Inside Micron Taiwan’s Semiconductor Factory | Taiwan’s Mega Factories EP1
Summary
TLDR这段视频脚本介绍了位于台湾的世界最清洁的半导体工厂,它位于人类成就的前沿,是技术与未来的交汇点。工厂不断在创新,因为不创新就无法在这个行业生存。工厂使用硅材料,将数十亿的电路和晶体管堆叠在一起,并且目标是在不断缩小的芯片上增加更多晶体管。台湾在芯片制造方面表现突出,拥有丰富的经验和地理位置优势,在全球代工服务市场中占有近70%的份额,在先进制造工艺中占有90%以上,在组装和测试方面也处于全球领先地位。Micron Technology是台湾最大的半导体制造商之一,其在台湾的工厂规模巨大,生产过程从研发到销售都在工厂内完成。工厂的自动化程度高,操作人员的角色已从体力劳动转变为基于知识和决策的角色。工厂在环保方面也做出了努力,如安装了世界上第一个化学浓缩系统,回收利用废弃的异丙醇,并且通过智能处理系统回收了近80%的水资源。此外,工厂还采用了绿色墙面和可再生能源,以减少对环境的影响。整个生产过程体现了艺术与科学的精妙结合,是人类文明快速发展的重要推动力。
Takeaways
- 🏭 这家工厂可能是世界上清洁度最高的工厂,代表着人类成就的前沿,技术与未来的交汇点。
- 🚀 工厂不断在发展,创新是生存的关键,否则就会落后于行业。
- 🔬 硅是制造微芯片的基础材料,通过在硅片上叠加数十亿的电路和晶体管来实现使命。
- 🌐 在一个依赖计算能力的世界里,未来正是在这些超级工厂内部被创造出来的。
- 💧 工厂在周一上午达到水和电使用的高峰,任何故障都可能导致灾难性的后果。
- 🌟 工厂的控制中心被称为'星舰',是整个工厂操作的大脑,控制着所有设施的电力系统、水系统、空调和化学管理。
- 📈 半导体制造涉及超过一千个步骤,其中任何一个步骤的中断都相当于整个工作流程的停止,重启将是一个挑战。
- 💰 生产中断可能会导致数百万美元的损失,能源中心在保障这个半导体巨头的命脉中起着至关重要的作用。
- 📊 芯片上放置的大量晶体管,这些所谓的开关,是所有计算的基本组成部分,晶体管数量越多,可能进行的计算就越复杂。
- 🏞️ 台湾在芯片制造方面表现突出,拥有丰富的经验和地理优势,几乎占据了全球代工服务市场70%的份额。
- 🌿 工厂通过安装世界上第一个化学浓缩系统,将废弃的异丙醇转化为可再利用的原材料,减少了对环境的负担。
Q & A
这个工厂为什么被称为世界上最干净的工厂?
-这个工厂采用了尖端技术,不断进行创新,并且在半导体制造过程中对环境和资源的保护做出了巨大努力,包括安装了世界上第一个化学浓度系统来回收利用废弃的异丙醇,以及通过智能处理系统回收近80%的用水,因此被称为世界上最干净的工厂。
为什么在半导体制造行业中创新是至关重要的?
-在半导体制造行业中,创新是生存和发展的关键。如果不进行创新,就无法在技术快速发展和竞争激烈的行业中保持竞争力。此外,半导体技术的进步对整个计算和电子行业具有基础性的影响。
硅在半导体制造中扮演什么角色?
-硅是制造微芯片的基础材料,它有时可以导电,有时则不导电,这取决于如何施加微小的电压,因此被称为半导体。在半导体制造中,硅被用来制造数以亿计的电路和晶体管。
台湾在全球半导体生产中占据什么地位?
-台湾在全球半导体生产中占据领导地位,拥有近70%的全球代工市场份额,超过90%的先进制造工艺市场份额,并且在组装和测试方面也处于全球领先地位。台湾是全球最重要的半导体生产地。
Micron Technology 在台湾的制造规模有多大?
-Micron Technology 在台湾的制造规模非常庞大,拥有25%的员工在台湾工作,生产了Micron 65%的DRAM,并且在全球市场的份额超过10%。台湾的工厂占地面积达100万平方米,相当于140个足球场的大小。
半导体制造过程中的设计阶段包括哪些内容?
