Process Mapping
Summary
TLDRProcess mapping is a visual tool that makes the invisible office processes visible, allowing for analysis and improvement. It involves identifying each step, the job function responsible, and the flow from suppliers to customers. A value stream map provides a macro-level view, while detailed mapping uses color-coded Post-it notes to represent different process elements. This method was successfully applied by the Bureau of Criminal Investigation to enhance their DNA analysis process, leading to faster criminal apprehension and swift justice.
Takeaways
- 🔍 **Process Mapping Reveals Invisible Workflows**: It makes the typically unseen processes in an office environment visible and analyzable.
- 🏭 **Manufacturing vs. Office Processes**: While manufacturing processes are more tangible, office processes often remain hidden and unexamined.
- 🚀 **Improvement Through Visibility**: Process mapping allows for the identification of inefficiencies and waste, leading to targeted improvements.
- 📈 **Starting with a SIPOC Diagram**: This high-level diagram outlines the process's suppliers, inputs, outputs, customers, and scope.
- 👥 **Engagement of Process Owners**: Those who work in the process should be involved in mapping it to ensure accuracy and buy-in.
- 🎨 **Visual Exercise with Physical Space**: A large space and visual tools like Post-it notes are used to organize and visualize each step of the process.
- 📝 **Verb Noun Format for Steps**: Steps should be written in a clear, actionable format to facilitate understanding and improvement.
- 🌈 **Color Coding for Clarity**: Different colors of Post-it notes represent different aspects of the process, such as steps, decisions, and delays.
- 🔗 **Connecting Steps with Arrows**: Straight arrows for tasks by the same function, box arrows for handoffs, and jagged arrows for electronic transfers.
- 🔍 **Analyzing for Value and Waste**: After mapping, identify value-added activities and non-value added steps, including those mandated by regulation.
- 💡 **Real-World Success Story**: The Bureau of Criminal Investigation used process mapping to improve their DNA analysis process, leading to faster results and increased efficiency.
Q & A
What is the primary purpose of process mapping?
-The primary purpose of process mapping is to make the invisible processes visible, allowing us to understand them, identify inefficiencies and waste, and take steps to improve them.
Why are manufacturing processes more visible compared to office processes?
-Manufacturing processes are more visible because they involve tangible transformations of raw materials into finished products that can be seen, whereas office processes are often intangible and not easily observed.
What does a SIPOC diagram represent in the context of process mapping?
-A SIPOC diagram represents the macro level big picture of a process, identifying the suppliers, inputs, outputs, and customers of the process, as well as the scope of the process.
Who should be involved in the process mapping exercise?
-The people who work in the process should be the ones doing the process mapping, as they have direct knowledge and experience with the process.
Why is ample space important for process mapping?
-Ample space is important for process mapping to organize each piece of the process visually and to allow for the placement and rearrangement of Post-it notes representing each step.
What is the significance of using different colors of Post-it notes in process mapping?
-Using different colors of Post-it notes helps to visually distinguish between various elements of the process, such as functional areas, decision points, and delays, making the process map easier to understand.
How should the steps of a process be written on Post-it notes during mapping?
-The steps should be written in a verb-noun format, which clearly describes the action and the object involved in each step.
What symbols are used to represent different types of steps in a process map?
-Straight arrows are used to connect steps within the same function, box arrows represent handoffs between functions, and jagged arrows indicate electronic handoffs.
What are the three types of activities identified during the analysis of a process map?
-The three types of activities identified are value-added activities, non-value added activities, and non-value added but necessary steps.
How did the Bureau of Criminal Investigation benefit from process mapping?
-The Bureau of Criminal Investigation benefited from process mapping by improving their DNA analysis process, leading to faster results, criminals being taken off the streets sooner, and swifter justice.
Where can one find more information on process mapping and its benefits?
-More information on process mapping and its benefits can be found on the website lean.ohio.gov under the resources tab.
