Bolting & Welding Primer - Part 5
Summary
TLDRThe transcript discusses critical principles of welding and structural connection design, emphasizing the importance of providing effective load paths and avoiding common pitfalls that can lead to failures. It highlights issues such as improper weld placement, the significance of weld quality, and the need for designers to consider the impact of welds on structural integrity. The speaker also introduces resources for finding material properties and specifications, ensuring that engineers can access essential information for their projects. Overall, the focus is on enhancing safety and performance in welded constructions.
Takeaways
- 🛠️ Toughness is crucial for materials used in construction; it can be measured using the Charpy V-notch test.
- 🌡️ Toughness values decrease at lower temperatures; it's essential to consider transition temperatures for material selection.
- 🔄 Ensure load paths in connections align with stiff parts to prevent stress concentrations and potential failures.
- 🚫 Avoid placing welds in areas subjected to bending; this can lead to cracks and structural failure.
- ⚙️ All welded components should be treated as primary members; improper backing can create weak points.
- 🔍 Inspect welds thoroughly to avoid 'nothing welds'—welds that appear strong but lack proper fusion.
- 📏 Adjust weld sizes according to AWS standards to account for gaps, ensuring the joint's strength is maintained.
- 🛑 Design connections that minimize reliance on the welder's skill, using simplified geometries where possible.
- 📞 Utilize resources like the AISC Solution Center for guidance on material properties and design standards.
- 📚 Consistent application of these principles can lead to safer and more reliable structural designs.
Q & A
What is the significance of toughness in structural materials?
-Toughness is crucial as it measures a material's ability to absorb energy during fracture, especially important in structural applications like bridges where low temperature performance is critical.
Why should welds not be placed in bending conditions?
-Welds are more susceptible to cracking when subjected to bending stresses, which can lead to structural failures.
What is a 'nothing weld'?
-'Nothing welds' appear structurally sound but lack proper fusion, making them weak despite their visual integrity. Non-destructive testing is essential to identify these issues.
How can joint design improve weld quality?
-By ensuring that the performance of a joint does not depend solely on the welder's skill and by minimizing gaps, joint design can facilitate proper welding and enhance structural integrity.
What role do load paths play in connection design?
-Load paths ensure that forces are directed through members in a manner that aligns with their stiffness, preventing concentrated stresses that could lead to failure.
What are the implications of having gaps in weld joints?
-Gaps in weld joints can reduce the effective throat size, increasing stress concentrations. AWS guidelines provide limits on acceptable gap sizes and require weld size adjustments accordingly.
What should be done if the main member is thicker than the branch member?
-If there’s a thickness disparity, special considerations must be taken, such as using backing bars or stepped connections to ensure quality welds and prevent gaps.
How can engineers ensure compliance with best practices in welding?
-Engineers can reference resources like the Lincoln Electric website for material properties and adhere to AWS (American Welding Society) standards to ensure proper design and welding practices.
Why is it important to consider secondary members in welded structures?
-There are no truly secondary members; all components must be designed to handle their structural roles to prevent failures due to incorrect assumptions about their significance.
What design modifications can mitigate bending stresses on welds?
-Design modifications may include using continuity plates, stiffeners, or changing the configuration of connections to better distribute loads and reduce bending effects.
Outlines
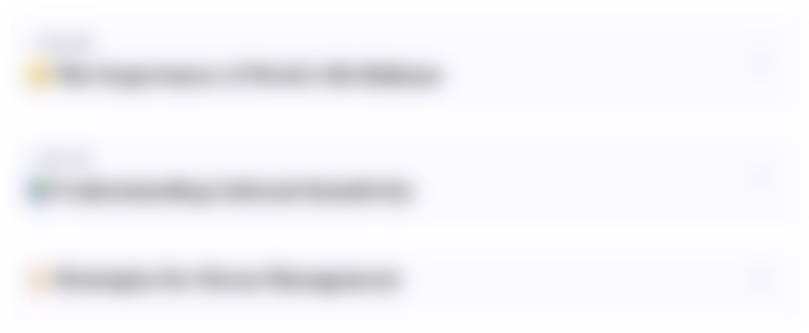
Cette section est réservée aux utilisateurs payants. Améliorez votre compte pour accéder à cette section.
Améliorer maintenantMindmap
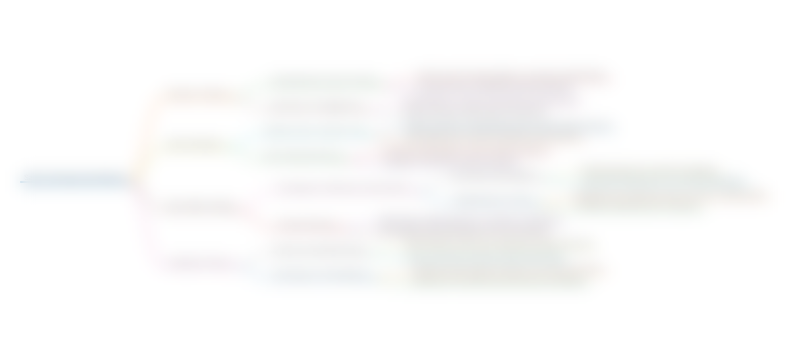
Cette section est réservée aux utilisateurs payants. Améliorez votre compte pour accéder à cette section.
