15 ILUSTRASI PERHITUNGAN BIAYA UNIT PESANAN
Summary
TLDRThis video script provides a detailed breakdown of how to calculate production costs for a batch of 20 leather backpacks. It covers the direct costs of materials, labor, and overhead, as well as the markup to determine the selling price. Using a job order costing system, each order is tracked separately with unique cost cards, ensuring accuracy and avoiding confusion. The final price per unit is calculated to be $174, which includes a 50% markup on the total production costs. The system ensures clear cost tracking and transparent pricing for each order.
Takeaways
- 😀 Direct materials cost for the custom order of leather backpacks is $1,000, which includes leather, thread, and buckles.
- 😀 Direct labor cost is calculated based on the 120 hours required for production at an hourly rate of $9, totaling $1,080.
- 😀 Overhead costs are applied at a rate of $2 per hour, resulting in a total overhead of $240 for the 120 hours of work.
- 😀 The total cost for producing 20 leather backpacks comes to $2,320, which is the sum of materials, labor, and overhead.
- 😀 A 50% markup is applied to the total cost of $2,320 to achieve a desired profit of $1,160.
- 😀 The final selling price for the entire order is $3,480, which is the total cost ($2,320) plus the profit ($1,160).
- 😀 The price per unit is calculated by dividing the total selling price by the number of units (20), resulting in a price of $174 per unit.
- 😀 Job order costing is used to track individual orders, ensuring accurate recording of costs for each specific order.
- 😀 Each job order is assigned a unique job order card to track direct materials, direct labor, and overhead costs independently.
- 😀 Job order costing cards also serve as subsidiary accounts, helping separate and track the costs associated with different orders.
Q & A
What is the primary focus of the script?
-The script focuses on calculating the unit cost for producing leather backpacks, including direct material costs, direct labor costs, overhead, and the markup strategy for pricing the backpacks.
How is the direct material cost for the leather backpacks calculated?
-The direct material cost is calculated by adding up the costs of the raw materials needed for the backpacks, which include leather, thread, and buckles. The total direct material cost for 20 backpacks is 1,000.
What are the types of direct labor required for producing the backpacks?
-Three types of direct labor are needed: labor for cutting, sewing, and assembling the backpacks.
How is the direct labor cost determined?
-The direct labor cost is determined by multiplying the estimated number of hours required for production (120 hours) by the direct labor rate, which is 9 per hour. Therefore, the total labor cost is 1,080.
How is overhead cost calculated for the production of the backpacks?
-The overhead cost is calculated by multiplying the overhead rate (2 per hour) by the total hours required for production (120 hours). The total overhead cost is 240.
What is the total cost for producing 20 backpacks?
-The total cost is the sum of direct material costs (1,000), direct labor costs (1,080), and overhead costs (240), which gives a total of 2,320 for 20 backpacks.
What markup percentage is applied to the total cost, and how is the selling price determined?
-A 50% markup is applied to the total cost. The markup is calculated as 1,160 (50% of 2,320), which is then added to the total cost (2,320) to arrive at the selling price of 3,480 for the entire order.
What is the cost per unit for the backpacks?
-The cost per unit is calculated by dividing the total cost (3,480) by the number of units (20). Therefore, the cost per unit is 174.
What is the role of the job order cost card in this process?
-The job order cost card is used to track the costs associated with each specific production order. It helps in calculating the cost of each order and serves as a subsidiary account for the company’s general ledger to ensure that costs are not mixed between different orders.
How does the company ensure that costs are recorded separately for each order?
-The company uses a job order cost card system where each card is numbered sequentially according to the order number. This ensures that costs related to each specific order are recorded separately and accurately.
Outlines
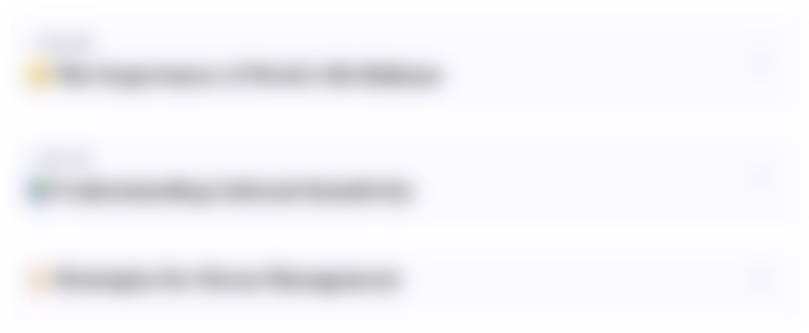
Esta sección está disponible solo para usuarios con suscripción. Por favor, mejora tu plan para acceder a esta parte.
