From Sales Order to Manufacturing Order | Odoo MRP
Summary
TLDRThis video walks through the integration of sales and manufacturing processes in Odoo, using Stealthy Wood's operations as an example. It explains how to set up automatic workflows to manage product sales and manufacturing efficiently. By configuring bills of materials, purchase orders, and reordering rules, the system ensures seamless inventory management and production. The video demonstrates how Odoo generates sales orders, purchase orders, and manufacturing orders to streamline operations. The final result is a smooth, automated process that prevents stock shortages and enables timely deliveries to customers.
Takeaways
- đ Odoo helps streamline sales and manufacturing integration by automating key processes like creating sales orders and purchase requests.
- đŠ When a product is purchased that needs to be manufactured, Odoo automatically generates sales orders, RFQs for components, and manufacturing orders.
- đȘ The example in the video focuses on manufacturing a conference chair, showcasing the step-by-step flow in the Stealthy Wood database.
- đ§ A bill of materials (BOM) is essential to set up for any product being manufactured in Odoo.
- đ To ensure automation works smoothly, the manufacturing route needs to be activated on the product form in Odoo.
- đ Odoo automates purchasing by linking the product's purchase route to specific vendors and setting up reordering rules.
- đ Reordering rules allow Odoo to know how many items to order when stock levels are low or a sales order is created.
- đ Once the sales order is confirmed, Odoo generates necessary purchase orders and manufacturing orders for missing components.
- đ„ Odoo tracks stock levels and ensures that all necessary steps are completed before allowing the delivery of products to customers.
- â After production is complete, Odoo updates the sales order, moving it to a ready stage, allowing for customer delivery.
Q & A
What is the primary objective of the process discussed in the script?
-The primary objective is to integrate sales with the manufacturing process using Odoo, allowing automatic behaviors when products that need to be manufactured are purchased, thus streamlining operations and preventing stock shortages.
How does Odoo help save time and prevent bottlenecks in the manufacturing process?
-Odoo automatically generates sales orders, requests for quotations from vendors, and manufacturing orders when a product is purchased, ensuring that all necessary components are in place to avoid delays and bottlenecks.
What is required to begin configuring the manufacturing process in Odoo?
-To configure the manufacturing process, a bill of materials (BOM) must be created for the product. Additionally, the 'Manufacture' route should be activated on the product form to signal that the product needs to be manufactured.
Why is it important to automate purchase orders for components in Odoo?
-Automating purchase orders ensures that components for the manufacturing process are reordered automatically, preventing stock shortages and delays in production.
What configuration must be done for individual components of a product in Odoo?
-For individual components, the 'Buy' route must be selected, indicating the item will be purchased from a vendor. Additionally, a vendor needs to be assigned to the product, and reordering rules should be configured to manage stock levels.
What is the purpose of setting reordering rules in Odoo?
-Reordering rules are set to determine the minimum and maximum quantities of a product that should be ordered when a sales order is created, ensuring that stock levels remain optimal.
How does the sales application in Odoo integrate with the manufacturing process?
-When a sales order is created for a product that needs to be manufactured, Odoo generates the necessary manufacturing orders and purchase orders for components, allowing the production process to begin seamlessly.
What steps are taken when a product is out of stock and needs to be manufactured?
-If a product is out of stock, a manufacturing order is generated, and any required components are ordered from vendors. Once the components arrive, the product is manufactured and delivered to the customer.
How does the replenishment process work in Odoo?
-The replenishment process involves going to the inventory application, selecting the product, and automating orders for manufacturing and purchasing components. Odoo will generate the necessary manufacturing and purchase orders automatically.
What happens after the manufacturing order is completed in Odoo?
-After the manufacturing order is completed, the product is marked as 'done,' and the sales order can be fulfilled. The delivery status is updated from 'waiting' to 'ready,' allowing the item to be delivered to the customer.
