Powder Metallurgy Process
Summary
TLDRThe script delves into the process of metal powder production for parts, highlighting the use of elemental or pre-alloyed powders mixed with additives. It details the consolidation in molds, the green state of parts, and the centering furnace process to achieve metallurgical bonding and increased density. Various consolidation methods like mechanical pressing, injection molding, and isostatic pressing are discussed, emphasizing the design flexibility and production efficiency of powder metallurgy.
Takeaways
- 🔩 Metal powders used in parts production can be elemental or pre-alloyed, with the latter having the desired composition already mixed.
- 🧱 Additives like binders and lubricants are commonly added to the powder before consolidation.
- 🗜️ The powder is then consolidated in molds or dies to shape and densify it into a compact, known as the 'green state'.
- 🏗️ The green state parts have limited strength, suitable only for handling and are not yet fully dense.
- 🔥 The centering process, which involves heating below the melting point, is crucial for metallurgically bonding the particles and increasing strength.
- 📏 The final part density is critical for structural performance, with higher density correlating to better performance.
- 🏭 Common consolidation methods include mechanical pressing, injection molding, and isostatic pressing, with mechanical pressing being the most common.
- ⏱️ Mechanical pressing is efficient, producing hundreds to thousands of parts per hour, and can create parts with close tolerances.
- 🔩 Pressing can be done at room temperature or elevated temperatures, and core rods are used to control hole formation in the parts.
- 🔄 After pressing, parts are transferred to a centering furnace, which has controlled atmosphere zones for proper metallurgical bonding.
- 🔄 The centering furnace atmosphere can vary based on the base metal, including endothermic, exothermic, hydrogen, or inert gas environments.
Q & A
What are the two types of metal powders used in parts production?
-The two types of metal powders used in parts production are elemental particles and pre-alloyed powder.
What is the purpose of adding binders and lubricants to the metal powder?
-Binders and lubricants are added to the metal powder to facilitate the consolidation process, ensuring the powder particles adhere together and ease the molding process.
What is the 'green state' of a part and why is it significant?
-The 'green state' refers to the initial stage after the powder has been consolidated into a compact but before sintering. It is significant because the part has only light green strength, sufficient for handling but not for use.
What happens during the centering process?
-During centering, parts are heated below the melting point of the base metal to metallurgically bond the individual particles, increasing the part's strength and density.
Why is final part density important in powder metallurgy?
-Final part density is crucial because it directly affects the performance of structural parts, with higher density leading to improved performance.
What are the common methods for consolidating and shaping metal powder for parts production?
-The common methods for consolidating and shaping metal powder include mechanical pressing, injection molding, and isostatic pressing.
How are parts produced by mechanical pressing typically made?
-Parts are made by mechanically pressing by automatically feeding powder into a die, where it is consolidated by the vertical action of a punch or punches to a specific density.
What is the role of core rods in mechanical pressing?
-Core rods are used inside the die during mechanical pressing to control the formation of holes parallel to the direction of pressing.
How does the density of pressed powder change along the part height?
-The density of pressed powder tends to decrease along the part height as the distance between the compacting punch and die increases.
What is the purpose of a centering furnace in the production process?
-A centering furnace is used to heat the compacted parts to a temperature below the melting point of the base metal, which helps to metallurgically bond the particles and further densify the parts.
What are the different types of atmospheres used in centering furnaces?
-The atmospheres used in centering furnaces can be endothermic (composed mainly of hydrogen, nitrogen, and carbon monoxide), exothermic (composed mainly of nitrogen and dissociated ammonia), or entirely hydrogen, vacuum, or inert gas.
Outlines
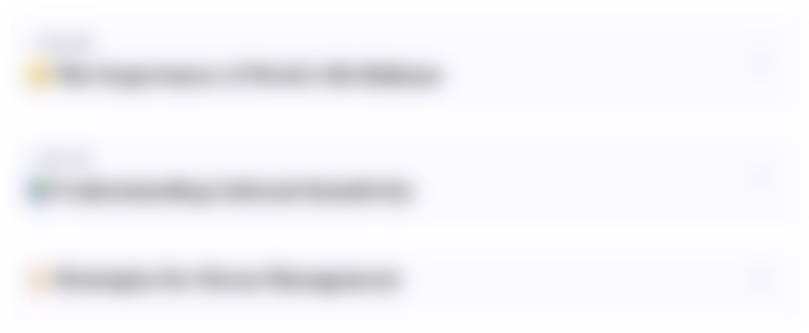
Cette section est réservée aux utilisateurs payants. Améliorez votre compte pour accéder à cette section.
