Pump and Cargo Handling System
Summary
TLDRThis script offers an in-depth look at the design and function of the aphromoo deep-well pump, highlighting its role in efficient cargo handling systems. It details the hydraulic systems by Frank Moon AAS, explaining the one pump per tank submerged cargo pumping system, which ensures safe and profitable operations with capacities ranging from 50 to 2000 cubic meters per hour. The script also covers the hydraulic system's open and closed-loop configurations, emphasizing the importance of clean hydraulic fluid for system efficiency and maintenance.
Takeaways
- 🚀 The script discusses the design and function of aphromoo deep-well pumps, focusing on the hydraulic systems developed by Frank Moon AAS for liquid cargo handling.
- 🛠 The one pump per tank submerged cargo pumping system was developed in cooperation with major chemical tanker operators, ensuring safe and profitable cargo handling with efficient stripping and cleaning.
- 🔢 Pump capacities vary from 50 to 2000 cubic meters per hour, with total discharge rates up to 15,000 cubic meters per hour, installed on various types of carriers including FPSOs and OBOS.
- 🔄 The working principle of a centrifugal pump is explained, where the rotation of the impeller causes liquid to flow towards the periphery due to centrifugal force.
- 🛡️ The cargo pump is supported by a deck trunk and includes a capacity control valve for remote and local operation, which regulates hydraulic pressure and oil flow to the motor.
- 📈 The hydraulic system can be built as a central hydraulic main ring line system, either in a closed or open loop, with considerations for oil flow and pressure control.
- 🌡️ The importance of maintaining the hydraulic oil within a recommended temperature range (30-55 degrees Celsius) and water content (up to 0.03 percent) is highlighted for optimal performance.
- 💧 The script emphasizes the need for clean hydraulic fluid to prevent reduced efficiency, excessive downtime, and increased maintenance costs.
- 🛑 Emergency stop procedures are outlined for critical situations such as damage to hydraulic pressure pipes or hoses, uncontrolled spillage, or leakage during discharging.
- 🔄 Post-operation procedures include reducing hydraulic system pressure, stopping main Power Packs, and ensuring one feed or jockey pump remains running to maintain overpressure in the system.
- ⚙️ The script provides detailed instructions for starting and stopping the hydraulic system, including checks on oil levels, cooling systems, and pressure settings.
Q & A
What is the purpose of the aphromoo deep-well pump?
-The aphromoo deep-well pump is designed for the handling of liquid cargoes, ensuring safe and profitable cargo handling, efficient stripping, and tank cleaning.
Who developed the one pump per tank submerged cargo pumping system?
-The one pump per tank submerged cargo pumping system was developed by Frank Moon AAS in cooperation with major chemical tanker operators.
What is the range of individual pump capacity in the Fram-o system?
-Individual pump capacity in the Fram-o system varies between 50 and 2000 cubic meters per hour.
What types of vessels are the pumps installed on?
-Pumps are installed on chemical carriers, product tankers, crude oil carriers, FPSOs, and OBO carriers.
How does the working principle of a centrifugal pump work?
-The working principle of a centrifugal pump involves the rotation of the impeller, which causes the liquid to flow towards the periphery due to the centrifugal force, evacuating the center and allowing liquid from the suction line to fill the void.
What is the function of the deck trunk in the pump system?
-The deck trunk supports the cargo pump and is welded to the deck, with all connections on the top cover plate for easy access and operation.
What is the role of the capacity control valve in the hydraulic system?
-The capacity control valve regulates hydraulic pressure and oil flow to the motor according to the given discharge situation, allowing for remote and local operation of the cargo pump.
What is the purpose of the cofferdam in the hydraulic section?
-The cofferdam completely segregates the hydraulic oil from the cargo, preventing any contamination and ensuring safe operation.
What are the two types of hydraulic systems mentioned in the script?
-The two types of hydraulic systems mentioned are the open-loop system and the closed-loop system.
What is the recommended maximum water content in hydraulic oil?
-The maximum recommended water content in hydraulic oil is 500 parts per million or 0.05 percent.
What should be checked before starting the main power packs in the hydraulic system?
-Before starting the main power packs, one should check the hydraulic system tank oil level, ensure the cooling pump for hydraulic oil is running, verify the cooling fan for Power Packs is operating, confirm the necessary number of generators are running, adjust the potentiometer for system pressure to minimum, set the speed control valves for all consumers to minimum, and ensure the cargo pump cofferdams are purged.
