What Are The Common Types Of Metal Casting Process In Engineering and Industry?
Summary
TLDRThis video provides an in-depth overview of metal casting processes, detailing both expendable and non-expendable methods. It explores various techniques like sand casting, plaster mold casting, shell mold casting, and investment casting, highlighting their applications, advantages, and challenges. The video also covers non-expendable methods such as pressure die casting, gravity die casting, and centrifugal casting, which are used for mass production of complex components. With a focus on the history and evolution of metal casting, this video serves as a comprehensive guide to understanding the processes used in engineering and industry today.
Takeaways
- 😀 Metal casting is a process where molten metal is poured into a mold to form solidified parts of desired shapes.
- 😀 Metal casting has been used for thousands of years, initially for sculptures, weapons, and tools, with the first known cast object being a copper frog from 3200 BC.
- 😀 Metal casting processes are divided into two main groups: expendable mold casting and non-expendable (permanent) mold casting.
- 😀 Expendable mold casting involves single-use molds made from materials like sand, ceramics, and plaster, and is ideal for complex shapes.
- 😀 Types of expendable mold casting include permanent pattern (e.g., sand casting, plaster mold casting) and evaporative pattern (e.g., lost foam casting, investment casting).
- 😀 Sand casting is a widely-used process where a pattern is made and placed in a sand mold, with liquid metal poured to create parts.
- 😀 Plaster mold casting uses plaster of Paris as the mold material, offering good surface finishes and dimensional accuracy, typically used for non-ferrous metals.
- 😀 Shell mold casting uses resin-covered sand to form molds, allowing for high precision and small part production, but has higher costs.
- 😀 Lost foam casting, an evaporative pattern process, uses polystyrene foam to create molds and offers high precision and smooth surface finishes.
- 😀 Non-expendable mold casting uses reusable molds and is better for simpler designs, with types like pressure die casting, gravity die casting, and centrifugal casting.
Q & A
What is the definition of the metal casting process?
-Metal casting is the process in which molten metal is poured into a mold that contains a hollow cavity of a desired geometrical shape and allowed to cool down to form a solidified part.
What are the two major groups of metal casting processes?
-The two major groups of metal casting processes are expendable mold casting and non-expendable or permanent mold casting.
What is the main difference between expendable mold casting and permanent mold casting?
-Expendable mold casting uses single-use or temporary molds, while permanent mold casting uses reusable molds that can be used multiple times.
What are the two types of expendable mold casting?
-Expendable mold casting is divided into permanent pattern and evaporative pattern types.
What materials are commonly used for making molds in sand casting?
-Common materials for sand casting molds include sand, ceramics, and plaster, which are bound with binders to improve mold quality.
What are the main advantages and disadvantages of sand casting?
-Advantages of sand casting include low setup cost, cost-effectiveness, and the ability to create complex parts. Disadvantages include high porosity, poor surface finish, and low dimensional accuracy.
How does plaster mold casting differ from sand casting?
-Plaster mold casting uses plaster of Paris instead of sand to form molds. It is generally used for non-ferrous metals and results in a better surface finish compared to sand casting.
What is the key advantage of investment casting (lost wax casting)?
-The key advantage of investment casting is the ability to produce parts with extremely complex shapes and intricate features, with excellent dimensional accuracy and surface finish.
What are the disadvantages of pressure die casting?
-The disadvantages of pressure die casting include the need for complex and expensive equipment, a large capital investment, and the possibility of porosity in the cast due to air pockets.
What is the principle behind centrifugal casting?
-In centrifugal casting, molten metal is poured into a rotating mold, where centrifugal force helps to fill the mold and form a high-density casting, often used for making cylindrical parts.