Améliorer maintenantKeywords
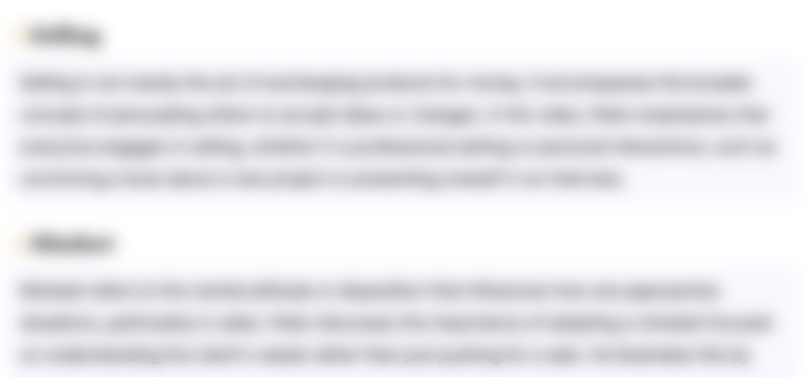
Cette section est réservée aux utilisateurs payants. Améliorez votre compte pour accéder à cette section.
Améliorer maintenantHighlights
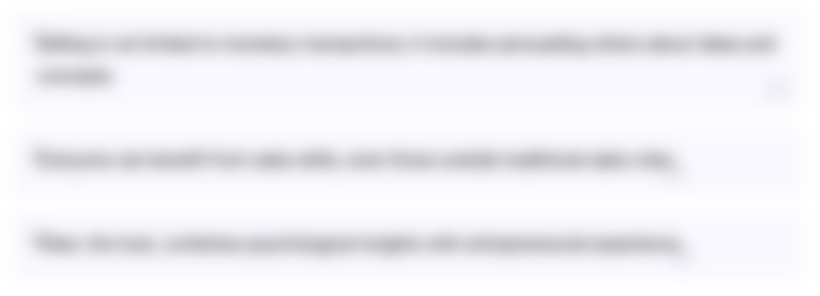
Cette section est réservée aux utilisateurs payants. Améliorez votre compte pour accéder à cette section.
Améliorer maintenantTranscripts
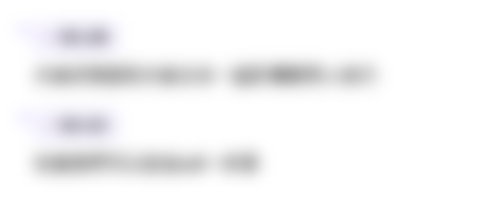
Cette section est réservée aux utilisateurs payants. Améliorez votre compte pour accéder à cette section.