Améliorer maintenantMindmap
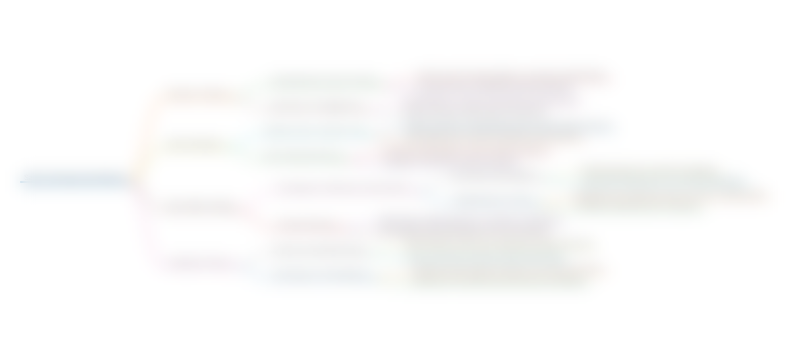
Cette section est réservée aux utilisateurs payants. Améliorez votre compte pour accéder à cette section.
Améliorer maintenantKeywords
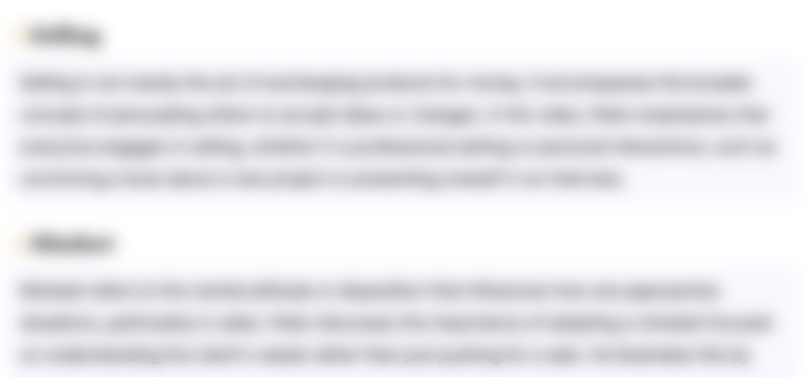
Cette section est réservée aux utilisateurs payants. Améliorez votre compte pour accéder à cette section.
Améliorer maintenantHighlights
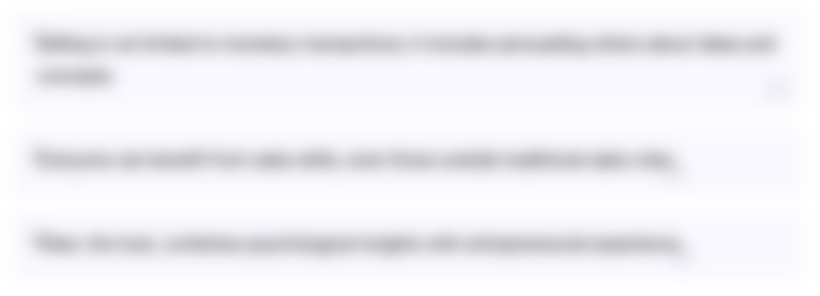
Cette section est réservée aux utilisateurs payants. Améliorez votre compte pour accéder à cette section.
Améliorer maintenantTranscripts
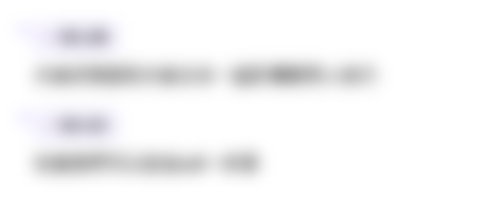
Cette section est réservée aux utilisateurs payants. Améliorez votre compte pour accéder à cette section.