-半导体制造过程中的设计阶段包括开发集成电路的架构,类似于建造摩天大楼时的建筑设计。设计阶段需要将数十亿个晶体管合理地布局在每个微小的芯片上。
如何确保半导体制造过程中的洁净度?
-为了确保半导体制造过程中的洁净度,工作人员需要穿上特制的防尘服(俗称兔装),并通过一个特殊的“淋浴”过程,使用过滤空气清除任何可能的污染物。此外,生产区域的清洁度是医院手术室的一百倍。
半导体制造中使用的光刻机的工作原理是什么?
-光刻机的工作原理类似于暗房中的照相印刷过程,但使用的是价值数百万美元的机器,并且具有极高的精确度。在机器内部,硅片暴露于紫外线下,通过带有设计图案的掩模(类似于胶片底片)投影,光学地将电路设计印刷到硅片上,使暴露区域固化,而未暴露区域则被蚀刻掉。
自动化在半导体制造中扮演什么角色?
-自动化在半导体制造中扮演着至关重要的角色,它可以减少人为污染的可能性,提高生产效率。通过自动化系统,机器可以自动搬运硅片,优化交付效率,并且允许单个操作员远程监控和操作更多的机器。
芯片制造完成后的最终挑战是什么?
-芯片制造完成后的最终挑战是将它们转化为可用的组件。这包括使用钻石刀片将硅片上的多个芯片分离,然后将单个芯片放置到电路板上,并通过精密机器用细金线进行连接。
这个工厂如何减少对环境的影响?
-这个工厂通过安装世界上第一个化学浓度系统来回收利用废弃的异丙醇,回收近80%的用水,采用垂直绿化方法在工厂墙壁上种植植被,创建绿色带,以及使用可再生能源来减少能源消耗,从而减少对环境的影响。
Outlines
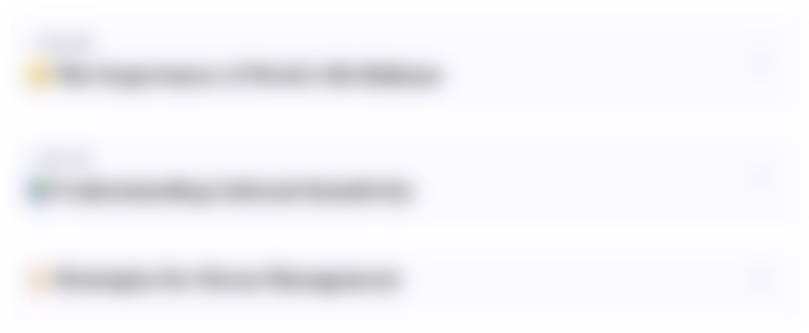
Cette section est réservée aux utilisateurs payants. Améliorez votre compte pour accéder à cette section.
Améliorer maintenantMindmap
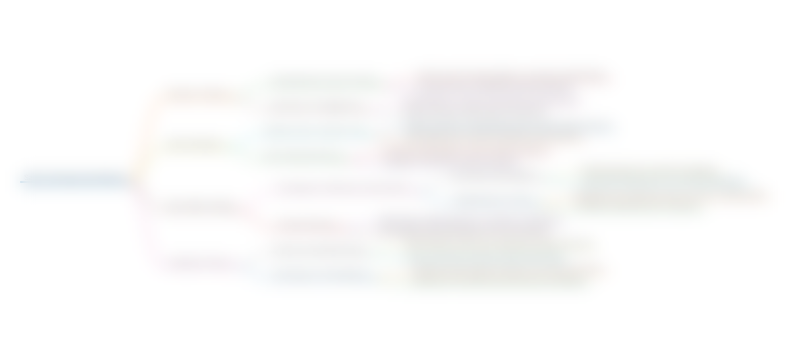
Cette section est réservée aux utilisateurs payants. Améliorez votre compte pour accéder à cette section.
Améliorer maintenantKeywords
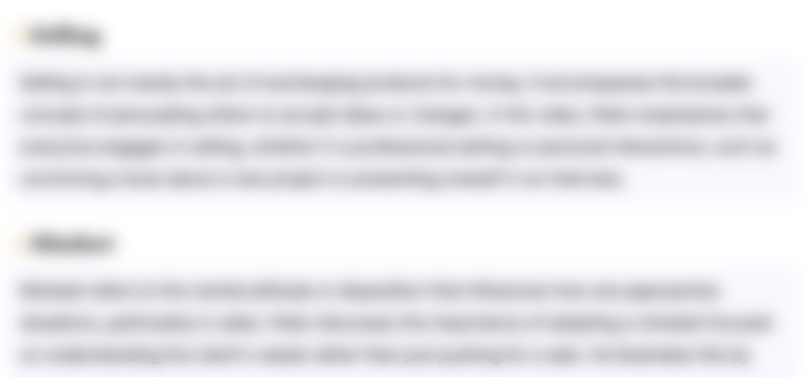
Cette section est réservée aux utilisateurs payants. Améliorez votre compte pour accéder à cette section.
