How Pringles are Made in Factory? | Captain Discovery
Summary
TLDRJoin Captain Discovery as we uncover the secrets of one of the world's largest Pringles factories. From harvesting potatoes to the innovative cylindrical packaging, witness how 650 workers operate 24/7 to produce the iconic, stackable chips. Learn about the meticulous selection, washing, peeling, and shaping processes, the unique seasoning method, and the environmental efforts by Kellogg's to make Pringles cans fully recyclable. Discover the history, production line, and the magic behind the irresistible crunch of Pringles.
Takeaways
- 🔍 Pringles are a unique type of potato chip invented in 1968 by Alexander Liepa at Proctor and Gamble.
- 🌏 The factory operates 24/7 with 650 workers to produce the popular snack.
- 🥔 Pringles source their potatoes from trucks, selecting only those that meet strict criteria for size, surface smoothness, and disease absence.
- 🚿 Potatoes undergo meticulous screening and washing to ensure they are free from dirt and debris before processing.
- 🔄 The production process includes peeling, shaping, and frying the potatoes at 200°C for about 11 seconds to achieve the desired crispy texture.
- 🍴 Pringles are known for their stackable design, achieved by using a blend of 1/3 water to 2/3 potato flakes and corn starch, shaped into ovals.
- 🌊 Seasoning at Pringles is done using a waterfall method, which seasons only one side of the chip, unlike traditional chips.
- 🌈 Pringles offers a variety of flavors, with over 25 in the US and a total of 318,000 unique flavor combinations globally.
- 📦 The packaging of Pringles, which includes a metal bottom, cardboard body, and plastic lid, presents recycling challenges.
- 🌱 Kellogg's, the brand owner, is experimenting with fully recyclable cans to address environmental concerns and promote sustainability.
Q & A
Who invented Pringles and when were they invented?
-Pringles were invented in the US in 1968 by Alexander Liepa, an engineer at Proctor and Gamble.
What is unique about Pringles' packaging?
-Pringles' packaging is iconic and cylindrical, designed to keep the chips from getting crumbled, which is a common issue with other potato chips.
How does the factory ensure the quality of potatoes used in Pringles?
-The factory selects only the finest potatoes based on strict criteria for size, surface smoothness, and absence of disease. They also undergo meticulous screening and washing processes.
What is the average annual potato consumption in the United States according to the script?
