How To Crash Test A $2 Million Koenigsegg Hypercar - www.APEX.one
Summary
TLDRChristoph von Koenigsegg, founder of Koenigsegg, shares the painstaking process of crash testing hypercars. He explains the rigorous US standards requiring tests without seatbelts and smart airbag systems that adapt to the passenger's size and position. Koenigsegg's innovative approach involves designing a carbon-fiber monocoque that can endure multiple crashes, reducing costs and resources. The company uses a supercomputer for crash simulations to ensure safety and accuracy, reflecting their commitment to building safe yet thrilling hypercars.
Takeaways
- đ Christoph von Koenigsegg has dedicated half his life to leading the hypercar industry with Swedish design and visionary technical solutions.
- đ„ The process of crash testing is emotionally challenging for the team as they witness the destruction of their cars.
- đ§ In the US, cars must be crash tested without seat belts and equipped with smart airbags that adjust deployment based on various parameters.
- đšâđ§ Koenigsegg designs its carbon-fiber monocoque to withstand multiple crash tests, reducing the need for multiple chassis and saving costs.
- đĄ The company uses a supercomputer to simulate crashes of carbon-fiber structures, which helps in reducing risks and improving the accuracy of physical tests.
- đ Specialists at Koenigsegg are dedicated to developing and refining the crash simulation programs for carbon-fiber cars.
- đ Physical test results are correlated back to simulations to ensure accuracy and continuous improvement of the crash test process.
- đ Koenigsegg builds the cars in Angelholm and sends them to their facilities in Barcelona for testing, incurring logistical costs and time.
- đ„ The team is present during the tests in Barcelona but cannot intervene in the preparation or execution of the crash tests.
- đ The process of crash testing is both a critical safety verification and a stressful experience due to the destruction of the cars.
Q & A
What is Christoph von Koenigsegg's goal in the hypercar industry?
-Christoph von Koenigsegg's goal is to be a leader in the hypercar industry by utilizing Swedish design combined with visionary technical solutions.
What is the emotional impact on Koenigsegg when preparing a car for crash tests?
-Preparing a car for crash tests is emotionally challenging for Koenigsegg, as it is painful to watch the car being slowly destroyed.
What are the requirements for crash testing cars in the US?
-In the US, cars must undergo crash tests without belts and be equipped with smart airbags that can sense the size of the person, their position, whether they are wearing a belt, and the angle of impact to adjust the deployment accordingly.
How does Koenigsegg save money during the crash testing process?
-Koenigsegg saves money by designing their carbon-fiber monocoque to withstand various crash tests without being destroyed, allowing the same monocoque chassis to be used for all tests.
What is the annual production of Koenigsegg compared to regular manufacturers?
-Regular manufacturers can produce 16 cars without issue, but for Koenigsegg, 16 cars is almost their entire annual production.
Why is it more cost-effective for Koenigsegg to rebuild and repair the same car for multiple crash tests?
-It is more cost-effective because the integral and most expensive part of the car, the monocoque chassis, does not need to be replaced after each test, only the bodywork and crash members.
What special equipment did Koenigsegg purchase to simulate crash tests?
-Koenigsegg purchased a supercomputer to simulate crashes of carbon-fiber structures, which is unusual in the industry.
How does the supercomputer help in reducing the risk during actual crash tests?
-The supercomputer allows for crash simulation of carbon-fiber cars, enabling Koenigsegg to know the results before actual physical tests, which helps correlate back to the simulation and increase the accuracy of subsequent tests.
What is the logistical process for Koenigsegg when sending a car for crash tests?
-Koenigsegg builds the car at their facility, then sends it to their test facilities in Barcelona, where the tests are conducted by the test facility with Koenigsegg's assistance.
What limitations does Koenigsegg face during the crash tests at the test facility?
-Koenigsegg can be present during the tests but cannot be inside the car during the crash or prepare the car for the crash test. They provide information on sensor placement and assist with the preparation process.
How does the crash testing process affect Koenigsegg's perception of their cars?
-The process is both exciting and painful for Koenigsegg, as they are committed to making their cars safe, but it is also difficult to see their creations being destroyed in the crash tests.
What is the significance of the crash testing process for Koenigsegg's supercars?
-The crash testing process is crucial for verifying the safety of Koenigsegg's supercars and ensuring that the smart airbag systems function correctly under various crash scenarios.
