Dasar Pengecoran Logam Part 2 Cetakan Solidifikasi dan Penyusutan
Summary
TLDRThis video delves into the fundamentals of metal casting, covering the various mold types such as expendable and permanent molds, and the critical role of risers, patterns, and cores in the casting process. It explains the complex interactions between pouring speed, turbulence, and the solidification phases of metals, as well as how shrinkage during cooling must be accounted for in mold design. Key principles like Korinov's Rule for riser design and the use of chills for controlled cooling are also highlighted, providing insights into optimizing casting quality and minimizing defects in manufacturing.
Takeaways
- 😀 The metal casting process can be classified based on the type of mold used: expendable molds (e.g., sand or gypsum) and permanent molds (typically made from metal).
- 😀 Expendable molds are broken after the casting process, while permanent molds are designed for repeated use and typically consist of two parts (the cope and drag).
- 😀 Sand molds are commonly used because they are cheap, easy to shape, and have porosity, allowing gases to escape during the casting process.
- 😀 The mold must account for the thermal properties of the metal being poured, including the heat required to raise the metal to its melting point and maintain a pourable temperature.
- 😀 Riser systems are crucial in preventing shrinkage defects, as they act as reserves of molten metal to fill in areas that shrink during solidification.
- 😀 The speed of pouring the molten metal into the mold must be controlled to avoid both premature cooling (causing incomplete filling) and turbulence (leading to defects).
- 😀 Pouring temperature, superheating, and cooling rates need to be carefully managed to ensure proper metal flow and prevent defects like oxidation or air pockets.
- 😀 The solidification process involves both the cooling of the molten metal and its shrinkage, which can lead to defects if not accounted for in the mold design.
- 😀 In alloys, solidification occurs over a temperature range rather than at a single temperature, affecting how the metal shrinks and solidifies.
- 😀 The use of chills (external cooling devices) can help accelerate cooling in specific areas of the mold, ensuring uniform solidification and preventing defects in hard-to-fill regions.
- 😀 Riser design involves applying formulas like the Korinov rule to estimate the appropriate size based on the volume-to-surface-area ratio, ensuring that the metal solidifies properly.
Q & A
What is the difference between expendable molds and permanent molds in metal casting?
-Expendable molds are destroyed after the casting process, typically made from sand or gypsum. These are used for single or small-batch productions. Permanent molds, on the other hand, are designed to be reused multiple times, usually made of metal, and are used in mass production with automation systems.
Why is the riser important in the metal casting process?
-A riser is a reservoir that holds extra molten metal to compensate for shrinkage as the metal cools and solidifies. It ensures that the mold cavity is completely filled even as the metal contracts.
What role does temperature control play in the metal pouring process?