Outlines
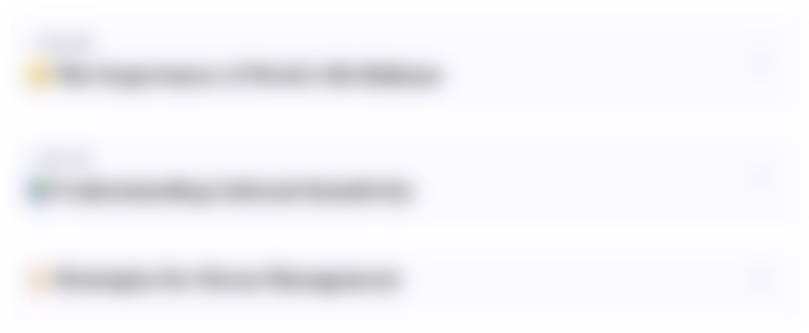
このセクションは有料ユーザー限定です。 アクセスするには、アップグレードをお願いします。
今すぐアップグレードMindmap
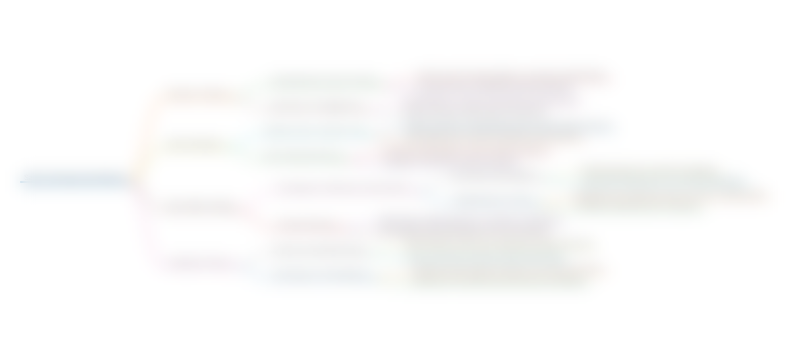
このセクションは有料ユーザー限定です。 アクセスするには、アップグレードをお願いします。
今すぐアップグレードKeywords
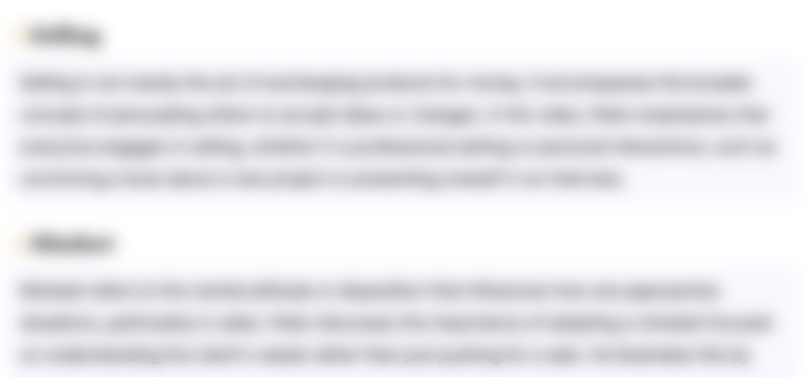
このセクションは有料ユーザー限定です。 アクセスするには、アップグレードをお願いします。
今すぐアップグレードHighlights