Mejorar ahoraMindmap
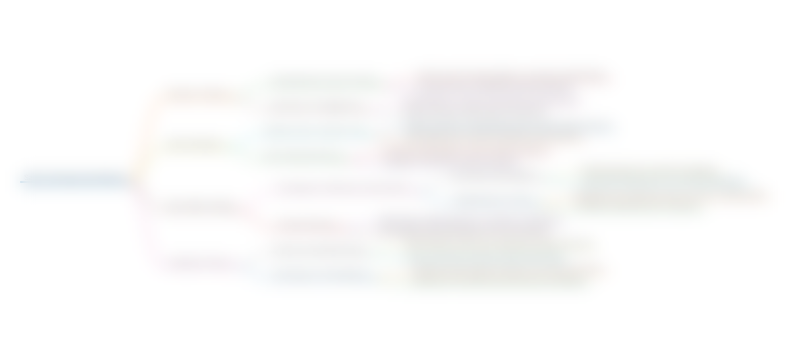
Esta sección está disponible solo para usuarios con suscripción. Por favor, mejora tu plan para acceder a esta parte.
Mejorar ahoraKeywords
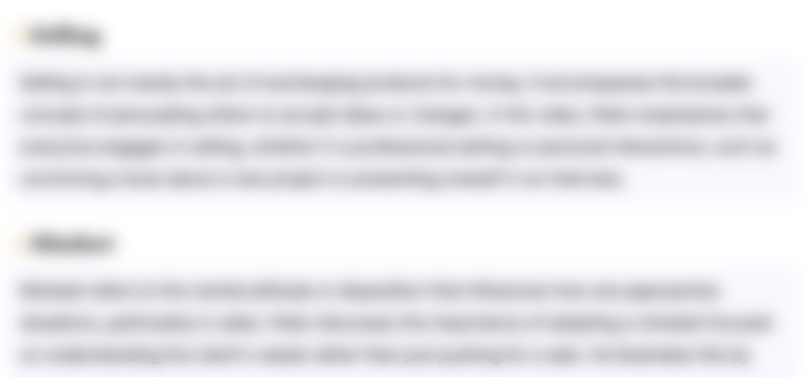
Esta sección está disponible solo para usuarios con suscripción. Por favor, mejora tu plan para acceder a esta parte.
Mejorar ahoraHighlights
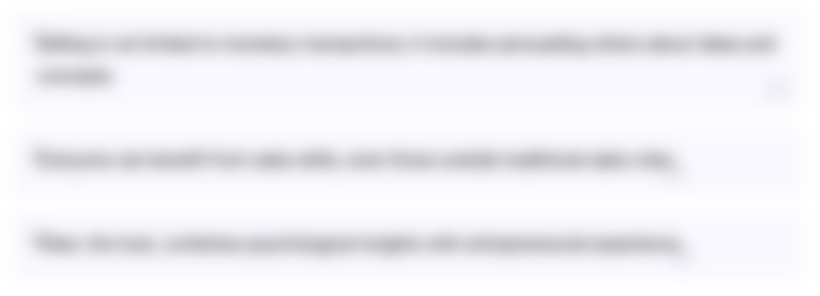
Esta sección está disponible solo para usuarios con suscripción. Por favor, mejora tu plan para acceder a esta parte.
Mejorar ahoraTranscripts
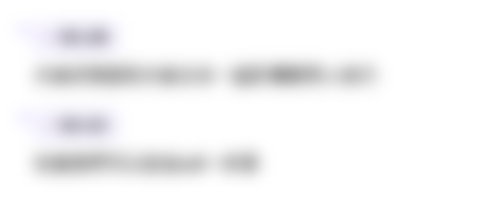
Esta sección está disponible solo para usuarios con suscripción. Por favor, mejora tu plan para acceder a esta parte.