-Americans consume an average of 125 lbs (56.7 kg) of potatoes per person per year.
How does the process of shaping Pringles into their iconic form take place?
-After blending a mix of 1/3 water to 2/3 potato chips and corn starch, the mixture is rolled into elongated sheets, shaped into ovals, and then fried.
At what temperature and for how long are Pringles fried?
-Pringles are fried at 200°C for about 11 seconds to achieve their crispy texture.
How does Pringles ensure that excess oil is removed after frying?
-After frying, Pringles are whisked under a blower to remove any excess oil, and then each slice is crisped in a saddle-shaped mold.
How does Pringles season their chips, and is it different from traditional chips?
-Pringles are seasoned on one side only, using a waterfall seasoning process rather than a mixer, which is different from traditional chips.
What is the significance of the number of flavors Pringles offers in the US and globally?
-Pringles offers over 25 flavors in the US and even more globally, totaling 318,000 unique combinations, showcasing their variety and innovation.
What are the environmental considerations associated with Pringles' packaging?
-The packaging, which consists of a metal bottom, cardboard body, and plastic lid, poses challenges for recycling. However, Kellogg's, the brand owner, is experimenting with fully recyclable cans to address this issue.
How does Pringles distribute their products globally?
-Pringles mobilizes 100 trucks daily for global distribution, indicating the scale of their operations and reach.
Outlines
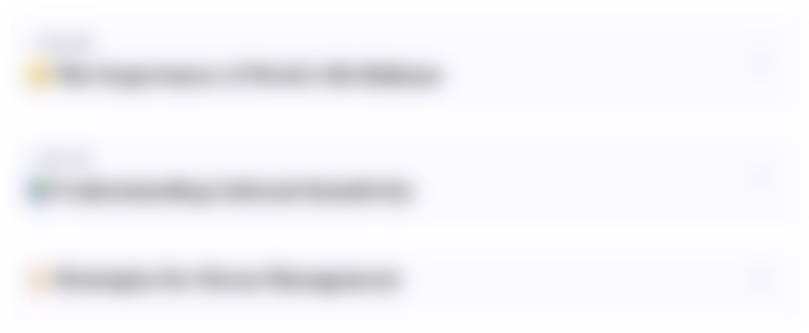
Cette section est réservée aux utilisateurs payants. Améliorez votre compte pour accéder à cette section.
Améliorer maintenantMindmap
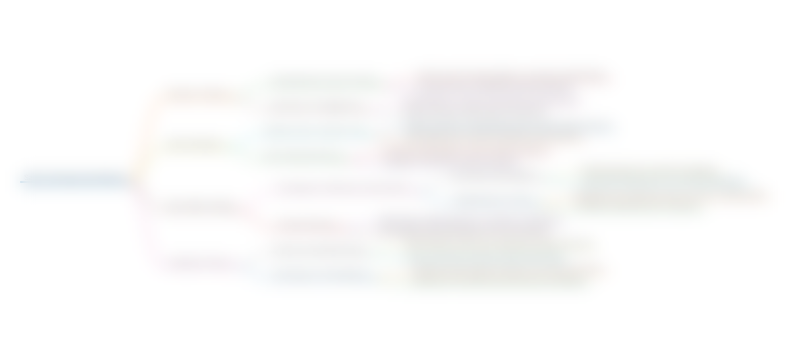
Cette section est réservée aux utilisateurs payants. Améliorez votre compte pour accéder à cette section.
Améliorer maintenantKeywords
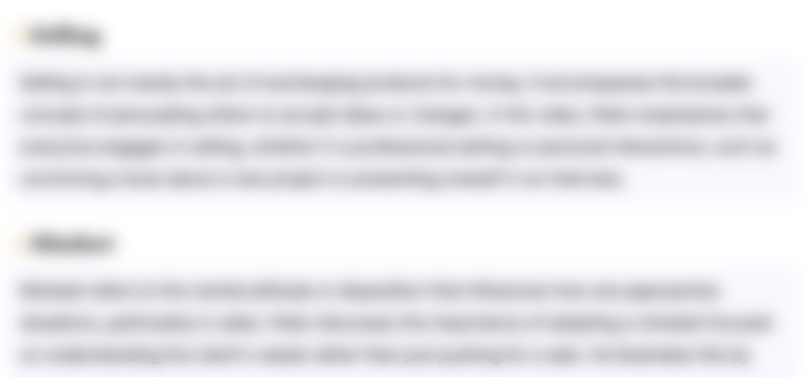
Cette section est réservée aux utilisateurs payants. Améliorez votre compte pour accéder à cette section.
Améliorer maintenantHighlights
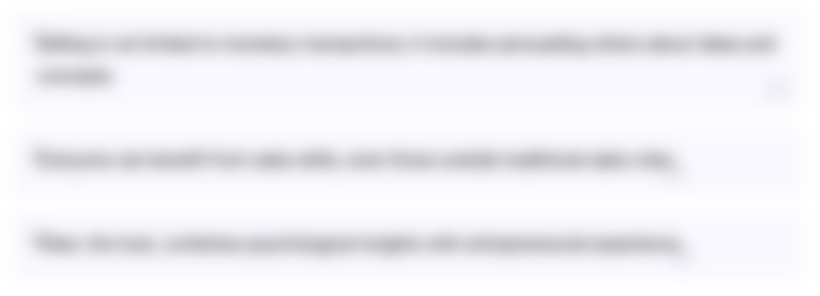
Cette section est réservée aux utilisateurs payants. Améliorez votre compte pour accéder à cette section.
Améliorer maintenantTranscripts
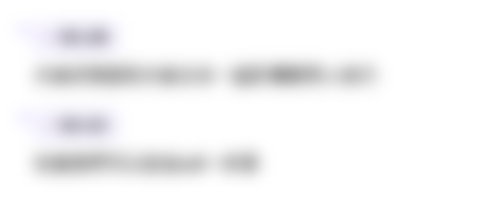
Cette section est réservée aux utilisateurs payants. Améliorez votre compte pour accéder à cette section.
Améliorer maintenantVoir Plus de Vidéos Connexes

