SUBMERGED ARC WELDING | How submerged arc welding works.
Summary
TLDRThis video explains submerged arc welding, a process where the welding arc is hidden under a blanket of granular flux to prevent atmospheric contamination. It covers the working principle, which involves melting the filler rod to create a strong weld, and the essential equipment needed, including power sources and flux delivery mechanisms. The advantages include reduced fumes and radiation, while the limitations involve restrictions to flat and horizontal positions. Applications range from automotive and aviation to shipbuilding and pressure vessel fabrication. Viewers are encouraged to subscribe for more informative content.
Takeaways
- 😀 Submerged arc welding (SAW) involves an arc generated between the filler rod electrode and the workpiece, submerged in granular flux.
- 😀 The granular flux protects the weld pool and arc zone from atmospheric contamination during the welding process.
- 😀 The working principle of SAW is similar to shielded metal arc welding, utilizing an arc to melt the filler rod and deposit filler metal.
- 😀 Key equipment for SAW includes a power source (AC or DC), electrode feed mechanism, flux delivery mechanism, and a control unit.
- 😀 The welding process begins with depositing cold flux on the work area, which acts as an insulator until the arc is generated.
- 😀 One of the major advantages of SAW is that it produces no spatter or fumes, enhancing safety and cleanliness.
- 😀 SAW can be automated, allowing for semi-automatic or fully automatic operations suitable for various environments.
- 😀 Limitations of SAW include its restriction to flat and horizontal welding positions and its compatibility mainly with nickel steel and stainless steel.
- 😀 Common applications of SAW include welding low carbon and low alloy steel, as well as in automotive, aviation, and shipbuilding industries.
- 😀 The process is efficient for fabricating pipes and pressure vessels, including circumferential welding in boiler construction.
Q & A
What is submerged arc welding?
-Submerged arc welding is a type of arc welding where the arc is generated between a filler rod electrode and the workpiece, submerged in a pool of granular flux that protects the weld pool and arc zone from atmospheric contamination.
How does the welding process begin?
-The welding process begins by depositing granular flux on the area to be welded. The flux acts as an insulator before the arc is generated by striking the electrode against the workpiece.
What are the key components of submerged arc welding equipment?
-The key components include a power source (AC or DC), an electrode feed mechanism, a flux delivery mechanism (flux hopper), a welding head or gun, and the filler rod, which is fed as continuous wire.
What types of current are used in submerged arc welding?
-Submerged arc welding typically uses direct current with the electrode positive (DCEP) in the range of 200 to 1,200 amps.
What are the advantages of submerged arc welding?
-Advantages include minimal spatter and fume generation, suppression of ultraviolet radiation, and the ability to perform semi-automatic or fully automatic welding, making it suitable for both indoor and outdoor applications.
What are the limitations or disadvantages of submerged arc welding?
-Disadvantages include limitations to flat welding positions, restricted to horizontal positions with modern tools, and its suitability primarily for nickel steel and stainless steel.
What materials can be welded using submerged arc welding?
-This welding method is effective for welding low carbon and low alloy steel, commonly used in automotive, aviation, and shipbuilding industries.
What is the role of granular flux in submerged arc welding?
-Granular flux protects the weld pool from contamination, melts to form a slag layer over the weld, and helps purify and fortify the molten weld metal.
In what applications is submerged arc welding commonly used?
-Common applications include fabrication of pipes, pressure vessels, automotive components, aviation structures, shipbuilding, and circumferential welding.
How is the welding process advanced during submerged arc welding?
-The welding process is advanced either by moving the welding assembly over the area to be welded or by moving the workpiece while keeping the welding system stationary.
Outlines
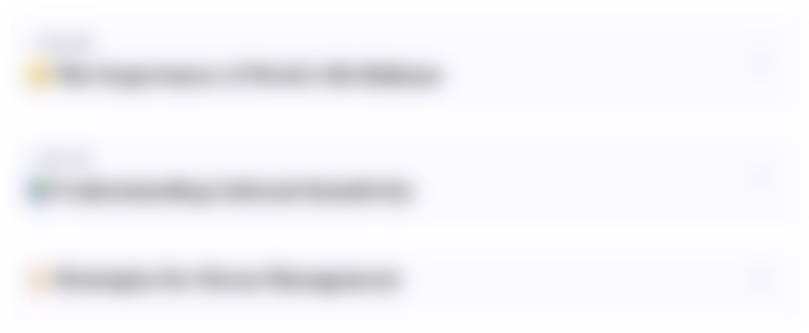
Cette section est réservée aux utilisateurs payants. Améliorez votre compte pour accéder à cette section.