Mejorar ahoraVer Más Videos Relacionados

Perhitungan Biaya Produksi - Materi Prakarya dan Kewirausahaan Kelas X KD 3.4/4.4
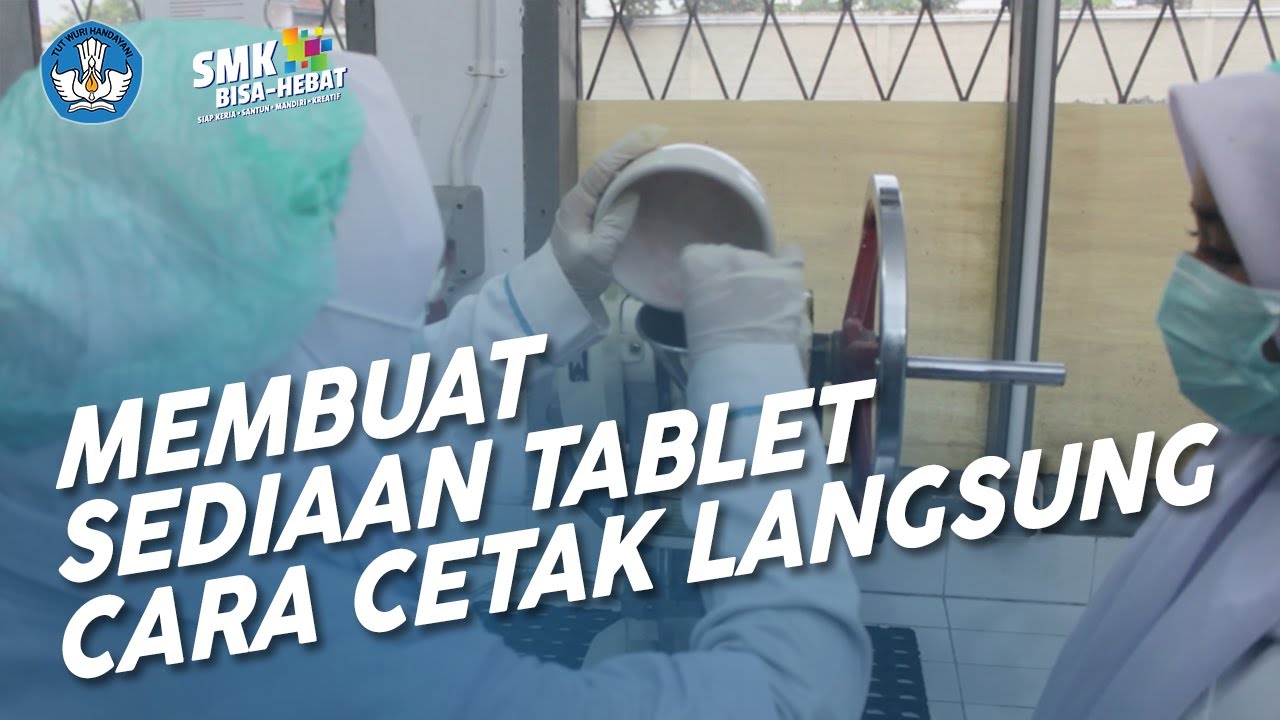
Membuat Sediaan Tablet Cara Cetak Langsung - Farmasi
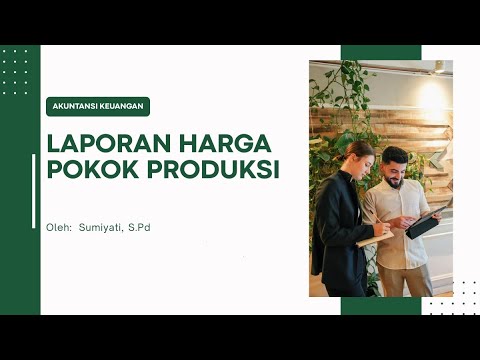
LAPORAN HARGA POKOK PRODUKSI
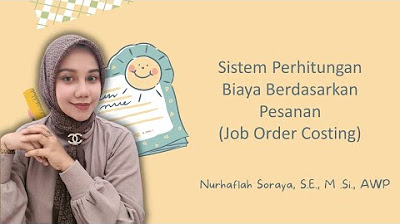