-Temperature control is crucial for ensuring the molten metal flows smoothly into the mold without prematurely solidifying. It involves managing the pouring temperature, the superheat (temperature difference between molten metal and its solidification point), and the cooling rate to prevent defects.
What is solidification and how does it affect the metal casting process?
-Solidification is the process where molten metal cools and transitions from liquid to solid. It results in shrinkage, which must be accounted for in mold design to prevent defects like voids. The cooling rate and the metal’s thermal properties directly influence how solidification occurs.
What is superheating, and why is it important in the casting process?
-Superheating refers to the temperature difference between the molten metal’s pouring temperature and the point at which it begins to solidify. Proper superheating ensures that the molten metal remains fluid enough to fully fill the mold before it starts solidifying.
How does pouring speed affect the quality of the cast?
-Pouring speed impacts the cooling rate and metal flow. Pouring too slowly can cause the metal to solidify prematurely, while pouring too quickly can create turbulence, leading to defects like erosion, trapped gases, and metal oxidation.
What is the purpose of using chills in metal casting?
-Chills are heat-absorbing materials placed in the mold to speed up the cooling in specific areas that are difficult to solidify. This ensures more uniform cooling and prevents defects such as incomplete filling or areas of excessive shrinkage.
How does the use of sand in expendable molds benefit the casting process?
-Sand is used in expendable molds because it is inexpensive, easy to manipulate, and has good porosity, allowing gases to escape during the casting process. This reduces the risk of defects such as gas pockets and porosity in the final cast.
What is the significance of mold porosity in casting?
-Mold porosity refers to the presence of tiny pores in the mold material, which allows gases to escape as the molten metal is poured. This is important to avoid defects like gas porosity in the cast product, as trapped gases can weaken the final structure.
What is the role of a pattern in the creation of a mold for casting?
-The pattern is the original shape or model used to form the mold cavity. It can be made from materials such as wood, plastic, or metal. The pattern defines the external shape of the final casting, and its design must consider factors like shrinkage and cooling behavior.
Outlines
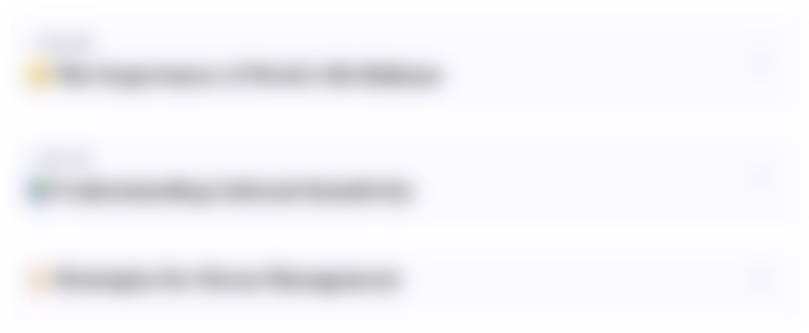
This section is available to paid users only. Please upgrade to access this part.
Upgrade NowMindmap
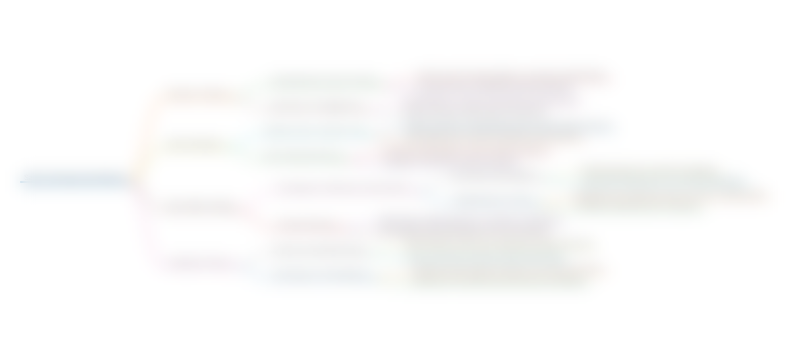
This section is available to paid users only. Please upgrade to access this part.
Upgrade NowKeywords
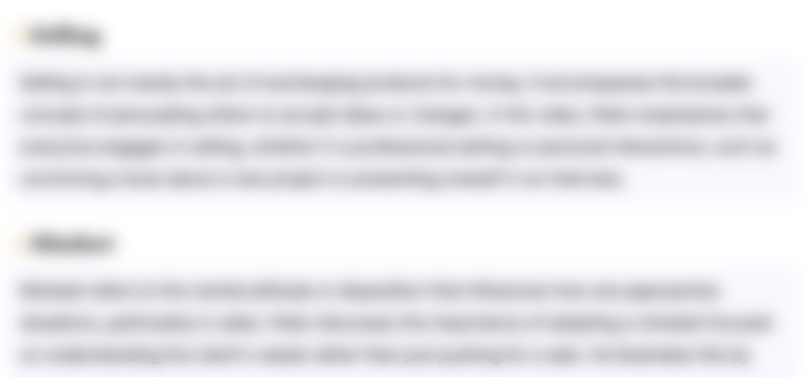
This section is available to paid users only. Please upgrade to access this part.
Upgrade NowHighlights
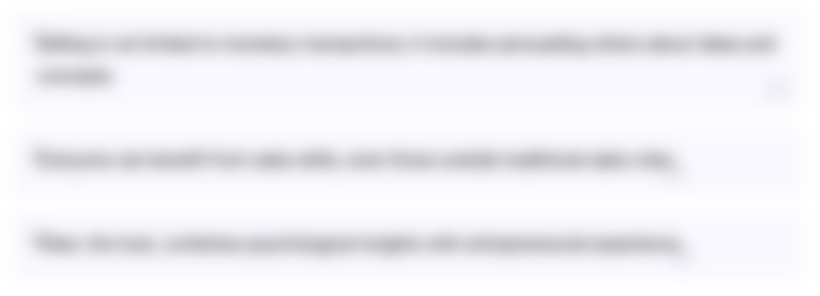
This section is available to paid users only. Please upgrade to access this part.
Upgrade NowTranscripts
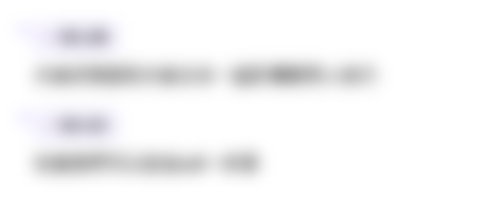
This section is available to paid users only. Please upgrade to access this part.
Upgrade NowBrowse More Related Video