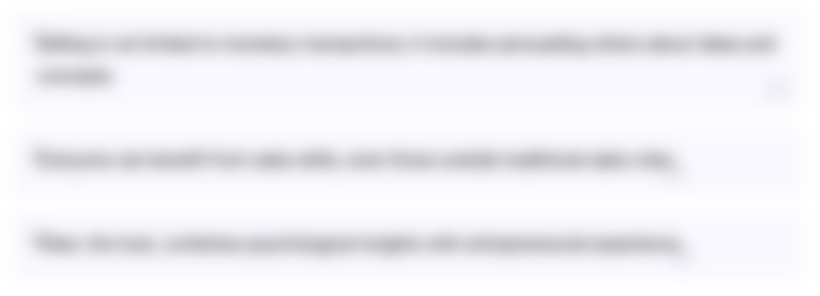
このセクションは有料ユーザー限定です。 アクセスするには、アップグレードをお願いします。
今すぐアップグレードTranscripts
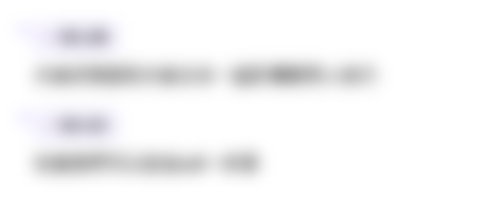
このセクションは有料ユーザー限定です。 アクセスするには、アップグレードをお願いします。
今すぐアップグレード関連動画をさらに表示

PENGECORAN LOGAM | Praktikum MK Teknologi Manufaktur

Dasar Pengecoran Logam Part 2 Cetakan Solidifikasi dan Penyusutan
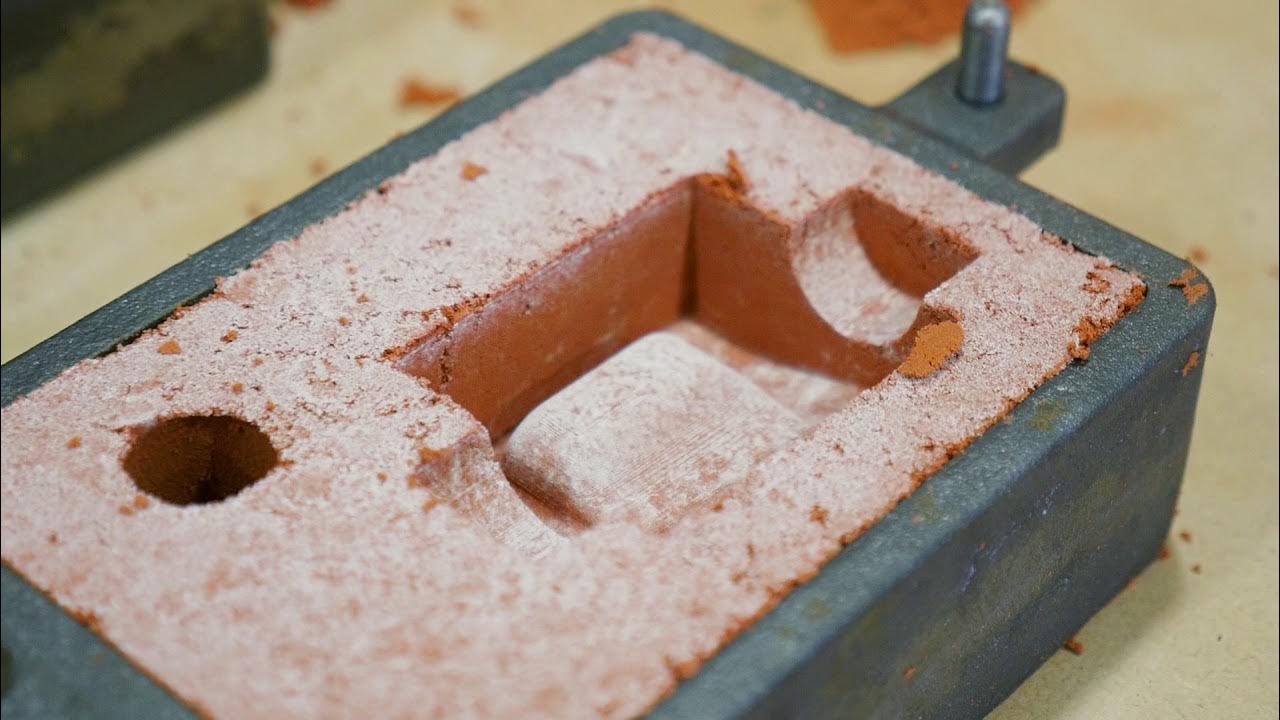
