufacturing and assembly. Manufacturing involves physical or chemical transformation of materials, while assembly involves combining components to create a product.
Can you provide an example of manufacturing and assembly processes from the script?
-An example given is the transformation of quartz sand into glass for a chandelier, which is a manufacturing process, and the installation of cables, decorations, and other components, which is an assembly process.
What is facility location and why is it important?
-Facility location is the process of choosing a geographical location for a company's operations. It is important because it involves considerations such as labor costs, availability of resources, transportation access, taxes, crime levels, government support, and more.
What is the concept of 'outsourcing' mentioned in the script?
-Outsourcing is the practice of contracting out a company's functions to another company that specializes in that particular activity, often over the internet, creating new relationships with suppliers.
What is the purpose of materials management in a company?
-The purpose of materials management in a company is to find high-quality resources, identify the best suppliers, and negotiate the best prices for quality goods and services.
What is Just-In-Time (JIT) inventory control and how does it work?
-Just-In-Time (JIT) inventory control is a principle that aims to keep inventory levels to a minimum and deliver supplies and other requirements exactly when they are needed on the assembly line.
What are Material Requirements Planning (MRP) and Enterprise Resource Planning (ERP)?
-Material Requirements Planning (MRP) is a computer-based system that uses sales forecasts to ensure that the necessary parts and materials are available at the right time and place. Enterprise Resource