Outlines
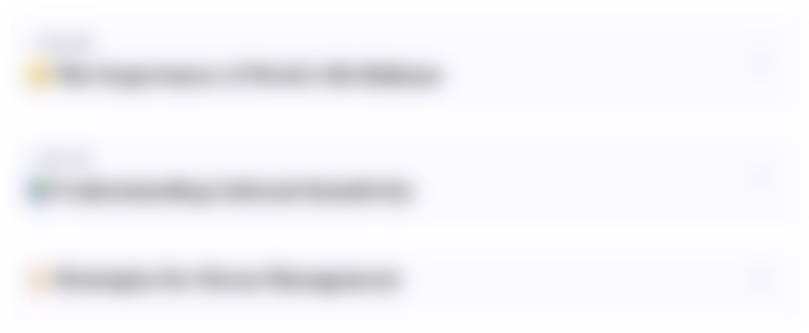
Cette section est réservée aux utilisateurs payants. Améliorez votre compte pour accéder à cette section.
Améliorer maintenantMindmap
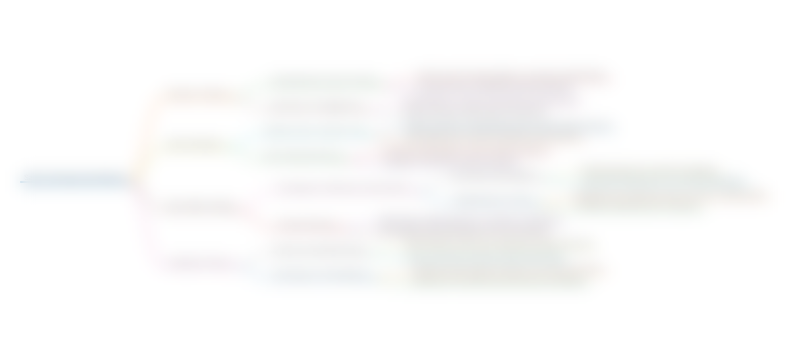
Cette section est réservée aux utilisateurs payants. Améliorez votre compte pour accéder à cette section.
Améliorer maintenantKeywords
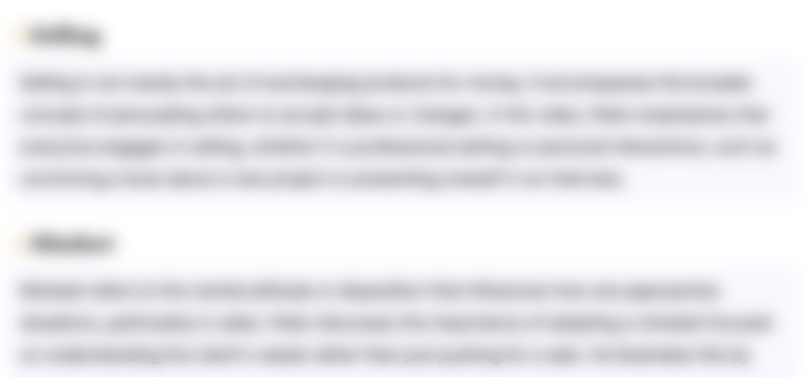
Cette section est réservée aux utilisateurs payants. Améliorez votre compte pour accéder à cette section.
Améliorer maintenantHighlights
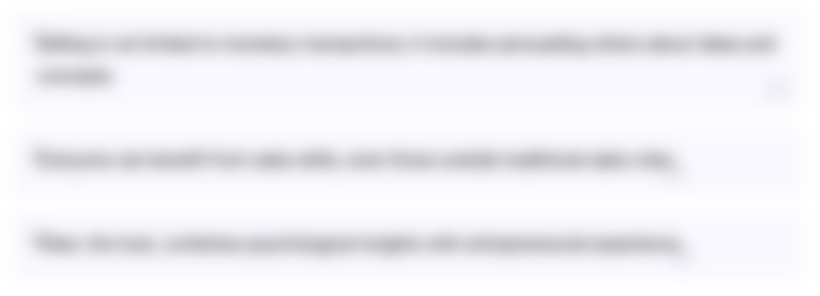
Cette section est réservée aux utilisateurs payants. Améliorez votre compte pour accéder à cette section.
Améliorer maintenantTranscripts
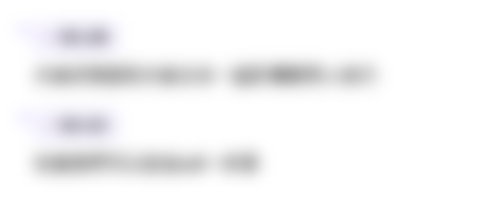
Cette section est réservée aux utilisateurs payants. Améliorez votre compte pour accéder à cette section.
Améliorer maintenant5.0 / 5 (0 votes)