Outlines
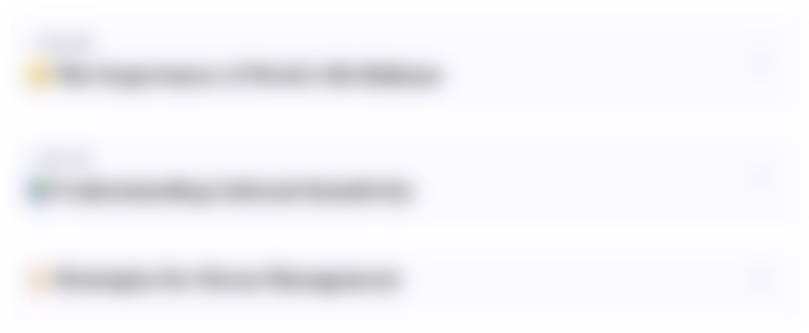
Cette section est réservée aux utilisateurs payants. Améliorez votre compte pour accéder à cette section.
Améliorer maintenantMindmap
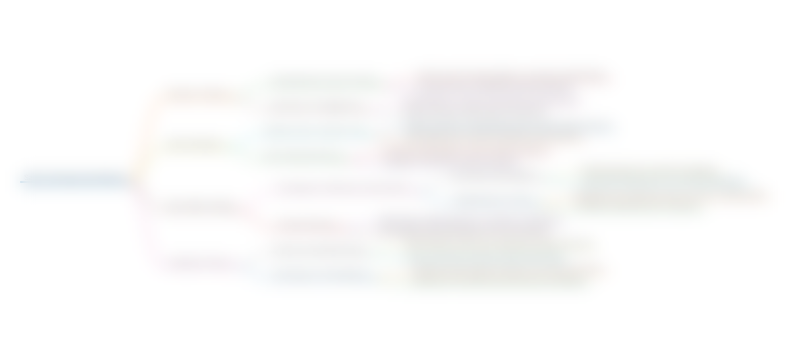
Cette section est réservée aux utilisateurs payants. Améliorez votre compte pour accéder à cette section.
Améliorer maintenantKeywords
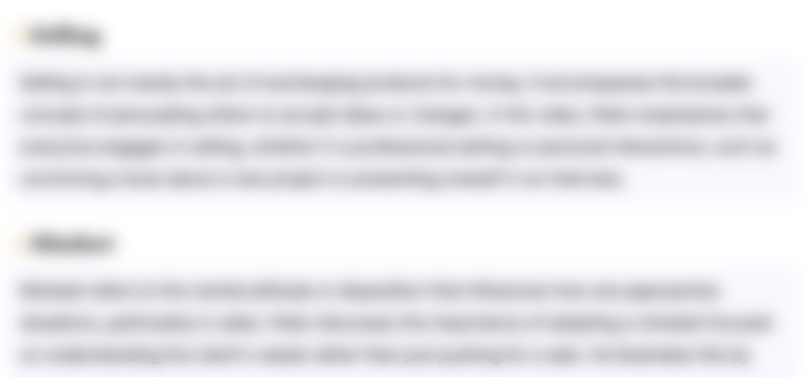
Cette section est réservée aux utilisateurs payants. Améliorez votre compte pour accéder à cette section.
Améliorer maintenantHighlights
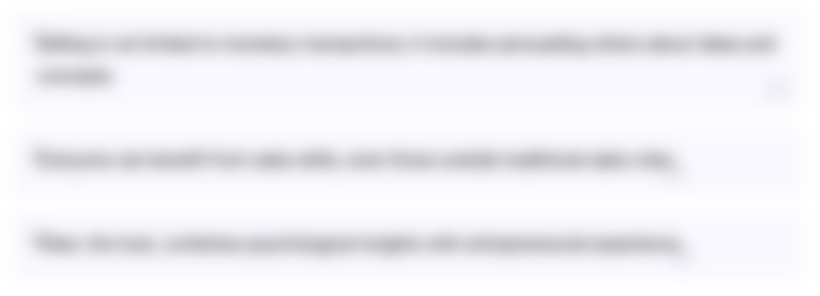
Cette section est réservée aux utilisateurs payants. Améliorez votre compte pour accéder à cette section.
Améliorer maintenantTranscripts
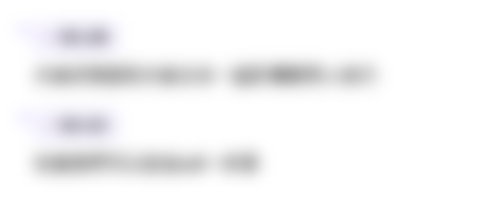
Cette section est réservée aux utilisateurs payants. Améliorez votre compte pour accéder à cette section.