Planning (ERP) is an updated version of MRP that integrates the functions of all divisions and subsidiaries of a company into a single, integrated software program using a single database.
What are some methods for monitoring and maintaining quality in operations management?
-Some methods for monitoring and maintaining quality include Six Sigma, Statistical Quality Control, Statistical Process Control, and the Deming Cycle.
Can you explain the Six Sigma quality method briefly?
-Six Sigma is a quality method that sets a benchmark of 1.33 defects per million opportunities and is based on the principle of preventing problems before they occur by detecting potential issues.
Outlines
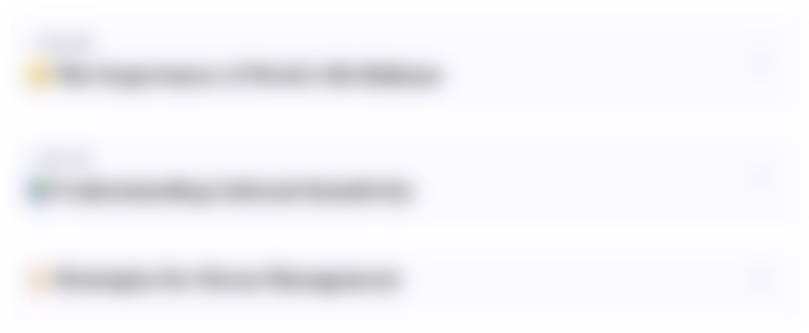
このセクションは有料ユーザー限定です。 アクセスするには、アップグレードをお願いします。
今すぐアップグレードMindmap
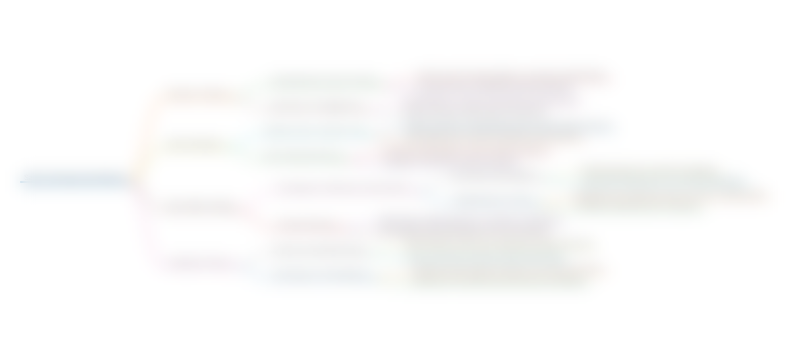
このセクションは有料ユーザー限定です。 アクセスするには、アップグレードをお願いします。
今すぐアップグレードKeywords
