Managing Your Assets 04 - The Future is Here
Summary
TLDRThis video explores the future of manufacturing, focusing on how technology, data, and equipment upgrades can enhance production efficiency and minimize downtime. It highlights the importance of planning for discontinued parts, migrating from legacy equipment, and integrating smart devices that predict failures. The use of data analytics for informed decision-making and proactive maintenance is emphasized, along with the importance of cybersecurity in an increasingly connected environment. The video also covers migration strategies, including leveraging expert tools and case studies to demonstrate successful upgrades and the potential risks of downtime in large-scale operations.
Takeaways
- 😀 The future of manufacturing will rely heavily on data, helping to predict failures and minimize downtime.
- 😀 Predictive maintenance will be key, with devices warning in advance of potential failures to avoid unplanned downtime events.
- 😀 Outdated or discontinued equipment poses a significant challenge, especially in terms of sourcing parts for long-term planning.
- 😀 A five-year or ten-year plan must consider the availability and reliability of parts, particularly those that are no longer in production.
- 😀 Modern manufacturing devices are becoming smarter, generating data that allows for more efficient analysis and decision-making.
- 😀 Migrating from legacy systems like PLC 5 to newer, more advanced equipment is crucial for maintaining operational efficiency and security.
- 😀 Data collection tools are necessary for real-time decision-making and optimization across all facets of manufacturing, including the supply chain.
- 😀 Automation teams and specialists are vital for planning migrations and identifying the best solutions for system upgrades.
- 😀 Security is becoming a more critical concern as manufacturing plants face an increasing number of cyber threats.
- 😀 Tools like Rockwell's Integrated Architecture Builder assist with hardware migration and system upgrades, making the process more streamlined and cost-effective.
- 😀 Large-scale migrations, though risky and costly, can be planned with fixed costs and long-term strategies to minimize downtime, as shown in real-world case studies.
Q & A
What is the primary focus when planning for future technological changes in a manufacturing facility?
-The primary focus is ensuring that current equipment can handle the technological advancements expected in the future. This includes assessing the availability of components and the feasibility of maintaining or upgrading legacy systems.
Why is the availability of discontinued equipment a concern for long-term planning?
-Discontinued equipment is a concern because parts for these systems may become increasingly difficult to obtain over time. Planning with discontinued products could lead to more difficulty in maintaining operations, especially in the next five to ten years.
How can data analytics help in avoiding downtime in a manufacturing facility?
-Data analytics can help by collecting information from devices to predict failures before they occur. This allows maintenance teams to schedule repairs proactively, avoiding unexpected downtimes and ensuring production continues smoothly.
What role do smart devices play in preventing downtime?
-Smart devices can monitor their own health and alert operators when they are about to fail. This predictive capability allows for the scheduling of maintenance or repair work before a failure happens, minimizing downtime.
How can the migration from legacy systems (e.g., PLC-5) to newer technologies help prevent production losses?
-Migrating from legacy systems to newer technologies with better diagnostics, data collection, and predictive maintenance capabilities can help prevent production losses by addressing potential issues before they cause failures. This enables smarter, more efficient operations.
What are some challenges when dealing with legacy systems in manufacturing?
-Challenges with legacy systems include difficulty obtaining replacement parts, lack of support for modern data collection, and the inability to predict failures in advance, leading to unexpected downtimes and production inefficiencies.
What is the role of the installed base evaluation in migration planning?
-The installed base evaluation helps by providing a detailed inventory of the existing equipment, allowing manufacturers to assess the condition of their assets, identify outdated or unsupported components, and make informed decisions about required upgrades.
What does a migration plan typically include in the context of upgrading manufacturing equipment?
-A migration plan includes an assessment of current equipment, a comparison against future requirements (such as Ethernet compatibility), and recommendations for upgrades. It also prioritizes actions based on the criticality of equipment and the potential impact of downtime.
How does the Integrated Architecture Builder assist in the migration process?
-The Integrated Architecture Builder assists by offering a tool to automatically recommend replacements for outdated components. It helps users generate bills of materials and provides budgetary pricing to plan a migration without needing to rewire the entire system.
Why is cybersecurity an important consideration when migrating manufacturing systems?
-Cybersecurity is crucial because manufacturing plants are increasingly targeted by cyber threats. Ensuring that new systems meet security standards is necessary to protect critical data and prevent vulnerabilities during the migration process.