Améliorer maintenantVoir Plus de Vidéos Connexes
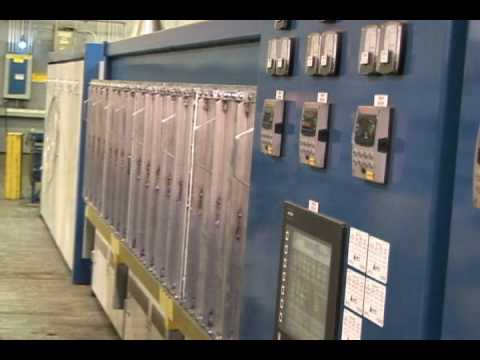
Powder Metallurgy Touches Your Life, Part 2
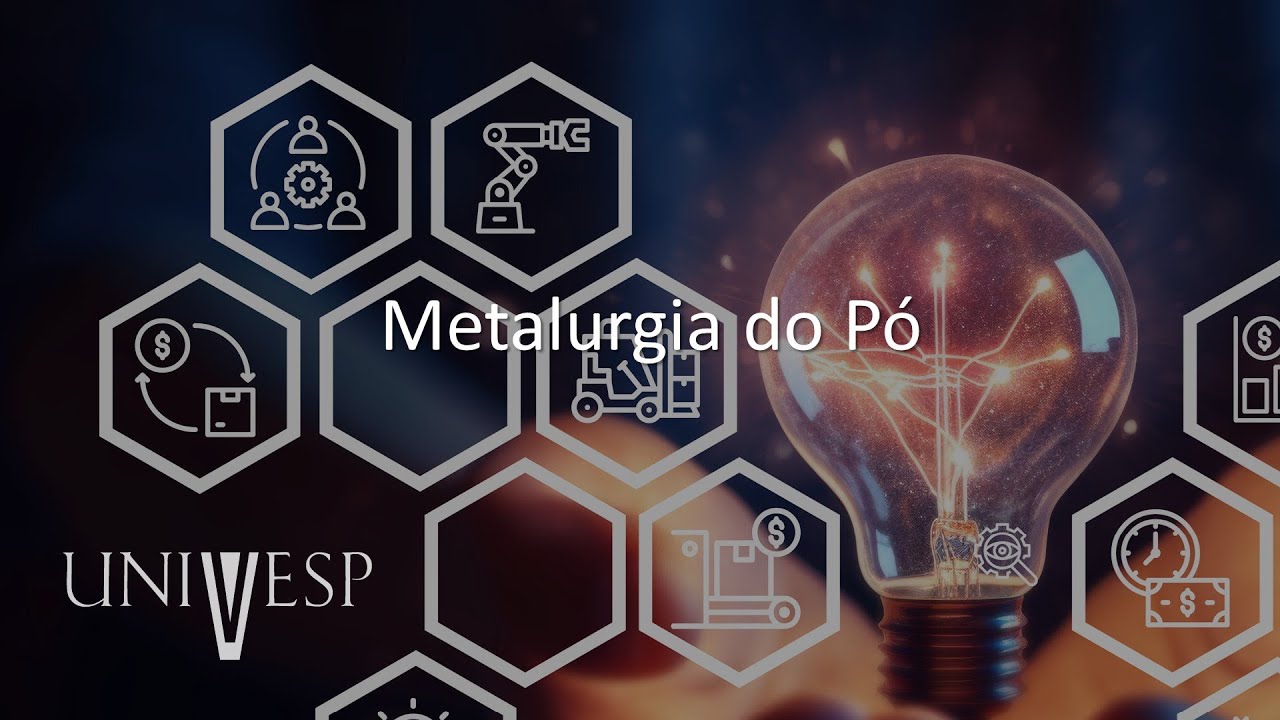