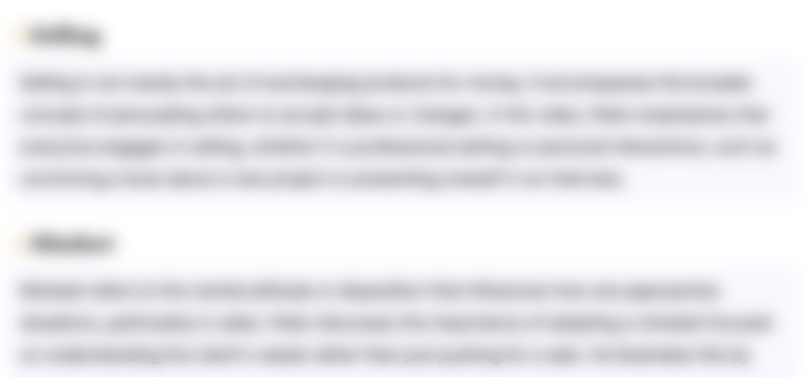
このセクションは有料ユーザー限定です。 アクセスするには、アップグレードをお願いします。
今すぐアップグレードHighlights
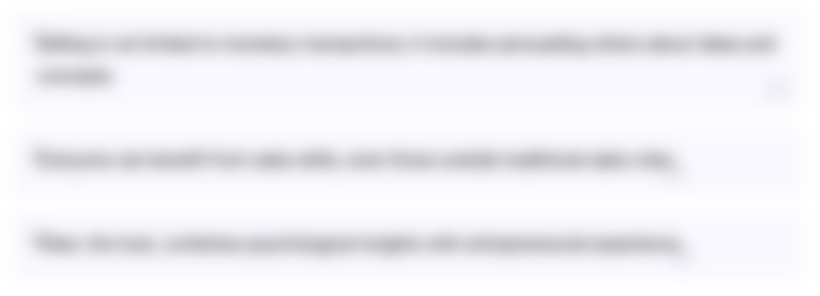
このセクションは有料ユーザー限定です。 アクセスするには、アップグレードをお願いします。
今すぐアップグレードTranscripts
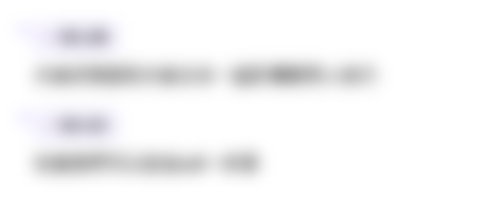
このセクションは有料ユーザー限定です。 アクセスするには、アップグレードをお願いします。
今すぐアップグレード関連動画をさらに表示
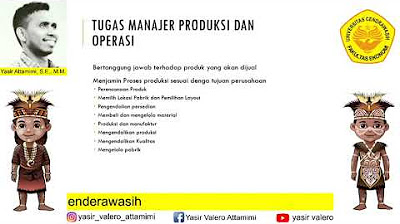
Materi kuliah Pengantar Bisnis, Pertemuan Ke-5

5.1 INTRODUCTION TO OPERATIONS MANAGEMENT / IB BUSINESS MANAGEMENT / production, sustainability
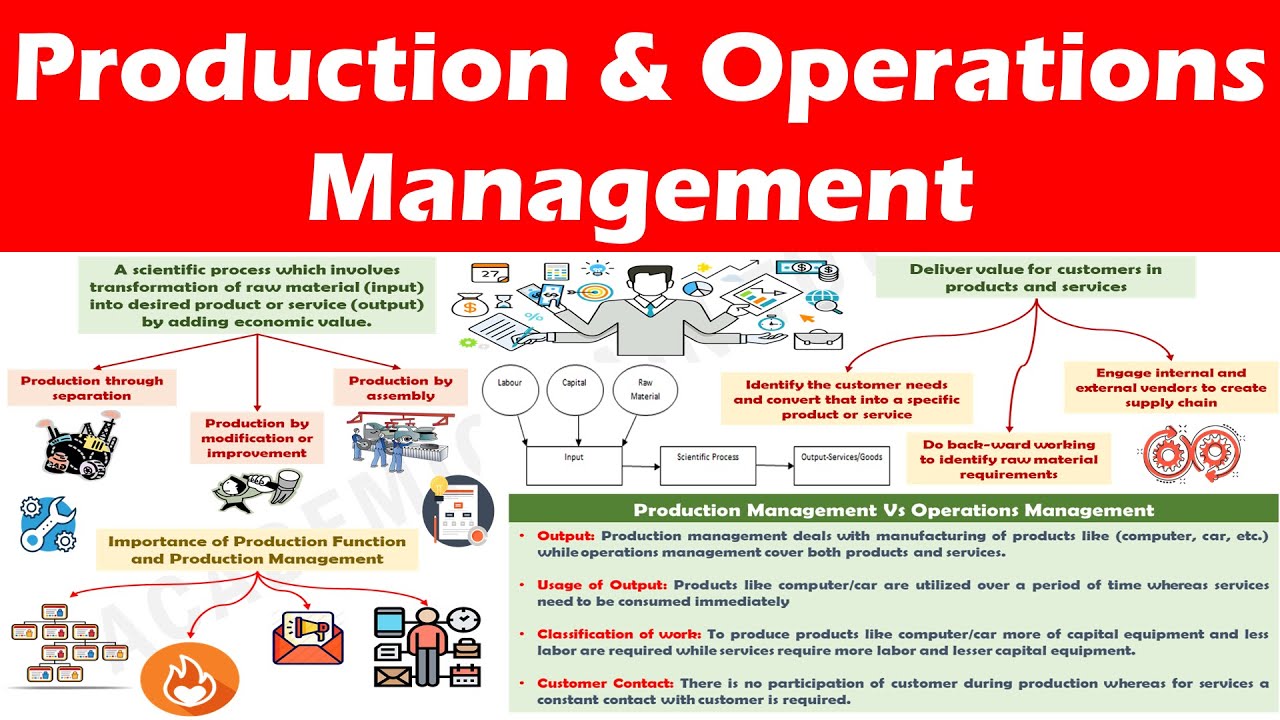
Production and Operations Management - Understanding the concept.
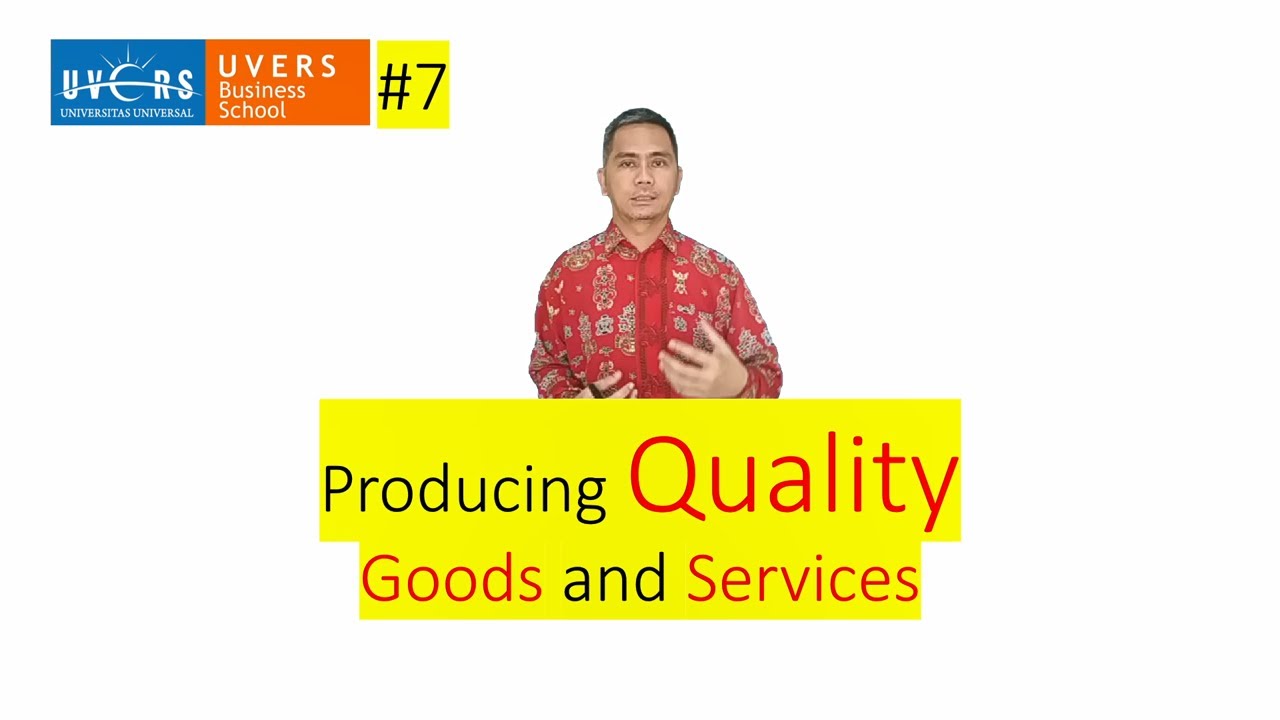
#7-#8 Producing Quality Goods and Services
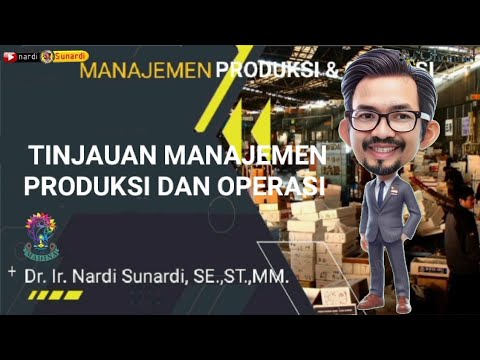
Bab 1 Tinjauan Manajemen Produksi dan Operasi
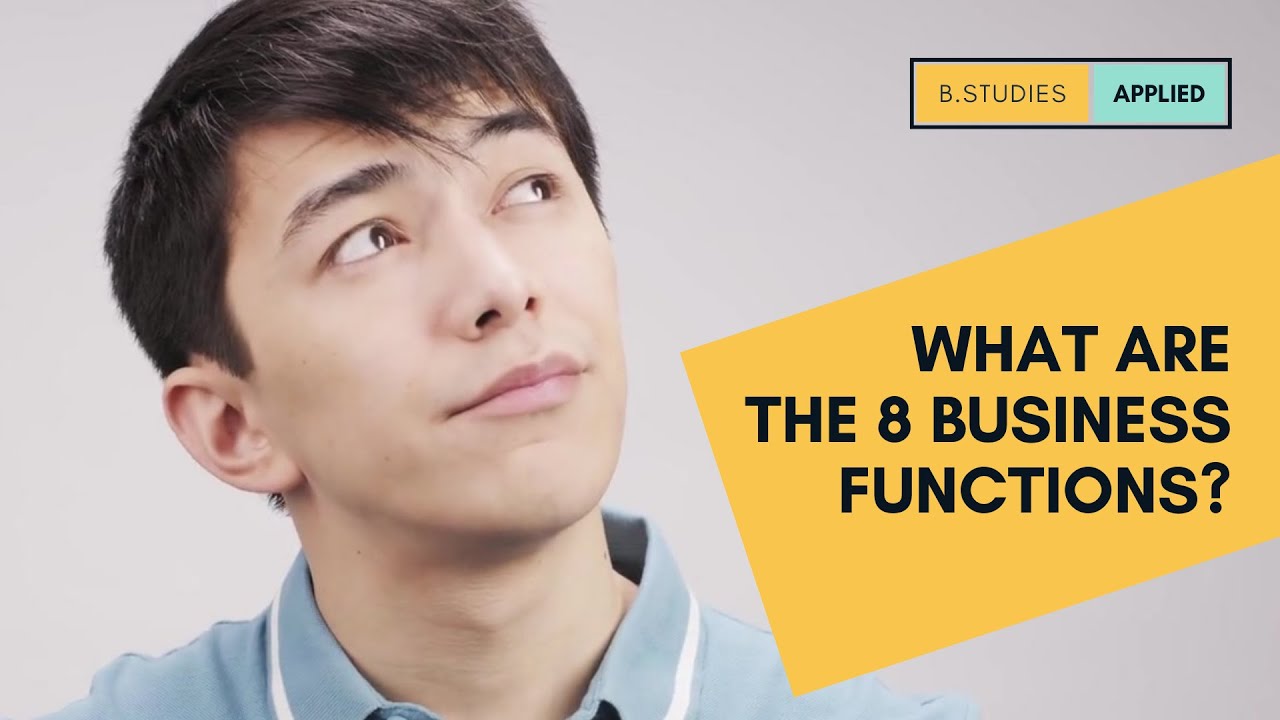
What Are The 8 Business Functions? A Simple Explanation | Introduction to Business Studies
5.0 / 5 (0 votes)