Casting Metal: showcasing the basics of casting and the Casting is the future Foundry Kit
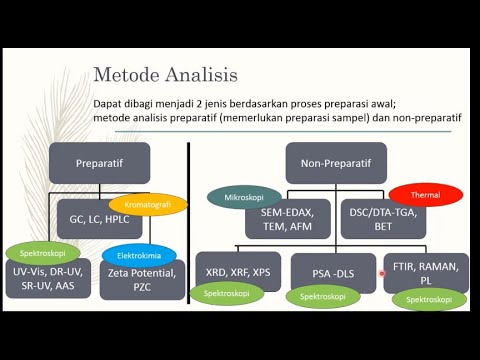
Karakterisasi Material

Proses Pengecoran
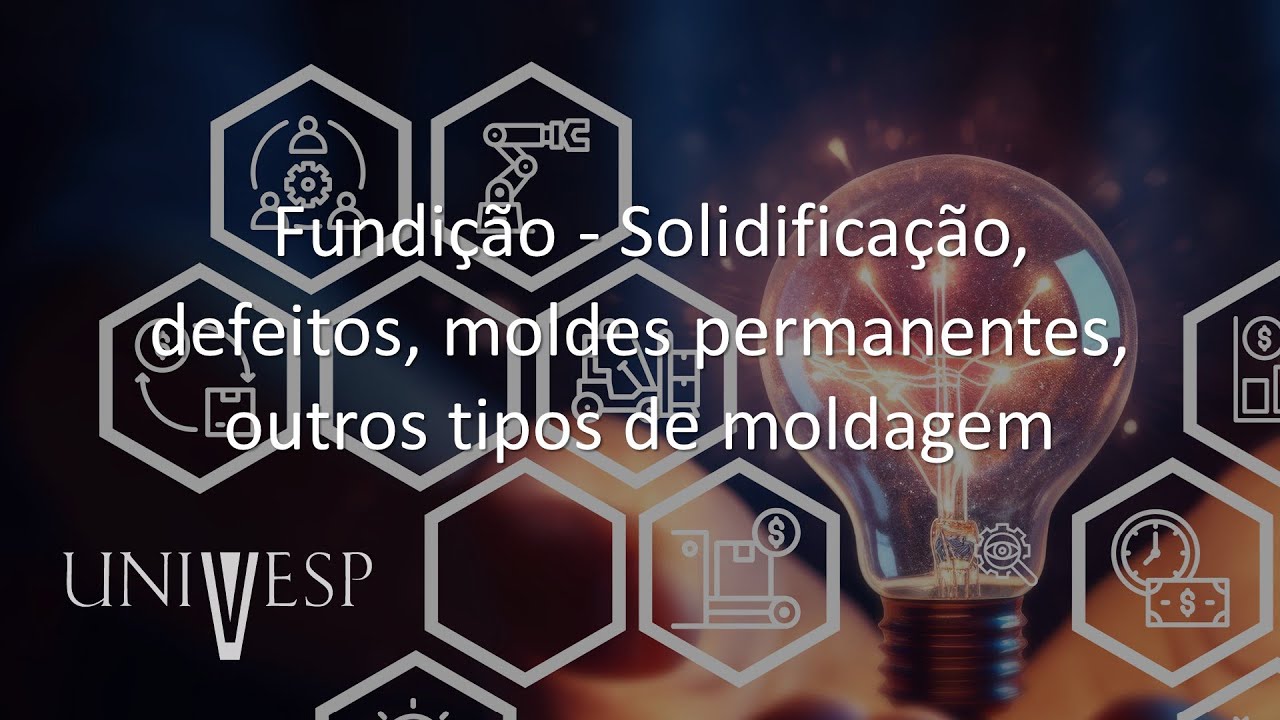
Materiais e Processos de Fabricação para Engenharia de Produção - Fundição - Solidificação, defeitos
5.0 / 5 (0 votes)