Alur Proses Produksi Semen (Tahapan Proses Produksi Semen)_Indonesia
Summary
TLDRThis video explains the comprehensive cement production process, covering everything from mining to packaging. It details each step: the extraction of raw materials (such as limestone), grinding them into raw meal, and the heating process in rotary kilns to create clinker. The clinker is then cooled, mixed with additives, and ground into final cement. The final product is packed either in bags or bulk, ready for delivery. Throughout, the video emphasizes energy efficiency, the use of specialized equipment, and dust management to ensure high-quality cement production.
Takeaways
- 😀 The video introduces the process of cement production, covering stages from raw material extraction to cement packaging.
- 😀 The cement production process is divided into five main stages: mining, raw material grinding, burning, clinker grinding, and cement packaging.
- 😀 In the mining stage, key activities include land clearing, drilling, blasting, hauling, and crushing limestone to reduce its size.
- 😀 After crushing, the limestone is transported to a storage plant and undergoes a preblending process to ensure quality consistency.
- 😀 The raw material grinding involves combining limestone, clay, silica sand, and iron sand in the correct proportions to create raw meal.
- 😀 Raw meal is then processed in a rotary kiln at temperatures between 1100°C to 1500°C, where it undergoes chemical and physical reactions to form clinker.
- 😀 The clinker is cooled in a cooler system and stored in silos before moving to the next stage of cement grinding.
- 😀 Cement grinding involves adding gypsum and additives to the clinker, resulting in finely ground cement ready for packaging.
- 😀 Packaging of cement can be done either in bags (40-50 kg) or in bulk (for larger orders), and the bags are manually or automatically packed.
- 😀 The final product is either loaded into trucks or ships for distribution, depending on the customer’s requirements.
- 😀 The video emphasizes the importance of each stage in cement production, including the use of technology to manage air quality and material consistency.
Q & A
What is the first step in the cement production process?
-The first step in the cement production process is mining. This involves land clearing, drilling, blasting, hauling, and crushing the limestone to reduce its size to less than 50 mm.
How is material preblended before it enters the grinding process?
-Material is preblended using a stacker belt conveyor, which helps mix materials of varying quality to create a homogeneous mixture before it is stored in the silo.
What equipment is used to grind raw materials in the cement production process?
-Raw materials are ground using either a Tube Mill or a Vertical Roller Mill. These mills help reduce the raw material to a fine powder, which is essential for the next steps in cement production.
What role does the kiln play in the cement production process?
-The kiln is used to burn the raw meal at high temperatures (1100-1500°C), where it undergoes chemical reactions to form clinker, a critical intermediate product in cement manufacturing.
What are the key chemical reactions that occur in the kiln?
-Key chemical reactions in the kiln include the formation of C3S, C2S, C3A, and C4AF, which are the main compounds responsible for the strength and properties of the final cement product.
How is clinker cooled after exiting the rotary kiln?
-Clinker is cooled using a cooler system, such as a Grate Cooler or Crossbar Cooler, which uses ambient air and cooling fans to reduce the temperature of the clinker to below 100°C.
What is the purpose of the cement mill in the production process?
-The cement mill is used to grind the cooled clinker together with gypsum and other additives. This produces the final fine cement powder with the required consistency and quality.
How does dust collection work during the grinding process?
-During the grinding process, dust is captured by a Dust Collector, which filters out airborne particles. The collected dust is then returned to the production process, while clean air is released through a chimney.
What types of packaging are used for cement products?
-Cement is packaged either in bags (typically 40-50 kg) or in bulk using bigbags (1000-1500 kg). Bags are filled using a rotary packer, and the packaging process may be automatic or manual.
How is bulk cement transported?
-Bulk cement is transported using bulk trucks or ships, and is loaded through pneumatic conveying systems to ensure efficient transfer without spillage or contamination.
Outlines
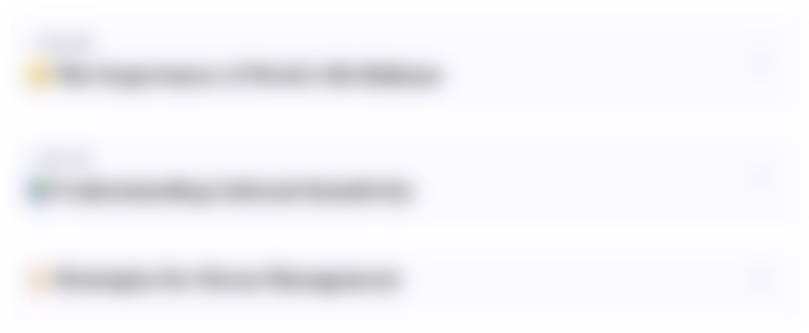
Esta sección está disponible solo para usuarios con suscripción. Por favor, mejora tu plan para acceder a esta parte.