Outlines
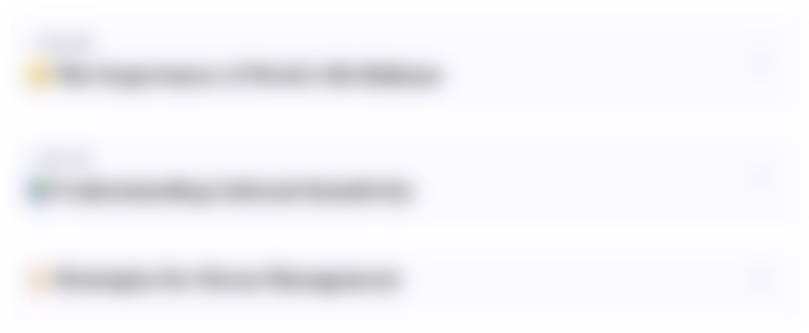
Cette section est réservée aux utilisateurs payants. Améliorez votre compte pour accéder à cette section.
Améliorer maintenantMindmap
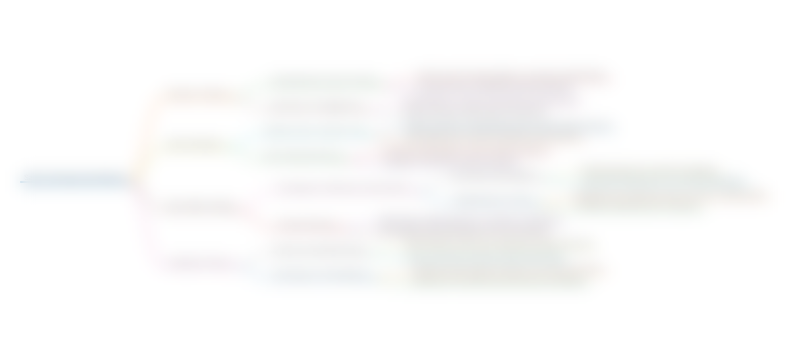
Cette section est réservée aux utilisateurs payants. Améliorez votre compte pour accéder à cette section.
Améliorer maintenantKeywords
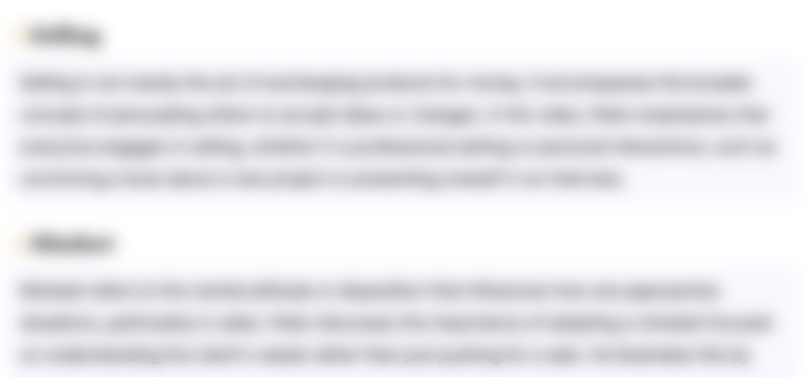
Cette section est réservée aux utilisateurs payants. Améliorez votre compte pour accéder à cette section.
Améliorer maintenantHighlights
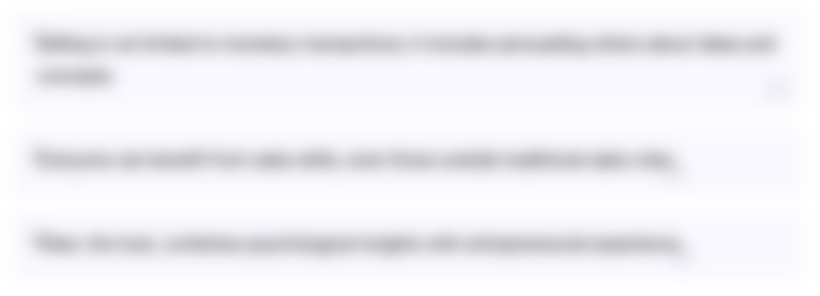
Cette section est réservée aux utilisateurs payants. Améliorez votre compte pour accéder à cette section.
Améliorer maintenantTranscripts
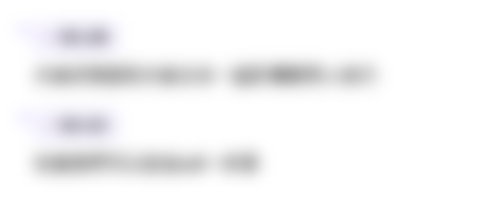
Cette section est réservée aux utilisateurs payants. Améliorez votre compte pour accéder à cette section.
Améliorer maintenantVoir Plus de Vidéos Connexes
5.0 / 5 (0 votes)