Making ammonia
Summary
TLDRThe script details the global production of ammonia, approximately 140 million tons annually, highlighting its diverse applications in explosives, medicines, and fertilizers. The manufacturing process involves reacting natural gas, primarily methane, with steam to produce hydrogen, followed by secondary reactions with air to form ammonia. The process includes desulfurization, carbon dioxide removal for alternative uses, and the use of catalysts under high pressure and temperature. Ammonia is either stored or directly utilized by nearby chemical plants, emphasizing the interconnectedness of industrial operations.
Takeaways
- 🌍 Global Ammonia Production: About 140 million tons of ammonia is produced worldwide each year.
- 💥 Uses of Ammonia: It is utilized in the manufacturing of explosives, die making, medicine preparation, and fertilizer production.
- 🔁 Production Process: Ammonia is made by reacting natural gas, primarily methane, with steam to form hydrogen, followed by further reactions with air.
- 🌐 Gas Stream Treatment: Carbon dioxide is removed from the gas stream by dissolving it in alkali, and the remaining hydrogen and nitrogen are combined to produce ammonia.
- ♻️ Recycling Uncombined Gases: Uncombined gases are recycled back to the converter for further processing.
- 📍 Plant Location: The plant is situated near other chemical plants for convenient use of the produced ammonia.
- 🌊 Natural Gas Source: Natural gas, which is about 90% methane, is sourced from the North Sea and fed to the plant through a pipeline.
- 💨 Raw Materials: The main raw materials for ammonia production are water, air, and natural gas, with air being filtered and compressed.
- 🚫 Desulfurization: Natural gas contains sulfur compounds that are removed to prevent catalyst poisoning in the desulfurizer.
- 🔥 Reformer Reaction: Methane and steam react in the presence of a nickel-based catalyst to produce carbon monoxide and hydrogen, with further reactions forming carbon dioxide and more hydrogen.
- 🔬 Secondary Reformer: Heated air is added to convert any remaining methane into carbon dioxide, which is then removed to prevent catalyst poisoning.
- 🌡️ Converter Conditions: The ammonia converter operates at high pressure and temperature to convert nitrogen and hydrogen into ammonia using an iron-based catalyst.
- 🔄 Gas Stream Recycling: The gas stream containing ammonia, hydrogen, and nitrogen is cooled and compressed, with ammonia condensing out as a liquid and the remaining gases recycled.
- 🚀 Transportation: Ammonia can be transported as a liquid under pressure in tankers or piped directly to nearby plants.
Q & A
How much ammonia is produced worldwide annually?
-Approximately 140 million tons of ammonia is produced per year worldwide.
What are some of the main uses of ammonia?
-Ammonia is used in the manufacturing of explosives, in the die-making industry, in preparing medicines, and in the production of fertilizers.
What is the primary raw material used to make ammonia?
-The primary raw material used to make ammonia is natural gas, which is mainly methane (CH4).
How is hydrogen produced in the ammonia production process?
-Hydrogen is produced by reacting natural gas with steam in the primary reformer.
What happens in the secondary reformer during ammonia production?
-In the secondary reformer, air is added to the gas stream, and any remaining methane is converted into carbon dioxide.
Why is carbon dioxide removed from the gas stream in ammonia production?
-Carbon dioxide is removed because it would poison the catalyst used for the conversion of nitrogen and hydrogen to ammonia.
What is the role of alkali in the ammonia production process?
-Alkali is used to dissolve and remove carbon dioxide from the gas stream in the converter.
What is the ratio of nitrogen to hydrogen in the gas stream fed to the ammonia converter?
-The ratio of nitrogen to hydrogen in the gas stream fed to the ammonia converter is 3:1.
What is the operating pressure and temperature of the ammonia converter?
-The ammonia converter operates at a pressure of 200 atmospheres and a temperature of about 400° C.
How is the produced ammonia separated from the gas stream?
-The hot gas stream containing ammonia, hydrogen, and nitrogen is cooled to about -1° C and compressed, causing ammonia to condense out as a liquid.
What happens to the uncombined gases after ammonia production?
-The uncombined gases are recycled back to the converter along with a fresh gas mixture.
How is the sulfur content in natural gas treated before it is used in ammonia production?
-The sulfur compounds in natural gas are removed in a desulfurizer before the gas is piped to the primary reformer.
What is the final form of ammonia for transportation or use?
-Ammonia can be transported in tankers as a liquid under pressure or piped directly to nearby plants for use.