Materiais e Processos de Fabricação para Engenharia de Produção - Metalurgia do Pó

Metalurgia do Pó
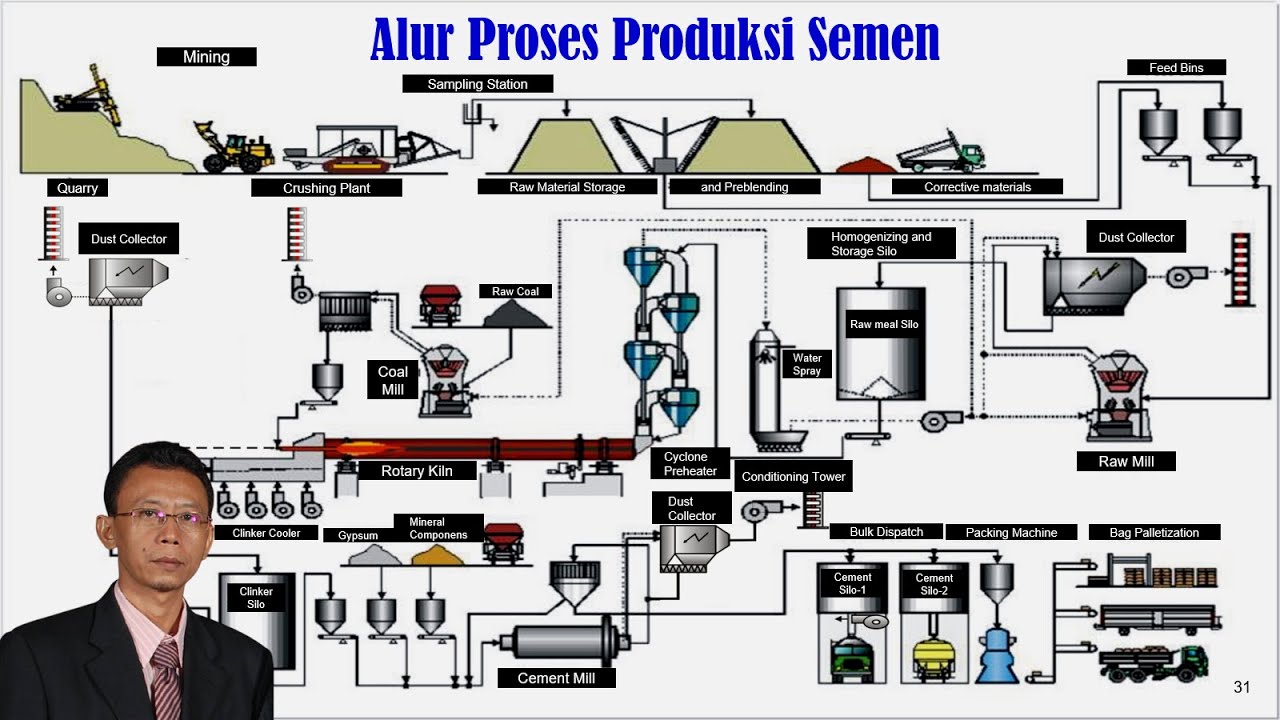
Alur Proses Produksi Semen (Tahapan Proses Produksi Semen)_Indonesia