Améliorer maintenantHighlights
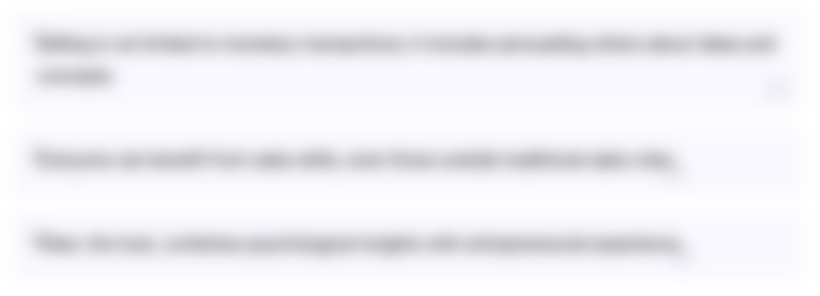
Cette section est réservée aux utilisateurs payants. Améliorez votre compte pour accéder à cette section.
Améliorer maintenantTranscripts
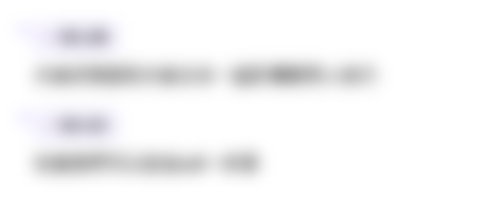