Mejorar ahoraMindmap
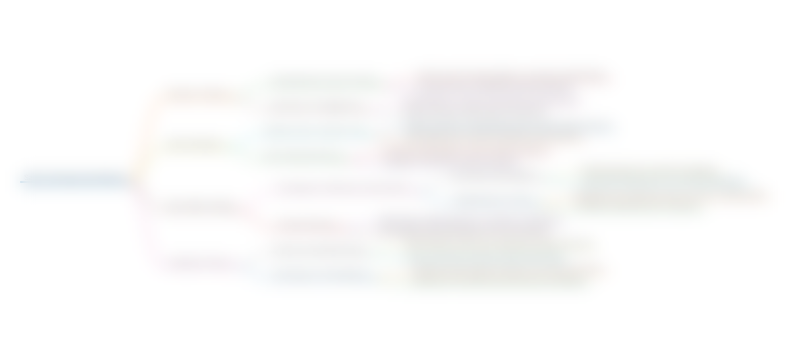
Esta sección está disponible solo para usuarios con suscripción. Por favor, mejora tu plan para acceder a esta parte.
Mejorar ahoraKeywords
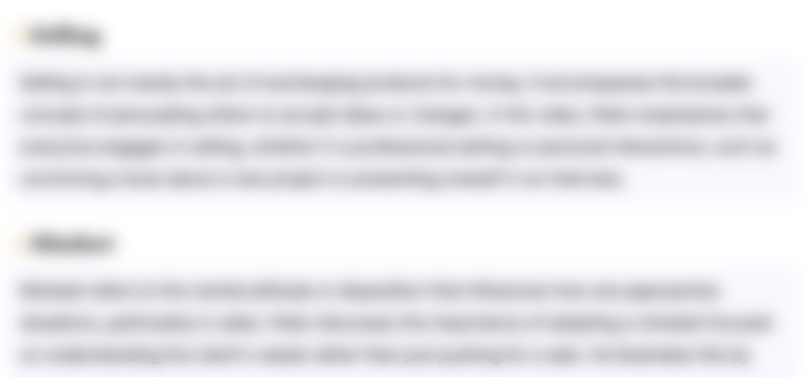
Esta sección está disponible solo para usuarios con suscripción. Por favor, mejora tu plan para acceder a esta parte.
Mejorar ahoraHighlights
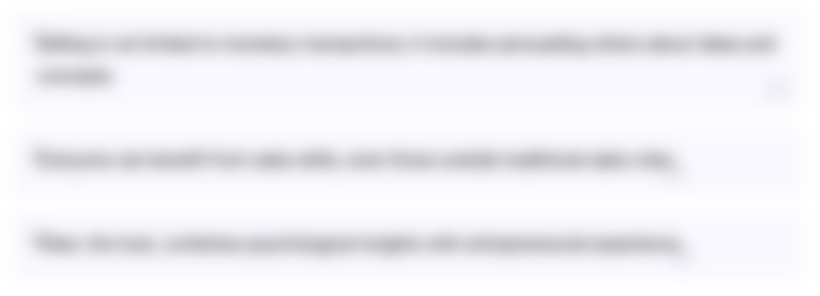
Esta sección está disponible solo para usuarios con suscripción. Por favor, mejora tu plan para acceder a esta parte.
Mejorar ahoraTranscripts
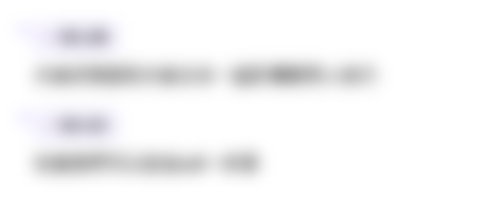
Esta sección está disponible solo para usuarios con suscripción. Por favor, mejora tu plan para acceder a esta parte.