Job Order Costing | Metode Harga Pokok Pesanan | Akuntansi Biaya | Bahan Ajar Akuntansi Polmed
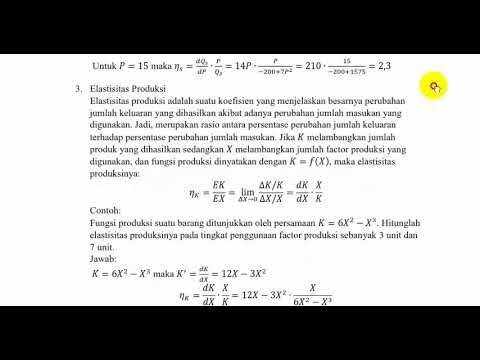
ELASTISITAS PERMINTAAN, PENAWARAN DAN PRODUKSI
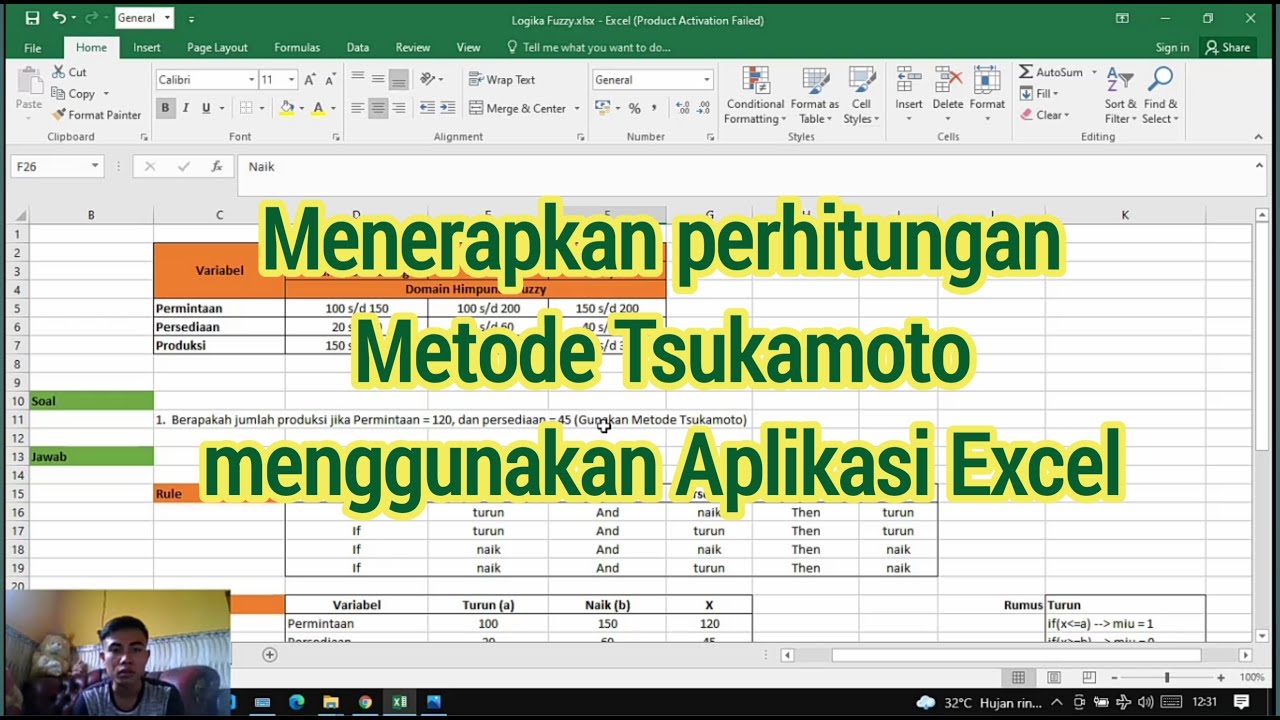
Perhitungan Metode Tsukamoto Menggunakan Aplikasi Microsoft Excel
5.0 / 5 (0 votes)