Cette section est réservée aux utilisateurs payants. Améliorez votre compte pour accéder à cette section.
Améliorer maintenantVoir Plus de Vidéos Connexes
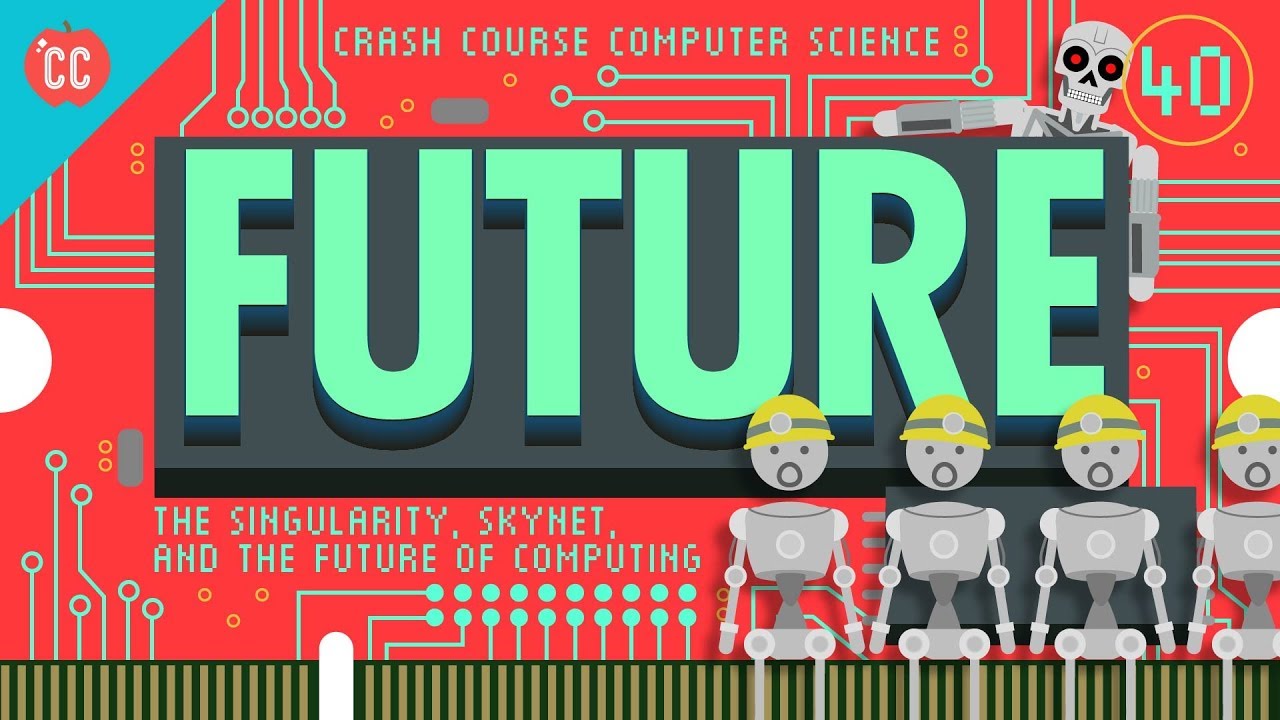
The Singularity, Skynet, and the Future of Computing: Crash Course Computer Science #40