How Nutella Is Made In Factory? | Captain Discovery

How M&Ms are Made In Factory? Largest M&Ms Factory Tour | Captain Discovery
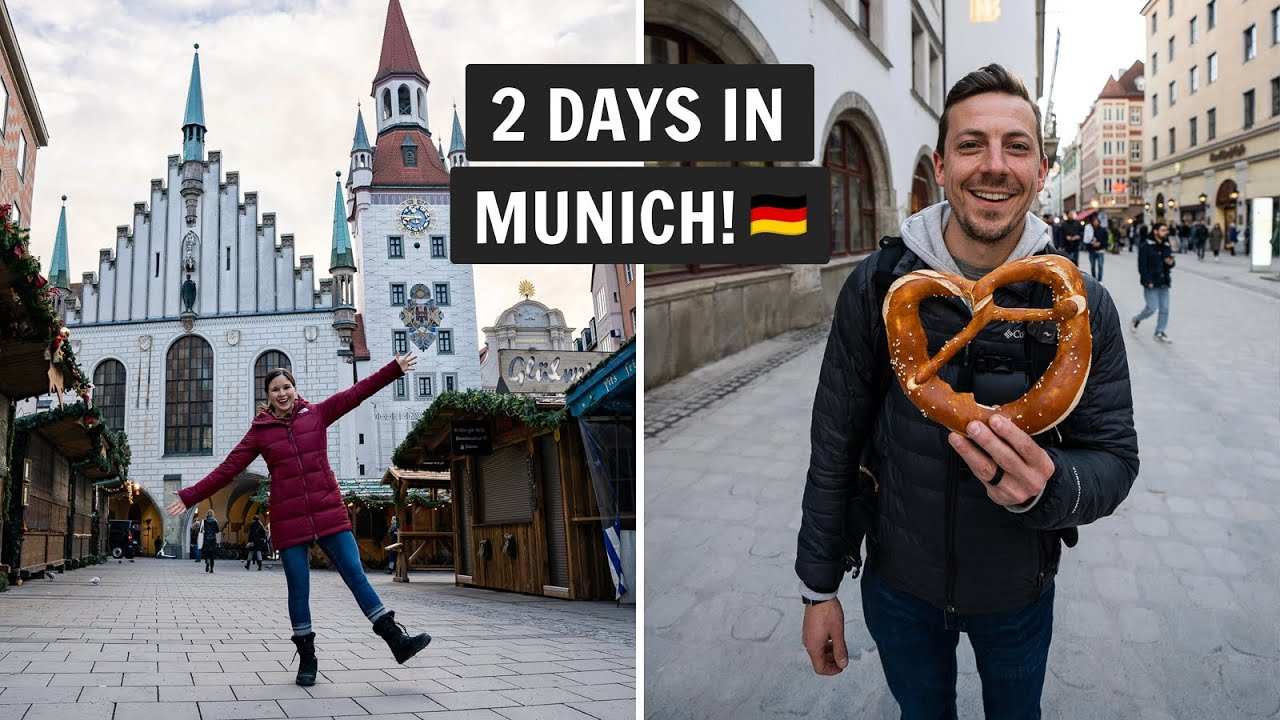
The BEST two days in Munich, Germany! 🇩🇪 (Things to do + local FOOD!)

What's Really Happening At CERN

Fakta tentang Berbagai Negara di Dunia

Discovering Tut : The Saga Continues |“Animated” Full(हिन्दी में)| Discovering Tut Class 11 in Hindi
5.0 / 5 (0 votes)