Améliorer maintenantVoir Plus de Vidéos Connexes

Gas tanker basics part 2 reliq plant, heater n dcp
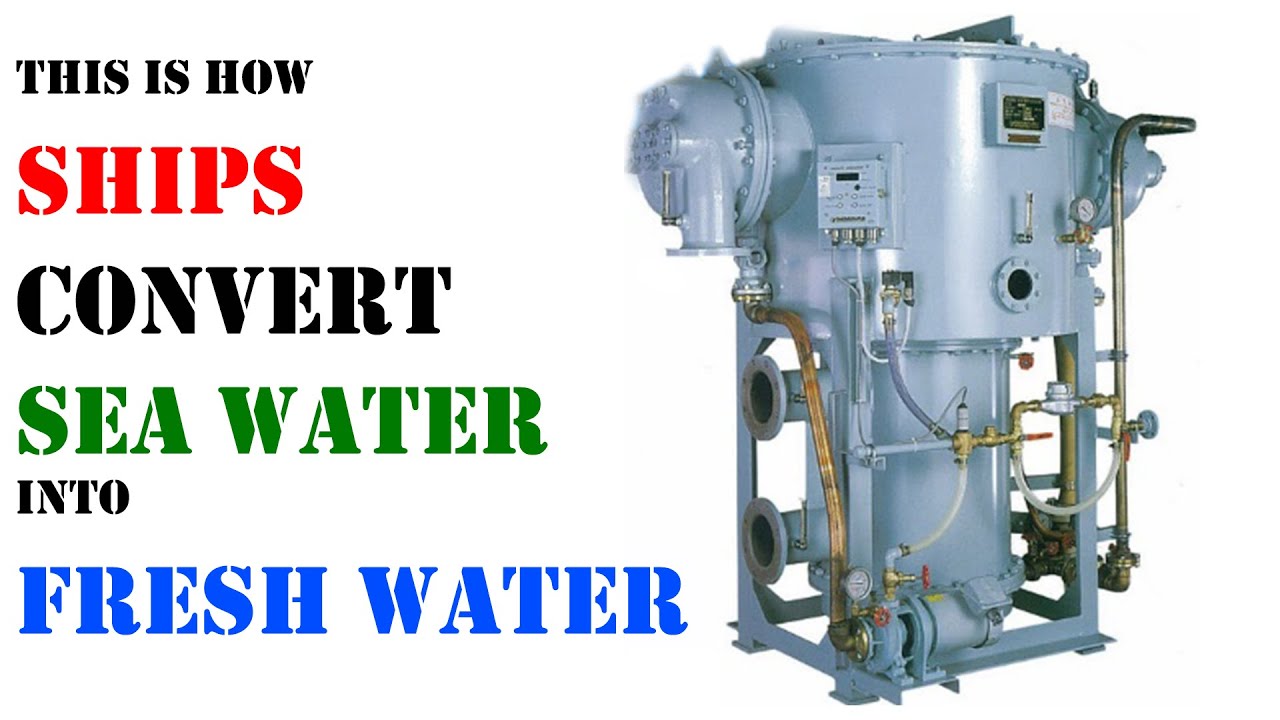
Ship's Fresh Water Generator (Distillation Plant) | Starting and Stopping Procedures | Chief MAKOi