PENGECORAN LOGAM | Praktikum MK Teknologi Manufaktur

What Are The Common Types Of Metal Casting Process In Engineering and Industry?

Proses Pengecoran

Sand Casting
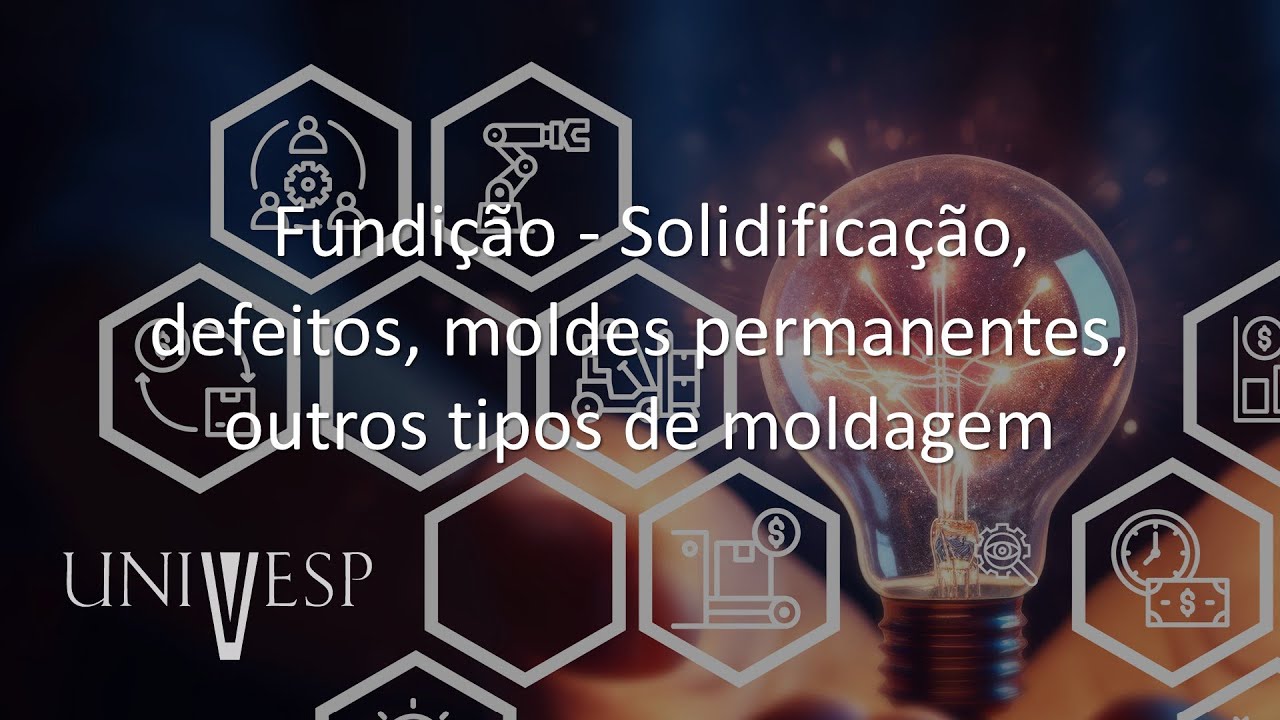
Materiais e Processos de Fabricação para Engenharia de Produção - Fundição - Solidificação, defeitos

What Is Casting? 11 Types of Casting Processes Explanation
5.0 / 5 (0 votes)