Outlines
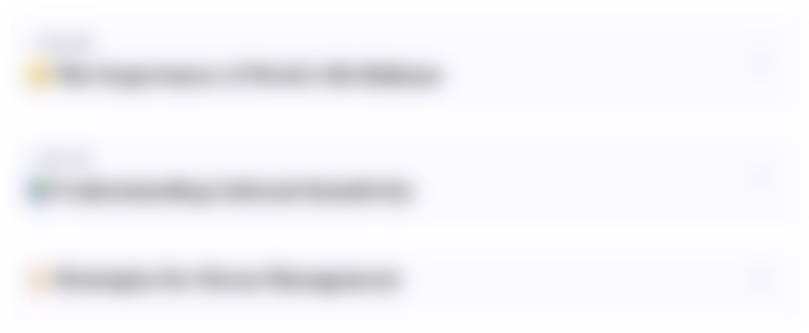
Cette section est réservée aux utilisateurs payants. Améliorez votre compte pour accéder à cette section.
Améliorer maintenantMindmap
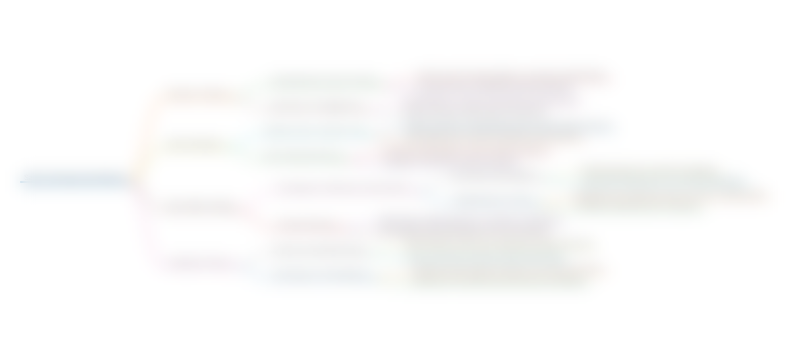
Cette section est réservée aux utilisateurs payants. Améliorez votre compte pour accéder à cette section.
Améliorer maintenantKeywords
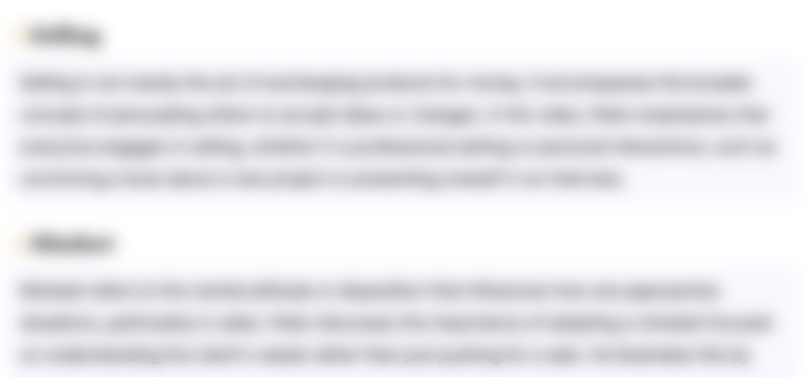
Cette section est réservée aux utilisateurs payants. Améliorez votre compte pour accéder à cette section.
Améliorer maintenantHighlights
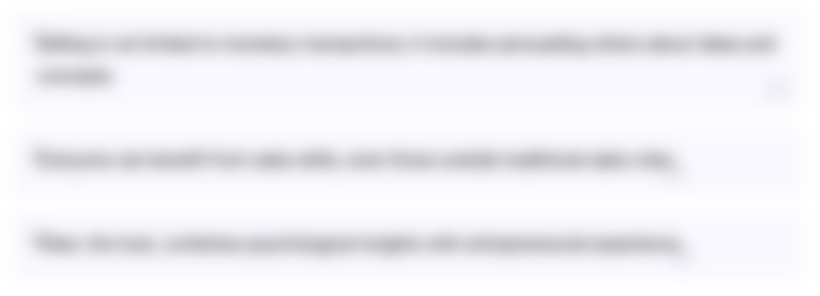
Cette section est réservée aux utilisateurs payants. Améliorez votre compte pour accéder à cette section.
Améliorer maintenantTranscripts
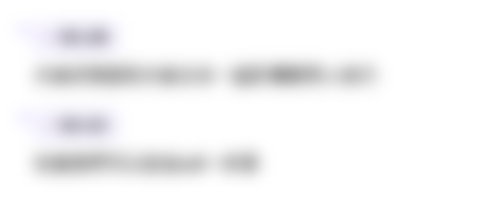
Cette section est réservée aux utilisateurs payants. Améliorez votre compte pour accéder à cette section.