Mejorar ahoraVer Más Videos Relacionados

Kimia Industri - Diagram Alir Proses Pembuatan Semen

How Cement is Made? Cement Production Process 🪨
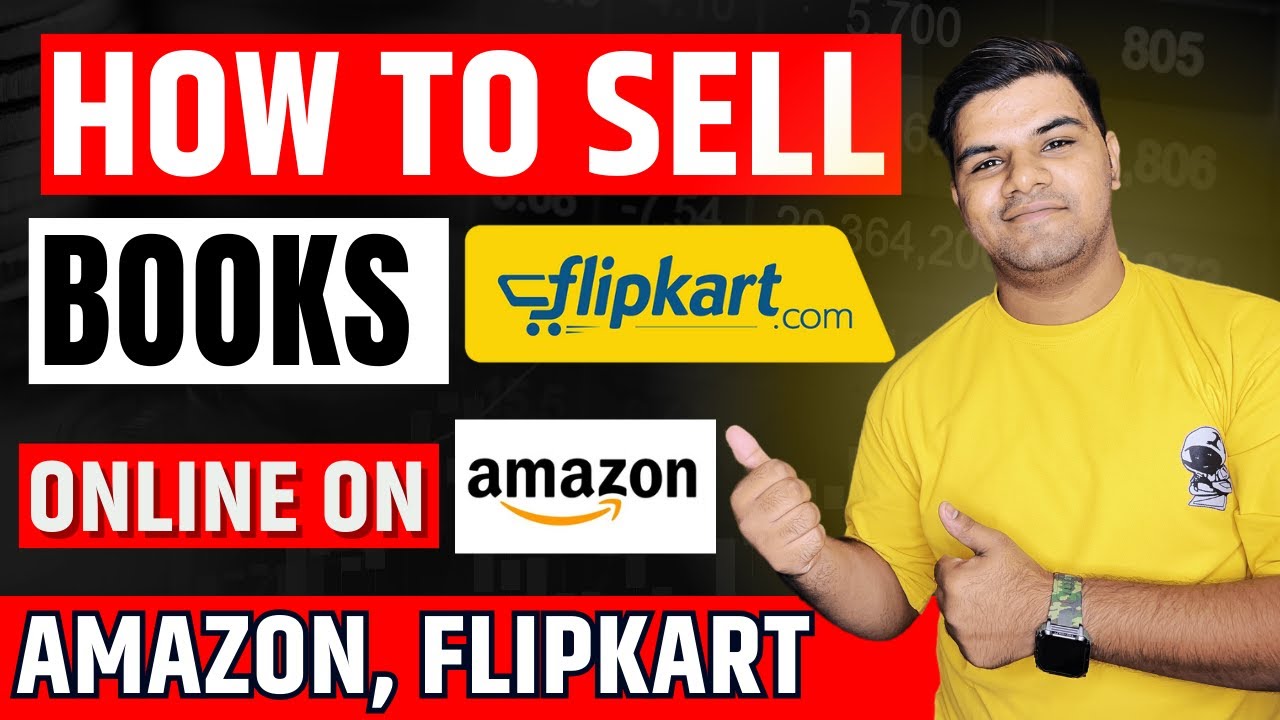
How to Sell Books Online on Amazon, Flipkart and Meesho | Make Money Online | Selling books online