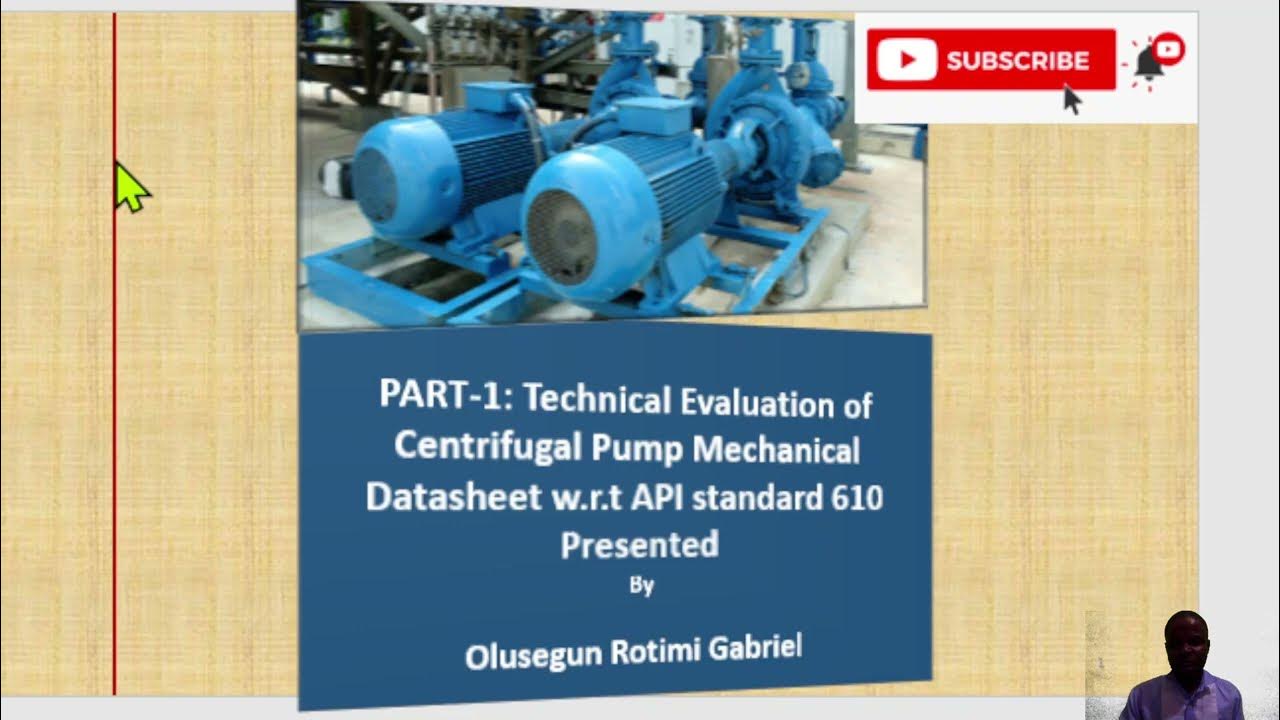
PART-1: Technical Evaluation of Centrifugal Pump Mechanical Datasheet with respect to API 610
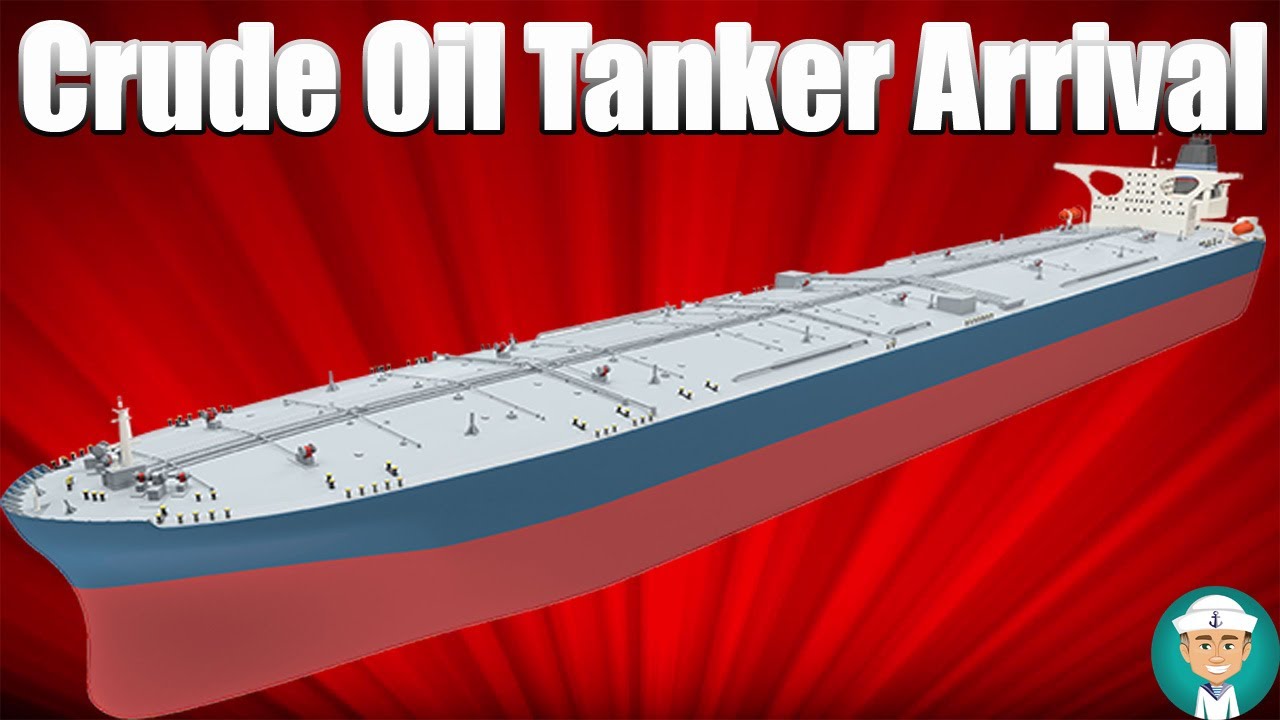
Procedures When a Crude Oil Tanker Arrives at Port