Améliorer maintenantVoir Plus de Vidéos Connexes

How To Become an Academic Weapon in 24 hours

Value Stream Mapping Tutorial | Value Stream Mapping Symbols Explained | Invensis Learning
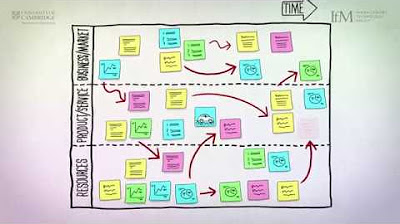
What is roadmapping and how can it benefit your organisation?
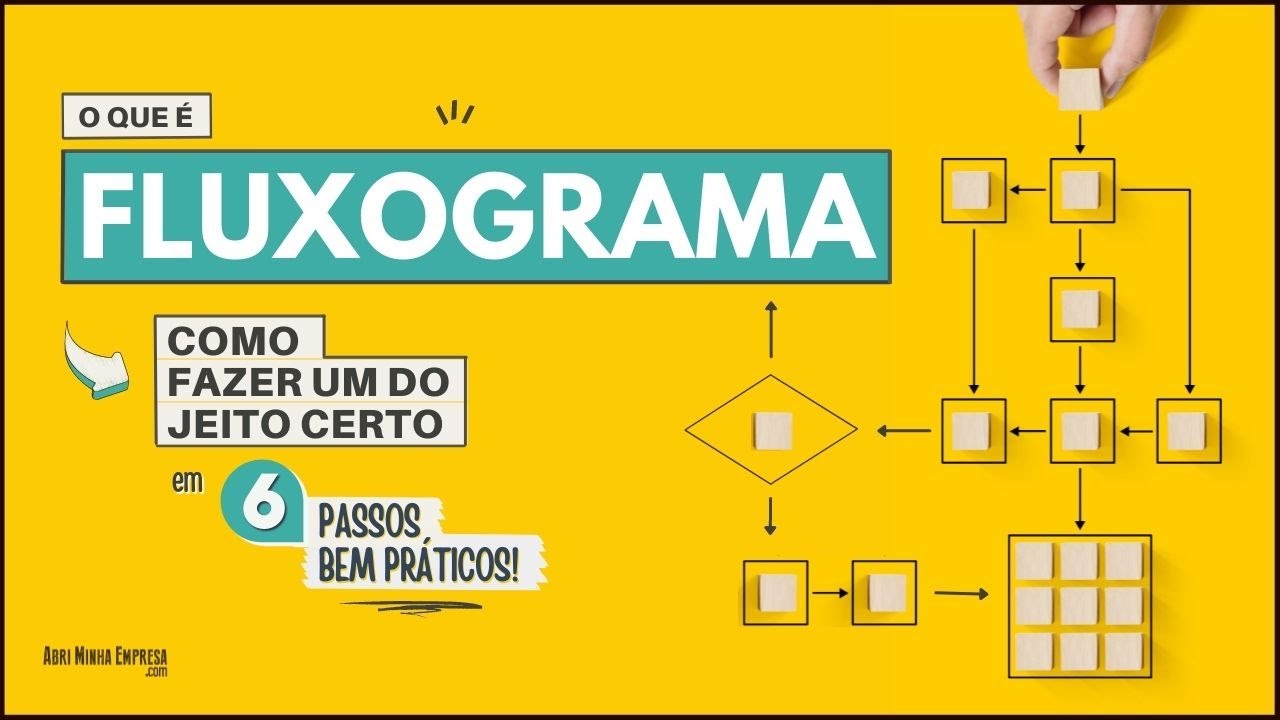
FLOWCHART WHAT IT IS AND HOW TO MAKE ONE (in 06 Very Practical Steps)
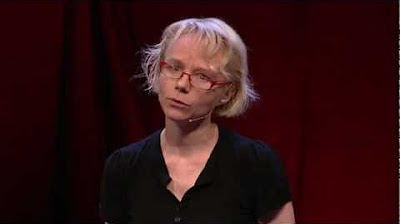
Nathalie Miebach: Art made of storms

Operations Management Chpt. 7 Palmer
5.0 / 5 (0 votes)