Outlines
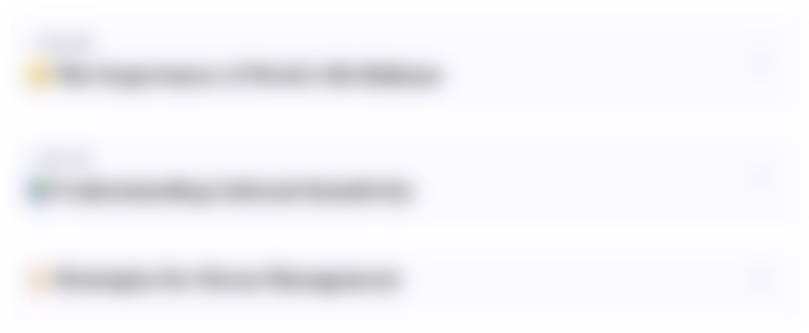
Cette section est réservée aux utilisateurs payants. Améliorez votre compte pour accéder à cette section.
Améliorer maintenantMindmap
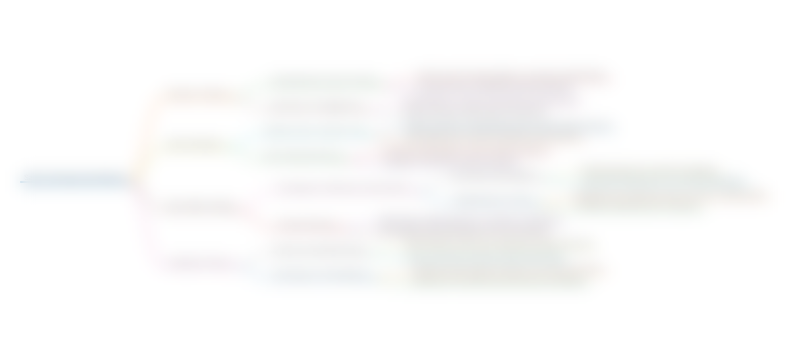
Cette section est réservée aux utilisateurs payants. Améliorez votre compte pour accéder à cette section.
Améliorer maintenantKeywords
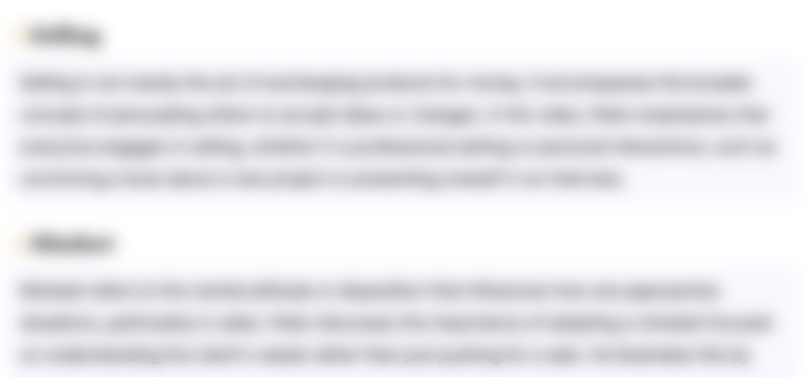
Cette section est réservée aux utilisateurs payants. Améliorez votre compte pour accéder à cette section.
Améliorer maintenantHighlights
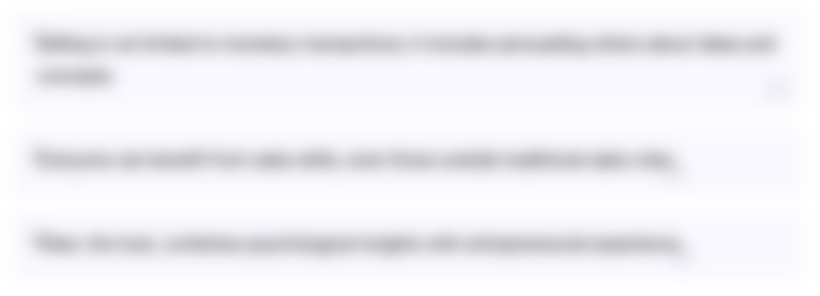
Cette section est réservée aux utilisateurs payants. Améliorez votre compte pour accéder à cette section.
Améliorer maintenantTranscripts
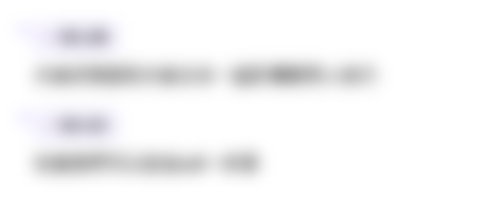
Cette section est réservée aux utilisateurs payants. Améliorez votre compte pour accéder à cette section.
Améliorer maintenant5.0 / 5 (0 votes)