Améliorer maintenantVoir Plus de Vidéos Connexes

NSCP 2015 LOAD PROVISION AND LOAD COMBINATIONS

Introduction to Wind Loads Part 1 (NSCP 2015)

Scalability Simply Explained in 10 Minutes
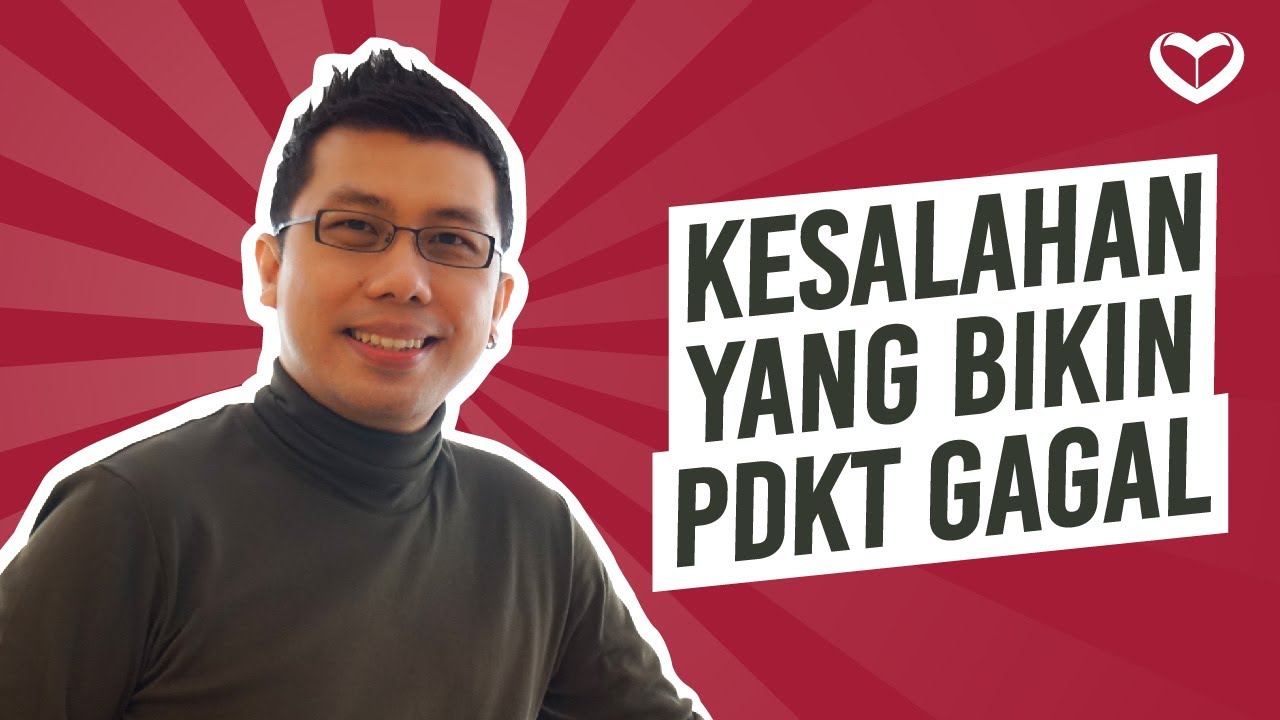
Kesalahan Yang Sering Bikin Kamu Gagal PDKT
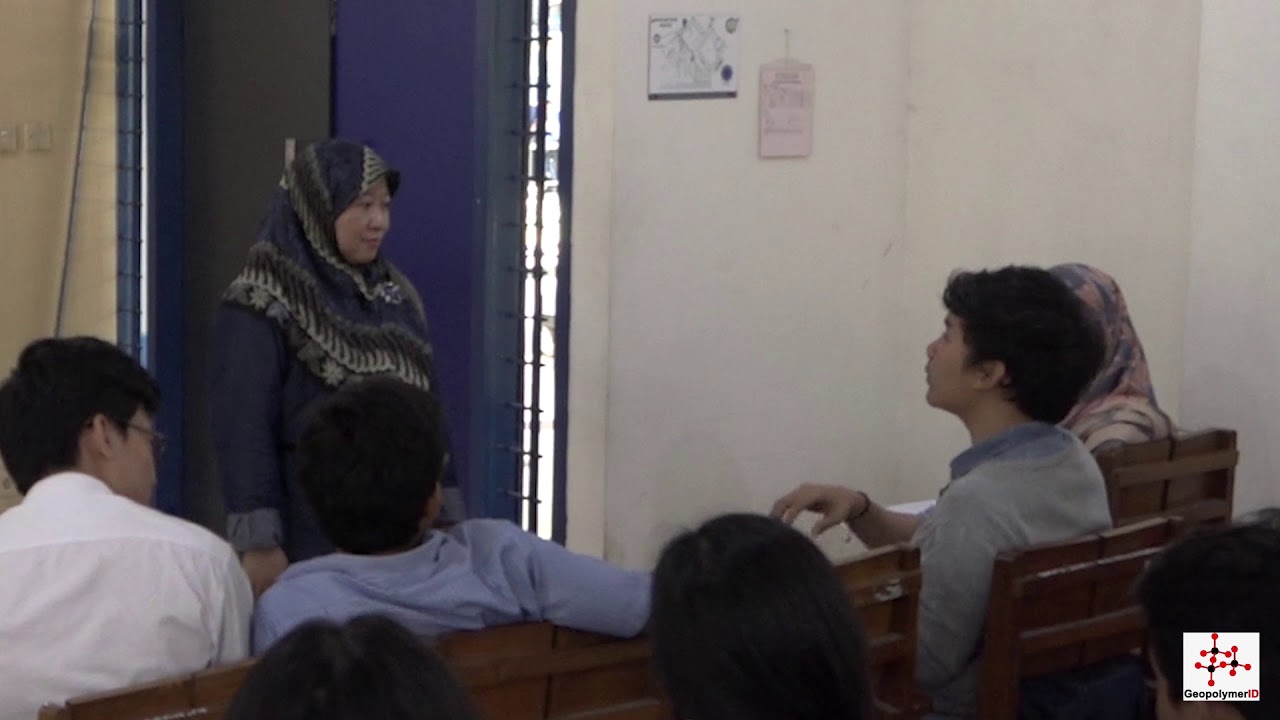
[TEKNOLOGI BAHAN & BETON] PERTEMUAN 5 "PENGUJIAN BETON KERAS NONDESTRUKTIF - PART 2" O/ Dr. JANUARTI
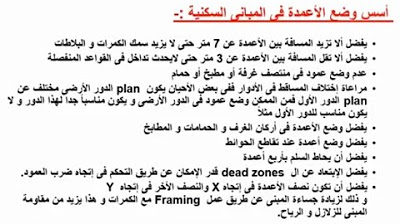
محاضرة 41 ( الـ Statical System _ أسس وضع الأعمدة جزء 1 ) هشام طارق
5.0 / 5 (0 votes)