Outlines
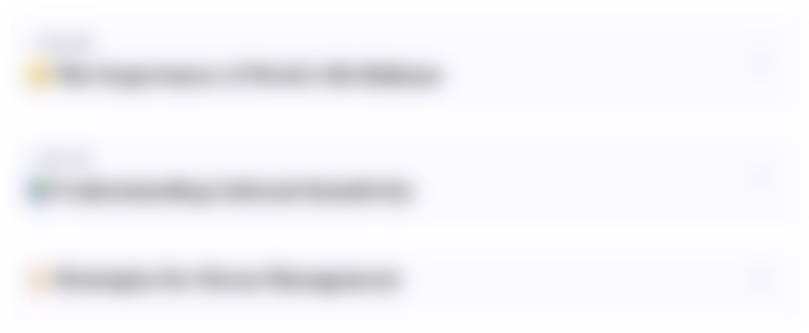
Cette section est réservée aux utilisateurs payants. Améliorez votre compte pour accéder à cette section.
Améliorer maintenantMindmap
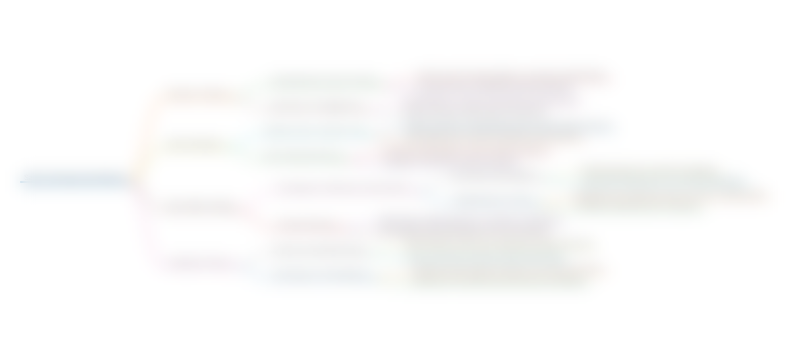
Cette section est réservée aux utilisateurs payants. Améliorez votre compte pour accéder à cette section.
Améliorer maintenantKeywords
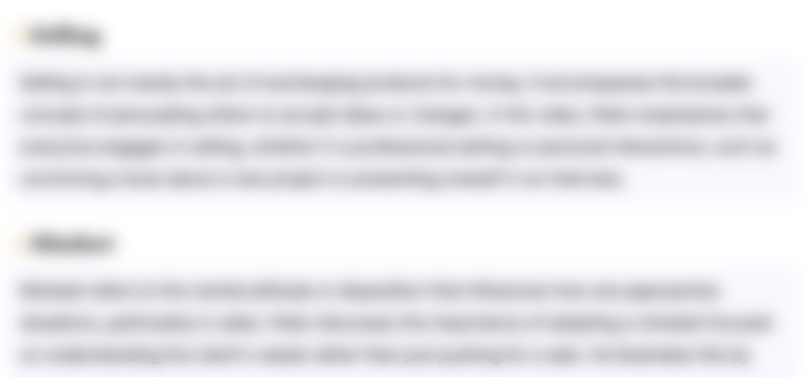
Cette section est réservée aux utilisateurs payants. Améliorez votre compte pour accéder à cette section.
Améliorer maintenantHighlights
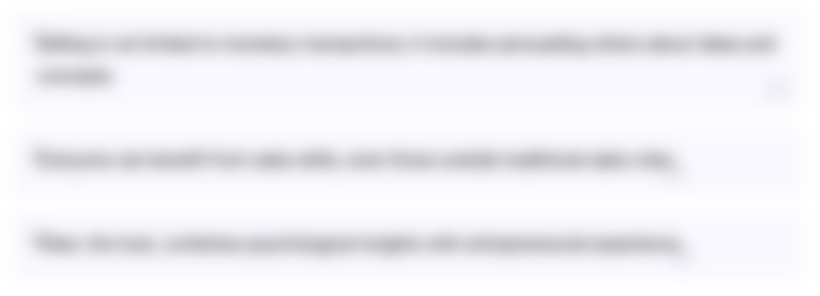
Cette section est réservée aux utilisateurs payants. Améliorez votre compte pour accéder à cette section.
Améliorer maintenantTranscripts
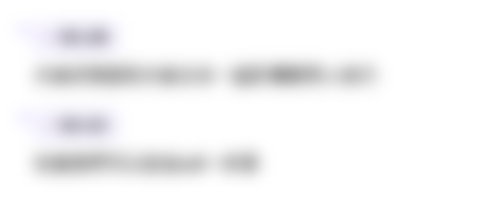
Cette section est réservée aux utilisateurs payants. Améliorez votre compte pour accéder à cette section.
Améliorer maintenant5.0 / 5 (0 votes)