Améliorer maintenantMindmap
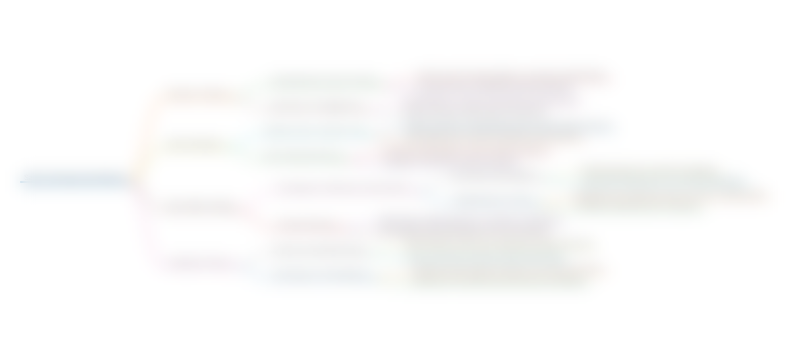
Cette section est réservée aux utilisateurs payants. Améliorez votre compte pour accéder à cette section.
Améliorer maintenantKeywords
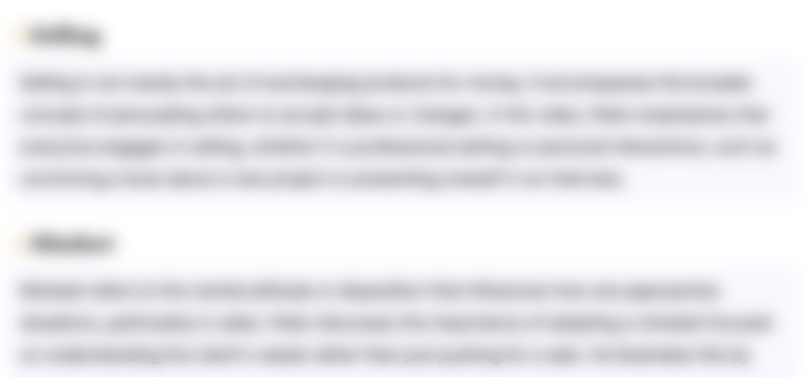
Cette section est réservée aux utilisateurs payants. Améliorez votre compte pour accéder à cette section.
Améliorer maintenantHighlights
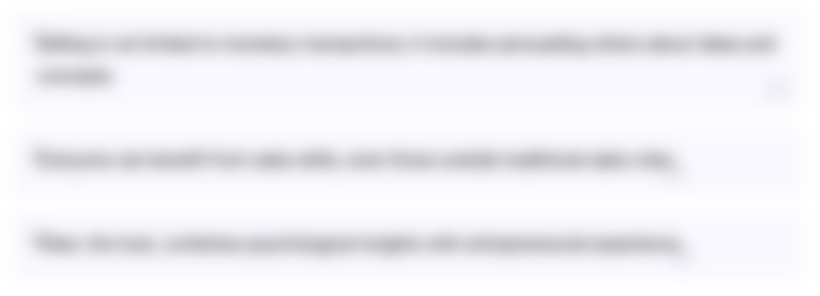
Cette section est réservée aux utilisateurs payants. Améliorez votre compte pour accéder à cette section.
Améliorer maintenantTranscripts
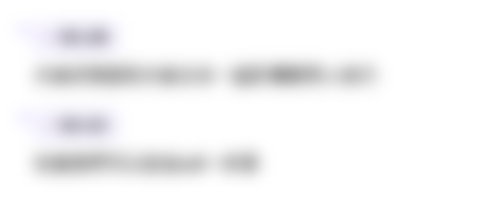
Cette section est réservée aux utilisateurs payants. Améliorez votre compte pour accéder à cette section.
Améliorer maintenant5.0 / 5 (0 votes)