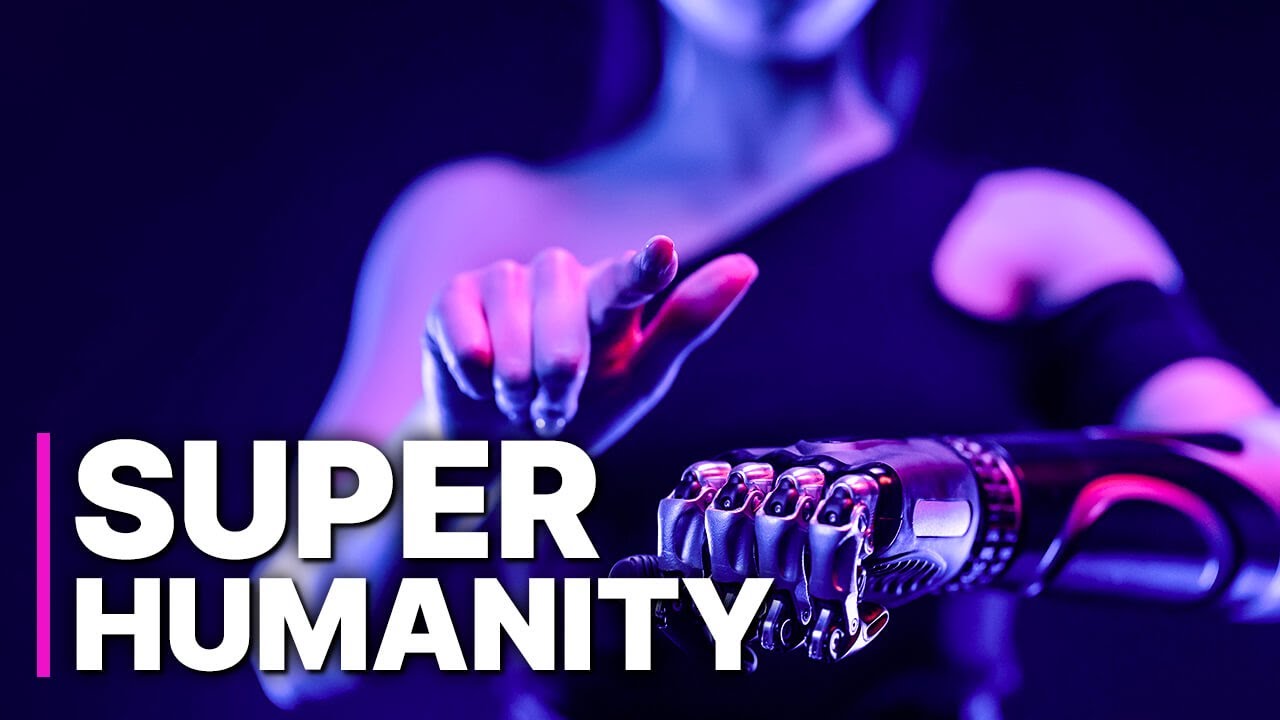
Super Humanity | Transhumanism
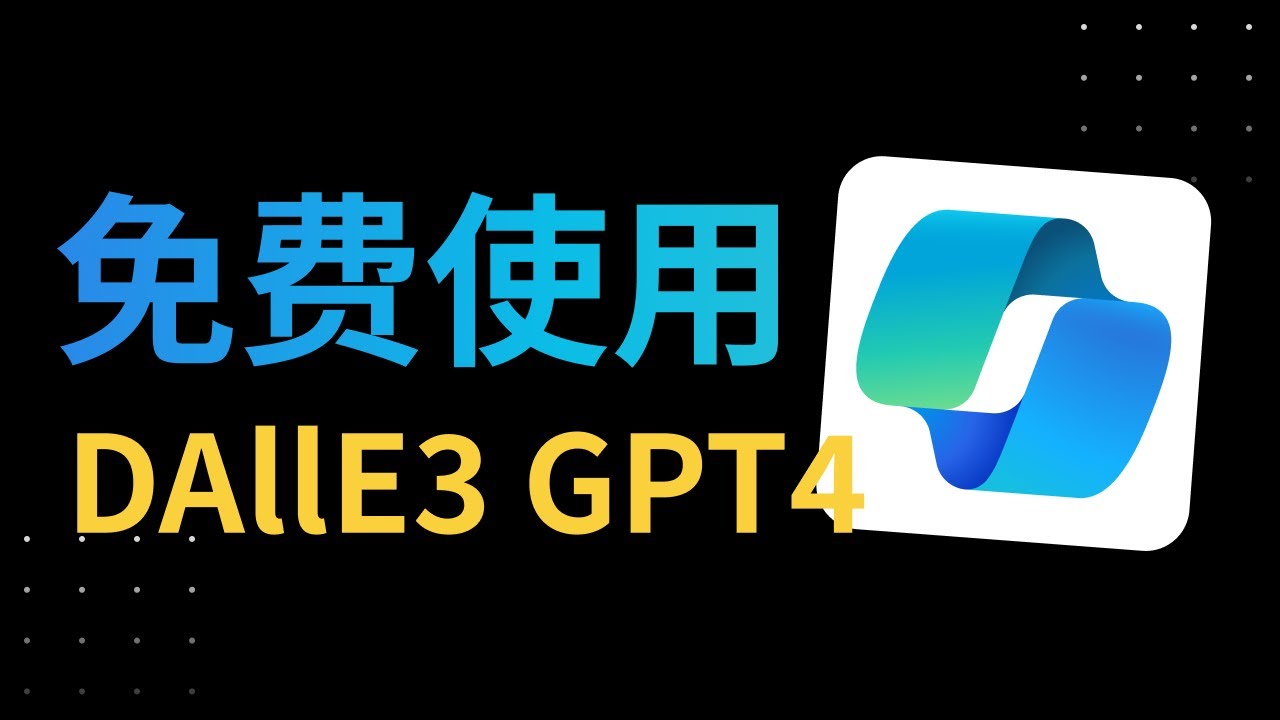
免费使用 GPT-4 Turbo、DALLE-3 绘画!Copilot 操作教程分享,在中国大陆也可以轻松使用
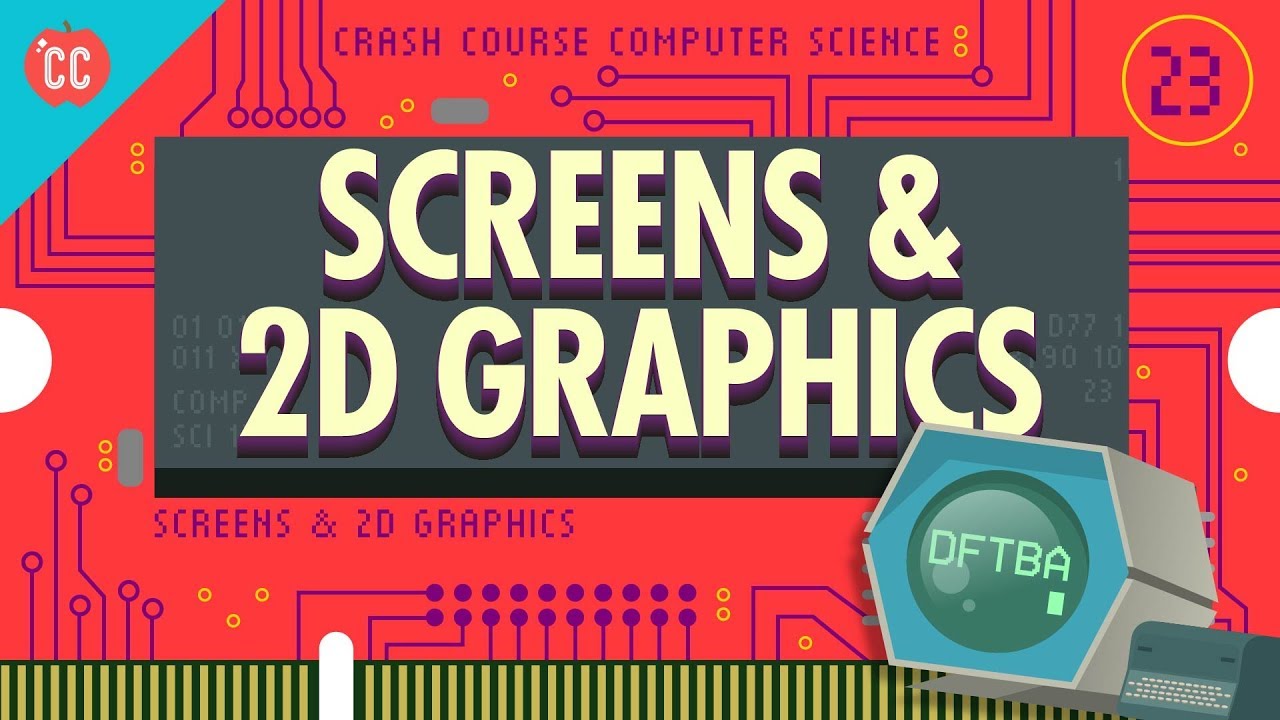