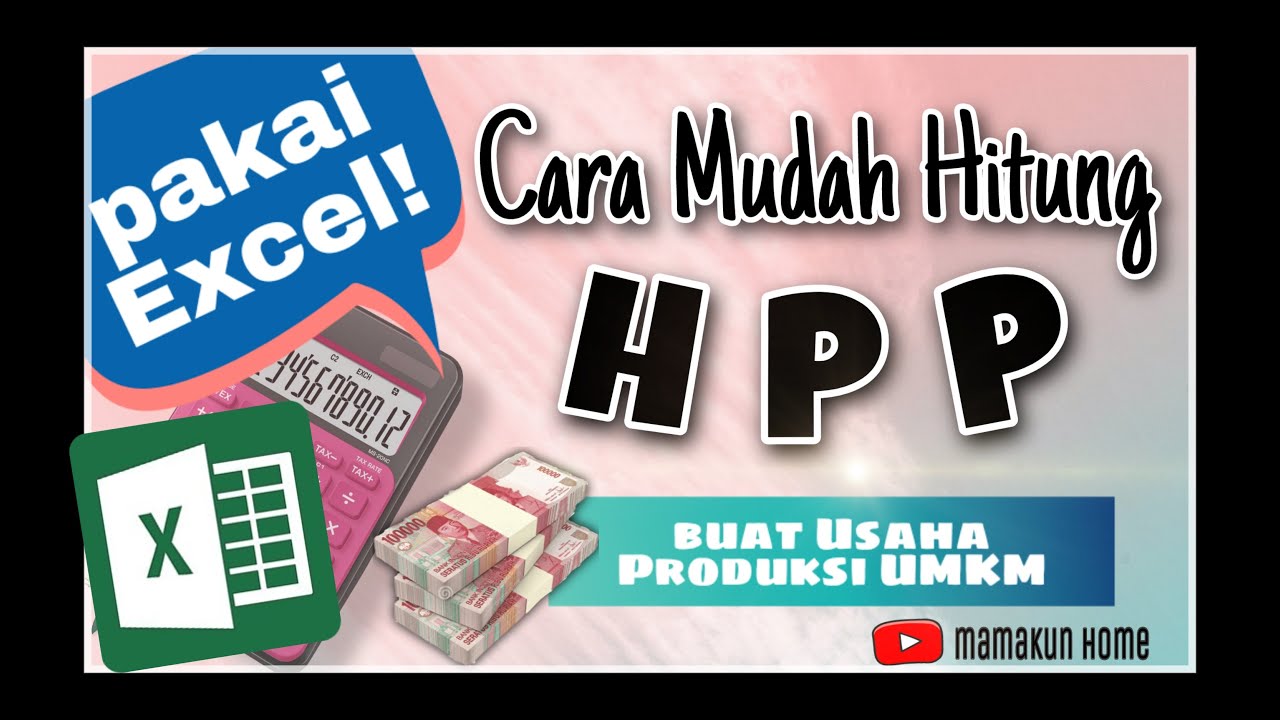
Cara Mudah Menghitung HPP dan Harga Jual usaha produksi UMKM
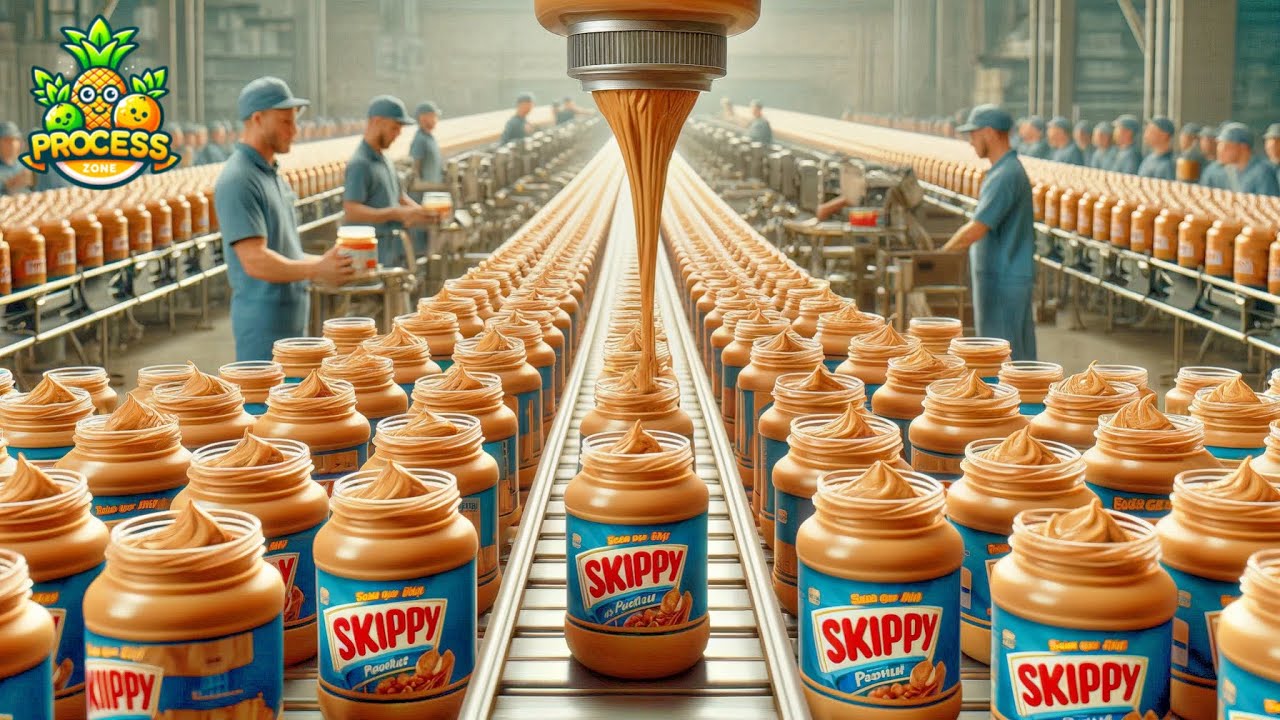
How Peanut Butter Is Made In Factory | Peanut Butter Factory Process

Kimia Industri - Pembuatan Cat (Diagram Alir Proses) (Bag.2 - Akhir)
5.0 / 5 (0 votes)