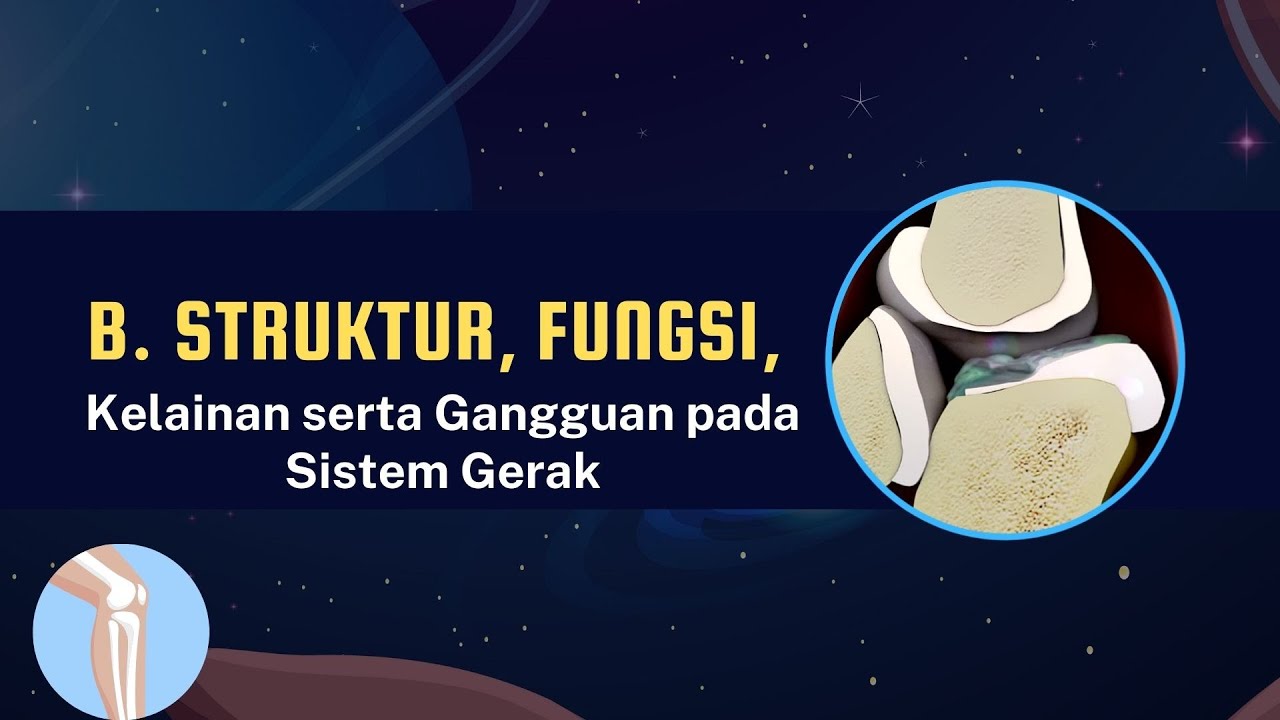
B Struktur, Fungsi, dan Kelainan serta Gangguan pada Sistem Gerak
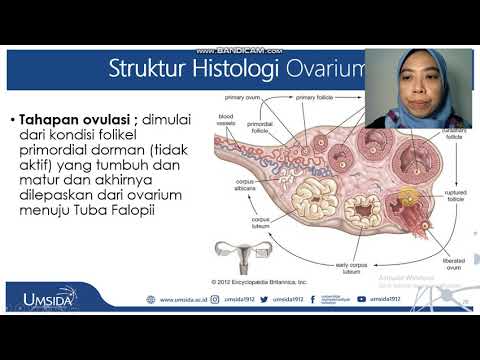
VIDEO SERI #2 ; GENETALIA INTERNA OVARIUM
5.0 / 5 (0 votes)