Screens & 2D Graphics: Crash Course Computer Science #23
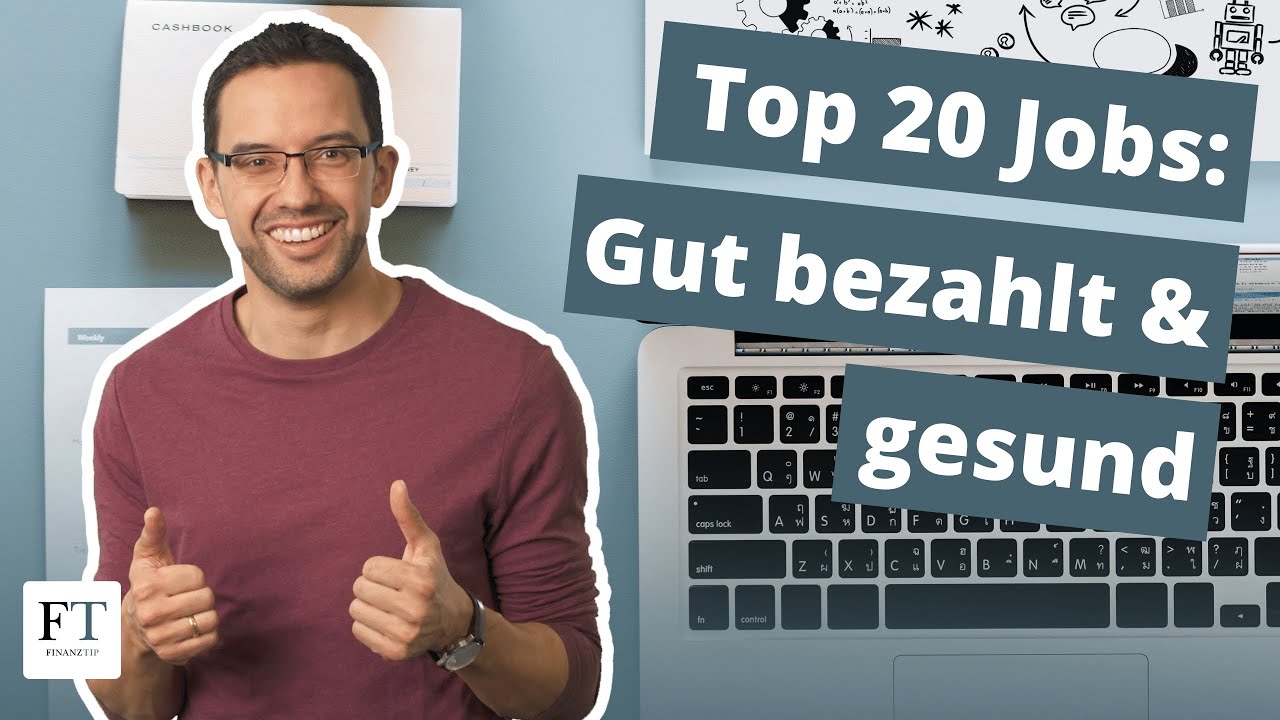
Die 20 bestbezahlten Jobs, die nicht krank machen

The 4 Great Emerging Technologies: A Journey Through the Digital Frontier! #technology #ai #vr
5.0 / 5 (0 votes)