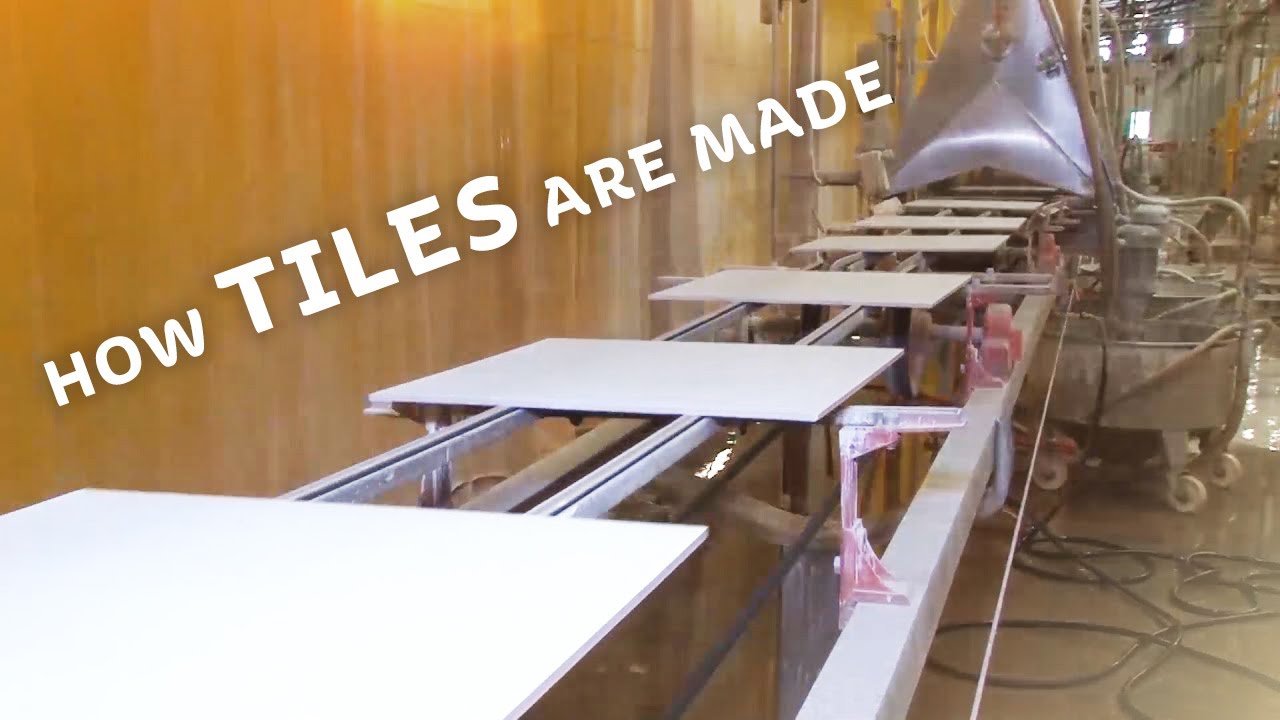
How TILES are Made
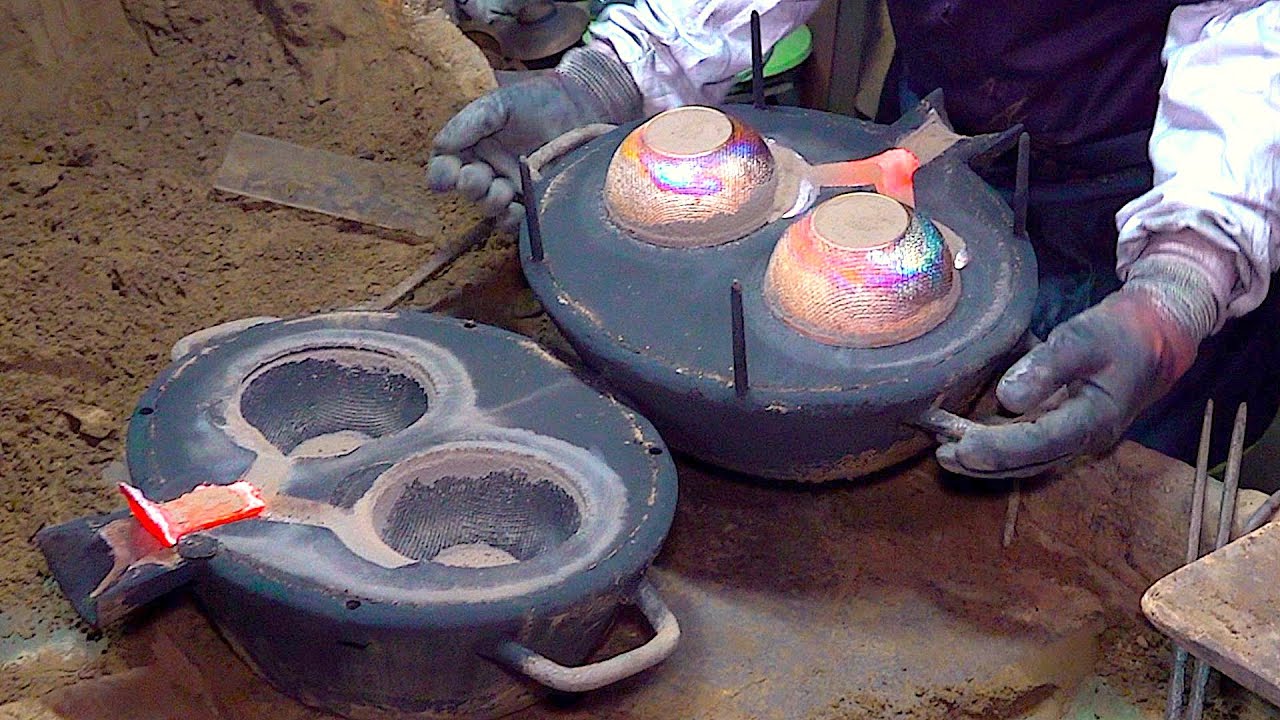
Amazing Process Of Making High Quality Bronze Bowls. Korean metal foundry
5.0 / 5 (0 votes)